BUDAYA KERJA INDUSTRI PERUSAHAAN JEPANG
Summary
TLDRThe 5S methodology is a Japanese concept aimed at improving workplace efficiency, safety, and productivity. It involves five steps: Seiri (Sort), which is removing unnecessary items; Seiton (Set in Order), which focuses on organizing essentials; Seiso (Shine), which ensures cleanliness and checks for potential issues; Seiketsu (Standardize), which establishes routine maintenance and standards; and Shitsuke (Sustain), which integrates 5S into daily habits and organizational culture. By adopting 5S, businesses can create a more organized, efficient, and healthier work environment.
Takeaways
- 😀 5S methodology helps increase productivity by reducing unnecessary activities and fostering teamwork.
- 😀 5S stands for five Japanese words: Seiri (Sort), Seiton (Set in order), Seiso (Shine), Seiketsu (Standardize), and Shitsuke (Sustain).
- 😀 Seiri (Sort) involves identifying and discarding unnecessary items, while keeping only what is essential.
- 😀 Seiton (Set in order) emphasizes organizing and labeling items for easy access and return to their proper places.
- 😀 Seiso (Shine) encourages regular cleaning of the workplace to ensure a healthy, safe, and efficient environment.
- 😀 Seiketsu (Standardize) refers to maintaining the standards achieved by consistently performing the first three S's daily.
- 😀 Shitsuke (Sustain) is about making 5S a daily habit and ensuring it becomes part of the company culture.
- 😀 Establish a reward system for employees who adhere to 5S and provide feedback to those who do not meet standards.
- 😀 Regular checks and maintenance are essential to keeping the workplace environment safe and organized.
- 😀 Adopting 5S as a daily routine helps prevent unhealthy or unsafe working conditions and promotes productivity.
Q & A
What is the purpose of the 5S methodology?
-The 5S methodology is designed to improve productivity, reduce unnecessary activities, and create a safer and more efficient workplace by focusing on organization and cleanliness.
What does 'Seiri' (Sort) involve in the 5S system?
-'Seiri' involves sorting through items and documents to identify what is necessary, what is rarely used, and what is no longer needed. Unnecessary items are removed, and the remaining items are organized for easier access.
How can you apply 'Seiton' (Set in Order) effectively?
-'Seiton' involves organizing necessary items by ensuring they are stored in easily accessible places. Everything should be labeled and kept in designated spots, making it easier for everyone to find and return items.
What does 'Seiso' (Shine) refer to in the 5S methodology?
-'Seiso' refers to cleaning the workplace to maintain a safe and healthy environment. It involves regular cleaning and checking for any equipment or processes that need maintenance or improvements.
Why is standardization ('Seiketsu') important in the 5S system?
-Standardization ensures that the practices of sorting, organizing, and cleaning are consistently maintained. It creates routines and guidelines that employees can follow daily to keep the workplace organized and efficient.
What role does 'Shitsuke' (Sustain) play in the 5S methodology?
-'Shitsuke' involves developing a culture of responsibility and continuous improvement, where everyone in the organization regularly practices the 5S principles, making them habitual and part of the workplace culture.
How can 5S contribute to a healthier and safer workplace?
-By maintaining a clean, organized, and well-structured workplace, 5S helps eliminate hazards, reduce clutter, and prevent accidents, leading to a healthier and safer working environment.
What should be done with items or documents that are no longer needed in the workplace?
-Items or documents that are no longer needed should be removed. For documents, they should be temporarily placed in an area for review to confirm that they are indeed unnecessary, and then properly discarded after a set period.
How can organizations ensure that 5S becomes a part of the workplace culture?
-Organizations can ensure 5S becomes a part of the culture by encouraging daily practice of the 5S principles, rewarding those who consistently follow the standards, and providing training to instill these practices as habitual behaviors.
What are the benefits of implementing 5S in the workplace?
-Implementing 5S leads to increased efficiency, reduced workplace frustration, improved safety, and a more organized environment. It also enhances teamwork and productivity, making the workplace healthier and more conducive to success.
Outlines
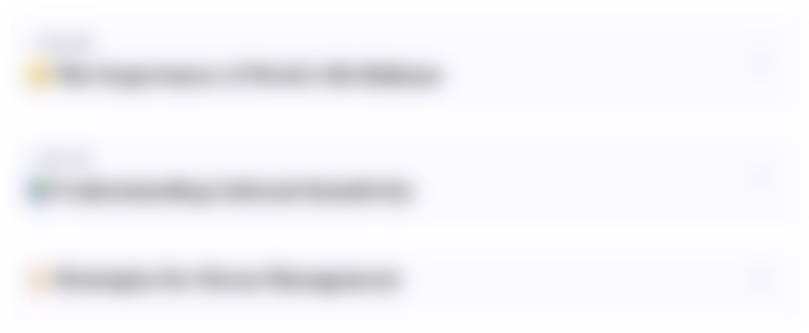
Dieser Bereich ist nur für Premium-Benutzer verfügbar. Bitte führen Sie ein Upgrade durch, um auf diesen Abschnitt zuzugreifen.
Upgrade durchführenMindmap
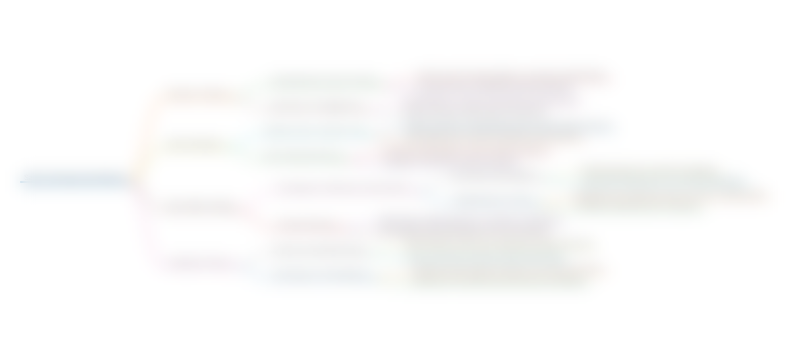
Dieser Bereich ist nur für Premium-Benutzer verfügbar. Bitte führen Sie ein Upgrade durch, um auf diesen Abschnitt zuzugreifen.
Upgrade durchführenKeywords
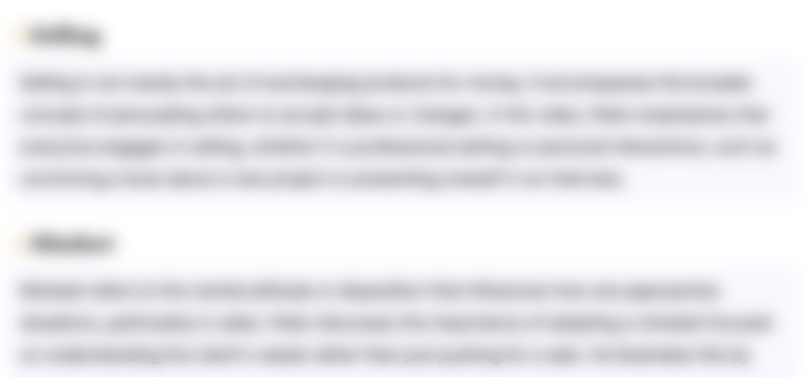
Dieser Bereich ist nur für Premium-Benutzer verfügbar. Bitte führen Sie ein Upgrade durch, um auf diesen Abschnitt zuzugreifen.
Upgrade durchführenHighlights
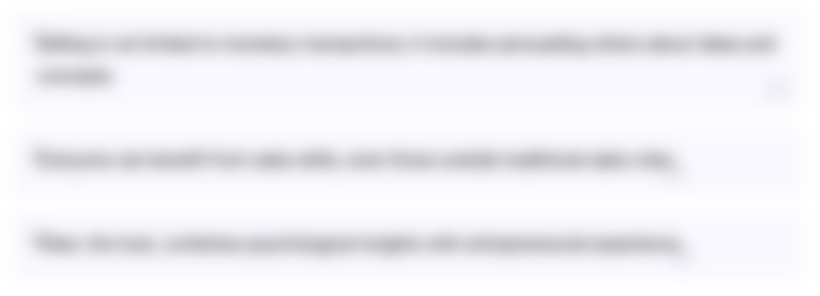
Dieser Bereich ist nur für Premium-Benutzer verfügbar. Bitte führen Sie ein Upgrade durch, um auf diesen Abschnitt zuzugreifen.
Upgrade durchführenTranscripts
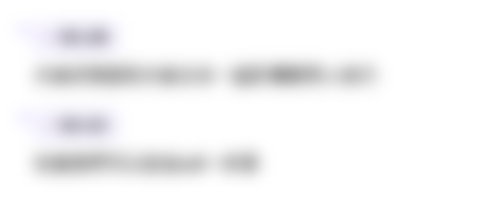
Dieser Bereich ist nur für Premium-Benutzer verfügbar. Bitte führen Sie ein Upgrade durch, um auf diesen Abschnitt zuzugreifen.
Upgrade durchführenWeitere ähnliche Videos ansehen
5.0 / 5 (0 votes)