The Manufacturing Process of Industrial Valves. 62 Years Old Cast Valve Factory in Korea
Summary
TLDRThis video provides an engaging and detailed walkthrough of the valve manufacturing process, from creating molds and cores to pouring molten steel and testing the final product. It highlights the precision involved, including adding coatings for a smooth surface, removing impurities, and conducting quality checks. The video also explains how valves are color-coded based on their application (e.g., red for fire hydrants, blue for water supply). With humor and a step-by-step approach, the video makes the complex process easy to follow and enjoyable to watch.
Takeaways
- ⚙️ The company has been manufacturing valves for 62 years and produces various types.
- 🏗️ The mold-making process starts with creating a valve pattern, using special sand that hardens within 10 minutes.
- 🔥 Molten steel is poured into the molds, with a focus on preventing leaks and ensuring smooth surfaces with special coatings.
- 🏖️ The core-making process is used to create hollow sections, allowing for water, steam, and gas to pass through the valve.
- ♻️ The sand used in the molds is recycled after the casting process, and the core breaks down naturally.
- 💥 After cooling for 8 hours, the valves undergo a shot blast process to trim and smooth the surface.
- 🔧 The final valve assembly involves precise processing, grinding, and drilling holes for bolts and assembly.
- 🧪 Valves undergo several tests, including pressure tests and leak detection using soap water.
- 🎨 Different colors are used to identify valve usage: red for fire hydrants, blue for water, and silver for steam.
- 📽️ The video was filmed by a South Korean company, and viewers are encouraged to like and subscribe.
Q & A
What is the purpose of the special sand used in the mold making process?
-The special sand is used to stamp the shape of the valve and hardens in 10 minutes to form the mold. It is also coated to provide a smooth surface and to protect the mold from extreme heat during the casting process.
Why is the core necessary in the valve casting process?
-The core is used to create hollow sections or cavities in the valve, allowing water, steam, and gas to pass through. It is installed within the mold, and the molten steel flows in the gap between the mold and the core.
What is the function of the molten steel supply holes and gas holes in the mold?
-The molten steel supply holes allow the molten metal to flow into the mold, while the gas holes allow gas to escape during the pouring process, preventing defects in the final casting.
Why is a special coating applied to the sand in both the mold and the core?
-The special coating ensures a smooth surface on the final product and protects the sand mold from the extreme heat of the molten steel. It also helps the core maintain its shape during the casting process.
What are the key steps in preparing the molten steel for casting?
-The molten steel is prepared by melting scrap metal, adding elements to improve its properties, removing impurities, checking its temperature, and pouring it into a ladle before filling the mold.
Why is it important to pour extra molten steel during the casting process?
-Extra molten steel is poured to account for contraction that occurs as the metal cools and solidifies. This ensures the mold is fully filled, preventing defects in the final product.
What happens after the molten steel has been poured into the mold?
-The molten steel is left to cool for 8 hours, after which the mold is opened. The sand core breaks down as it is made of sand and is recycled. The casting is then shot blasted to smooth the surface.
What is the purpose of the shot blast process?
-The shot blast process shoots tiny steel balls at the valve to remove any uneven surfaces and ensure the casting has a smooth, uniform finish.
What final tests are performed on the valve after the casting process?
-Final tests include a quality check, pressure testing, and using soap water to detect leaks. If bubbles appear, it indicates a leak that needs to be addressed.
How are different valve types distinguished based on their colors?
-Valves are color-coded based on their usage: red for fire hydrants, blue for water supply, and silver for steam. The purpose of the gray color remains unclear in the video.
Outlines
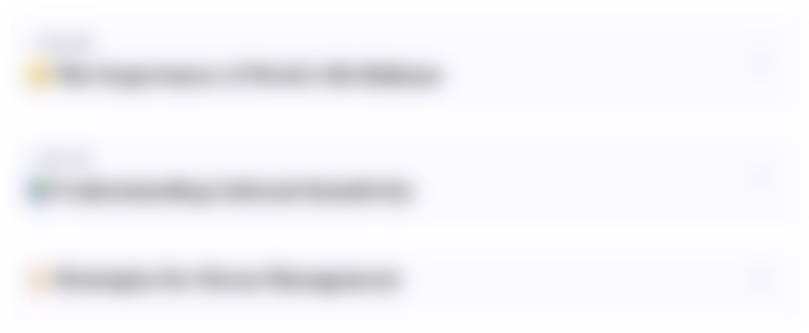
このセクションは有料ユーザー限定です。 アクセスするには、アップグレードをお願いします。
今すぐアップグレードMindmap
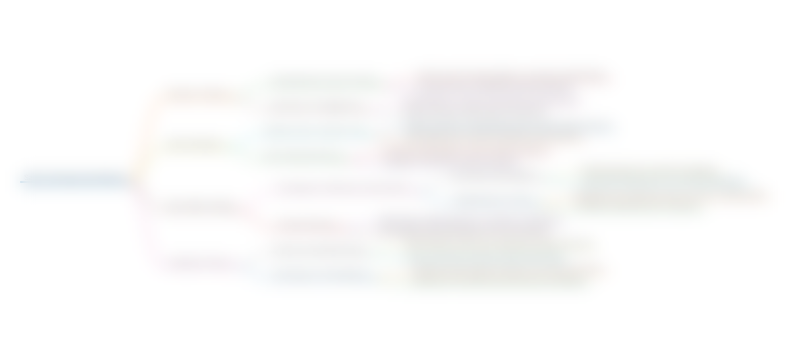
このセクションは有料ユーザー限定です。 アクセスするには、アップグレードをお願いします。
今すぐアップグレードKeywords
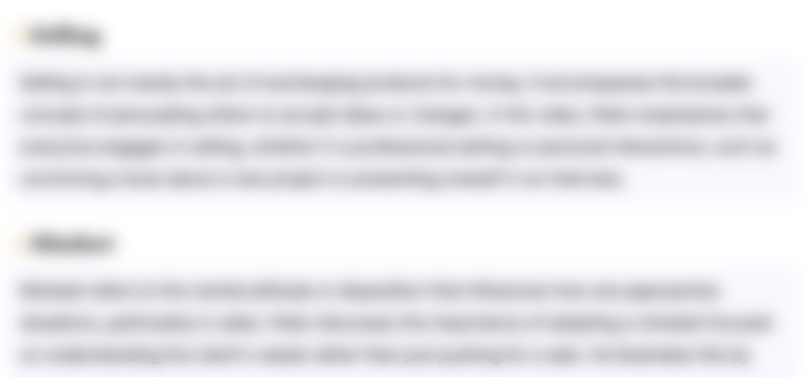
このセクションは有料ユーザー限定です。 アクセスするには、アップグレードをお願いします。
今すぐアップグレードHighlights
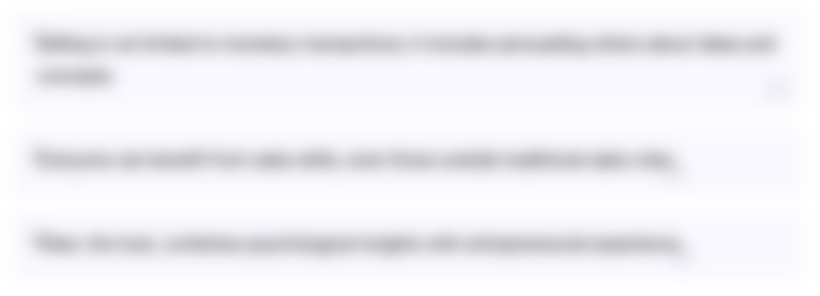
このセクションは有料ユーザー限定です。 アクセスするには、アップグレードをお願いします。
今すぐアップグレードTranscripts
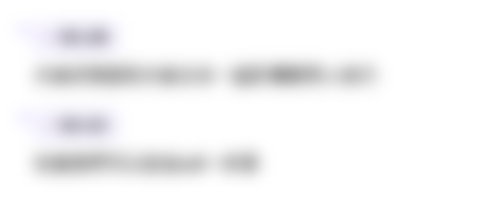
このセクションは有料ユーザー限定です。 アクセスするには、アップグレードをお願いします。
今すぐアップグレード関連動画をさらに表示

Proses Pengecoran
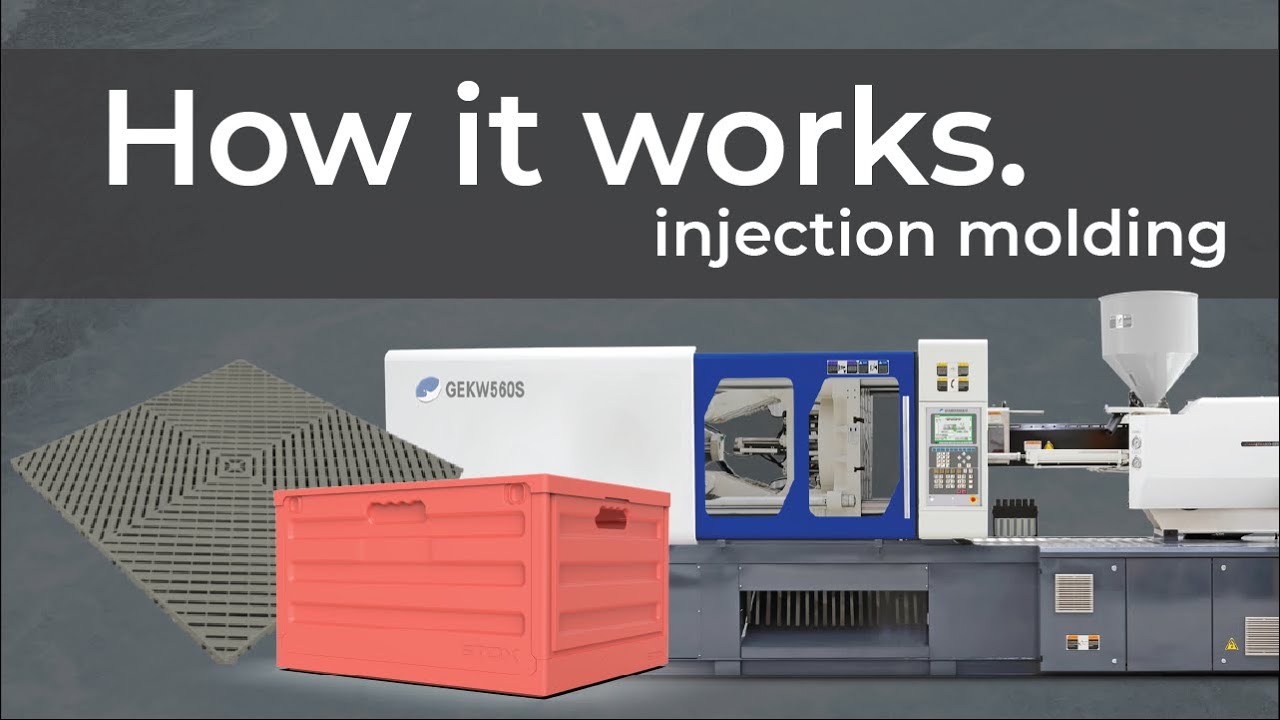
How Plastic Products are Made | The Injection Molding Process
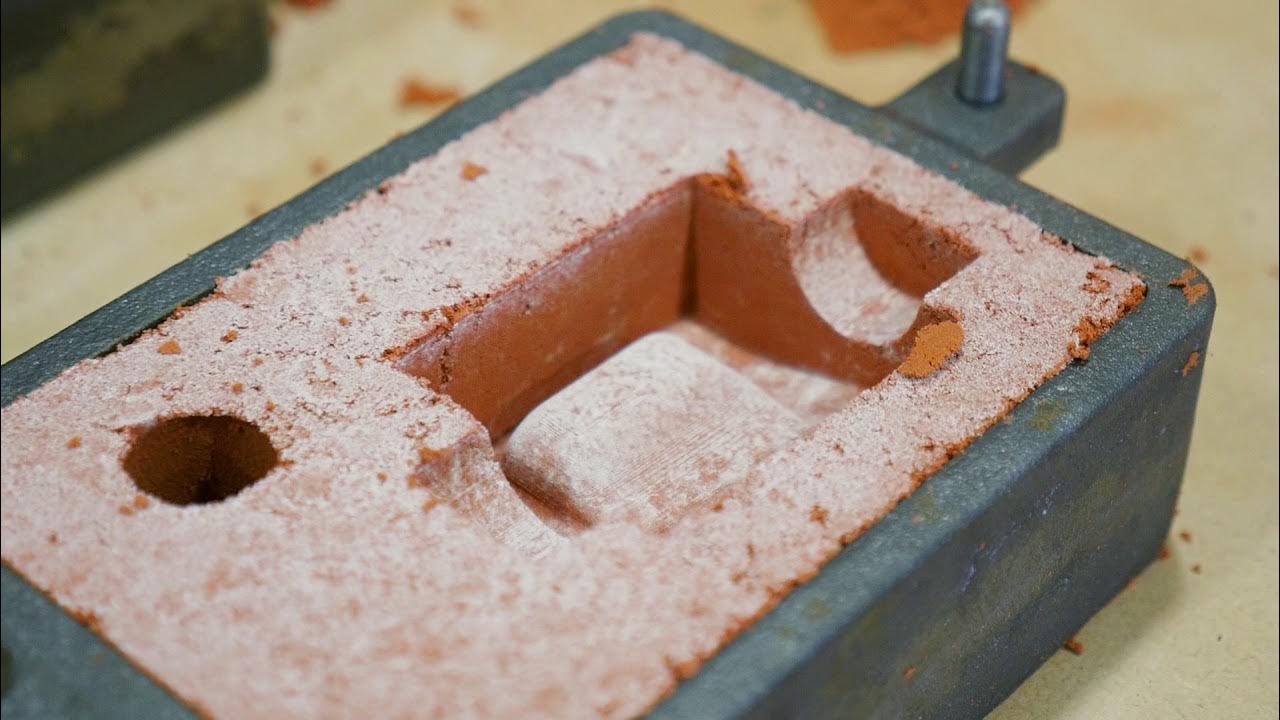
Casting Metal: showcasing the basics of casting and the Casting is the future Foundry Kit
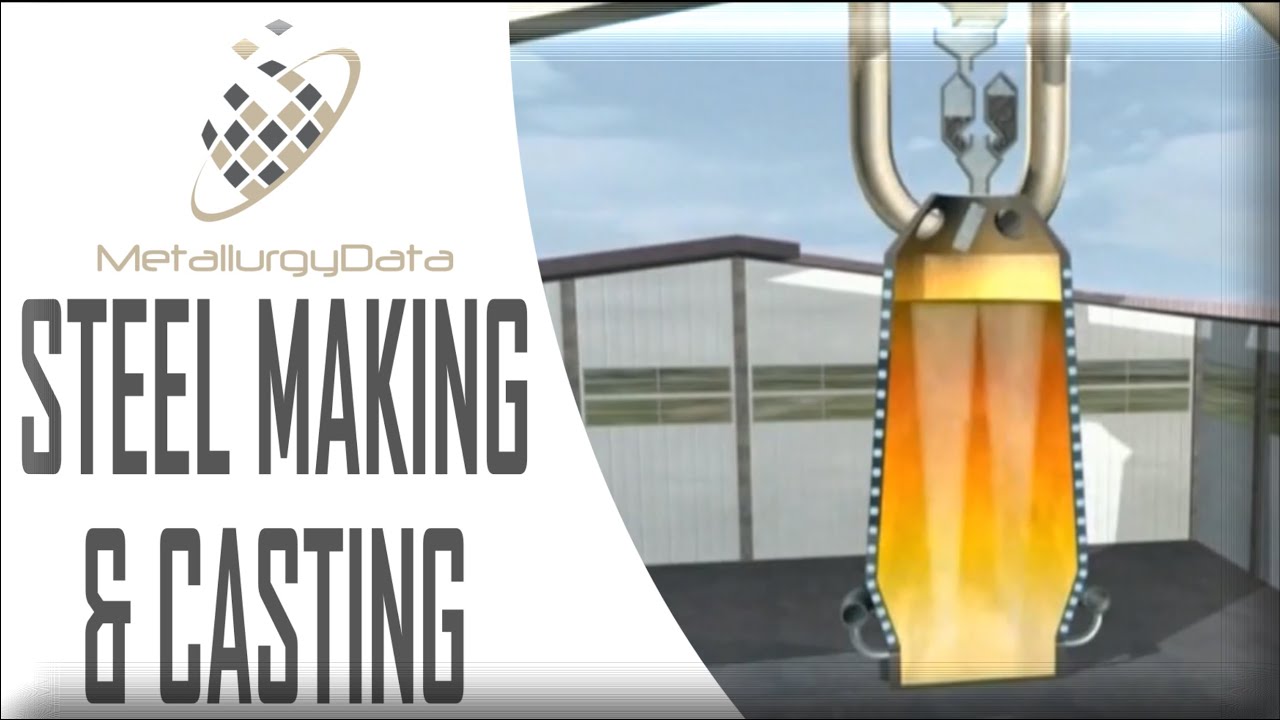
Steel Making and Casting (Principles of Metallurgy)
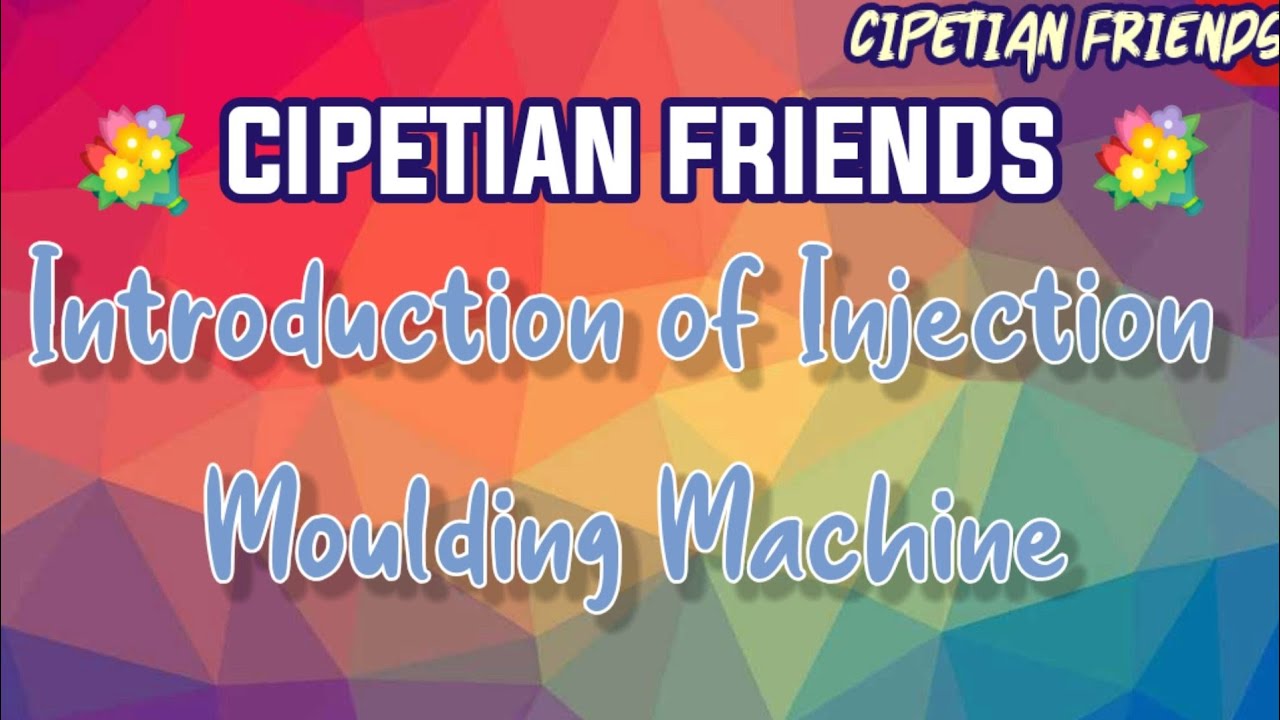
Introduction Of Injection Moulding Machine
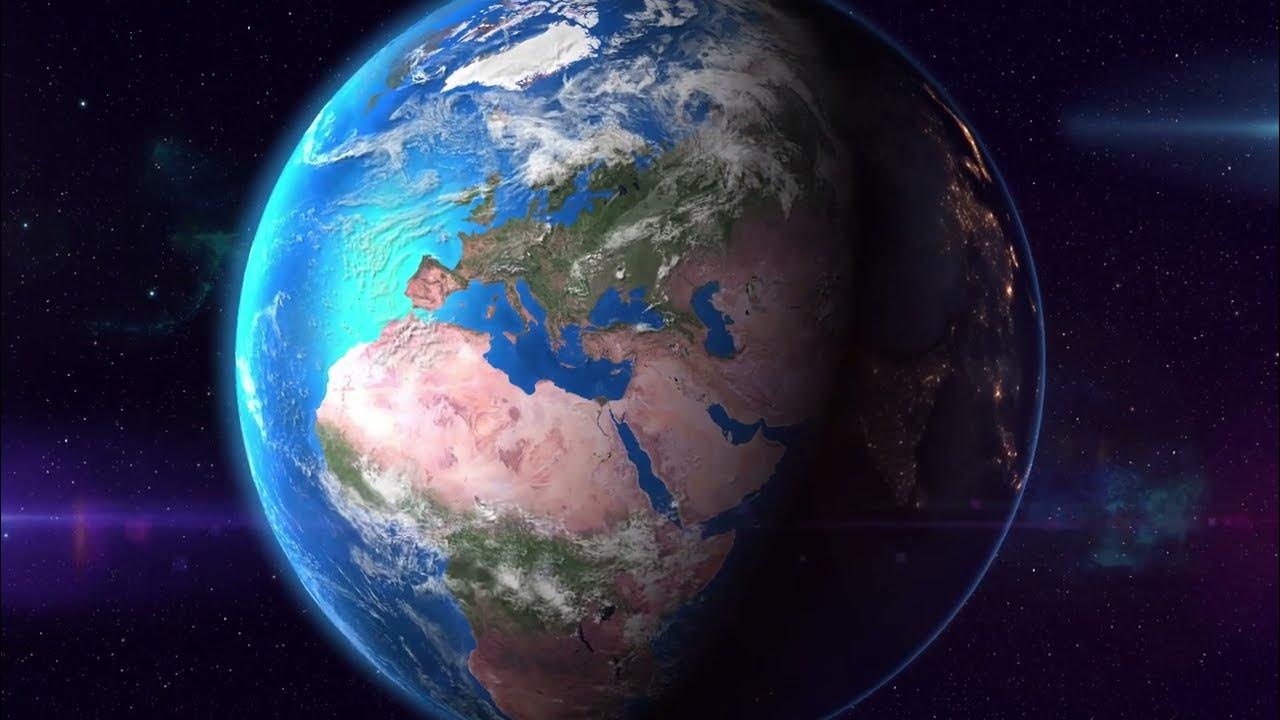
İsdemir Fabrikasında Çelik Üretim Süreci
5.0 / 5 (0 votes)