Intro to Large Deformation — Lesson 1
Summary
TLDRThis lesson on large deformation explores how significant shape changes in mechanical systems lead to non-linear responses. It covers four key types of geometric nonlinearities: large strain, large rotation, stress stiffening, and spin softening. Through practical examples like fishing rods, drive shafts, guitar strings, and rotating machinery, the video demonstrates the importance of using large deformation formulations in accurate structural analysis. Engineers learn when these effects are most critical for design and analysis, ensuring more reliable predictions and avoiding design flaws in mechanical systems.
Takeaways
- 😀 Large deformation analysis is necessary when significant changes in the shape of a structure occur, introducing nonlinearity in the system’s response.
- 😀 The stiffness of a mechanical system depends on both the material and geometry, and large deformation analysis takes both factors into account.
- 😀 Large deformation considers the change in shape of a structure and introduces geometric nonlinearities that affect the system’s behavior.
- 😀 Four important types of geometric nonlinearities are: large strain, large rotation, stress stiffening, and spin softening.
- 😀 Large strain results in nonlinear force-displacement behavior, where the structure’s shape changes and impacts the applied load.
- 😀 The fishing rod example demonstrates how large strain affects the deflection of a structure under load, highlighting the need for large deformation analysis to avoid inaccurate predictions.
- 😀 Large rotation must be accounted for even in rigid structures when large angular displacements occur, as small rotation assumptions lead to errors.
- 😀 In the case of large rotations, such as in a drive shaft, using small angle approximations can cause inaccuracies, especially with increasing rotation angles.
- 😀 Stress stiffening refers to changes in a structure’s stiffness due to pre-existing stress, which can affect the system’s response to external forces.
- 😀 The guitar string example demonstrates stress stiffening, where tension increases the stiffness of the string and alters its vibration frequency.
- 😀 Spin softening occurs in rotating machinery, where centrifugal forces cause radial deformation, affecting the structural response and vibrational properties of components like turbines and jet engines.
Q & A
What is the main purpose of using the large deformation formulation in structural analysis?
-The large deformation formulation is used to account for the changes in shape of a structure and the corresponding stresses developed in it. This helps to incorporate nonlinearity in the system's response, providing a more accurate prediction of deflections and structural behavior under significant loads.
Why is it important to consider both material and geometric properties in the stiffness of a structure?
-The stiffness of a structure depends on both its material properties (like elasticity) and its geometry. For example, a stainless steel bar is stiffer than a spring made from the same material due to differences in their geometry. The spring's helical shape makes it more flexible, despite using the same material.
What are the four important types of geometric nonlinearities in large deformation analysis?
-The four types of geometric nonlinearities are: 1) Large strain, 2) Large rotation, 3) Stress stiffening, and 4) Spin softening. These nonlinearities are introduced when using the large deformation formulation, and the prominence of each depends on the specific application.
How does large strain affect a system, and can you provide an example?
-Large strain occurs when a structure deforms significantly, affecting its load-bearing capacity. An example is a fishing rod: when a fish is caught, the rod bends under the applied load, causing a change in its shape. This change reduces the moment applied at the free end, leading to a nonlinear force-displacement response. If large strain is ignored, deflection predictions could be inaccurate.
What is the significance of considering large rotation in mechanical systems?
-Large rotation must be considered even if the structure is not undergoing significant deformation. For example, a drive shaft in an automobile experiences torque that causes it to rotate. At large rotation angles, the trigonometric functions describing the system's behavior become nonlinear, and neglecting this can result in significant errors in the analysis.
Why does the approximation of small rotation (sin(θ) = θ) fail at large rotations?
-The approximation of sin(θ) = θ and cos(θ) = 1 is valid for small angles, but at large rotations, this leads to errors. The shaft may appear to grow radially, which is physically incorrect. Using large deformation formulation accounts for this nonlinear behavior, ensuring more accurate results at larger rotations.
What is stress stiffening, and how does it affect a system?
-Stress stiffening occurs when a material experiences internal stresses that alter its stiffness. For example, in a guitar, the strings are stretched during tuning, increasing their stiffness and changing their vibration frequencies. In any bolted assembly, tightening bolts introduces stress, which increases the system's stiffness. Not accounting for stress stiffening can lead to inaccurate results in structural analysis.
How does stress stiffening affect the design of structures?
-Stress stiffening changes the way a structure behaves under load by increasing its stiffness due to internal stresses. For example, in a guitar, tuning the strings adds stress, making them stiffer. Engineers must account for these changes in stiffness to ensure the accuracy of structural calculations and avoid errors in design.
What is spin softening, and how does it affect rotating machinery?
-Spin softening is a phenomenon in which rotating components, such as turbines or jet engines, experience radial deformation due to centrifugal forces. As these components spin, their radius of rotation increases, which in turn amplifies the centrifugal force, leading to more deformation. This effect is captured using large deformation formulation and is critical for analyzing the behavior of heavy rotating machinery.
Why is it important to use large deformation formulation in studying heavy rotating machinery?
-Large deformation formulation is crucial for accurately modeling the behavior of rotating machinery like wind turbines and jet engines. These components experience significant centrifugal forces that cause radial deformation. If not accounted for, these effects can lead to inaccurate predictions of the machinery's performance and vibrational properties.
Outlines
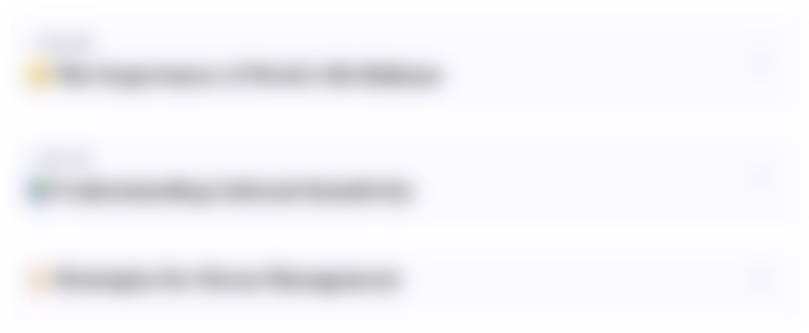
Dieser Bereich ist nur für Premium-Benutzer verfügbar. Bitte führen Sie ein Upgrade durch, um auf diesen Abschnitt zuzugreifen.
Upgrade durchführenMindmap
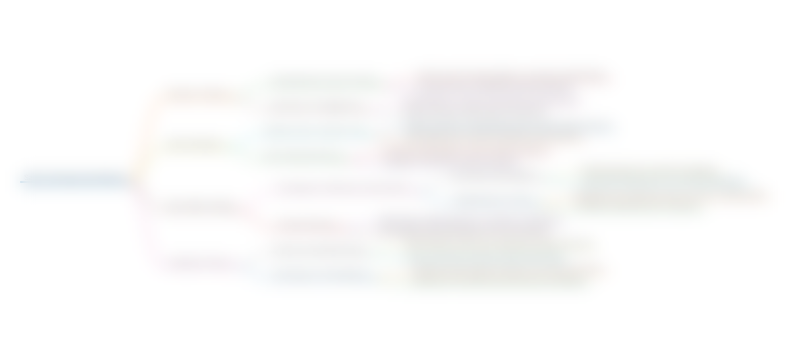
Dieser Bereich ist nur für Premium-Benutzer verfügbar. Bitte führen Sie ein Upgrade durch, um auf diesen Abschnitt zuzugreifen.
Upgrade durchführenKeywords
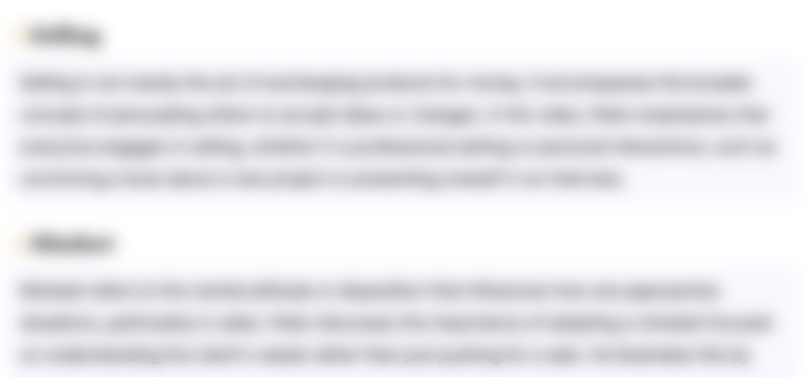
Dieser Bereich ist nur für Premium-Benutzer verfügbar. Bitte führen Sie ein Upgrade durch, um auf diesen Abschnitt zuzugreifen.
Upgrade durchführenHighlights
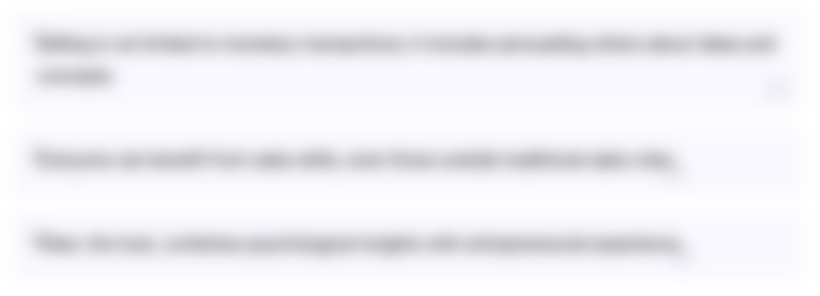
Dieser Bereich ist nur für Premium-Benutzer verfügbar. Bitte führen Sie ein Upgrade durch, um auf diesen Abschnitt zuzugreifen.
Upgrade durchführenTranscripts
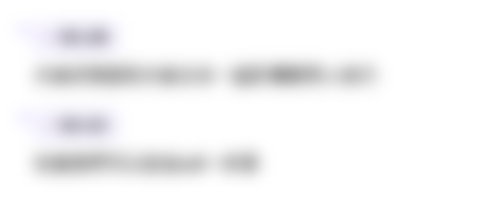
Dieser Bereich ist nur für Premium-Benutzer verfügbar. Bitte führen Sie ein Upgrade durch, um auf diesen Abschnitt zuzugreifen.
Upgrade durchführenWeitere ähnliche Videos ansehen

Constitutive Models— Lesson 1
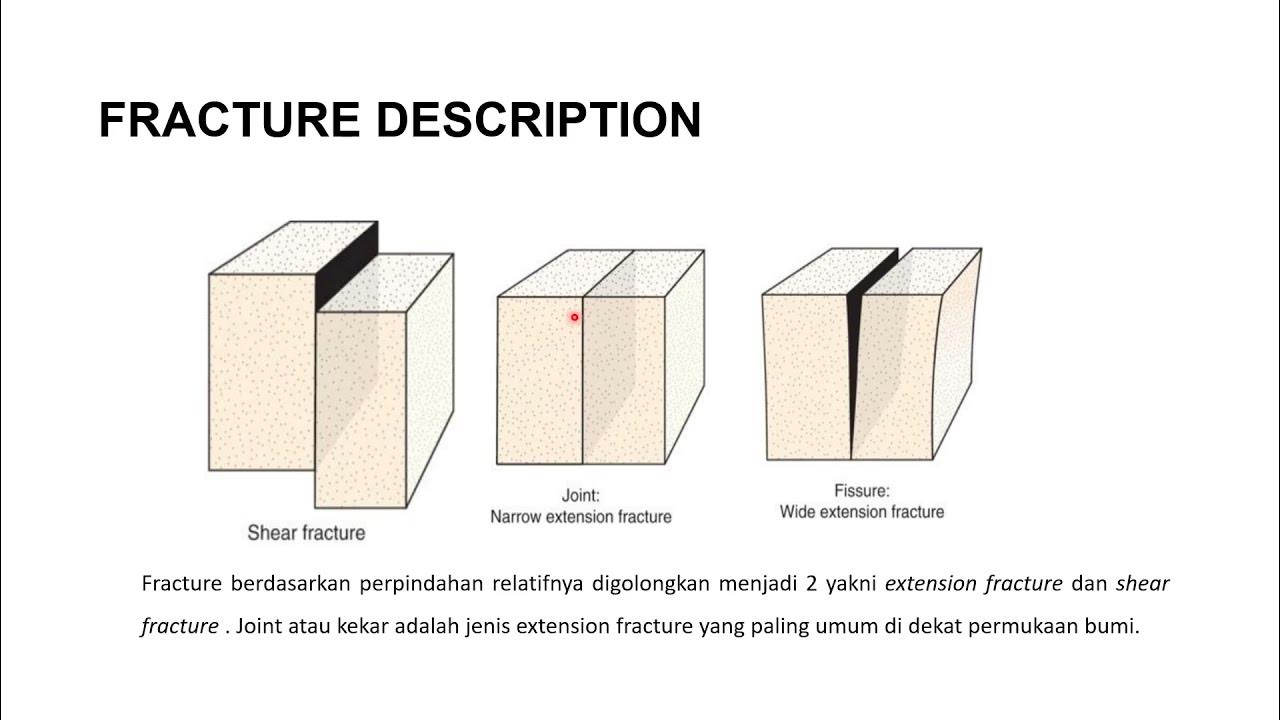
Deformasi Batuan II KEKAR
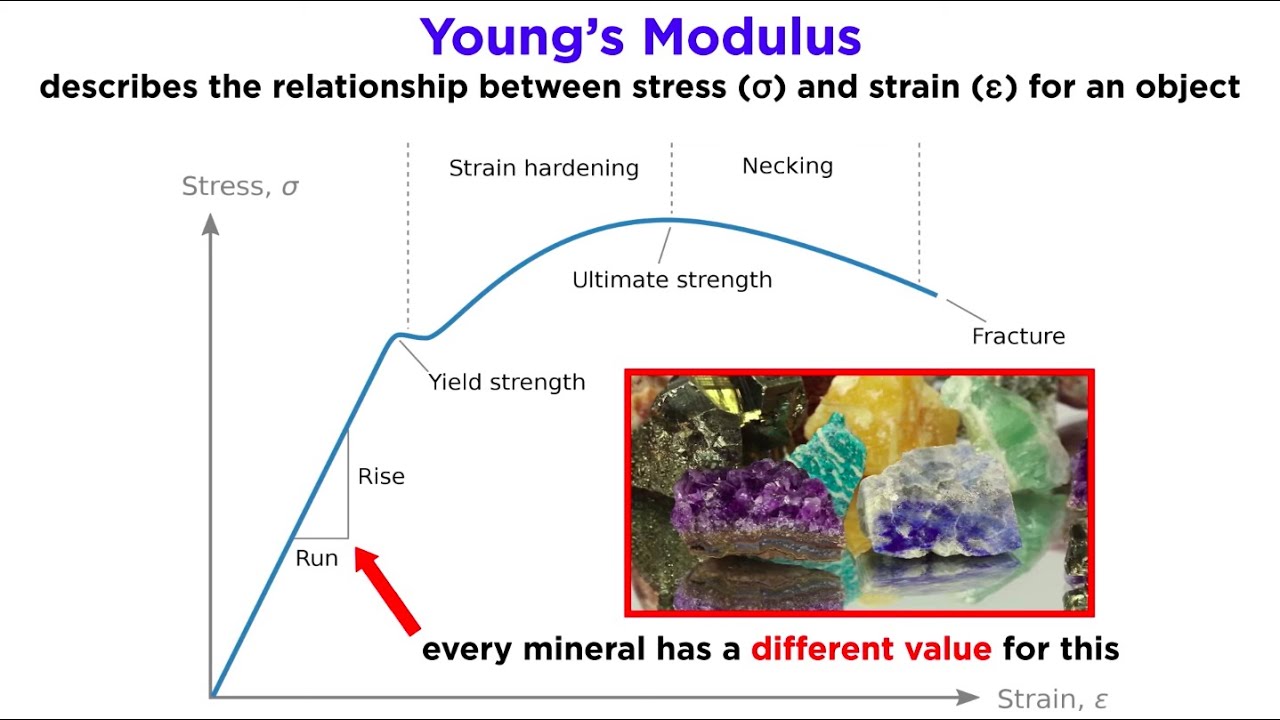
Overview of Geologic Structures Part 1: Rock Deformation, Stress and Strain
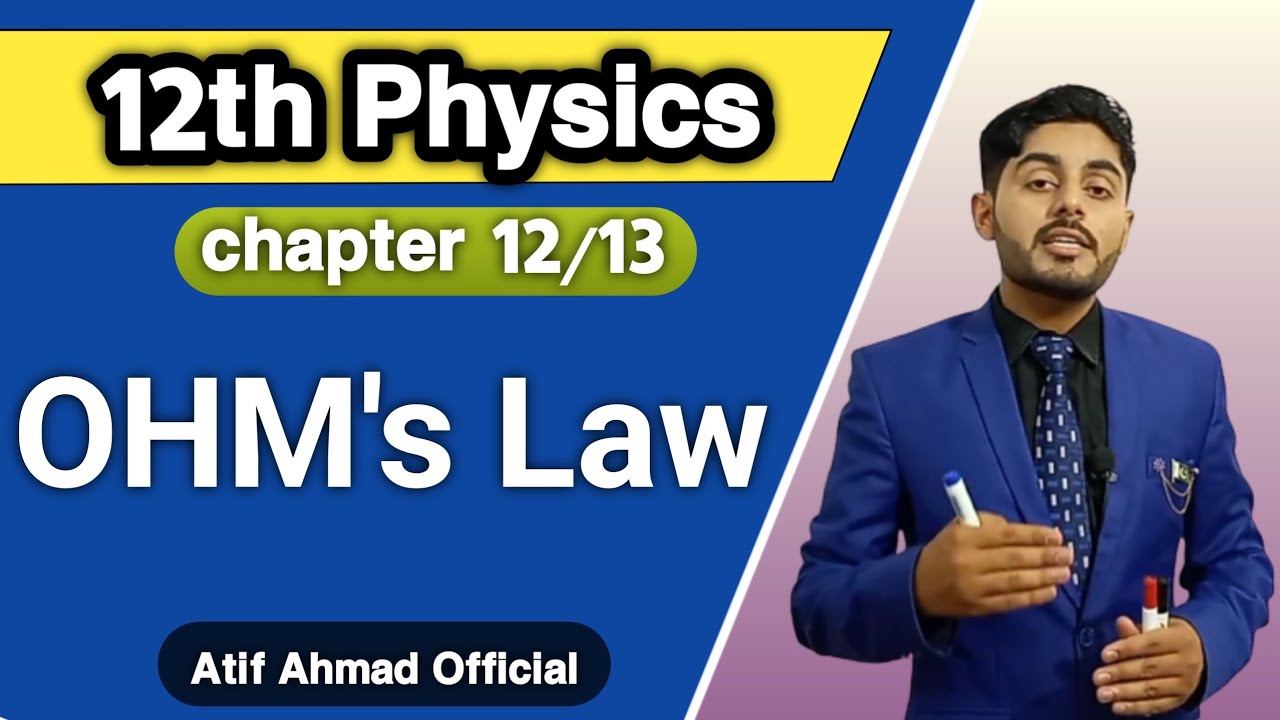
ohms law class 12 | ohmic and non ohmic devices | limitations of ohms law | 12th class physics
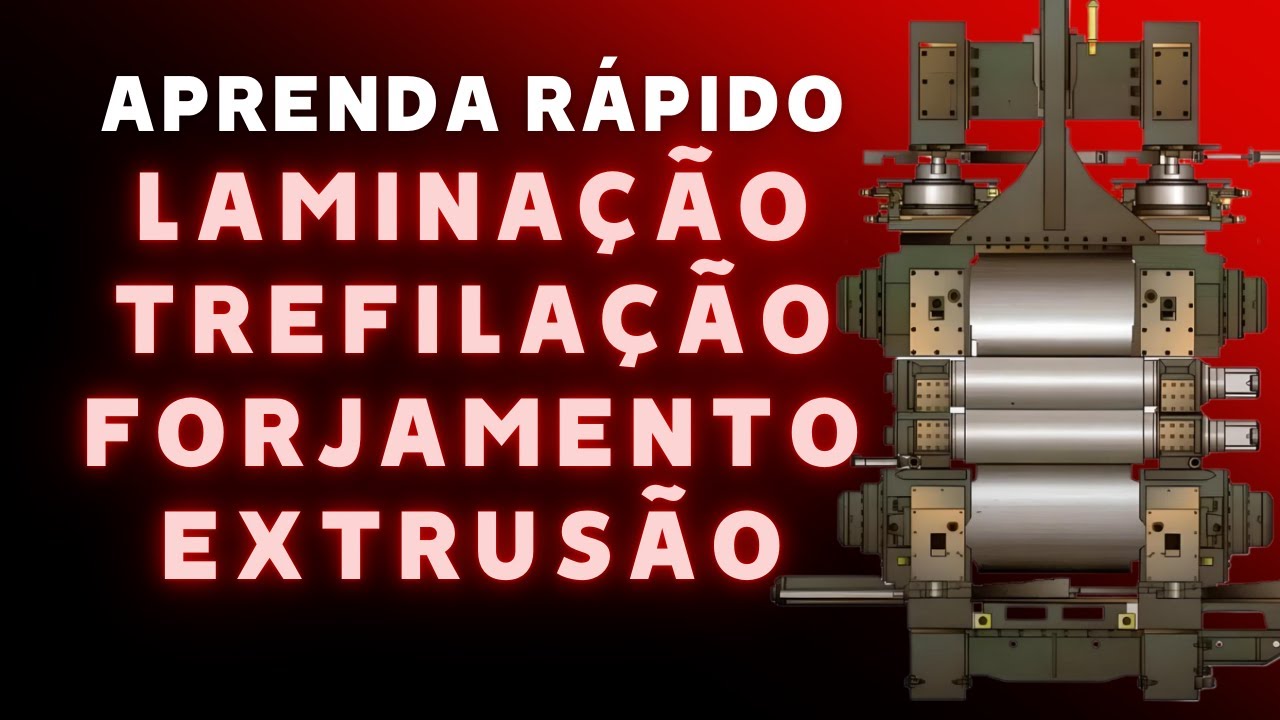
Aprenda os processos de CONFORMAÇÃO / FABRICAÇÃO - Laminação, trefilação, extrusão e forjamento
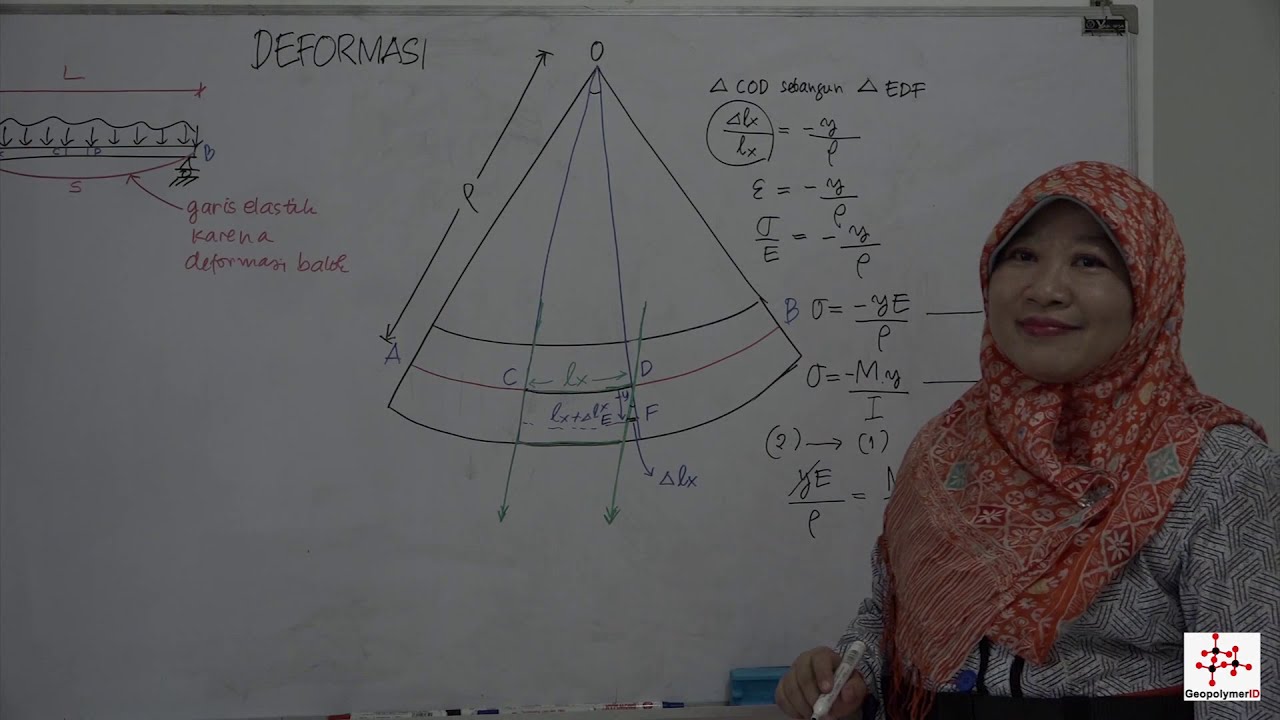
[MEKANIKA BAHAN] PERTEMUAN-17 : "DEFORMASI METODE DOUBLE INTEGRAL PART-1" OLEH Dr. JANUARTI J. E.
5.0 / 5 (0 votes)