evo Doubles Order Picking Productivity in Time for Peak Season
Summary
TLDREvo, a multi-channel retailer in the action sports industry, has grown rapidly, especially during the pandemic. To manage this growth and improve efficiency, Evo implemented Locust Robotics' autonomous mobile robots to streamline order fulfillment. These robots have significantly boosted productivity, reducing the need for carts and walking. The introduction of the robots not only increased order picking efficiency but also helped with social distancing in the warehouse. Evo plans to scale further by adding more robots for peak seasons and exploring additional uses like directed put-away and transportation of goods within the facility.
Takeaways
- 😀 Evo is a multi-channel retailer specializing in action sports gear and apparel, such as skis, snowboards, mountain bikes, and wakeboards.
- 😀 Evo operates from a 165,000 square foot fulfillment facility, primarily handling business-to-consumer (B2C) transactions while also supporting business-to-business (B2B) growth.
- 😀 The company experienced rapid growth during the COVID-19 pandemic, doubling its business and expanding its store network.
- 😀 Evo sought solutions to address challenges from COVID-19 restrictions, social distancing, and high throughput demands in their distribution center.
- 😀 Locus Robotics was chosen as a flexible solution to meet Evo’s operational needs, especially due to its integration with their existing warehouse management system.
- 😀 The implementation of Locus robots was completed in just 53 days, from signing the contract to the first pick, demonstrating efficient deployment.
- 😀 The robots were well-received by Evo’s team, who appreciated their personalities and saw them as helpful tools rather than replacements.
- 😀 The introduction of Locus robots significantly improved picking efficiency, increasing the units picked per hour (UPH) from 35 to 90, and even up to 113 in some cases.
- 😀 The robots helped with social distancing by reducing the number of people needed in each zone, allowing Evo to optimize staffing levels from 12-15 people to just five.
- 😀 Locus robots allowed Evo to handle peak season demands more efficiently, reducing congestion, increasing speed, and supporting scalable growth with fewer staff on the floor.
- 😀 Evo plans to add more robots for future peak seasons, and sees potential for additional use cases like directed put-away and goods transport within the warehouse.
Q & A
What is EVO, and what types of products do they sell?
-EVO is a multi-channel retailer catering to the action sports industry, selling products like skis, snowboards, mountain bikes, wakeboards, apparel, and accessories related to the action sports lifestyle.
What was the main reason EVO decided to handle its own fulfillment?
-EVO decided to handle its own fulfillment to maintain better control over the customer experience, inventory management, and overall operations.
How has EVO's business growth been impacted by the COVID-19 pandemic?
-EVO has experienced tremendous growth during the COVID-19 pandemic, doubling their business in the last year and also adding new stores. This growth has increased both their B2C and B2B needs.
What challenges did EVO face during the pandemic that required a solution?
-EVO needed solutions to combat COVID-19 restrictions, including social distancing and improving throughput in their distribution center.
Why did EVO choose Locus Robotics as their solution?
-EVO chose Locus Robotics because their flexible solution could grow with EVO's rapidly expanding business, and the system's compatibility with EVO's warehouse management system (WMS) made the integration smoother.
What was the timeline for implementing Locus Robotics at EVO?
-The implementation of Locus Robotics at EVO took just 53 days, from signing the contract to having the system live and operational, showcasing the efficiency and creativity of both the Locus and Kerber teams.
How did EVO's employees react to the introduction of robots in the warehouse?
-The introduction of robots was met with excitement by EVO's team, who embraced the technology. The robots were seen as a tool to help employees, not replace them, and their presence made the work environment more enjoyable.
What specific efficiencies did EVO gain after implementing Locus Robotics?
-After implementing Locus Robotics, EVO saw a significant increase in picking efficiency. The units per hour (UPH) rose from 35 to 90, with some operators reaching up to 113. Additionally, the robots helped with social distancing and reduced the number of workers needed in a zone.
How did Locus Robotics improve the training process for EVO's warehouse staff?
-Locus Robotics made the training process quick and efficient. New employees could be trained in just 10-15 minutes, as the robots are intuitive and easy to use, minimizing room for error and speeding up the learning curve.
What impact did the robots have during EVO's peak season?
-During the peak season, the robots significantly improved the efficiency of the picking process, reducing congestion and the number of workers needed, allowing EVO to handle a larger volume of orders with less effort.
What are EVO's plans for future use of robotics in their operations?
-EVO plans to add more robots for future peak seasons, with an additional 40 robots expected during the holiday period. They also see potential for robotics in directed put-away and transporting goods across the warehouse.
Outlines
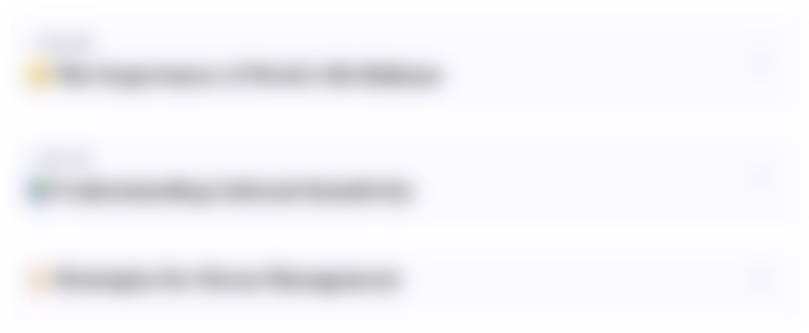
Dieser Bereich ist nur für Premium-Benutzer verfügbar. Bitte führen Sie ein Upgrade durch, um auf diesen Abschnitt zuzugreifen.
Upgrade durchführenMindmap
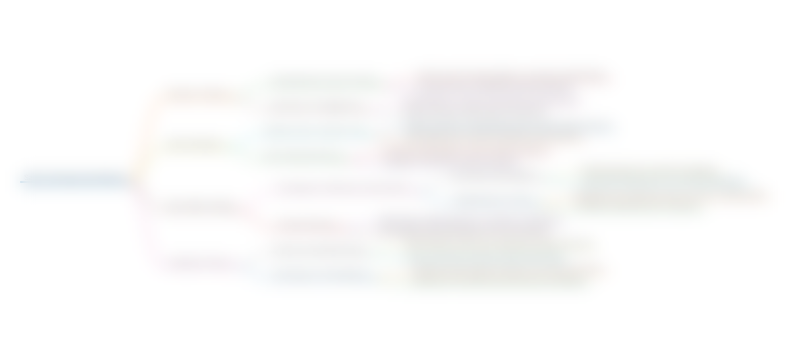
Dieser Bereich ist nur für Premium-Benutzer verfügbar. Bitte führen Sie ein Upgrade durch, um auf diesen Abschnitt zuzugreifen.
Upgrade durchführenKeywords
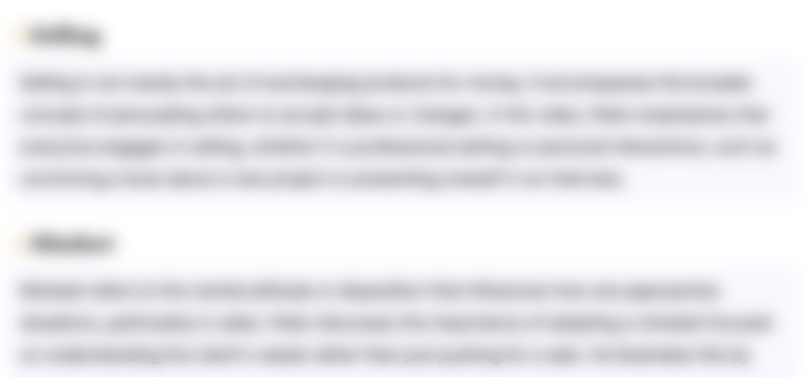
Dieser Bereich ist nur für Premium-Benutzer verfügbar. Bitte führen Sie ein Upgrade durch, um auf diesen Abschnitt zuzugreifen.
Upgrade durchführenHighlights
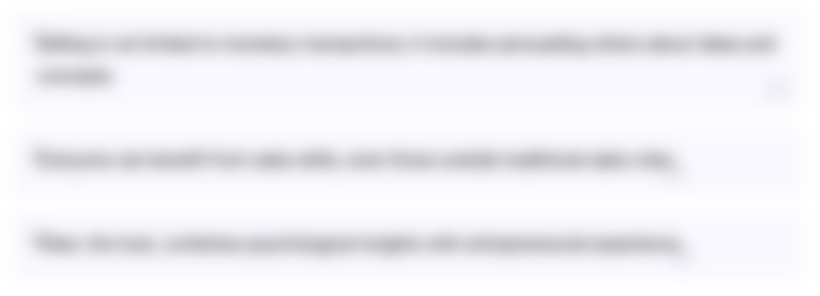
Dieser Bereich ist nur für Premium-Benutzer verfügbar. Bitte führen Sie ein Upgrade durch, um auf diesen Abschnitt zuzugreifen.
Upgrade durchführenTranscripts
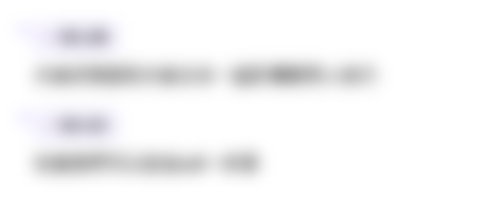
Dieser Bereich ist nur für Premium-Benutzer verfügbar. Bitte führen Sie ein Upgrade durch, um auf diesen Abschnitt zuzugreifen.
Upgrade durchführenWeitere ähnliche Videos ansehen
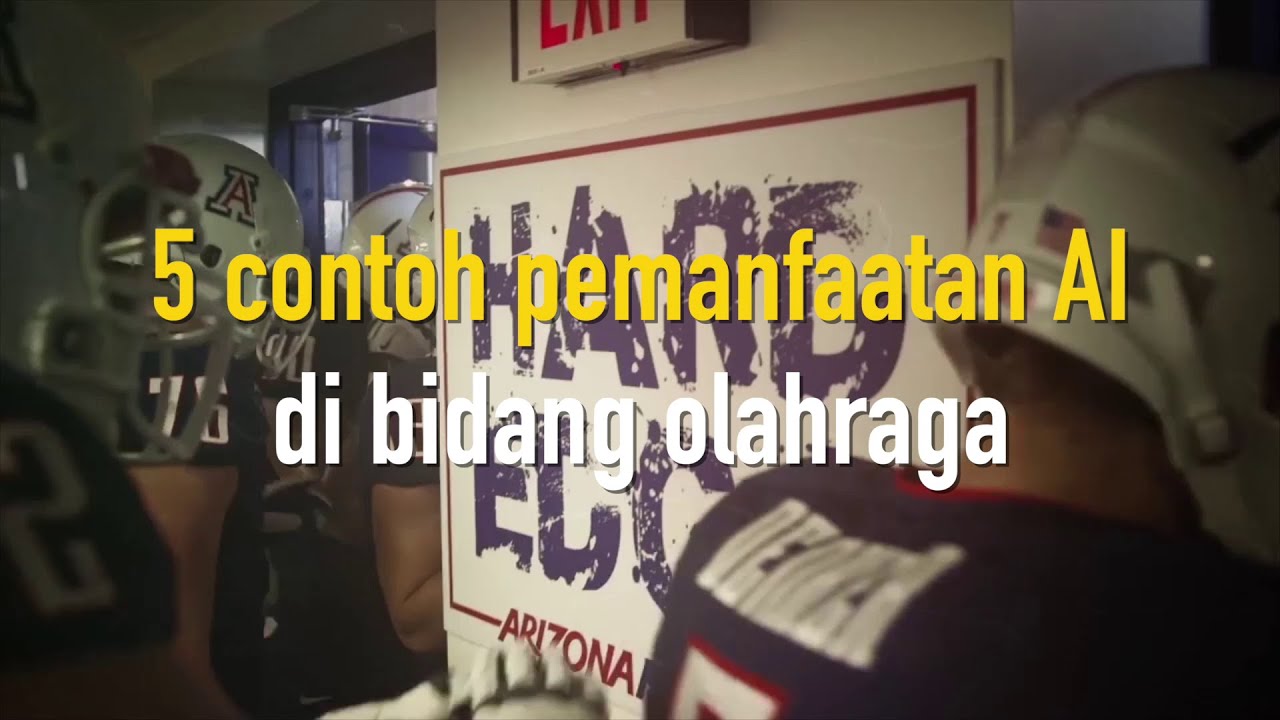
5 Contoh Pemanfaatan AI di Bidang Olahraga
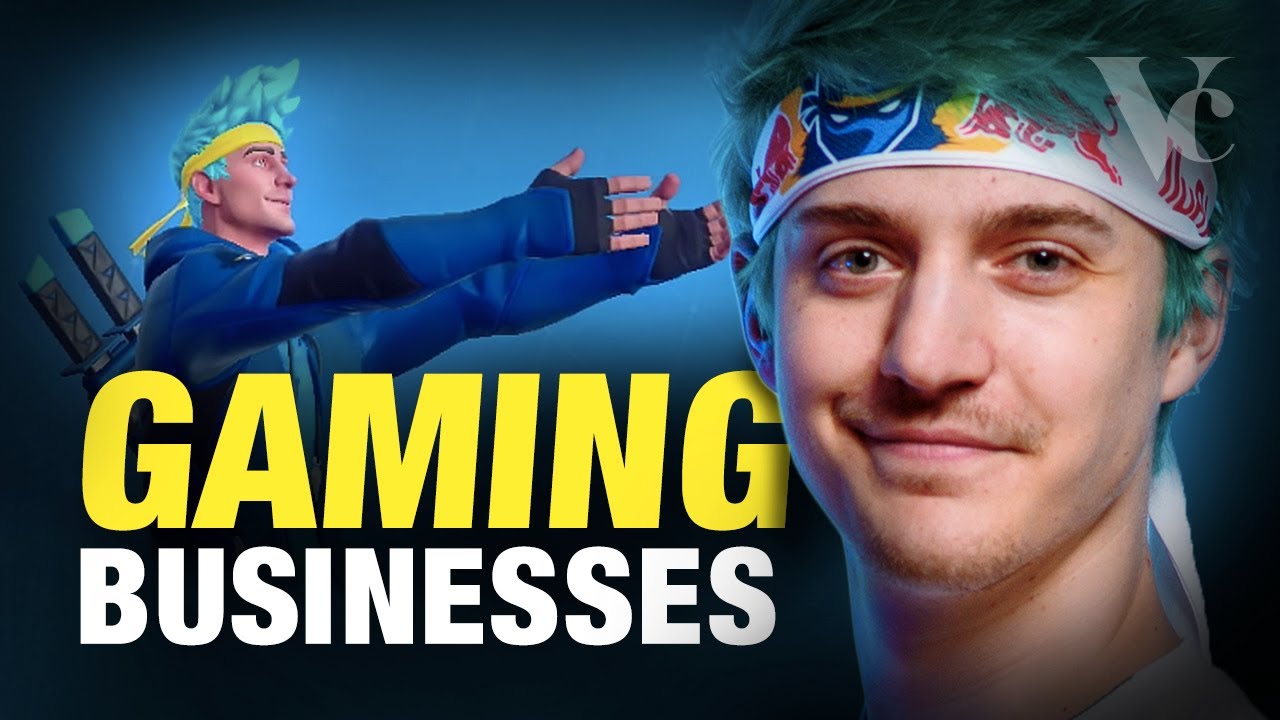
Gaming Inc: The business of E-Sports

Objek Wisata Pantai Indah Kemangi | Tugas bahasa indonesia meliput berita

Aku Kamu Dia dan Pancasila bagian 2: Berkarya dengan Gotong Royong

How Home Depot Became the World’s Largest Home-Improvement Retailer | WSJ The Economics Of

FE em Ação | Macakitos
5.0 / 5 (0 votes)