Proses Produksi Papan Komposit / Wood Plastic Composite (WPC)
Summary
TLDRThis video explains the process of making composite boards from wood and plastic waste. It covers the steps involved, starting with the preparation of materials like plastic pellets and wood powder. These are then mixed, dried, and molded into boards, followed by compression and cooling. The final product is tested for physical and mechanical properties, including density, moisture content, and bending strength. The composite boards are durable, water- and fire-resistant, making them ideal for use in interior and exterior building applications. This sustainable material offers an innovative solution for utilizing waste materials.
Takeaways
- 😀 Composite boards are made from a combination of wood waste and plastic waste or virgin plastic.
- 😀 The production process involves several stages, starting with raw material preparation.
- 😀 Raw materials include two main components: matrix (plastic beads and waste plastic) and filler (wood powder).
- 😀 Wood powder is sifted to obtain a fine texture before it is dried to reduce moisture content.
- 😀 After drying, the materials are mixed in a ratio of 70% plastic to 30% wood powder.
- 😀 The mixed materials are pressed into molds to form composite boards according to desired sizes.
- 😀 The boards are then subjected to compression to ensure they become solid and cohesive.
- 😀 After the boards are cooled to room temperature, they are cut to required dimensions.
- 😀 The boards undergo physical testing, such as density, water content, absorption, and thickness expansion.
- 😀 Mechanical properties like bending strength, break strength, and internal bonding strength are also tested.
- 😀 Composite boards are more fire and water-resistant compared to regular wooden boards, and they can still be nailed, sawed, and treated like wood.
Q & A
What is composite board made from?
-Composite board is made from a mixture of wood waste and plastic waste, combining materials like plastic pellets and wood powder to create a durable product.
Why is composite board preferred over traditional wood boards?
-Composite boards have unique characteristics such as resistance to fire and water, making them more durable and versatile for both interior and exterior applications.
What is the first step in the production of composite boards?
-The first step is the preparation of raw materials, which involves selecting and processing the matrix (plastic pellets and waste plastic) and filler (wood powder).
How is wood powder processed before use in composite board production?
-The wood powder is sifted to ensure it is fine and free of impurities, followed by drying to reduce moisture content, which helps prevent air pockets during pressing.
What is the typical ratio of plastic to wood powder used in the composite board mixture?
-The typical ratio is 70% plastic and 30% wood powder. This ensures a balance between durability and flexibility in the final product.
What is the purpose of pressing and molding the mixture in the production process?
-Pressing and molding the mixture helps fuse the plastic and wood powder into a solid, unified composite, giving the board its shape and structural integrity.
How are the composite boards cooled after molding?
-After molding, the composite boards are left to cool at room temperature. This step ensures that the boards adjust to the environmental conditions and are ready for further processing.
What testing is done on the composite boards after production?
-The boards undergo physical testing (such as density, moisture content, and absorption rate) and mechanical testing (including flexural strength, breaking strength, and internal bonding) to assess their quality and durability.
Can composite boards be cut, nailed, or shaped like traditional wood?
-Yes, composite boards maintain the flexibility of wood, allowing them to be cut, nailed, or shaped in the same way as traditional wood, which makes them versatile for various applications.
What are some common applications of composite boards?
-Composite boards are commonly used for flooring, wall paneling, and other decorative or structural applications both inside and outside buildings due to their durability and resistance to the elements.
Outlines
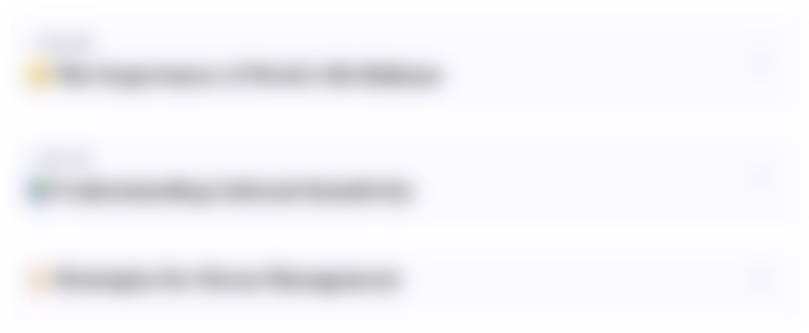
Dieser Bereich ist nur für Premium-Benutzer verfügbar. Bitte führen Sie ein Upgrade durch, um auf diesen Abschnitt zuzugreifen.
Upgrade durchführenMindmap
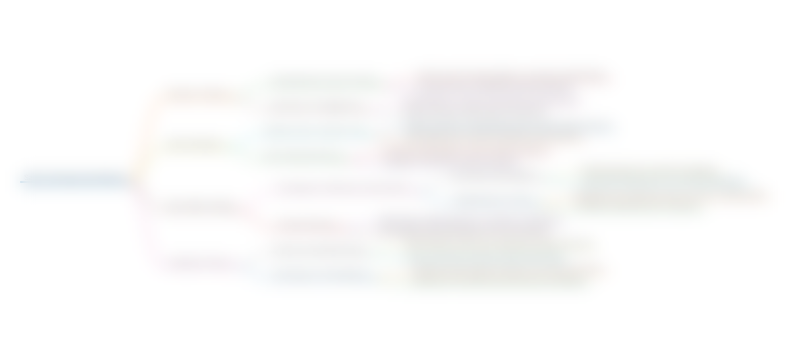
Dieser Bereich ist nur für Premium-Benutzer verfügbar. Bitte führen Sie ein Upgrade durch, um auf diesen Abschnitt zuzugreifen.
Upgrade durchführenKeywords
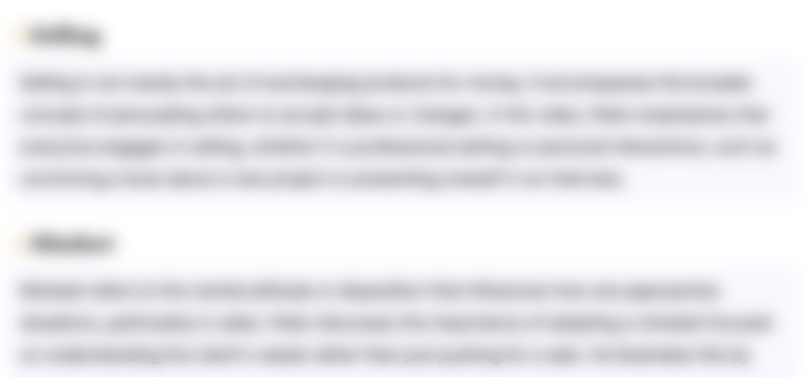
Dieser Bereich ist nur für Premium-Benutzer verfügbar. Bitte führen Sie ein Upgrade durch, um auf diesen Abschnitt zuzugreifen.
Upgrade durchführenHighlights
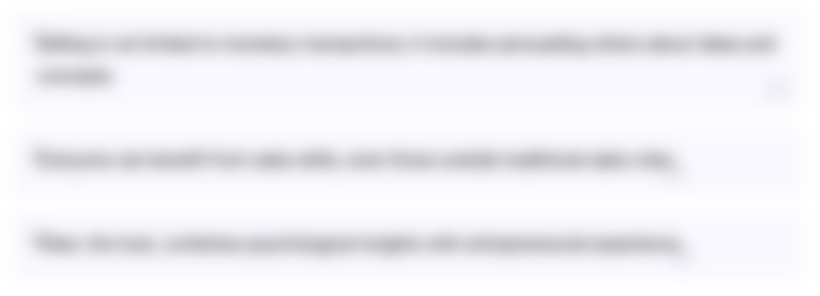
Dieser Bereich ist nur für Premium-Benutzer verfügbar. Bitte führen Sie ein Upgrade durch, um auf diesen Abschnitt zuzugreifen.
Upgrade durchführenTranscripts
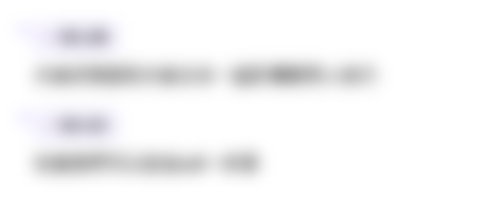
Dieser Bereich ist nur für Premium-Benutzer verfügbar. Bitte führen Sie ein Upgrade durch, um auf diesen Abschnitt zuzugreifen.
Upgrade durchführenWeitere ähnliche Videos ansehen

DBS Foundation Business for Impact Grant Award Programme 2023: Plana
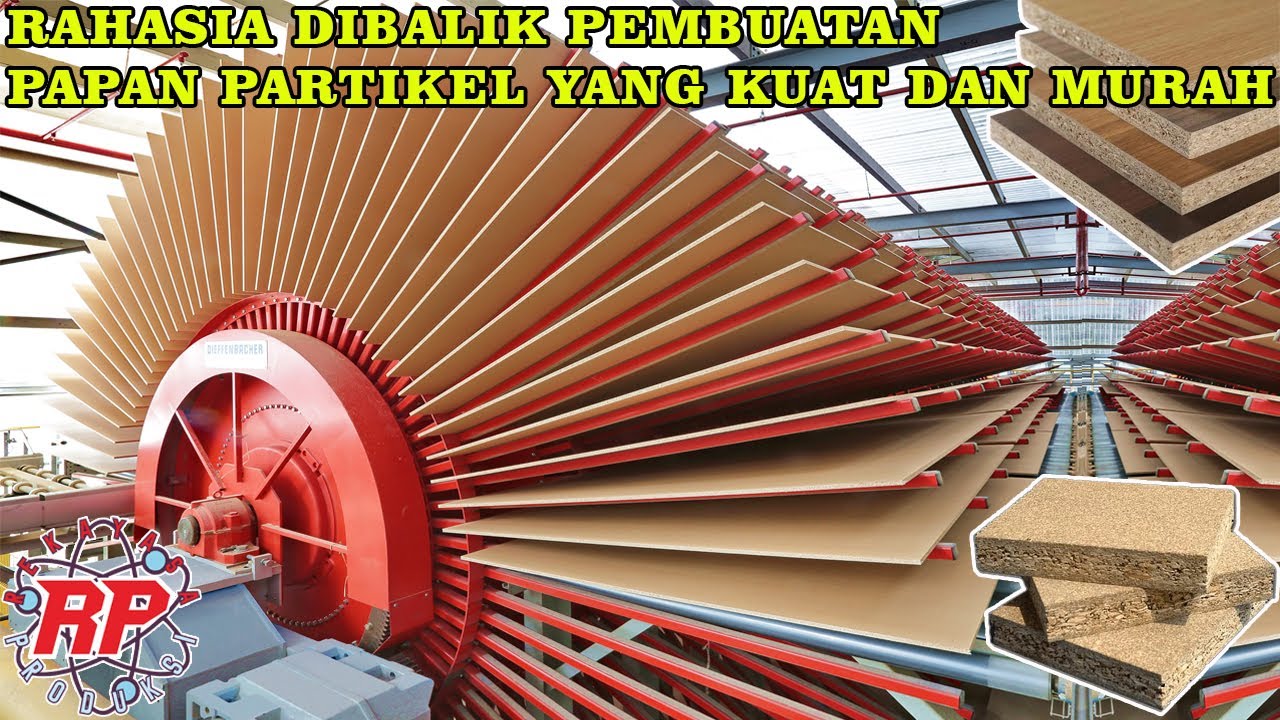
INILAH TEKNOLOGI TERBARU UNTUK MEMBUAT PAPAN PARTIKEL! TEROBOSAN REVOLUSIONER DI INDUSTRI
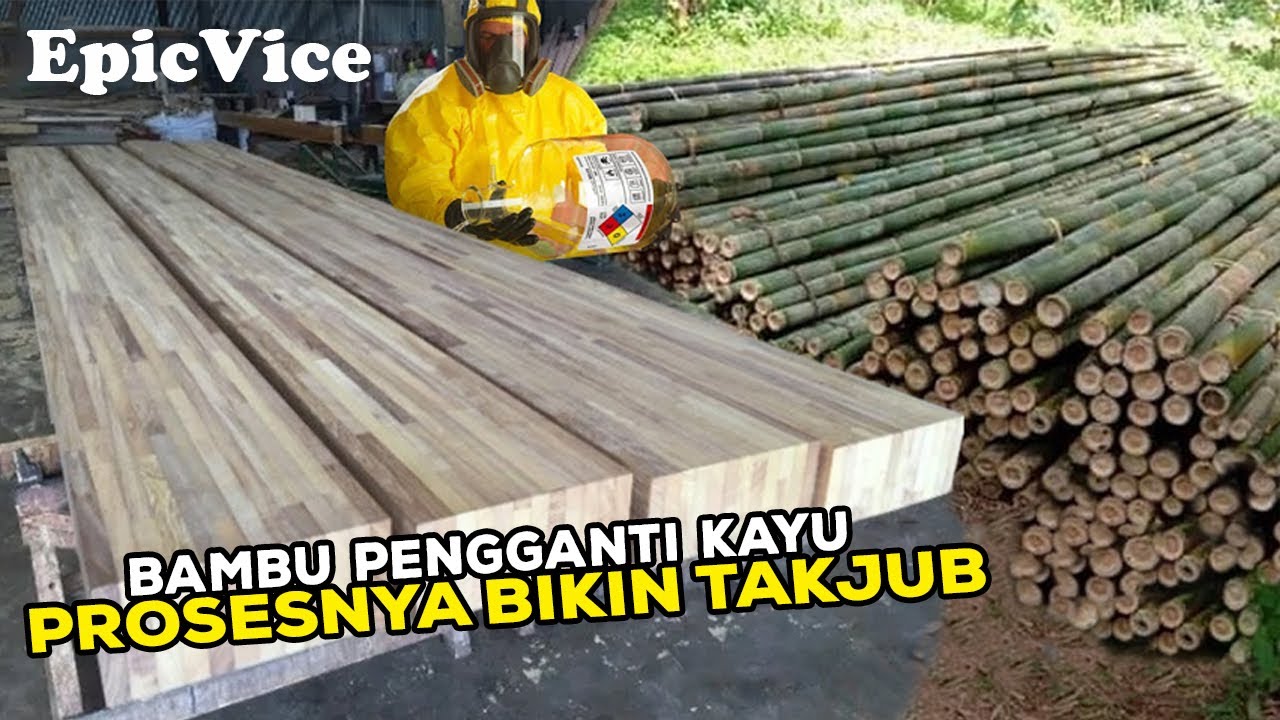
Gak Lama Lagi, KAYU Akan TERGANTI...!!! Canggihnya PABRIK Pengolahan Bambu Menjadi Papan

Animasi Pengenalan dan Pembuatan Ecobrick
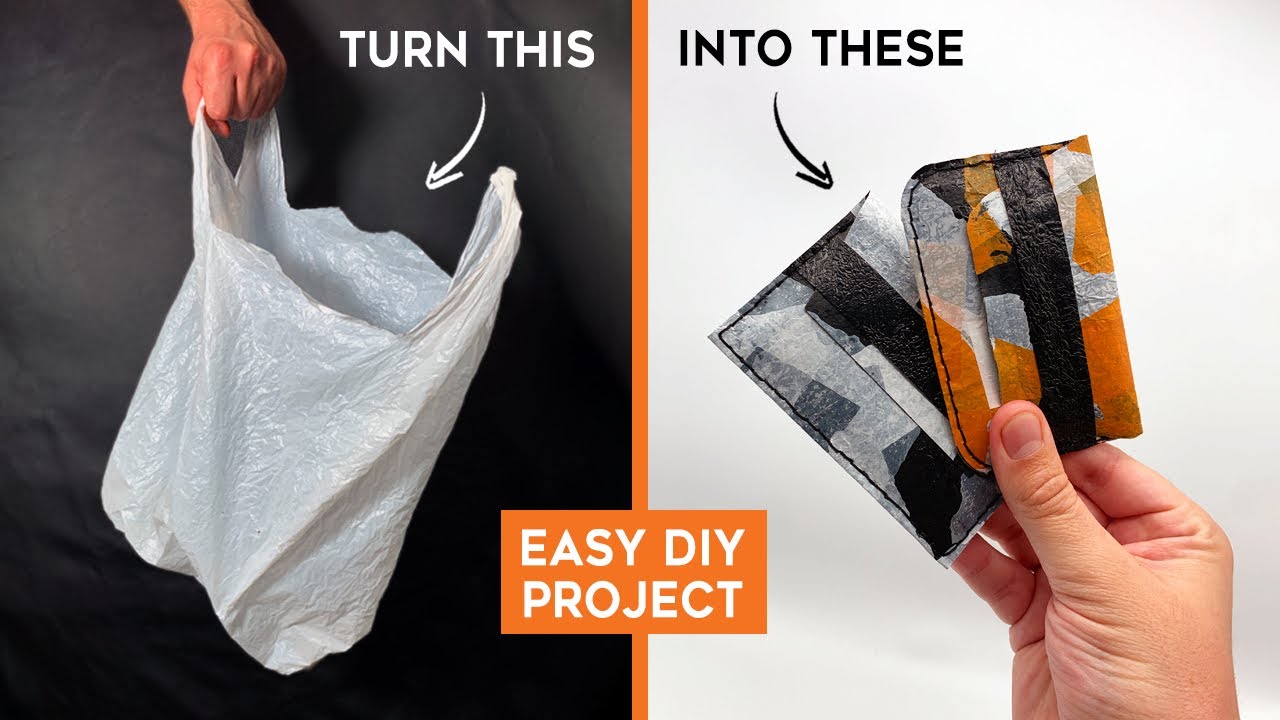
Beginners' Guide to Plastic Bag Recycling - How to Make a Wallet
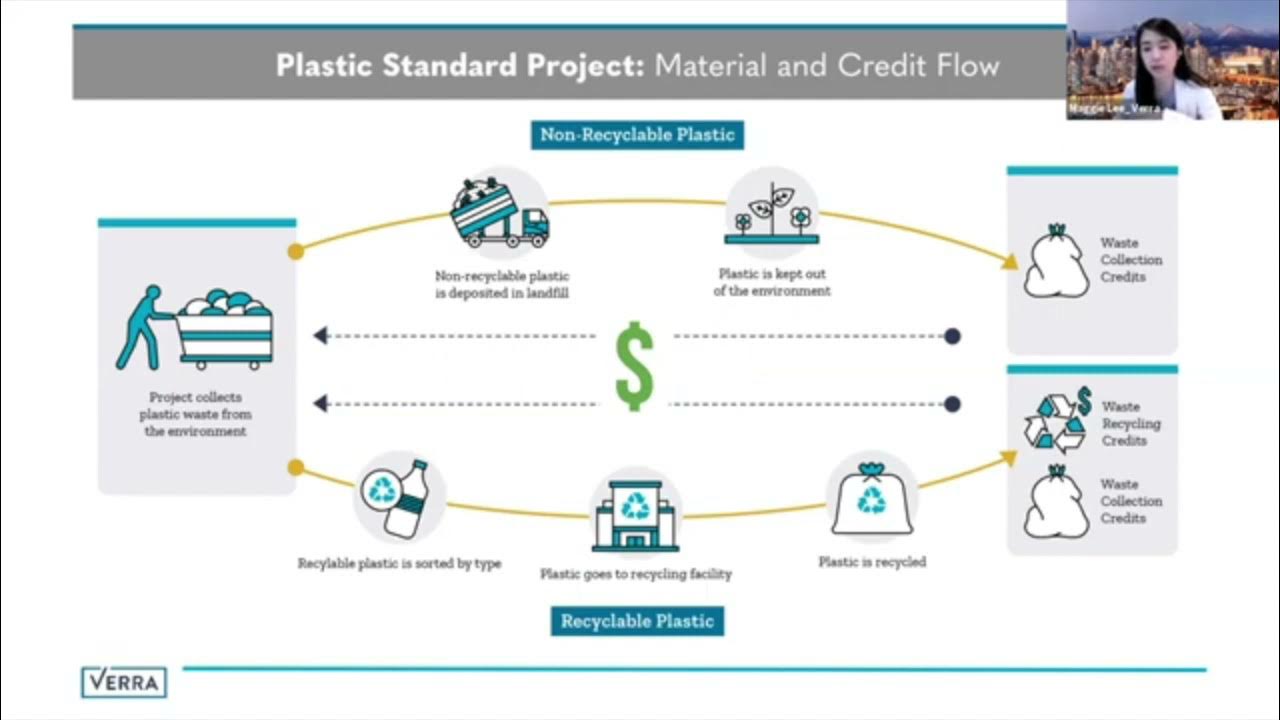
Plastic Standard Project by Verra
5.0 / 5 (0 votes)