Introduction to PAR Inventory Management by Trident Edge Consulting
Summary
TLDRThis educational video provides an in-depth introduction to par inventory management in the healthcare supply chain. It covers essential concepts such as 'par' (periodic automated replenishment), mobile par counting, and advanced replenishment solutions like point-of-use systems. The video also explores the two-bin kanban method, which efficiently manages inventory by using visual indicators to trigger reordering. The goal is to enhance supply chain efficiency, reduce waste, and improve the replenishment process. Viewers are encouraged to understand these inventory strategies to ensure smooth operations in clinical departments and hospitals.
Takeaways
- 😀 Par Inventory refers to 'Periodic Automated Replenishment,' a system used to manage supplies in healthcare settings where inventory isn't perpetually tracked.
- 😀 Mobile Par Counting involves using handheld devices to track inventory levels and manage replenishment in real time.
- 😀 Par locations are non-perpetual supply areas managed by supply chain staff, but the department owns the inventory once supplies are issued.
- 😀 It's important to label chargeable supplies in par locations clearly to ensure that patient charges are properly tracked and billed.
- 😀 The par replenishment process begins with staff members walking through par locations, identifying low stock, and generating electronic requisitions using either handheld devices or desktop computers.
- 😀 Advanced replenishment solutions like Pixis, Omnicell, and others offer automated inventory tracking but require staff compliance for accurate data (e.g., scanning, using probes, or weighing bins).
- 😀 Point-of-use inventory systems can help improve replenishment efficiency by reducing the need for manual stock counting and increasing accuracy through automation.
- 😀 If using a point-of-use inventory system, it's essential to ensure compliance with required transaction steps (e.g., taking and putting back items) for accurate inventory tracking.
- 😀 The Two-Bin Kanban system is a lean inventory method where items are stored in two bins, with replenishment triggered when the first bin is empty.
- 😀 Kanban systems, when properly implemented, can streamline replenishment processes, reduce stockouts, enforce FIFO policies, and minimize waste.
Q & A
What is par inventory management?
-Par inventory management is a system used to manage inventory levels at specific locations, ensuring that the required stock is maintained without overstocking or running out of supplies. It is typically used in healthcare settings for managing supplies in clinical departments.
What does the term 'par' refer to in healthcare supply chain management?
-In healthcare supply chain management, 'par' refers to Periodic Automated Replenishment. It can designate a storage location or the maximum stocking quantity for an item at a given location.
What is 'mobile par' counting?
-Mobile par counting refers to the process of inventory replenishment performed using a handheld device. This device helps track items that need restocking by scanning barcodes and updating inventory in real-time.
How does the replenishment process work in a hospital using par inventory?
-The replenishment process involves supply chain staff walking through par locations, identifying items running low, and generating electronic requisitions. Replenishments are processed either from the storeroom or external suppliers based on the inventory system's recommendations.
What is the role of 'point of use inventory management' systems?
-Point of use inventory management systems are advanced solutions that track inventory at the point where supplies are used. These systems help ensure that inventory levels are accurately recorded, reducing the need for manual counting and improving the replenishment process.
What challenges are associated with point of use inventory systems?
-Challenges with point of use systems include staff non-compliance with recording take and put-back transactions, incorrect bin placements, and potential technical issues with system features like barcode scanning or weight-based monitoring.
What are the benefits of using point of use inventory management systems?
-The benefits include more accurate tracking of inventory quantities, improved replenishment efficiency, and the ability to integrate with patient billing systems for accurate chargeback of supplies used in patient care.
How does the two-bin kanban method work in inventory management?
-The two-bin kanban method involves using two bins for each item: one in use and one as a backup. When the first bin is emptied, it is replaced by the second bin, and the empty bin is reordered based on the labeled quantity. This method ensures efficient stock rotation and prevents stockouts.
What items are best suited for the two-bin kanban system?
-The two-bin kanban system works well for smaller, frequently used items such as syringes, bandages, and vials. These items are easy to store in bins and are typically used in clinical settings.
How does the two-bin kanban method support FIFO (First-In, First-Out) inventory practices?
-The two-bin kanban method supports FIFO by ensuring that the first bin of supplies is used before the second bin, which helps reduce waste and ensures that older stock is used first, minimizing expiration issues.
Outlines
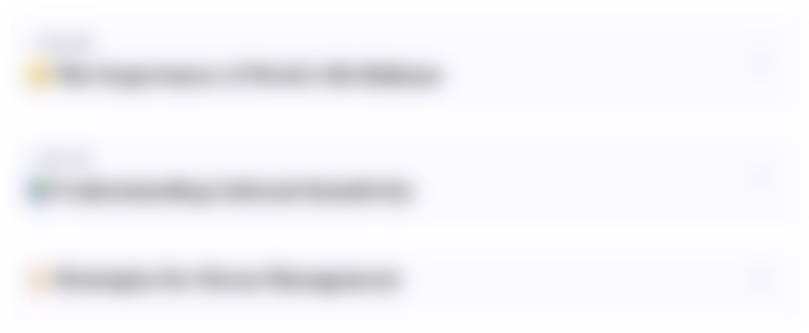
このセクションは有料ユーザー限定です。 アクセスするには、アップグレードをお願いします。
今すぐアップグレードMindmap
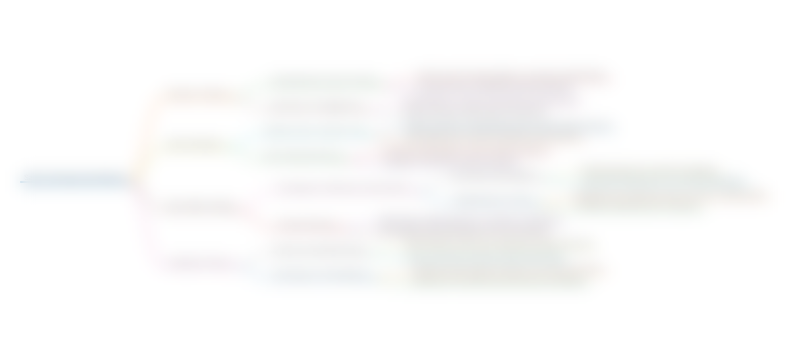
このセクションは有料ユーザー限定です。 アクセスするには、アップグレードをお願いします。
今すぐアップグレードKeywords
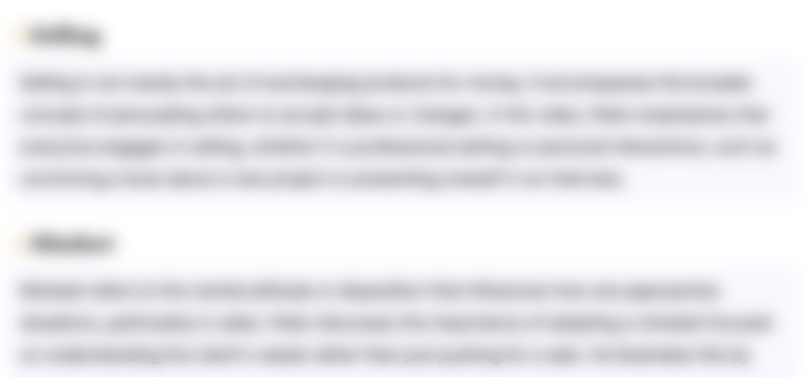
このセクションは有料ユーザー限定です。 アクセスするには、アップグレードをお願いします。
今すぐアップグレードHighlights
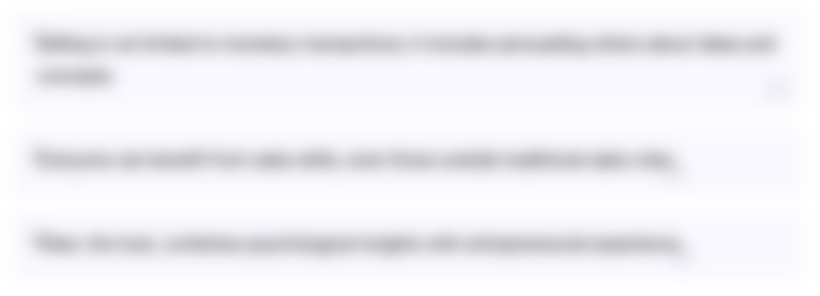
このセクションは有料ユーザー限定です。 アクセスするには、アップグレードをお願いします。
今すぐアップグレードTranscripts
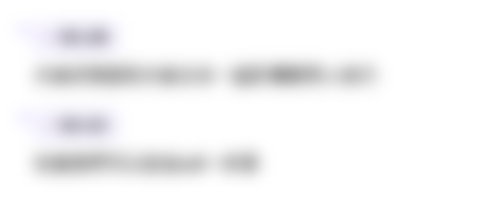
このセクションは有料ユーザー限定です。 アクセスするには、アップグレードをお願いします。
今すぐアップグレード関連動画をさらに表示
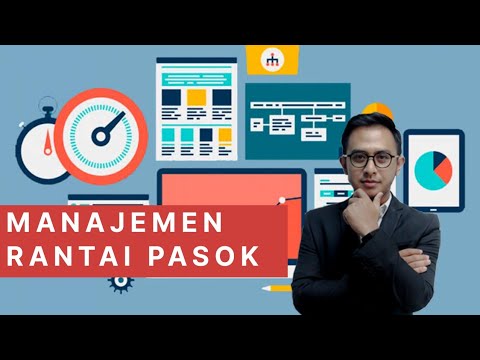
Manajemen Produksi - Ep.13 Supply Chain Management/Manajemen Rantai Pasok
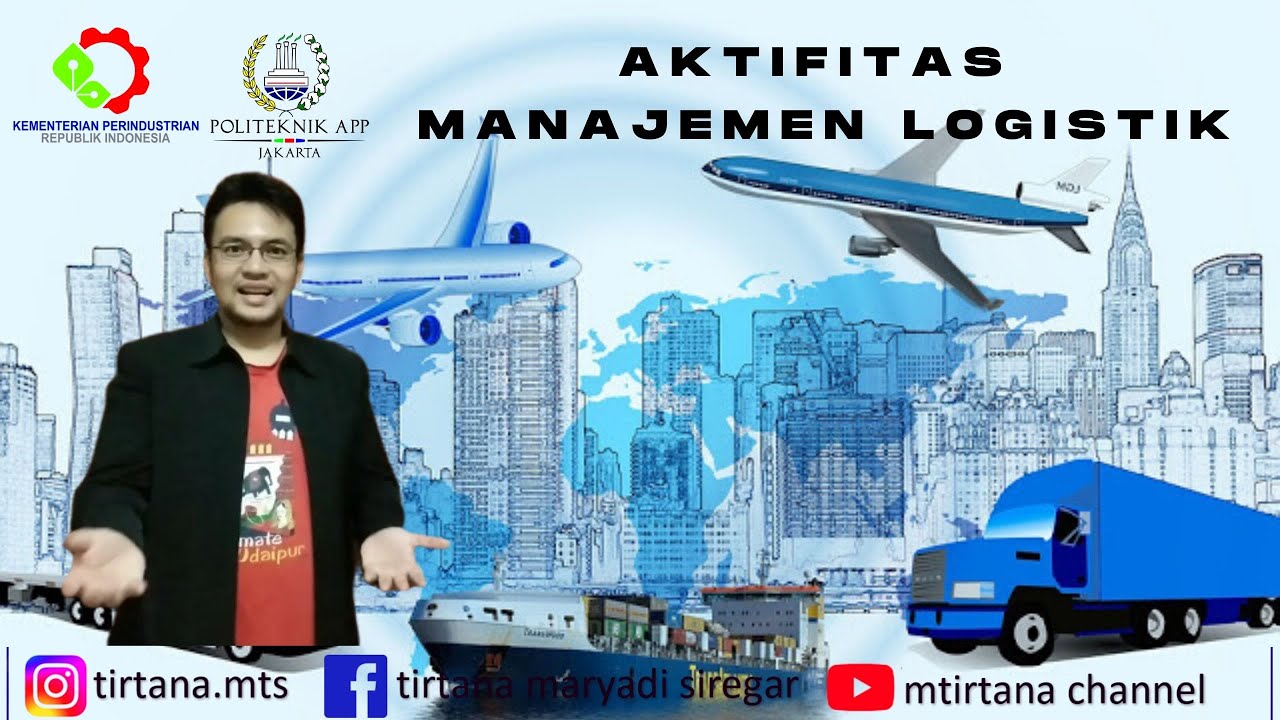
(PART 1) : Aktifitas Manajemen Logistik

Manajemen Alat dan Bahan - Administrasi Logistik

Understanding Inventory Management (INSIDE THE SUPPLY CHAIN SERIES) Lesson 1

H&M Fast Fashion Case Study | Global Supply Chain Strategy | MBA Case Study Analysis with Solution
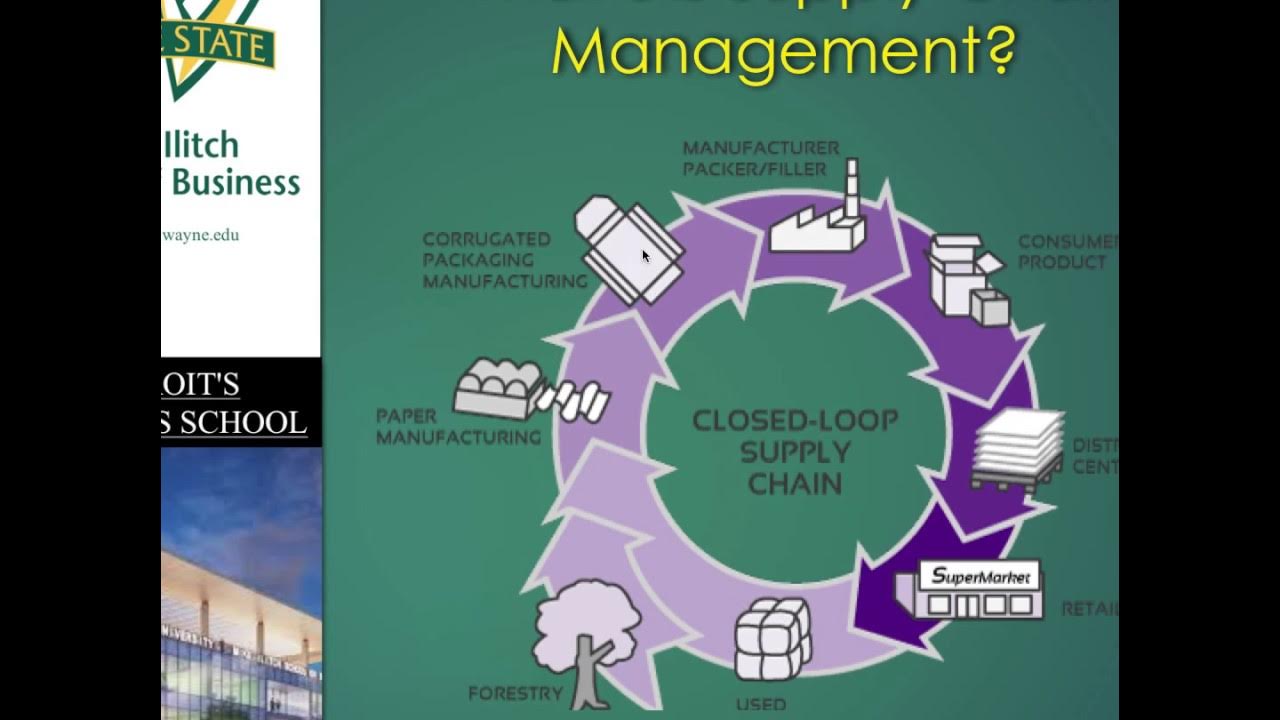
What is a Supply Chain?
5.0 / 5 (0 votes)