Designed to Fail: Chemical Release at LyondellBasell
Summary
TLDRA tragic incident at the LyondellBasell LaPorte complex in Texas on July 27, 2021, resulted in the eruption of 164,000 pounds of acetic acid, fatally injuring two workers. The accident was caused by workers mistakenly removing critical components from a plug valve during maintenance, leading to the release of the toxic chemical. The Chemical Safety Board (CSB) identified issues with valve design and inadequate worker training. The CSB recommended redesigning valves to prevent human error and improving training and procedures for contractors to ensure worker safety, highlighting the need for stronger safeguards in industrial settings.
Takeaways
- 😀 A tragic accident occurred on July 27, 2021, at LyondellBasell's LaPorte complex in Texas, when three contract workers were exposed to a dangerous acetic acid mixture, resulting in two fatalities and one serious injury.
- 😀 The incident was caused when workers inadvertently removed pressure-retaining fasteners from a plug valve while attempting to remove its actuator, leading to the sudden release of 164,000 pounds of acetic acid.
- 😀 Acetic acid is a highly corrosive substance that can cause severe skin burns, eye damage, and respiratory harm, making it critical to handle safely during maintenance operations.
- 😀 The workers had not received proper training or procedures for the actuator removal, and LyondellBasell lacked a detailed procedure for this task, contributing to the failure.
- 😀 This incident is part of a recurring issue where workers accidentally remove pressure-retaining components from plug valves, a problem linked to valve design and lack of clear procedures.
- 😀 The CSB investigation revealed that the design of plug valves should be improved to prevent human error and that components should be clearly marked to avoid accidental removal during maintenance.
- 😀 The CSB recommended that valve design standards be updated to require better labeling of pressure-retaining components and to make new plug valves harder to inadvertently disassemble.
- 😀 The lack of proper risk assessment, procedures, and oversight during the maintenance work was another critical safety issue identified by the CSB.
- 😀 CSB recommended that LyondellBasell establish clear written procedures for actuator removal, ensure contractors are properly trained, and implement better oversight for similar work.
- 😀 The incident serves as a reminder that even routine maintenance tasks can become dangerous if not carefully planned and executed with proper safeguards in place.
Q & A
What happened at the LyondellBasell LaPorte complex on July 27, 2021?
-On July 27, 2021, three contract workers accidentally caused a release of 164,000 pounds of acetic acid while attempting to remove an actuator from a plug valve. The release resulted in the deaths of two workers and injuries to a third, as well as 29 others seeking medical treatment.
What was the cause of the acetic acid release?
-The acetic acid release occurred when the workers inadvertently removed pressure-retaining fasteners from a plug valve while trying to remove the actuator. This caused the valve to fail, and the acetic acid mixture was ejected under pressure.
What safety failures contributed to the incident?
-The incident was caused by several safety failures, including the improper design of the plug valve, lack of clear procedures for actuator removal, insufficient training for the workers, and inadequate oversight by LyondellBasell.
Why was the valve design considered problematic?
-The plug valve's design allowed for the accidental removal of pressure-retaining components, which had previously resulted in other serious incidents. The design made it easy for workers to unknowingly compromise the valve's integrity, leading to dangerous chemical releases.
What could have been done to prevent the accident?
-To prevent the accident, LyondellBasell should have ensured that the workers had clear written procedures for actuator removal, proper training, and adequate oversight. Additionally, a thorough risk assessment should have been conducted to ensure safe working conditions, and the valve design should have been more resistant to human error.
What recommendations did the CSB make to prevent future incidents?
-The CSB recommended redesigning plug valves to prevent the inadvertent removal of pressure-retaining components, marking critical components with clear labels or color codes, and ensuring that workers receive proper training, procedures, and risk assessments for maintenance tasks.
What were the key issues identified with the safety procedures at the LaPorte complex?
-Key issues included the lack of a specific procedure for removing the actuator from the valve, the absence of a risk assessment to identify hazards, and insufficient training for the workers. LyondellBasell also did not oversee the work, assuming the task was simple enough to be performed without strict guidelines.
What role did the contract workers from Turn2 Specialty Companies play in the incident?
-The contract workers from Turn2 Specialty Companies were tasked with removing the actuator from the valve. They unintentionally compromised the valve's integrity by removing critical fasteners and applying excessive force to remove a coupler, which led to the acetic acid release.
What immediate actions did LyondellBasell take after discovering the leak in the acetic acid unit?
-Upon discovering a small leak in the acetic acid unit, LyondellBasell decided to shut down the unit during a larger shutdown of an adjacent process. They planned to use this downtime to fix the leak and isolate the affected section by closing the plug valve, but the improper removal of the actuator led to the accident.
What are the main safety issues identified by the CSB regarding valve design?
-The CSB identified that the plug valve design allowed workers to inadvertently remove pressure-retaining components, which could lead to catastrophic failures. They recommended redesigning valves to prevent human error and marking critical components clearly to reduce the risk of accidental removal.
Outlines
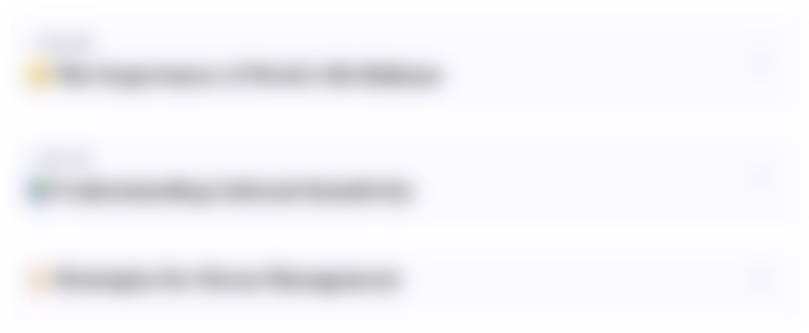
Dieser Bereich ist nur für Premium-Benutzer verfügbar. Bitte führen Sie ein Upgrade durch, um auf diesen Abschnitt zuzugreifen.
Upgrade durchführenMindmap
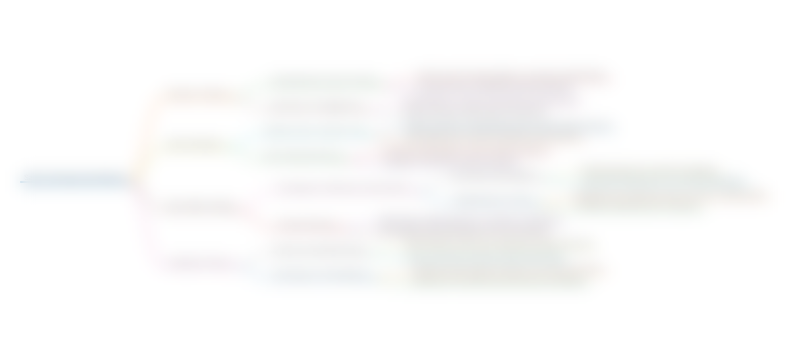
Dieser Bereich ist nur für Premium-Benutzer verfügbar. Bitte führen Sie ein Upgrade durch, um auf diesen Abschnitt zuzugreifen.
Upgrade durchführenKeywords
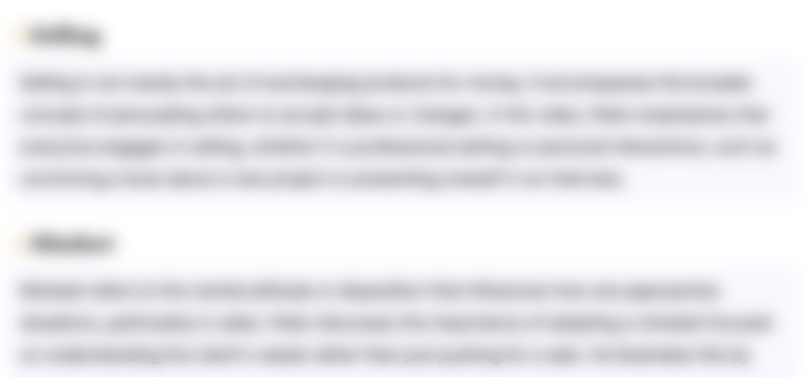
Dieser Bereich ist nur für Premium-Benutzer verfügbar. Bitte führen Sie ein Upgrade durch, um auf diesen Abschnitt zuzugreifen.
Upgrade durchführenHighlights
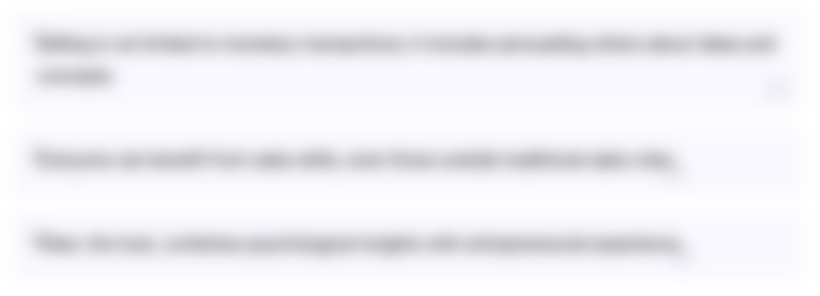
Dieser Bereich ist nur für Premium-Benutzer verfügbar. Bitte führen Sie ein Upgrade durch, um auf diesen Abschnitt zuzugreifen.
Upgrade durchführenTranscripts
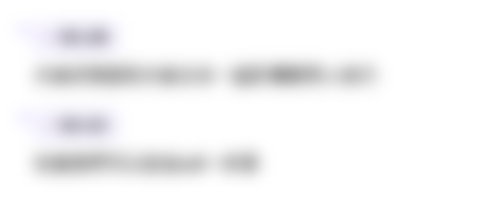
Dieser Bereich ist nur für Premium-Benutzer verfügbar. Bitte führen Sie ein Upgrade durch, um auf diesen Abschnitt zuzugreifen.
Upgrade durchführenWeitere ähnliche Videos ansehen
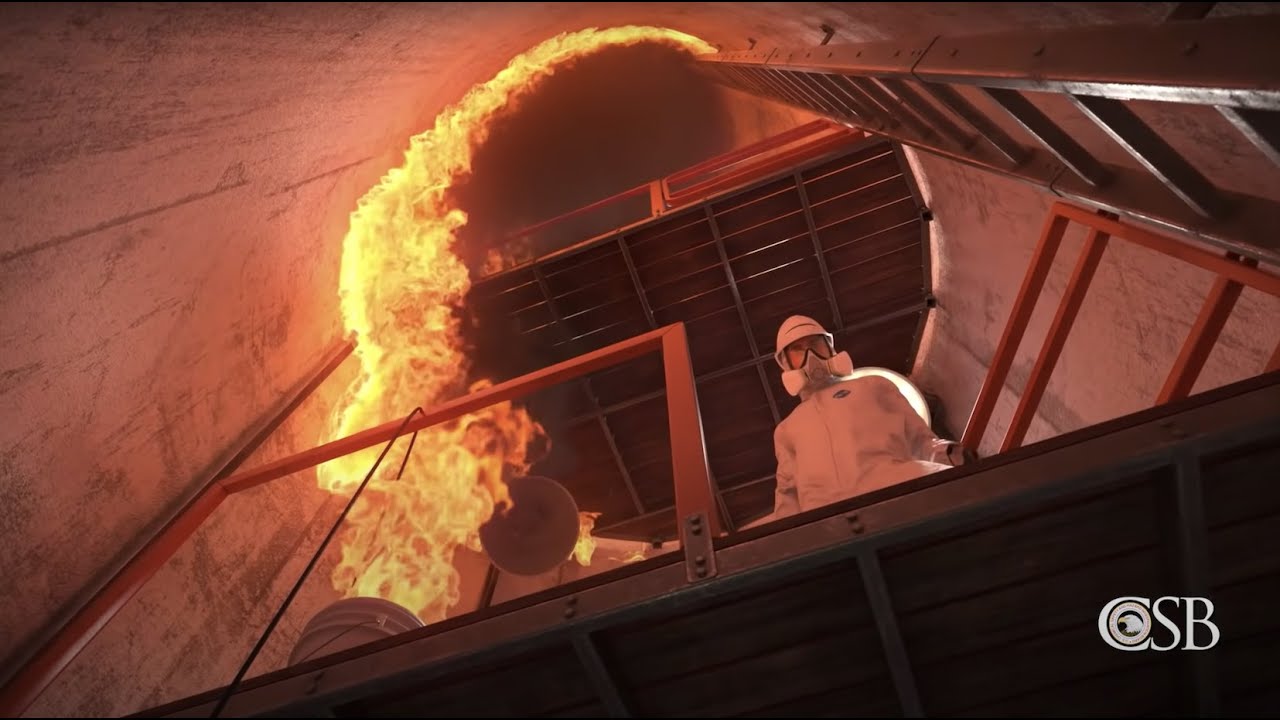
Simultaneous Tragedy: Fire at Evergreen Packaging
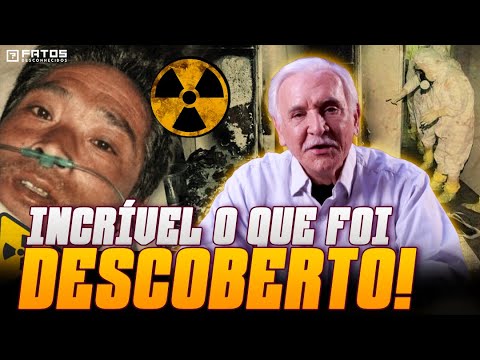
Hisashi Ouchi - A pessoa mais radioativa da história!

Accident case event in the Philippines - Industrial safety management
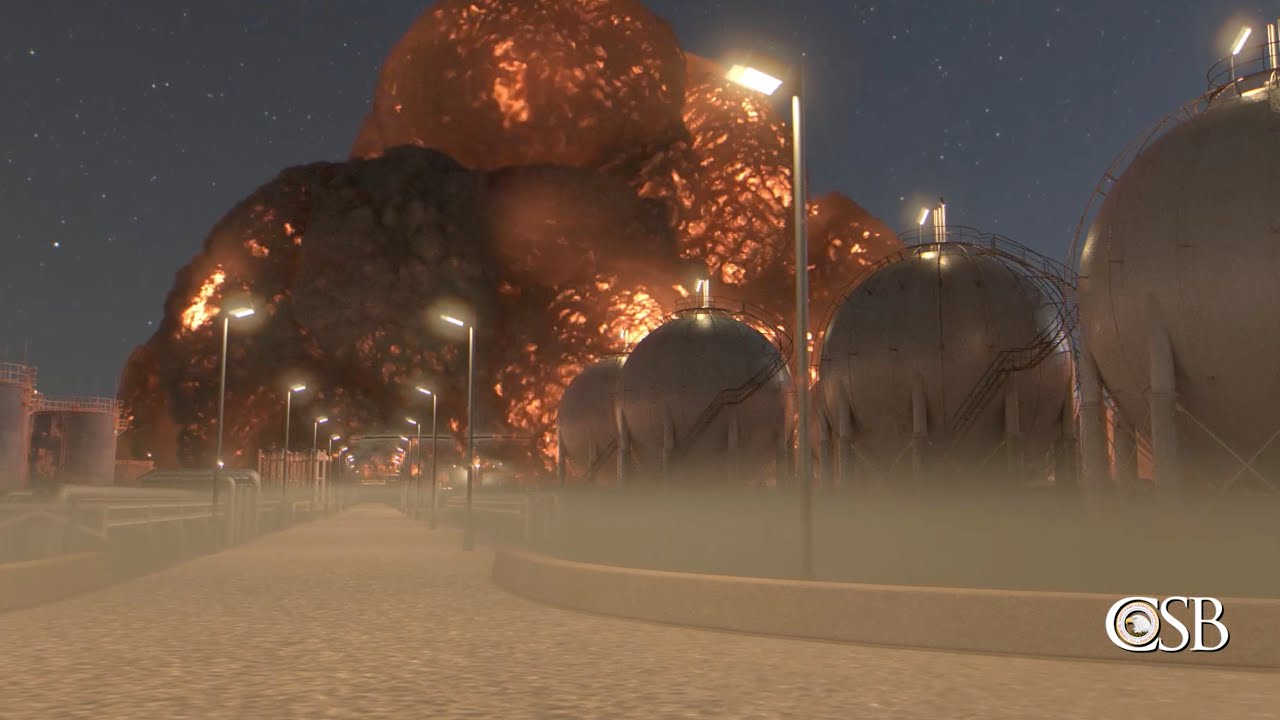
The Danger of Popcorn Polymer: Incident at the TPC Group Chemical Plant

News at 7:30|27 SEP 2023|HONG KONG English Latest NEWS
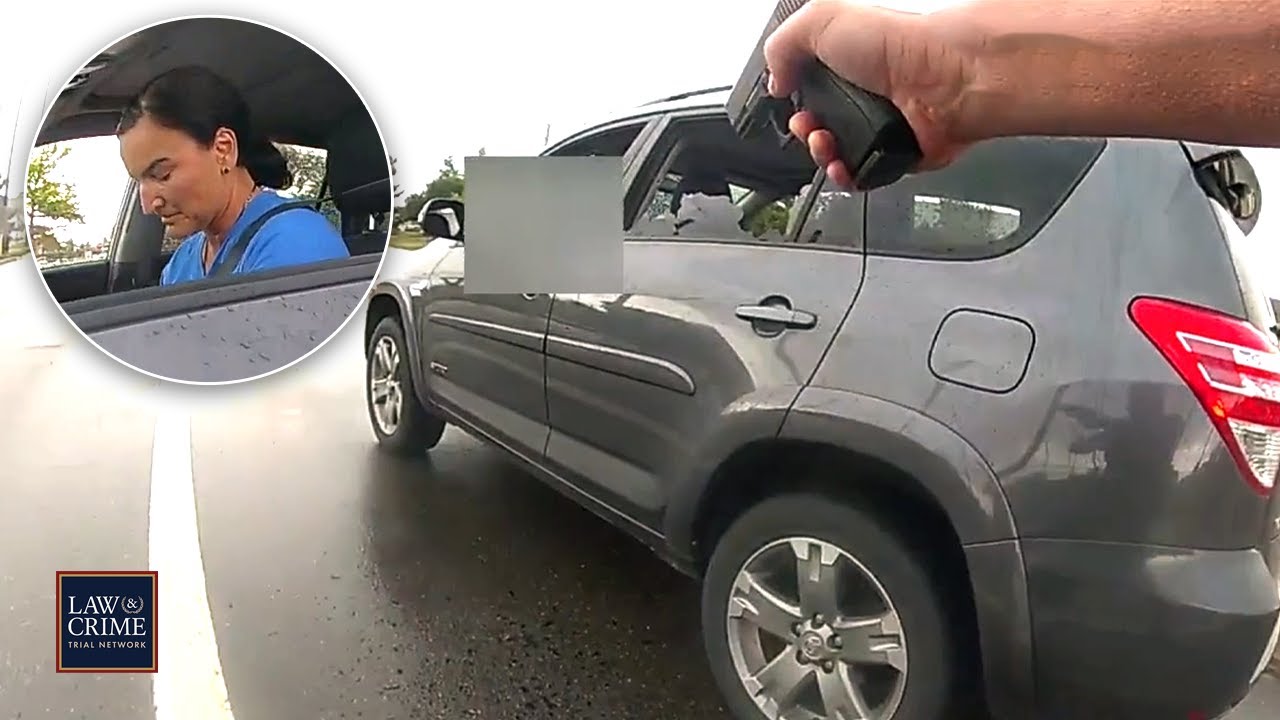
Bodycam: Colorado Cop Shoots Woman Who Allegedly Pulled Gun in Traffic Stop
5.0 / 5 (0 votes)