Prinsip Dasar Ultrasonic Testing 2
Summary
TLDRThis video script explains the principles of ultrasonic wave generation using piezoelectric materials, focusing on their role in non-destructive testing (NDT). It covers how electrical signals cause piezoelectric crystals to vibrate and generate ultrasonic waves, which are used to detect material flaws in processes like welding. The script also discusses how the angle of wave propagation affects wave types (longitudinal and shear), and how thickness influences detection. The content highlights the advantages of ultrasonic testing for thicker materials and guides learners to further explore the topic through interactive online tools and practical applications.
Takeaways
- 😀 Piezoelectric materials vibrate when an electric current passes through them, generating ultrasonic waves.
- 😀 Ultrasonic waves are crucial for industrial applications like welding inspections, where they detect internal flaws in materials.
- 😀 The frequency of ultrasonic waves can reach up to 4 million vibrations per second, making them highly efficient.
- 😀 The propagation of ultrasonic waves can be influenced by the angle at which the transducer is set (ranging from 5° to 70°).
- 😀 At lower angles (5°-30°), longitudinal waves dominate, while shear waves appear at higher angles (above 30°).
- 😀 For effective material inspection, ultrasonic waves are most effective for materials that are at least 12 mm thick.
- 😀 Ultrasonic inspection faces challenges in detecting imperfections in materials thinner than 8-9 mm, especially in near-field areas.
- 😀 The ultrasonic inspection technique can detect flaws in materials in real-time, which is crucial for quality control in industries.
- 😀 Different material thicknesses and properties (e.g., metal type) affect the behavior and effectiveness of ultrasonic wave propagation.
- 😀 The presentation encourages self-learning through online tools and resources, enabling independent study and exploration of ultrasonic inspection principles.
- 😀 For successful ultrasonic inspections, understanding the theoretical principles of wave propagation, material thickness, and transducer setup is vital.
Q & A
What is a piezoelectric material and how does it work in ultrasonic wave generation?
-A piezoelectric material generates ultrasonic waves when an electrical charge is applied. These materials expand and contract rapidly when an electrical current passes through them, producing vibrations that turn into ultrasonic waves.
How fast can a piezoelectric material vibrate when generating ultrasonic waves?
-A piezoelectric material can vibrate up to 4 million times per second, creating high-frequency ultrasonic waves. These vibrations are fast and efficient, allowing for precise wave propagation.
What is the difference between longitudinal and shear ultrasonic waves?
-Longitudinal waves involve particle movement along the direction of wave propagation, whereas shear waves cause particles to move perpendicular to the direction of wave propagation. Longitudinal waves are used for deeper inspection, while shear waves are used for surface-level flaw detection.
How does the angle of the ultrasonic transducer affect wave propagation?
-The angle at which the ultrasonic transducer is positioned determines the type of wave generated. At lower angles (e.g., 5°–20°), longitudinal waves dominate, while at higher angles (above 30°), only shear waves are detectable.
Why is it important to consider the angle when performing ultrasonic testing on materials?
-The angle influences the type and effectiveness of the ultrasonic waves in detecting flaws. For instance, angles below 30° produce both longitudinal and shear waves, but above 30°, only shear waves are detectable, which may be crucial depending on the inspection needs.
What does the term 'nearfield' refer to in ultrasonic testing?
-Nearfield refers to the area very close to the ultrasonic transducer where waves are poorly detected due to interference and insufficient penetration. It is essential to avoid performing tests in the nearfield area to ensure accurate results.
What is the 'farfield' and why is it significant in ultrasonic testing?
-Farfield is the area further away from the transducer where ultrasonic waves propagate effectively, allowing for accurate detection of flaws and material characteristics. It is the preferred zone for inspection during ultrasonic testing.
What is the minimum material thickness recommended for effective ultrasonic testing?
-For accurate ultrasonic testing, the material thickness should typically be at least 8–9 mm. For materials thinner than this, ultrasonic waves might not penetrate effectively, making it difficult to detect defects.
How does material thickness affect the ability to detect defects with ultrasonic waves?
-Thicker materials allow for better detection because ultrasonic waves can propagate further without significant attenuation. In contrast, thin materials might fall within the nearfield, making defect detection unreliable.
What is the typical frequency range used in ultrasonic testing for welding inspections?
-The typical frequency for ultrasonic testing in welding inspections is around 5 MHz to 10 MHz. Lower frequencies are used for thicker materials, while higher frequencies are used for finer resolution in thinner materials.
Outlines
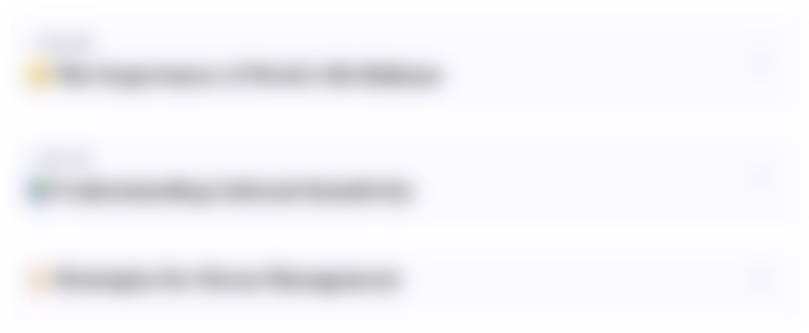
Esta sección está disponible solo para usuarios con suscripción. Por favor, mejora tu plan para acceder a esta parte.
Mejorar ahoraMindmap
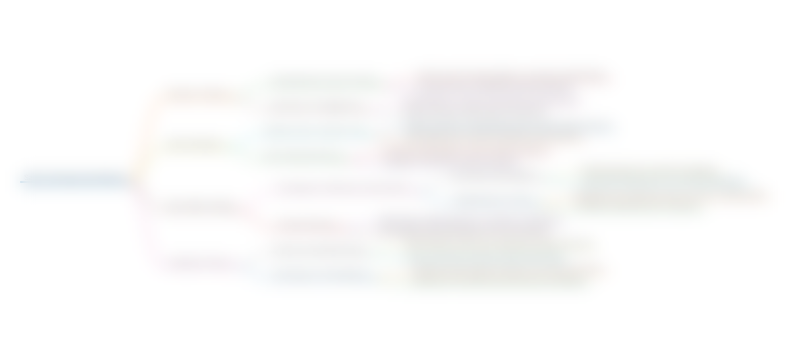
Esta sección está disponible solo para usuarios con suscripción. Por favor, mejora tu plan para acceder a esta parte.
Mejorar ahoraKeywords
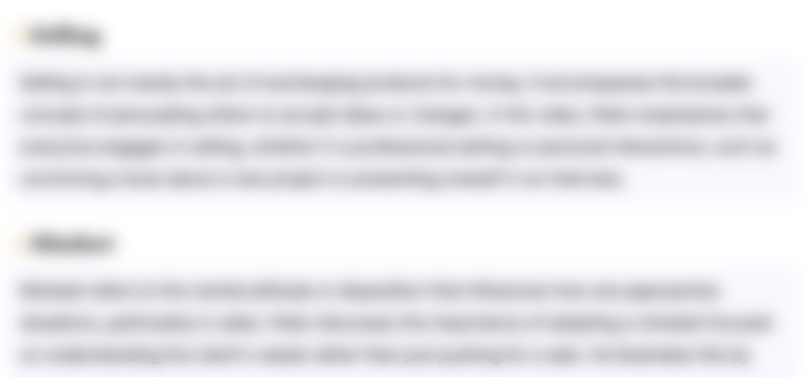
Esta sección está disponible solo para usuarios con suscripción. Por favor, mejora tu plan para acceder a esta parte.
Mejorar ahoraHighlights
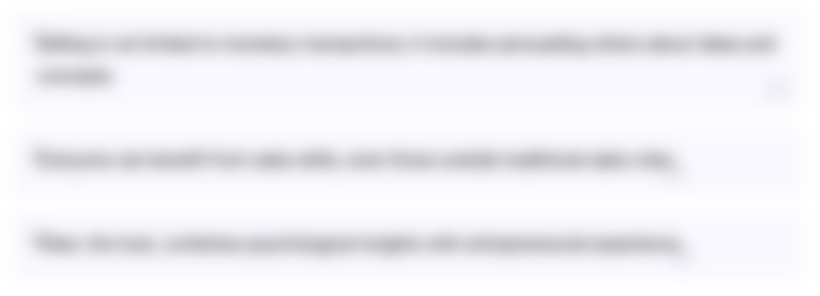
Esta sección está disponible solo para usuarios con suscripción. Por favor, mejora tu plan para acceder a esta parte.
Mejorar ahoraTranscripts
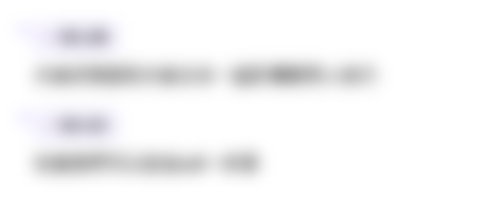
Esta sección está disponible solo para usuarios con suscripción. Por favor, mejora tu plan para acceder a esta parte.
Mejorar ahora5.0 / 5 (0 votes)