Ejemplo Costeo ABC
Summary
TLDRThe video covers the implementation of Activity-Based Costing (ABC) and its impact on pricing, product mix optimization, cost reduction, and process improvement. It discusses how to calculate direct and indirect costs for products, such as empanadas and arepas, by using cost drivers like machine hours and units produced. The process involves assigning costs to each product and calculating total and unit costs. Additionally, the video explores pricing strategies, determining breakeven points, and optimizing production to achieve profitability, offering valuable insights for administrative decision-making.
Takeaways
- 🔧 The ABC costing system helps in determining the right product mix and price fixation based on accurate cost calculations.
- 📉 ABC costing aids in identifying inefficiencies and reducing production costs by analyzing activities in the production process.
- 💡 It also allows for making informed decisions on product design and production processes based on cost-efficiency findings.
- 🥟 In the example, a company produces 600 empanadas and 800 arepas, requiring both direct and indirect cost assessments.
- 📊 Direct costs include $400,000 for empanada labor, $500,000 for arepa labor, $150,000 for empanada materials, and $200,000 for arepa materials.
- 🔨 Maintenance costs for machinery, based on 10,000 machine hours, are $600,000, while preparation of inputs costs $800,000, divided across 1,400 units produced.
- 💰 The cost of each empanada is calculated based on direct and indirect costs, leading to a total unit cost of $2,188 per empanada.
- 📦 For arepas, the total unit cost is calculated at $1,671, using a similar method of dividing direct and indirect costs.
- 📈 Based on these costs, the company can set break-even prices of $2,200 for empanadas and $1,700 for arepas.
- ⚖️ The company can use this information to determine optimal production quantities and adjust pricing for profitability.
Q & A
What is the ABC costing method?
-The ABC (Activity-Based Costing) method is a system used to allocate overhead costs more accurately by assigning costs based on specific activities required for production. It helps companies determine the true cost of each product by analyzing both direct and indirect costs.
What are some administrative decisions related to implementing the ABC costing method?
-Implementing ABC costing can lead to several key decisions, such as setting optimal pricing for products, determining the right product mix, reducing costs by optimizing activities, and redesigning products or production processes to minimize inefficiencies.
How can the ABC costing method impact product pricing?
-ABC costing helps determine accurate production costs for each product, allowing businesses to set prices that reflect the true cost and ensure profitability. This method considers both direct and indirect costs, enabling better pricing strategies.
What are the two main activities considered in the example provided in the script?
-The two main activities in the example are: 1) Maintenance of machinery, and 2) Preparation of inputs. These activities were used to allocate indirect costs based on hours of machinery used and the number of units produced, respectively.
How are direct costs for producing empanadas and arepas calculated in the example?
-Direct costs are calculated separately for each product. For empanadas, the direct labor cost is 400,000 pesos, and the direct material cost is 150,000 pesos. For arepas, the direct labor cost is 500,000 pesos, and the direct material cost is 200,000 pesos.
What is the base for allocating the indirect costs of machinery maintenance in the example?
-The base for allocating the indirect costs of machinery maintenance is the total hours of machinery used, which is 10,000 hours. Out of these, 7,000 hours are used for empanadas and 3,000 hours for arepas.
What is the base for allocating the indirect costs of input preparation?
-The base for allocating the indirect costs of input preparation is the total number of units produced, which is 1,400 units (600 empanadas and 800 arepas).
What is the cost unit for materials and direct labor for both products?
-The cost per unit of materials for both empanadas and arepas is 250 pesos. The direct labor cost per unit is 667 pesos for empanadas and 625 pesos for arepas.
How are the total and unit indirect costs calculated for each activity?
-For machinery maintenance, the indirect cost rate is 60 pesos per hour. For empanadas, the total is 420,000 pesos (7,000 hours), and for arepas, it's 180,000 pesos (3,000 hours). For input preparation, the rate is 571.43 pesos per unit. For empanadas, it's 342,857 pesos (600 units), and for arepas, 457,143 pesos (800 units).
What are the final total and unit costs for empanadas and arepas after adding direct and indirect costs?
-For empanadas, the total cost is 1,312,857 pesos, with a unit cost of 2,188 pesos. For arepas, the total cost is 1,337,143 pesos, with a unit cost of 1,671 pesos.
Outlines
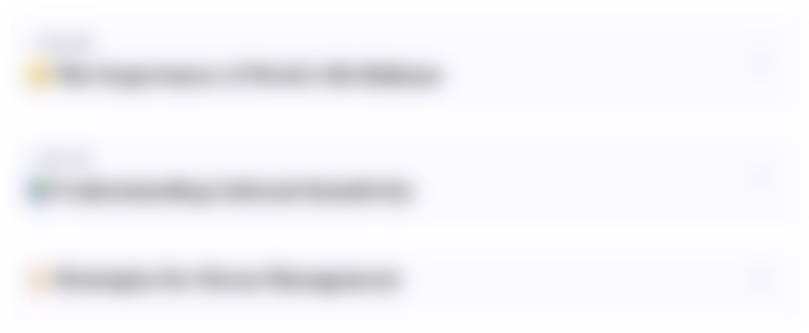
このセクションは有料ユーザー限定です。 アクセスするには、アップグレードをお願いします。
今すぐアップグレードMindmap
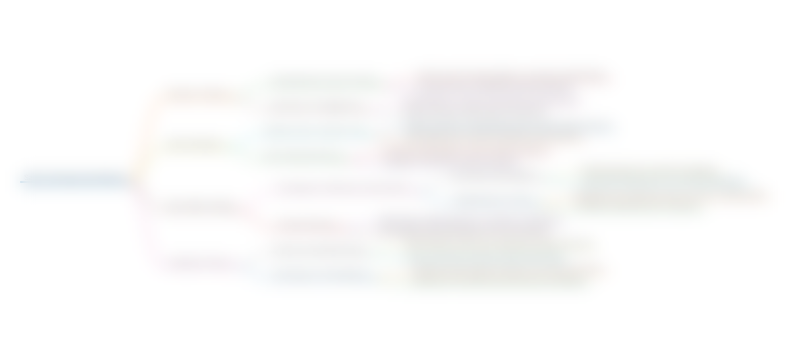
このセクションは有料ユーザー限定です。 アクセスするには、アップグレードをお願いします。
今すぐアップグレードKeywords
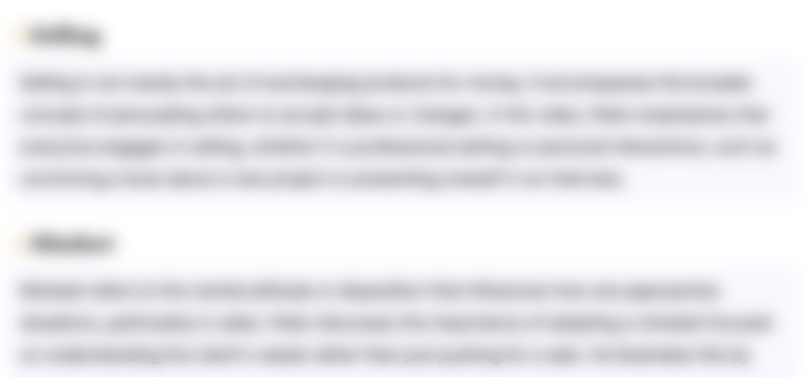
このセクションは有料ユーザー限定です。 アクセスするには、アップグレードをお願いします。
今すぐアップグレードHighlights
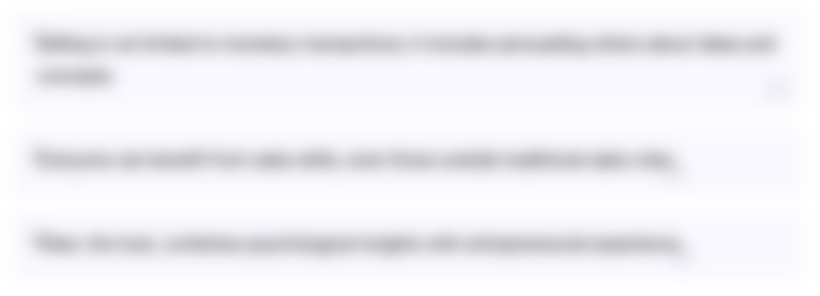
このセクションは有料ユーザー限定です。 アクセスするには、アップグレードをお願いします。
今すぐアップグレードTranscripts
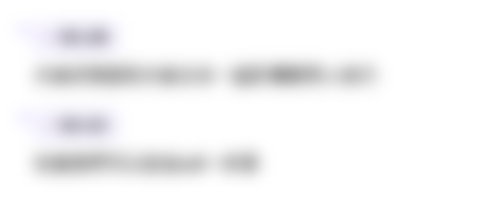
このセクションは有料ユーザー限定です。 アクセスするには、アップグレードをお願いします。
今すぐアップグレード5.0 / 5 (0 votes)