Casting Allowances in Hindi || Allowances in Casting
Summary
TLDRThis video discusses the concept of pattern allowances in casting processes, explaining different types of allowances such as shrinkage, draft, machining, and shake allowances. Shrinkage allowance accounts for the reduction in volume when metal changes from liquid to solid, while draft allowance helps in easy removal of the pattern from the mold. Machining allowance ensures enough material is left for a smooth finish, and shake allowance facilitates easier removal of the pattern. The speaker emphasizes that while these concepts are taught theoretically, practical knowledge is gained in real industry settings.
Takeaways
- 📏 Casting processes require allowances for changes in size and shape during production.
- 📉 Shrinkage allowance compensates for the reduction in volume when metal cools and solidifies.
- ⚙️ Different materials require specific shrinkage allowances: white cast iron needs 21 mm per meter, grey cast iron needs 10 mm per meter, and copper/brass/aluminum need 16 mm per meter.
- 🔍 Shrinkage affects internal diameters, so allowances are made to ensure the final size is accurate after shrinkage.
- 🧊 Draft allowance is a taper given to patterns to allow for easy removal from the mold.
- ✂️ A finish and machining allowance is added to ensure the final product has a smooth surface, as cast surfaces are often rough.
- 🔧 The mold flask is often wrapped and shaken to loosen the pattern, making removal easier.
- 🏗️ Different casting processes like sand casting, shell molding, and centrifugal casting may require different allowances.
- 🎯 These allowances are crucial for ensuring accuracy in the final product, especially in industrial applications.
- 💡 Engineers learn about allowances in theory, but practical application happens in the field, during actual manufacturing processes.
Q & A
What is the purpose of allowances in casting?
-Allowances are added to the mold or pattern to compensate for changes in size or shape that may occur during the casting process. These adjustments ensure the final product meets the desired specifications.
What is shrinkage allowance in casting?
-Shrinkage allowance is the compensation given for the reduction in volume when metal changes from liquid to solid during the casting process. Different materials have different shrinkage rates, and this allowance helps in maintaining accurate final dimensions.
Why is the shrinkage measured in linear terms instead of volumetric?
-Although shrinkage happens volumetrically, it is often converted into linear measurements (e.g., mm per meter) to make it easier to calculate and apply during the design and manufacturing processes.
Why is a riser used in the casting process?
-A riser is used to compensate for the shrinkage of the metal during solidification. It ensures that the casting is not starved of metal as shrinkage occurs, helping to maintain the shape and size of the final product.
What is draft allowance and why is it necessary?
-Draft allowance is a taper provided on the pattern to ensure the easy removal of the pattern from the mold. It prevents damage to the mold during the removal process and ensures a smooth production flow.
How is surface finish improved in castings?
-Surface finish is improved by giving a machining allowance, which is extra material added to the casting. This extra material is later removed through machining processes to achieve a smooth surface.
What is the function of wrapping or shake allowance?
-Wrapping or shake allowance compensates for any slight movement or shaking of the mold during pattern removal. This allowance ensures that the pattern can be easily removed without damaging the mold.
Why is a larger internal diameter given in casting patterns?
-A larger internal diameter is provided in the casting pattern to account for shrinkage. As the metal solidifies and shrinks, the final internal diameter matches the desired specification after shrinkage compensation.
How does the material type affect the shrinkage allowance?
-Different materials have different shrinkage rates. For example, white cast iron may require a shrinkage allowance of 21 mm per meter, while gray cast iron requires 10 mm per meter. These values are adjusted based on the material's properties.
Why is casting surface finish typically poor, and how is it addressed?
-Casting often results in poor surface finish due to the roughness of the mold and the cooling process. To address this, a machining allowance is provided, allowing for the rough surface to be machined down to a smooth, finished surface.
Outlines
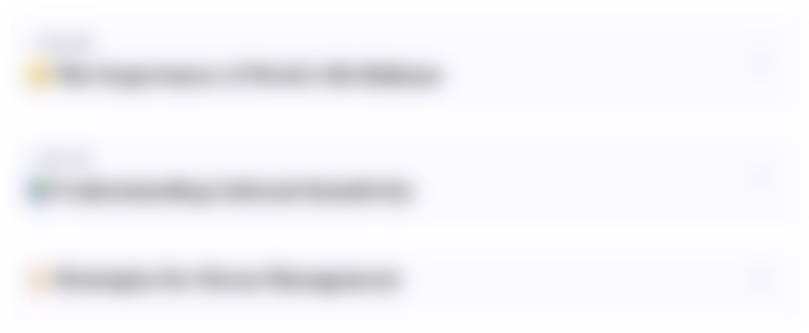
このセクションは有料ユーザー限定です。 アクセスするには、アップグレードをお願いします。
今すぐアップグレードMindmap
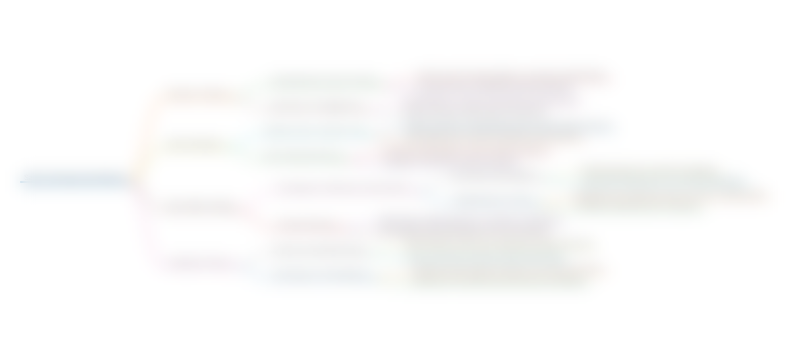
このセクションは有料ユーザー限定です。 アクセスするには、アップグレードをお願いします。
今すぐアップグレードKeywords
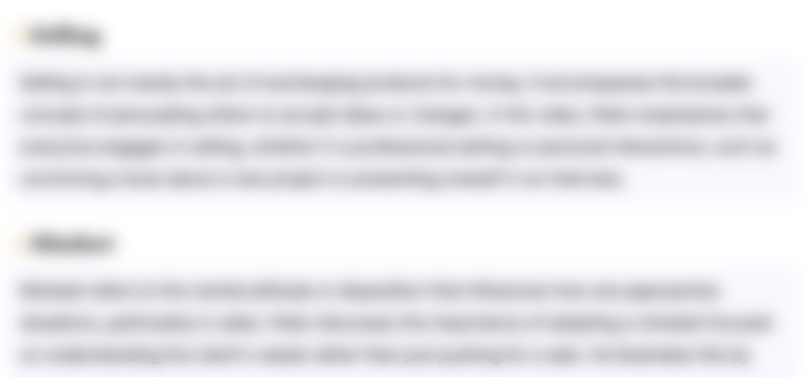
このセクションは有料ユーザー限定です。 アクセスするには、アップグレードをお願いします。
今すぐアップグレードHighlights
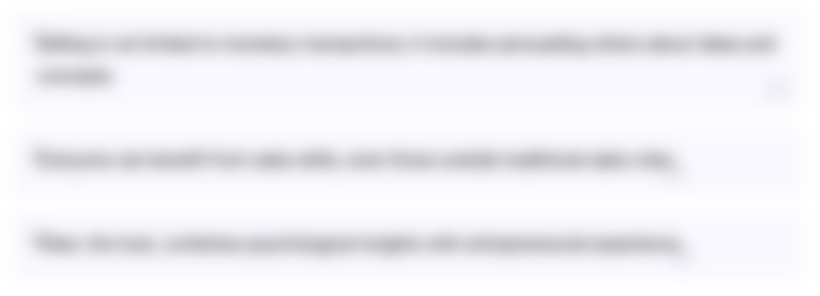
このセクションは有料ユーザー限定です。 アクセスするには、アップグレードをお願いします。
今すぐアップグレードTranscripts
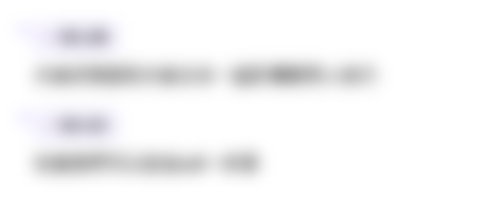
このセクションは有料ユーザー限定です。 アクセスするには、アップグレードをお願いします。
今すぐアップグレード関連動画をさらに表示
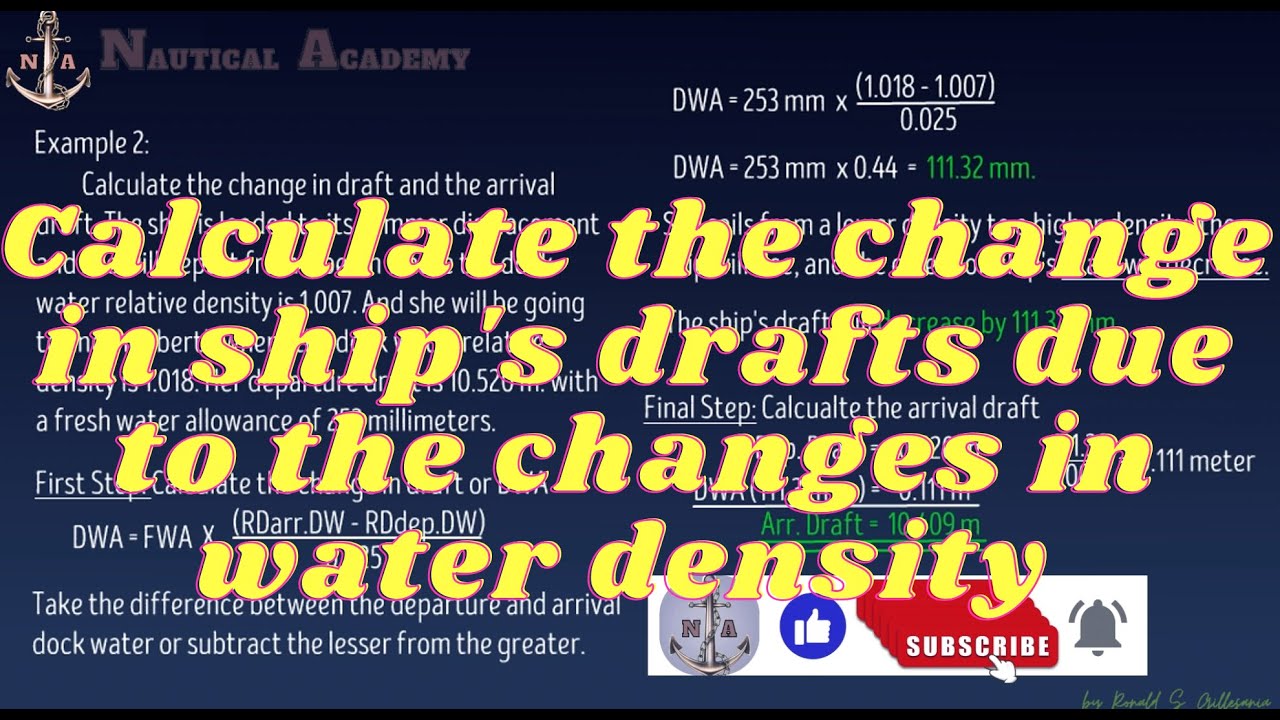
Calculate the Fresh Water Allowance & Dock Water Allowance II Change in Ship's Drafts due to Density

Training Session 14 05 02 2021 Payroll 2 employee termination 9

Part 1: NAJIS (Kajian Fathul Qarib) Bersama Ust. Busrah Latif, S.Sy., M.E
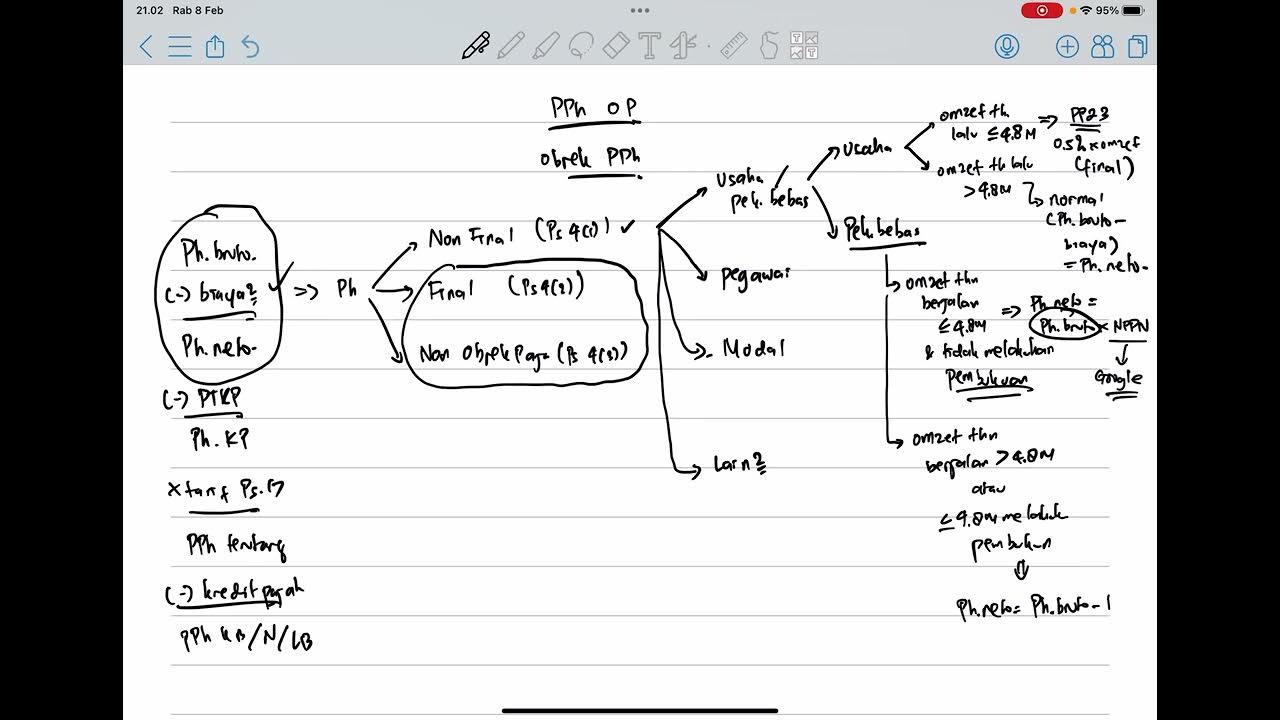
PPH Orang Pribadi (Update 2023) - 2. Objek Pajak

Payroll Orientation Part 1
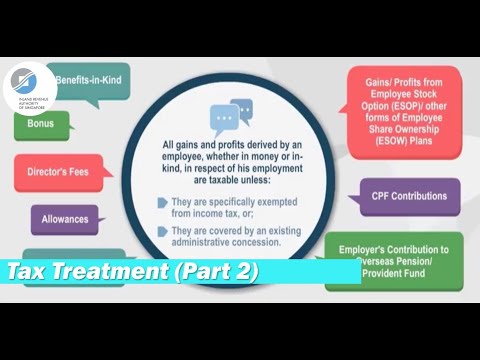
Tax Treatment of Remuneration Components (Part 2)
5.0 / 5 (0 votes)