Overview and basics of SAP Warehouse Management
Summary
TLDRThis video provides an in-depth overview of Warehouse Management Systems (WMS), explaining their structure, advantages, and key functionalities. WMS optimizes warehouse operations by enabling precise tracking of materials at the bin level, managing hazardous materials, and integrating with barcode and RFID systems. The video also discusses the hierarchical setup of WMS, including storage types, sections, and bins, and distinguishes it from inventory management by emphasizing the location-specific tracking capabilities of WMS. The system's ability to streamline operations and improve efficiency in both storage and picking processes is highlighted, offering businesses a comprehensive solution for managing complex warehouse tasks.
Takeaways
- 😀 Warehouse Management (WM) provides detailed location tracking of materials down to the storage bin level, enhancing operational efficiency.
- 😀 Putaway refers to placing materials in storage, while picking involves retrieving them for shipping. Both processes can be automated or manually controlled.
- 😀 WM supports the flexible use of different strategies for putaway and picking, allowing businesses to prioritize older or newer items based on specific needs.
- 😀 WM integrates with RFID and barcode scanners, enabling automatic updates for material details, reducing manual data entry errors.
- 😀 Warehouse Management includes specialized processes for storing hazardous materials safely, such as flammable or dangerous goods.
- 😀 SAP WM has a hierarchical structure with warehouses at the top, followed by storage types, sections, and bins. Each level has specific roles in organizing materials.
- 😀 Interim Storage Types in SAP WM serve as virtual spaces within the system that connect inventory management with warehouse management without being physically present.
- 😀 Storage sections group storage bins based on characteristics like size, material type, and frequency of movement (e.g., heavy, bulky, or fast-moving items).
- 😀 Inventory Management (IM) tracks materials at the storage location level, while Warehouse Management (WM) provides precise bin-level location details, offering better control and accuracy.
- 😀 A warehouse management system improves operational transparency by clearly identifying material locations, unlike basic inventory systems that require manual searching.
- 😀 WM can interface with different storage types (e.g., high-rack, bulk storage) and assign materials to these areas based on their properties and handling requirements.
Q & A
What is warehouse management and why is it important?
-Warehouse management refers to the system used to track materials at the granular level of storage bins. It helps to optimize warehouse operations, ensuring accurate material location, efficient storage, and retrieval. The system improves visibility, reduces errors, and supports automated processes for handling complex warehouse tasks.
What are the key advantages of using warehouse management systems (WMS)?
-WMS provides several advantages, such as enabling accurate tracking of materials, offering flexibility in warehouse operations, automating complex processes, and supporting efficient picking and putaway strategies. It also improves safety for hazardous materials and integrates with technologies like RFID and barcodes for streamlined operations.
What is the difference between putaway and picking in warehouse management?
-Putaway refers to the process of placing materials into the warehouse, which can be directed manually or automated. Picking is the process of retrieving materials from storage for shipment or use. The system can prioritize picking based on material age, such as oldest or newest items.
How does warehouse management handle hazardous materials?
-Warehouse management systems can handle hazardous materials by assigning special processes for their storage and retrieval. For example, dangerous or flammable items can be stored in designated areas with additional safety measures, separate from general inventory.
What role do RFID and barcode systems play in warehouse management?
-RFID and barcode systems streamline material tracking by automatically updating the system with information such as material number, batch, and quantity. These systems reduce manual data entry errors and improve operational efficiency by quickly scanning and updating inventory records.
What is the hierarchical structure of warehouse management?
-The structure of warehouse management includes several levels: the warehouse itself (the highest level), followed by storage types, storage sections, and storage bins. These levels help organize materials and optimize warehouse space and operations, ensuring effective storage and retrieval.
What is the difference between physical and interim storage types in warehouse management?
-Physical storage types refer to actual, physical areas in the warehouse where materials are stored (e.g., bulk storage or high-rack storage). Interim storage types, on the other hand, are virtual areas that exist in the system but are not physically present in the warehouse. They serve as transitional storage points for materials.
How are storage sections used in warehouse management?
-Storage sections group together storage bins with similar characteristics, such as size, material type, or movement speed. These sections help optimize the process of putting away and retrieving materials, with specific sections dedicated to fast-moving items, heavy parts, or bulky materials.
What is the concept of 'quant' in warehouse management?
-A 'quant' represents the quantity of a material within a storage bin. It is generated based on criteria such as material type, batch, or stock category. Multiple quants can exist within a bin if different types or batches of materials are stored together.
How does warehouse management integrate with inventory management?
-Warehouse management is integrated with inventory management at the plant and storage location level. This integration ensures that inventory records are synchronized with warehouse operations, allowing for accurate tracking and management of materials across both systems.
Outlines
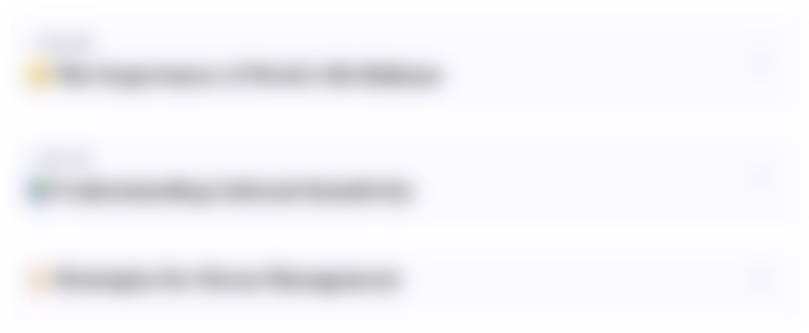
このセクションは有料ユーザー限定です。 アクセスするには、アップグレードをお願いします。
今すぐアップグレードMindmap
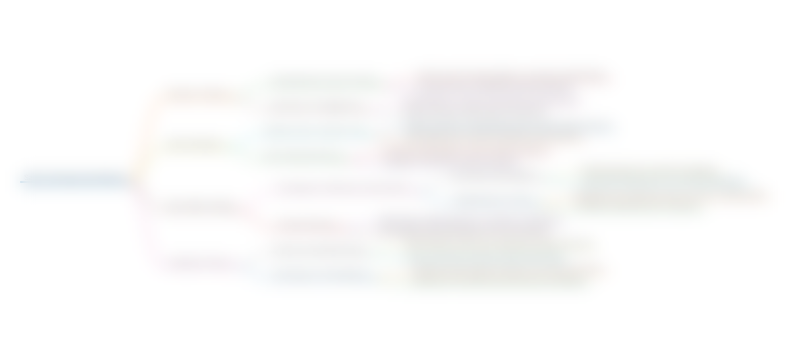
このセクションは有料ユーザー限定です。 アクセスするには、アップグレードをお願いします。
今すぐアップグレードKeywords
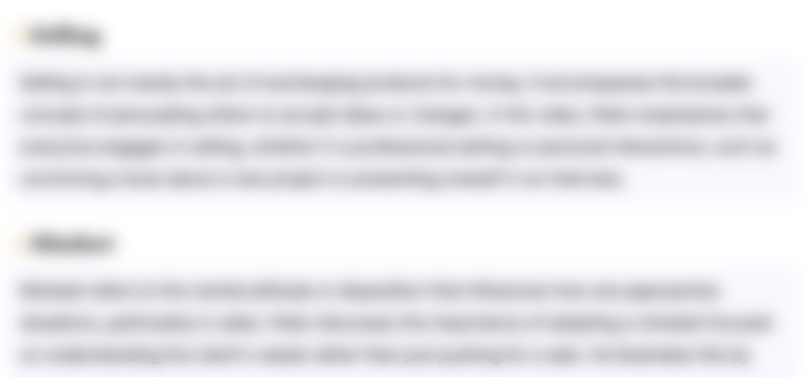
このセクションは有料ユーザー限定です。 アクセスするには、アップグレードをお願いします。
今すぐアップグレードHighlights
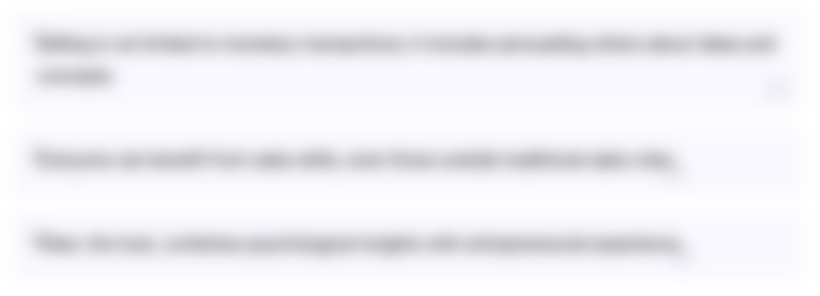
このセクションは有料ユーザー限定です。 アクセスするには、アップグレードをお願いします。
今すぐアップグレードTranscripts
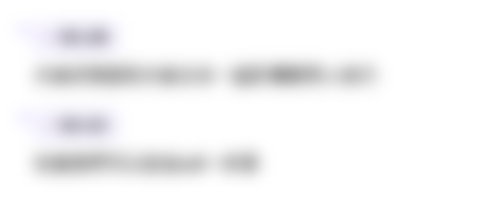
このセクションは有料ユーザー限定です。 アクセスするには、アップグレードをお願いします。
今すぐアップグレード関連動画をさらに表示

What is Warehouse Management System? How WMS Works
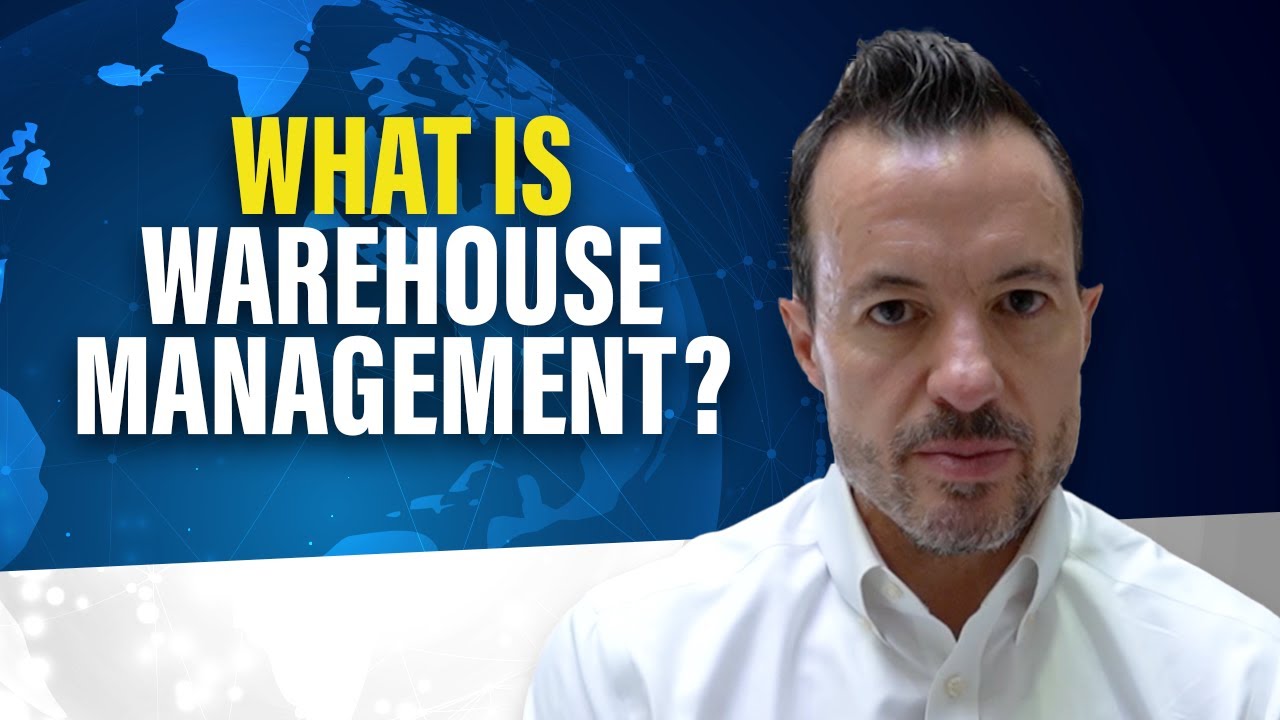
What is Warehouse Management? [Intro to Inventory Management, Pick Pack Ship, WMS Software, etc]
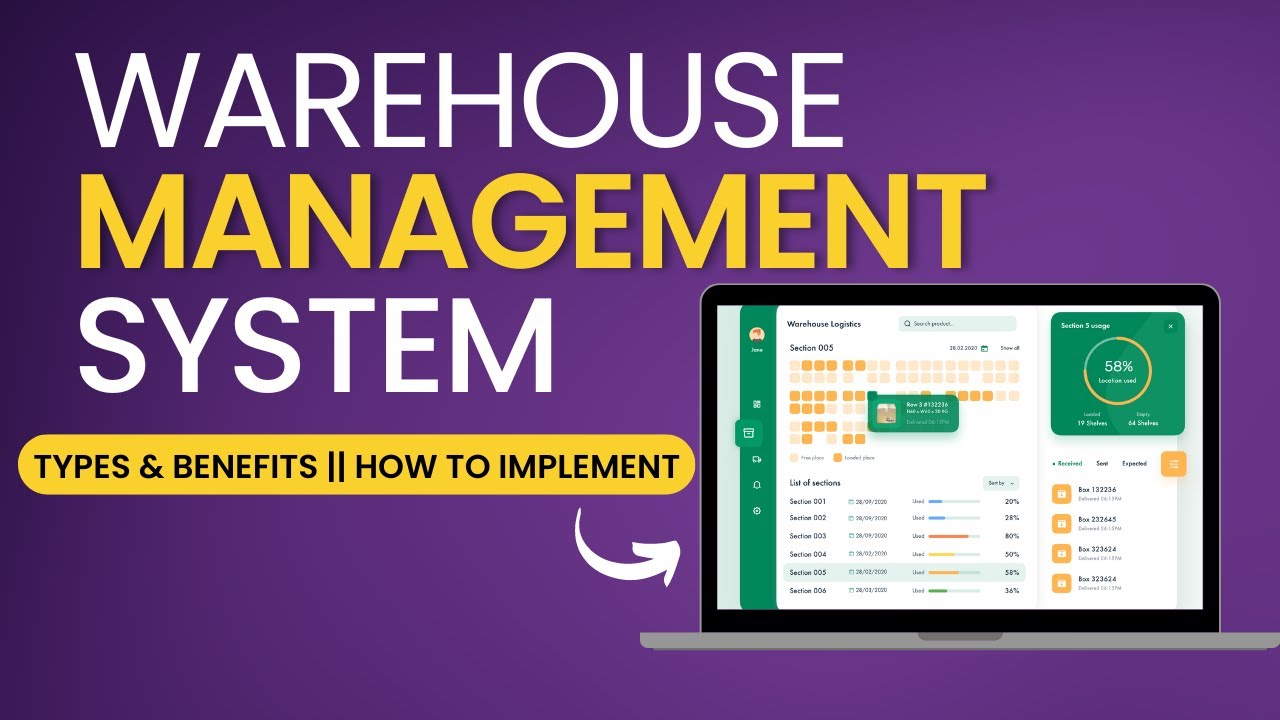
What is Warehouse Management System | WMS Software | Functions & Benefits of WMS | How WMS works

Optimizing Your Space: A Step-by-Step Guide to Designing an Efficient Warehouse Layout
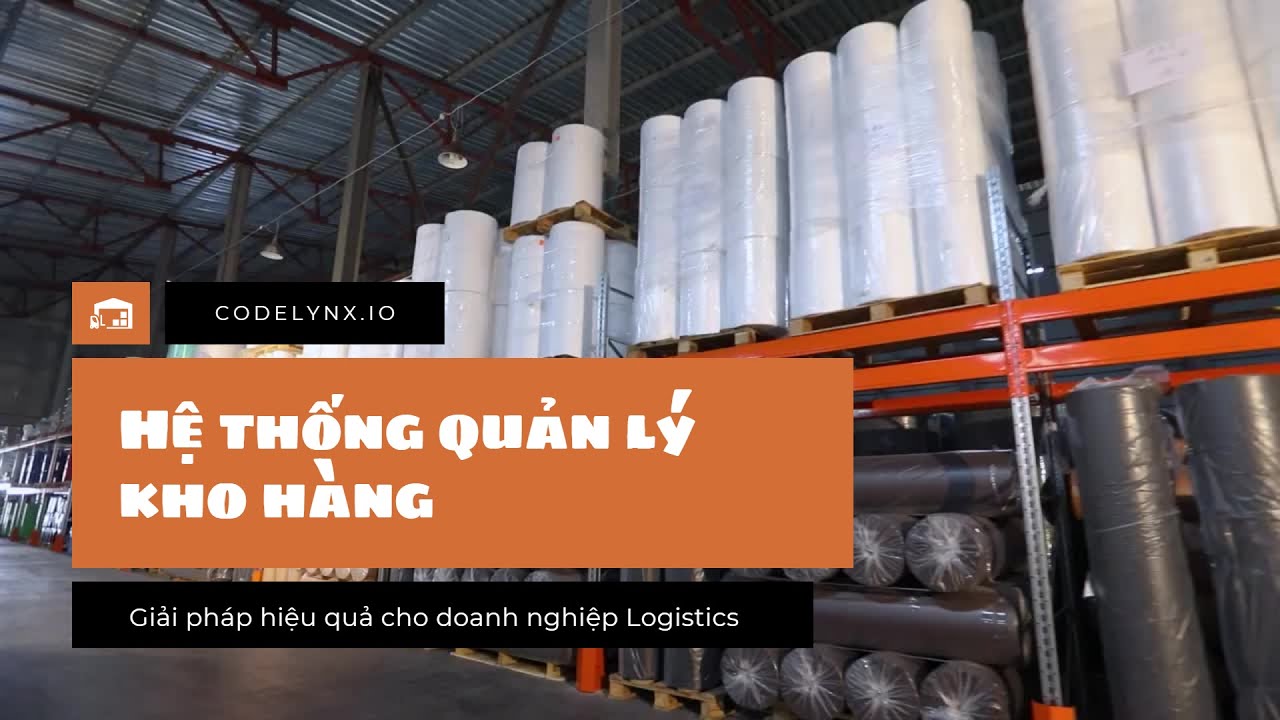
Hệ thống quản lý kho hàng - Giải pháp hiệu quả cho doanh nghiệp Logistics

Warehouse Practice & Warehouse Management System
5.0 / 5 (0 votes)