Glasherstellung - Das Floatverfahren (Saint-Gobain)
Summary
TLDRThe script delves into the intricate process of glass manufacturing, highlighting its ubiquitous yet invisible nature in modern applications. Key ingredients like quartz sand, soda, and lime are crucial, with dolomite added for building and automotive glass. The float process is central, detailing the mixing, melting, and slow cooling stages. It emphasizes the float plant's role in producing high-quality, cost-effective glass, showcasing the importance of the float bath and the use of tin to create a smooth, planar glass surface. The script concludes by noting the adaptability of float glass for various applications, such as thermal insulation and soundproofing.
Takeaways
- 🏭 Glass is a material with a wide range of applications and is produced through an intricate process.
- 💠 The main raw materials for glass production are quartz sand, soda, and lime, with dolomite added for building and vehicle glass.
- 🔥 The raw materials are mixed and melted at temperatures between 800 to 900°C, with the melting process being observable only through special glasses.
- 🌡 The melting process involves three areas: melting of the mixture, refining at up to 1560°C, and cooling to around 1100°C.
- 💧 The float process is used for industrial glass production, where the glass is formed by flowing over a bed of molten tin.
- 🔄 The float process involves a non-visible transition area between the melting pot and the float bath, facilitated by a lip stone.
- 🌌 The principle of glass spreading evenly over the tin bath is similar to how two immiscible liquids like chloroform and glycerin form a smooth separation layer.
- 📏 The thickness of the glass is controlled by the speed at which the molten glass is drawn over the tin bath, managed by top rollers.
- 🌡️ The cooling process in the float bath is carefully controlled to prevent stress in the glass, with the temperature dropping from 1100°C to 600°C.
- 🛠️ The flat glass is then slowly cooled in a roller cooler to room temperature, ensuring a stress-free cooling process over a length of 160 meters.
- ♻️ Defective areas are identified and marked for automatic sorting out, and the glass is cut to size for transportation and potential recycling.
Q & A
What are the main raw materials used in glass manufacturing?
-The main raw materials for glass manufacturing are quartz sand, soda, and lime. For building and vehicle glass, dolomite is also added as an additional raw material.
What is the float process in glass manufacturing?
-The float process is an industrial method used to produce flat glass of a high quality standard. It involves floating molten glass on a bed of molten tin to create a flat, parallel surface.
Why is dolomite added to the raw materials for building and vehicle glass?
-Dolomite is added to the raw materials for building and vehicle glass to improve the chemical composition and physical properties of the final product.
What causes the brownish-red color of the glass mixture?
-The brownish-red color of the glass mixture is due to small amounts of iron oxide added to the raw materials.
How is the glass mixture melted and at what temperature?
-The glass mixture is melted in a melting furnace at temperatures between 800 and 900°C. The melting process begins when the quartz sand melts at around 1450°C.
What is the purpose of the three different areas in the melting furnace?
-The melting furnace has three areas: the first for melting the mixture, the second for refining at up to 1560°C to homogenize the glass melt and remove gas bubbles and streaks, and the third for cooling the melt to about 1100°C.
How does the float bath work in the glass manufacturing process?
-The float bath works by utilizing the different densities of tin and glass. The molten glass spreads evenly over the entire tin bath, floating on the surface due to the density difference.
Why is tin used in the float bath?
-Tin is used in the float bath because it remains liquid at 600°C and does not evaporate even at 1100°C, which is necessary for the glass to cool and solidify evenly.
How is the thickness of the glass controlled during the float process?
-The thickness of the glass is controlled by the speed at which the molten glass is drawn across the tin bath and managed with the help of top rollers.
What happens to the glass after it leaves the float bath?
-After leaving the float bath, the glass is slowly cooled in a roller cooler from 600°C to 200°C over a length of 160 meters to ensure stress-free cooling.
How is the quality of the glass checked after it is formed?
-The quality of the glass is checked for inclusions, bubbles, and streaks. Defective areas are marked and later automatically sorted out for potential recycling back into the melting process.
Outlines
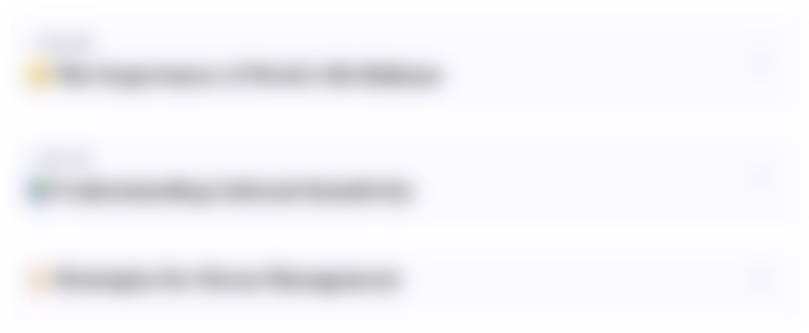
このセクションは有料ユーザー限定です。 アクセスするには、アップグレードをお願いします。
今すぐアップグレードMindmap
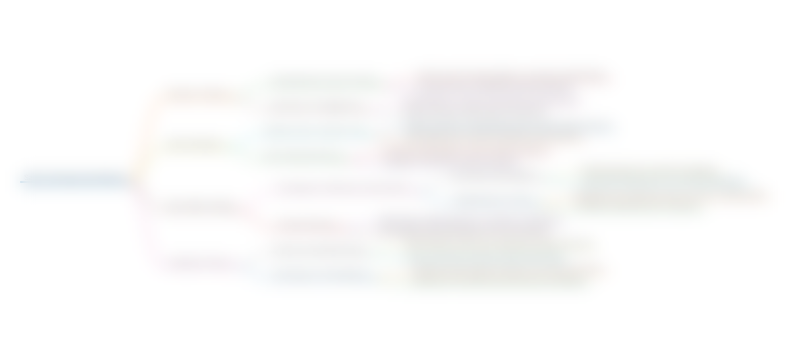
このセクションは有料ユーザー限定です。 アクセスするには、アップグレードをお願いします。
今すぐアップグレードKeywords
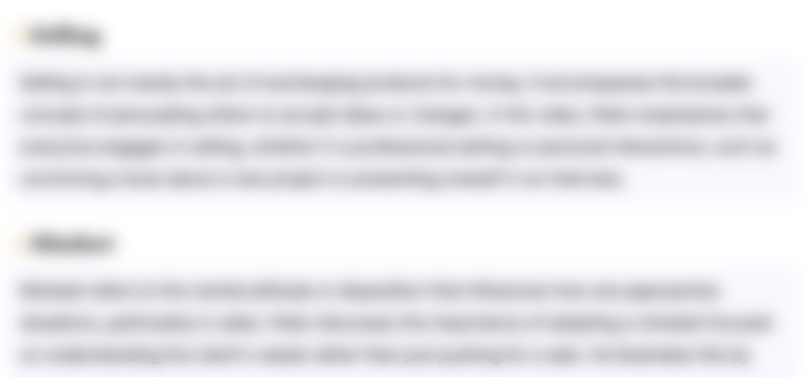
このセクションは有料ユーザー限定です。 アクセスするには、アップグレードをお願いします。
今すぐアップグレードHighlights
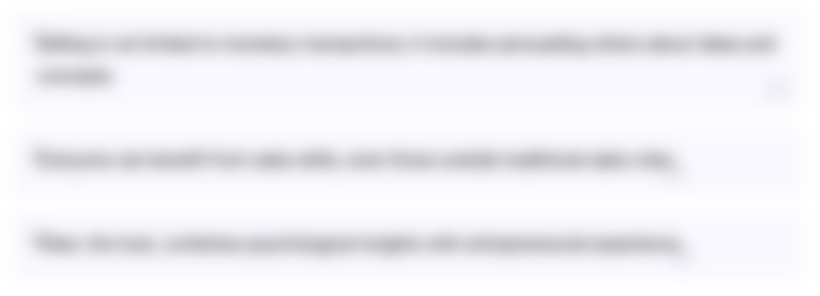
このセクションは有料ユーザー限定です。 アクセスするには、アップグレードをお願いします。
今すぐアップグレードTranscripts
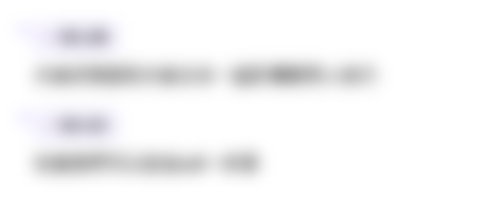
このセクションは有料ユーザー限定です。 アクセスするには、アップグレードをお願いします。
今すぐアップグレード5.0 / 5 (0 votes)