Quality Control in Electronics Manufacturing
Summary
TLDRZ-axis is committed to continuous improvement in quality, surpassing ISO 9001-2015 standards. By integrating internal systems, inspections at every stage, and tools like the Z-axis Inspection Protocol (ZIP), they ensure exceptional product quality and minimize risks. Their focus on first pass yield and root cause analysis enhances product consistency. With a dedicated machine shop, skilled employees, and thorough training, Z-axis delivers fast, reliable solutions. Through customer feedback and ongoing refinement, Z-axis strives to meet and exceed expectations, making quality an integral part of every process.
Takeaways
- 😀 Z-axis prioritizes continuous improvement, using ISO 9001:2015 as a foundation for quality management.
- 😀 Z-axis exceeds ISO 9001:2015 requirements by implementing advanced internal systems that enhance accessibility and usability of information.
- 😀 The Z-axis inspection protocol (ZIP) ensures real-time inspections, reducing risks and improving product quality at each stage of production.
- 😀 Z-axis emphasizes improving first pass yield to ensure higher product quality and quicker project turnaround times.
- 😀 The company's troubleshooting database logs all non-conformities, identifying trends and enabling quick resolution of recurring issues.
- 😀 Z-axis employs process fixture and validation procedures to maintain consistency in tasks like crimping cables and stripping wires.
- 😀 In-house manufacturing capabilities are strengthened by Z-axis's own machine shop for creating jigs, a feature many electronic manufacturers lack.
- 😀 Calibration of instruments and equipment, like multimeters and reflow ovens, is part of Z-axis's commitment to accuracy and quality.
- 😀 Root cause analysis is used to implement corrective and preventative actions, ensuring continuous improvement even when no longer required by the latest ISO standards.
- 😀 Paperless processes, such as automatic product labels and shipping documents, are standard in Z-axis to minimize human error and increase efficiency.
Q & A
What is the primary focus of Z-Axis when it comes to quality management?
-Z-Axis focuses on continuous improvement and exceeding the ISO 9001:2015 standard to deliver high-quality products to their customers and suppliers. Their quality management system (QMS) is always evolving to provide growing benefits.
How does Z-Axis go beyond ISO 9001:2015 compliance?
-Z-Axis goes beyond ISO 9001:2015 by using internal systems that are searchable, shareable, and user-friendly. These systems ensure that skilled employees have access to the information they need, and experienced engineers are readily available for support.
What is the Z-Axis Inspection Protocol (ZIP), and how does it help in quality management?
-The Z-Axis Inspection Protocol (ZIP) allows for the easy recording and retrieval of critical-to-quality (CTQ) dimensions. ZIP is used for inspections at multiple stages, including incoming, in-process, and outgoing inspections, minimizing risk throughout the production process.
Why does Z-Axis focus on improving first pass yield?
-Z-Axis focuses on improving first pass yield because a higher first pass yield indicates that a greater percentage of the products pass the test the first time, which signifies better product quality and shorter project timelines.
How does the troubleshooting database contribute to quality at Z-Axis?
-The troubleshooting database helps Z-Axis track and analyze non-conforming products, identifying trends and offering insights into current issues. This tool ensures that past problems, such as soldering issues, are addressed to prevent future defects.
What role do process fixtures and validation procedures play in Z-Axis's operations?
-Process fixtures and validation procedures at Z-Axis ensure consistency in tasks like crimping cables and stripping wire jacketing. These steps help maintain the high quality of the manufacturing process.
How does Z-Axis ensure consistency in their manufacturing process?
-Z-Axis ensures consistency by calibrating instruments like multimeters and equipment such as reflow ovens. This attention to detail in calibration helps maintain the accuracy and reliability of their manufacturing processes.
What is the significance of root cause analysis at Z-Axis?
-Root cause analysis is essential at Z-Axis for identifying and addressing defects in products. It helps them prepare corrective and preventative action plans, ensuring long-term improvement in product quality.
How does Z-Axis minimize human error in their processes?
-Z-Axis minimizes human error by implementing paperless travelers and automatically creating product labels and shipping documents as part of their standard operating procedures, reducing the reliance on manual processes.
What is the role of customer feedback in Z-Axis's commitment to quality?
-Customer feedback is a key part of Z-Axis's commitment to continuous improvement. They actively listen to customer concerns and use this input to refine their processes and ensure customer satisfaction.
Outlines
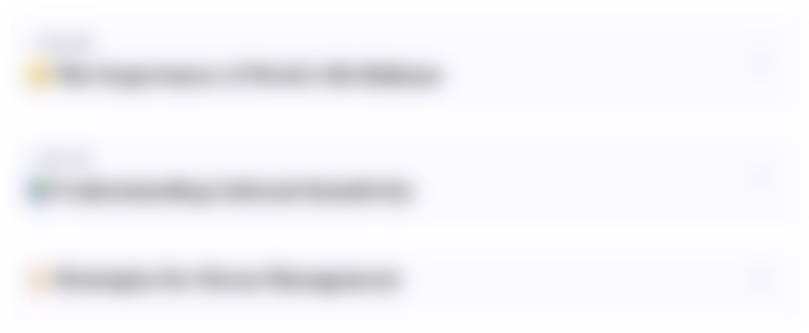
Dieser Bereich ist nur für Premium-Benutzer verfügbar. Bitte führen Sie ein Upgrade durch, um auf diesen Abschnitt zuzugreifen.
Upgrade durchführenMindmap
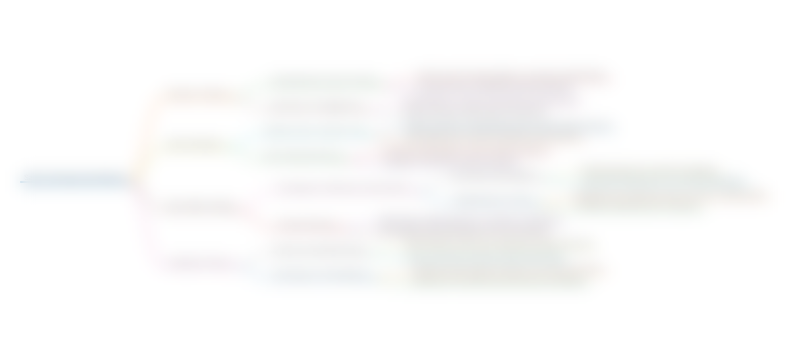
Dieser Bereich ist nur für Premium-Benutzer verfügbar. Bitte führen Sie ein Upgrade durch, um auf diesen Abschnitt zuzugreifen.
Upgrade durchführenKeywords
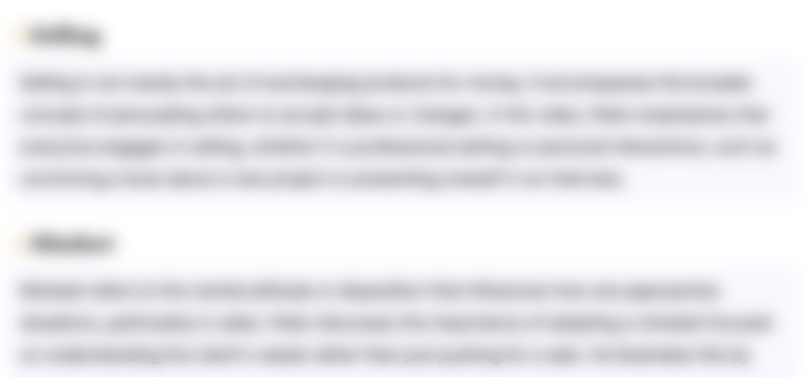
Dieser Bereich ist nur für Premium-Benutzer verfügbar. Bitte führen Sie ein Upgrade durch, um auf diesen Abschnitt zuzugreifen.
Upgrade durchführenHighlights
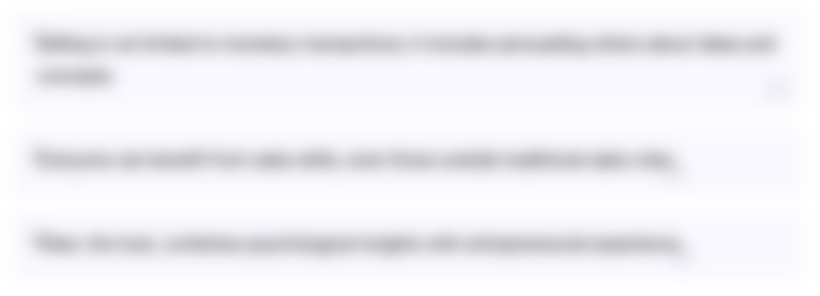
Dieser Bereich ist nur für Premium-Benutzer verfügbar. Bitte führen Sie ein Upgrade durch, um auf diesen Abschnitt zuzugreifen.
Upgrade durchführenTranscripts
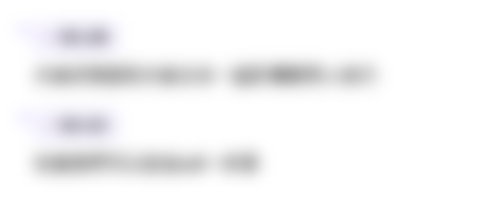
Dieser Bereich ist nur für Premium-Benutzer verfügbar. Bitte führen Sie ein Upgrade durch, um auf diesen Abschnitt zuzugreifen.
Upgrade durchführenWeitere ähnliche Videos ansehen

O que é ISO 9001 e por que certificar minha empresa (COMPLETO)

Profile Komatsu Balikpapan Kalimantan - Timur

ISO 9001, Memahami Strategi Bisnis VERSI ISO 9001:2015

Seri Penerapan Standar ISO di Poyek Konstruksi - Pengantar ISO 9001:2015

Penjelasan Singkat 10 Klausul ISO 9001:2015
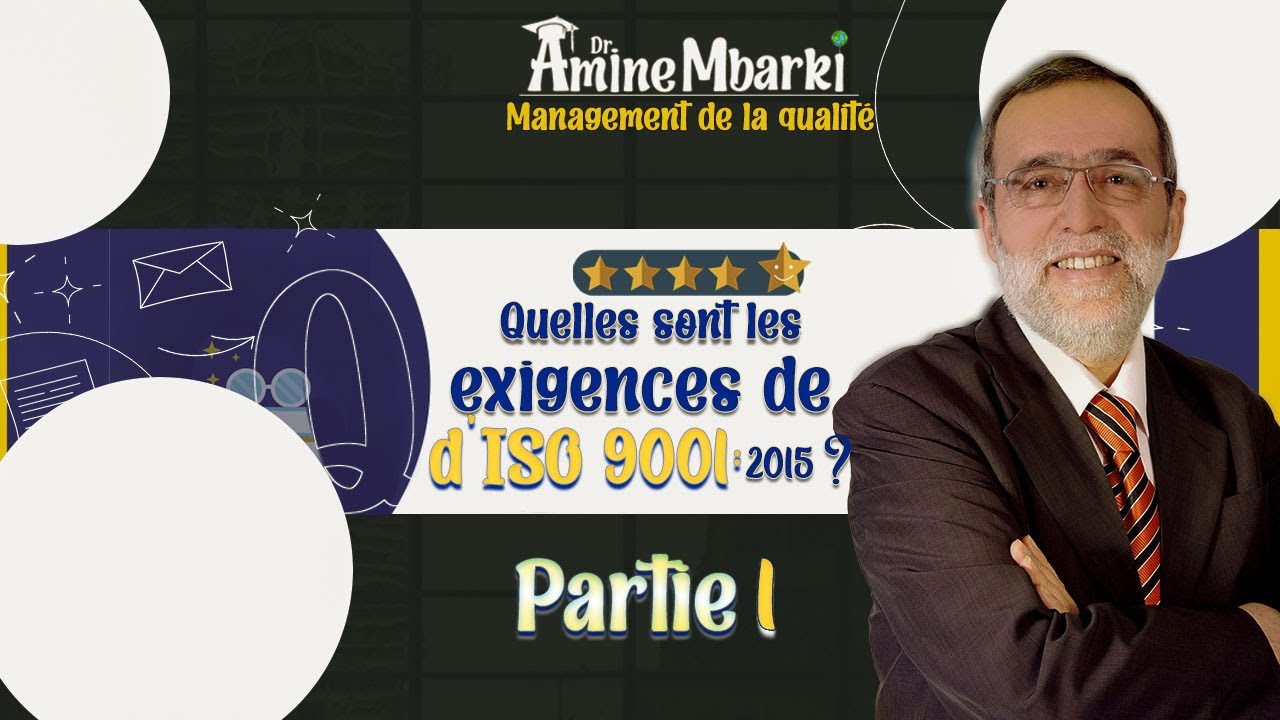
Quelles sont les exigences de ISO 9001:2015 ? Partie 1.
5.0 / 5 (0 votes)