How To Make Rectangle Tube Bends WITHOUT a Bender in ANY Size + Radius!!
Summary
TLDRIn this video, the host demonstrates how to create a rectangle tube bend using a DIY approach, perfect for custom fabrication projects. Despite the challenging 'hard way' method, the tutorial shows a step-by-step process of bending hollow structural steel into a tube donut. The host uses spacers and a welding tank to achieve the bend, emphasizing the importance of smooth cuts and consistent welding for a professional finish. The result is a reusable template for creating custom tube bends, showcasing creativity and resourcefulness in metalworking.
Takeaways
- 🎥 The video is a premiere of 'Metal Reborn' at a twilight drive-in, which has been a huge success despite the weather.
- 🌐 'Metal Reborn' is also available online for viewing at metalreborn.com.
- 🔩 The video tutorial focuses on making a rectangle tube bend the 'hard way', which involves more material to bend compared to the 'easy way'.
- 🛠️ The presenter demonstrates how to create a tube donut using welding techniques to bend rectangle tubing.
- 👷♂️ The motivation for the video is to explain how the floor bracing for a model 8 was made, which required custom bending of rectangle tubing.
- 🛠️ The process involves creating spacers to hold materials at the right height for bending.
- 💡 A welding tank is suggested as an alternative to a roller for bending flat bar into circles, showing creativity in the absence of specialized tools.
- 🔨 The importance of smooth cutting with a plasma cutter is emphasized to minimize slag and ensure a nice, clean circle.
- 🔩 Clamping and spacers are crucial for accurate assembly of the rectangle tube.
- 🔥 Welding is done using a small 110 welder, demonstrating that it's possible to achieve quality results with basic equipment.
- ✂️ After welding, the tube is cut and ground to create a smooth, finished tube bend that can be used for various structures.
Q & A
What is the event being discussed in the script?
-The event being discussed is the premiere of 'Metal Reborn' at a drive-in theater.
What is the website mentioned for checking out 'Metal Reborn' online?
-The website mentioned is metalreborn.com.
What is the purpose of the video tutorial in the script?
-The purpose of the video tutorial is to teach viewers how to make a rectangle tube bend using a homemade method.
What is referred to as 'the hard way' in the context of bending rectangle tubing?
-Bending rectangle tubing in a direction that requires more material to bend is referred to as 'the hard way'.
What is a 'tube donut' as mentioned in the script?
-A 'tube donut' is a term used in the script to describe a circular shape made from bending a rectangle tube, which can be cut into various angles for different structures.
What is the motivation behind creating the tube donut as explained in the script?
-The motivation is to replicate the floor bracing for the model 8, which requires bent 1x2 rectangle tubing.
What is the significance of the welding tank in the script?
-The welding tank is used as a substitute for a roller to help bend flat bar into a circle without specialized equipment.
What is the importance of being smooth when using a plasma cutter as mentioned in the script?
-Being smooth with a plasma cutter is important to achieve a nice, clean cut with less slag and easier cleanup.
What technique does the script suggest for welding corner joints?
-The script suggests using the whip and pause welding technique for corner joints, which involves welding on the corner edge to create a radius on the weld.
What is the reason for leaving a gap when cutting the sizes for the weld?
-Leaving a gap is important for structural welds to ensure that the joint can be filled with weld material effectively.
What are the steps involved in grinding the weld after it has been made?
-The steps include grinding the flats, grinding the corner at a 45-degree angle, and then rounding it out to be consistent all the way around.
Outlines
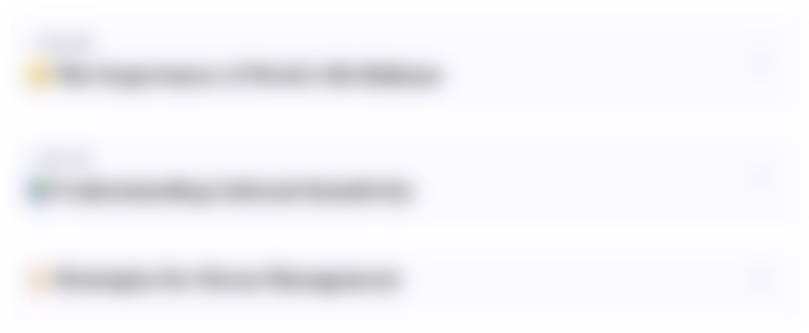
Cette section est réservée aux utilisateurs payants. Améliorez votre compte pour accéder à cette section.
Améliorer maintenantMindmap
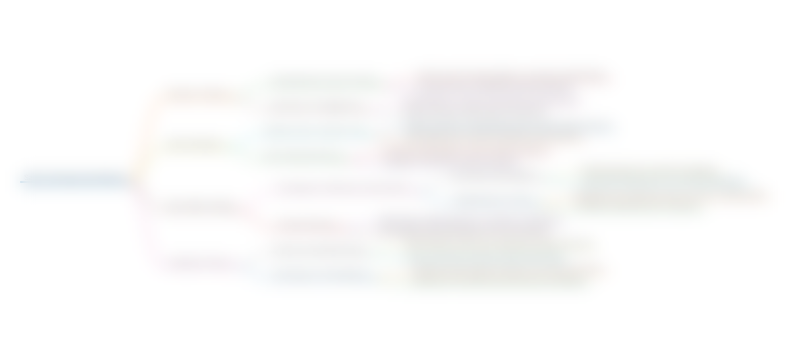
Cette section est réservée aux utilisateurs payants. Améliorez votre compte pour accéder à cette section.
Améliorer maintenantKeywords
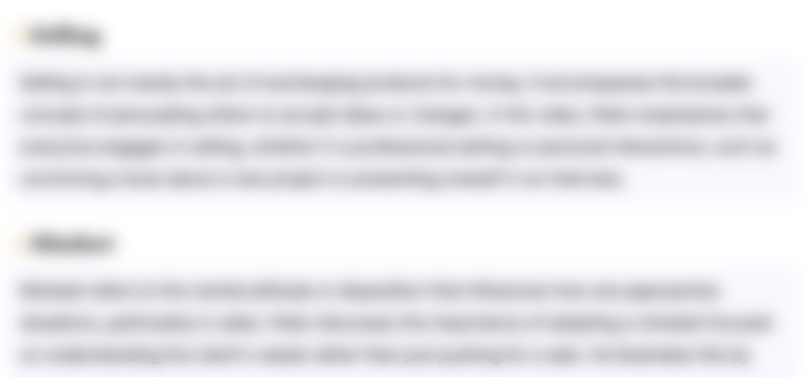
Cette section est réservée aux utilisateurs payants. Améliorez votre compte pour accéder à cette section.
Améliorer maintenantHighlights
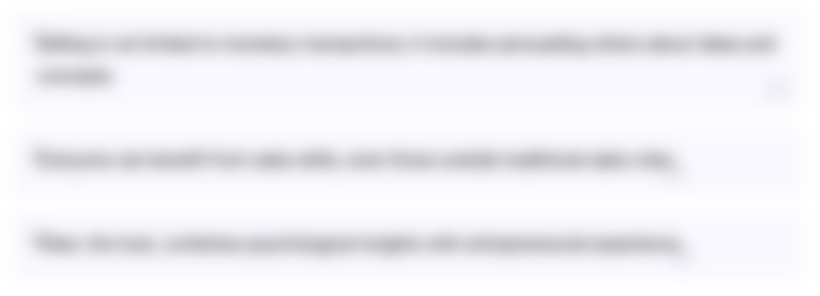
Cette section est réservée aux utilisateurs payants. Améliorez votre compte pour accéder à cette section.
Améliorer maintenantTranscripts
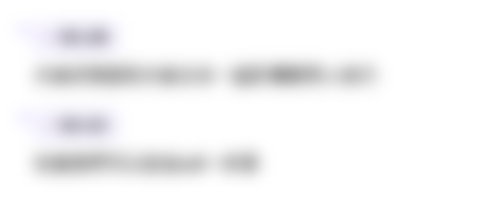
Cette section est réservée aux utilisateurs payants. Améliorez votre compte pour accéder à cette section.
Améliorer maintenantVoir Plus de Vidéos Connexes
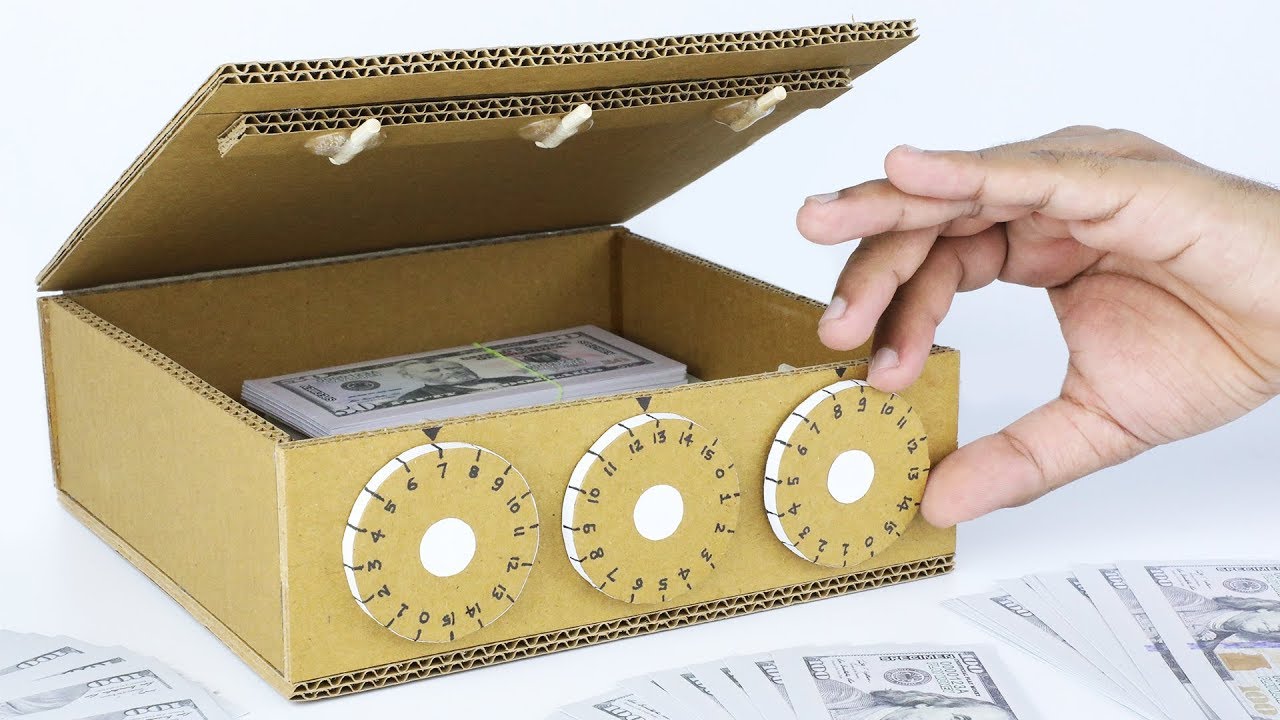
How to make safe using Cardboard
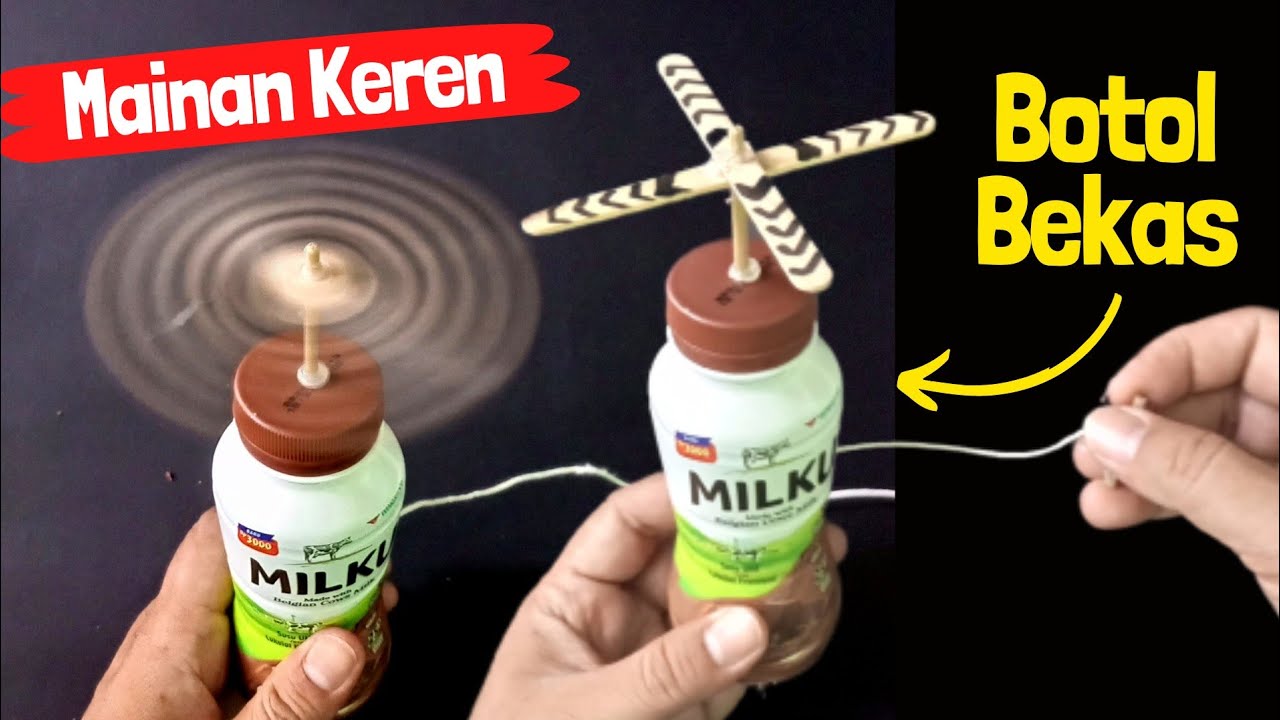
Cara Membuat Mainan Dari Botol Bekas !! Ide Kreatif, Bottle Craft
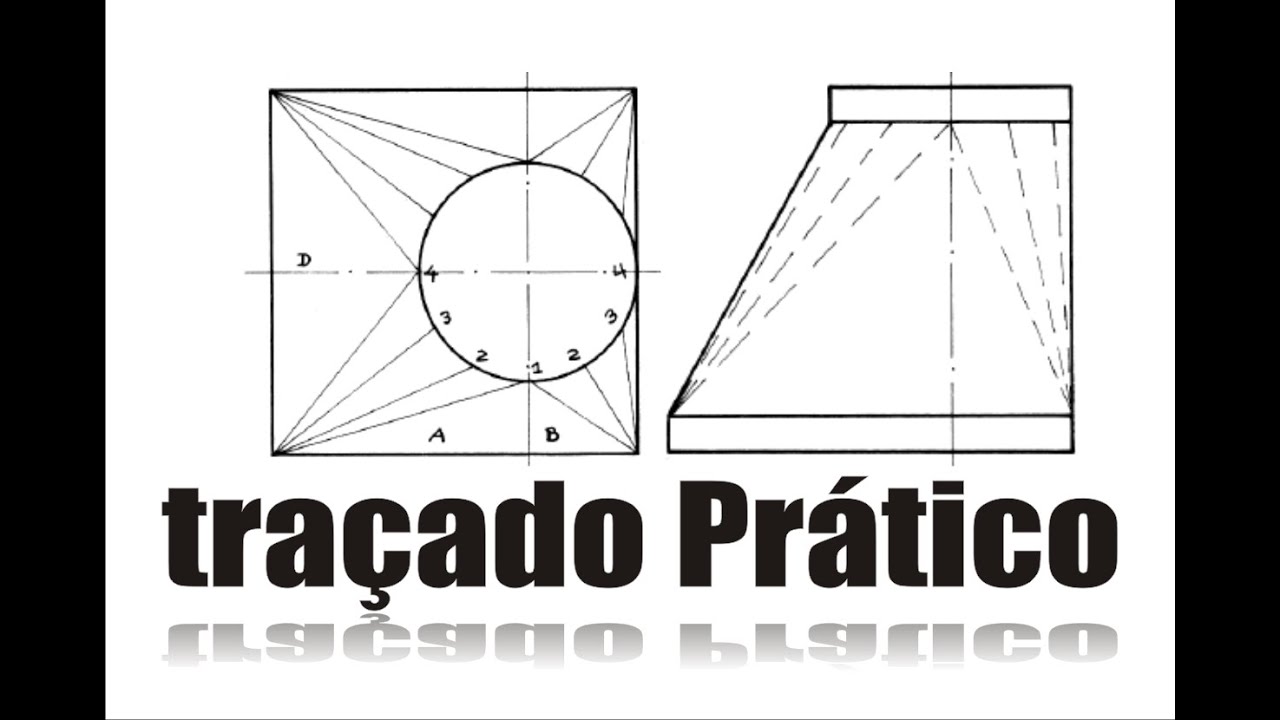
Quadrado p/ Redondo Excêntrico - Traçado de Caldeiraria

Kata Mama Senja Sumpah Gampang Banget | Meronce Manik

Orderan Langka ! Ampe 3Jt ... Bikin Papan Nama Ruangan / Kelas Untuk SMP Lab
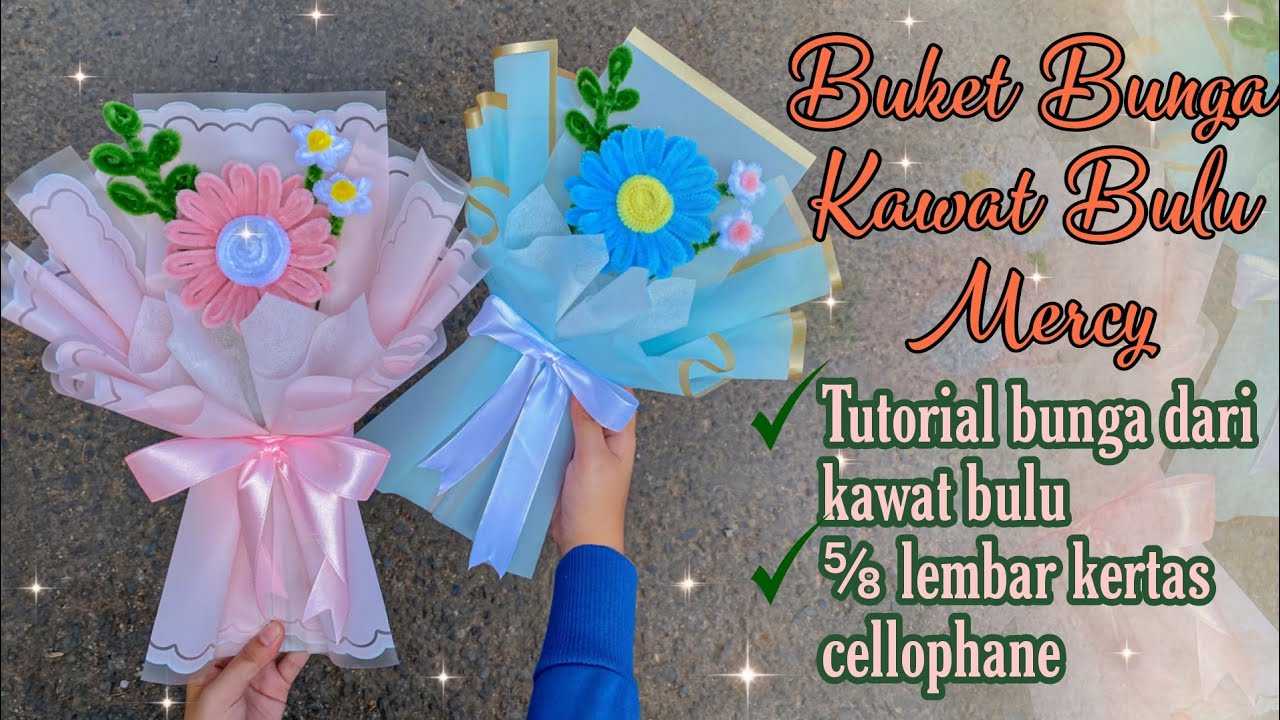
BUKET BUNGA DARI KAWAT BULU MERCY WRAPPING ⅝ LEMBAR KERTAS CELLOPHANE || PIPE CLEANER FLOWER BOUQUET
5.0 / 5 (0 votes)