Recycled Plastic Bricks - Do They Work?
Summary
TLDRThe video explores the potential of recycled plastic bricks as a solution to global housing and pollution issues. It features Circular 11, a company turning plastic waste into bricks. Founders Ben and Connor discuss the process, challenges, and pivot from bricks to outdoor furniture due to technical and commercial risks. The video also includes insights from Rory, the original brick mold designer, who suggests humanitarian applications. The discussion highlights the need for innovation in recycling and sustainable construction materials.
Takeaways
- 🌍 Ben and Connor, co-founders of Circular 11, are tackling global housing and pollution issues by turning plastic waste into recycled bricks.
- 🔥 They were motivated by the harmful practice of open-air burning of plastic waste, which they witnessed during their stay in the Philippines.
- 🏗️ The bricks are created through a process of extrusion, where plastic is pumped into molds, making them stronger than concrete blocks.
- ♻️ Each brick contains about 1.5 kg of plastic, equivalent to roughly 1,000 milk bottle tops, highlighting the scalability of the process.
- 🚿 After molding, bricks are cooled in a water bath for 15-20 minutes before being demolded, ensuring they retain their shape and strength.
- 🏗️ The bricks interlock and can be quickly and easily assembled, making construction faster and more efficient.
- 🔧 Despite their strength, the bricks have limitations such as UV degradation, flammability, and creep, which require solutions like rendering or special framing.
- 🔄 The business has pivoted from producing bricks to creating outdoor furniture and landscaping products due to the technical and commercial risks associated with brick production.
- 🌳 Rory, the original designer of the brick mold, suggests that the best application for these bricks might be in disaster response and popup shelters.
- 🌱 The potential future for recycled plastic bricks lies in local, small-scale production, where waste is turned into construction materials that benefit the community.
Q & A
What is the primary goal of Circular 11's business?
-The primary goal of Circular 11's business is to turn plastic waste into recycled bricks to address global housing and pollution problems.
Why did Ben and Connor start Circular 11?
-Ben and Connor started Circular 11 after experiencing the negative effects of burning plastic waste in the Philippines, which motivated them to find a way to create value from mixed low-grade plastics.
How are the recycled plastic bricks made?
-The recycled plastic bricks are made through a process of extrusion, where plastic is pumped into a mold and then cooled in a water bath to harden.
What is the strength of the recycled plastic bricks compared to traditional concrete blocks?
-The recycled plastic bricks are actually stronger than concrete blocks, as mentioned in the script, they can support a load equivalent to 'a number of elephants'.
What are the challenges associated with the long-term use of recycled plastic bricks?
-The challenges include UV degradation, flammability, and creep (long-term sagging of the material). These can be mitigated with treatments like applying a render to protect from UV damage and using non-flammable renders for fire resistance.
Why did Ben and Connor pivot away from producing bricks?
-They pivoted away from producing bricks because the technical and commercial risks associated with developing a new product from low-grade plastics were too high for their small business.
What is the current focus of Circular 11's business after pivoting?
-After pivoting, Circular 11 now focuses on making outdoor furniture and landscaping products like benches, planters, tables, and fencing from waste plastic.
What is the significance of Rory's involvement in the development of the recycled plastic bricks?
-Rory was the original designer of the brick mold and his insights have been crucial in understanding the potential and limitations of the bricks, including their strength and durability.
What are the potential applications for recycled plastic bricks according to Rory?
-Rory suggests that the strongest application for the bricks is in humanitarian response and disaster relief, such as popup shelters made from waste like water bottles.
What is the current state of the second version of the recycled plastic brick?
-The second version of the recycled plastic brick is still in the early theoretical research stage, with no current funding to push the development further.
Outlines
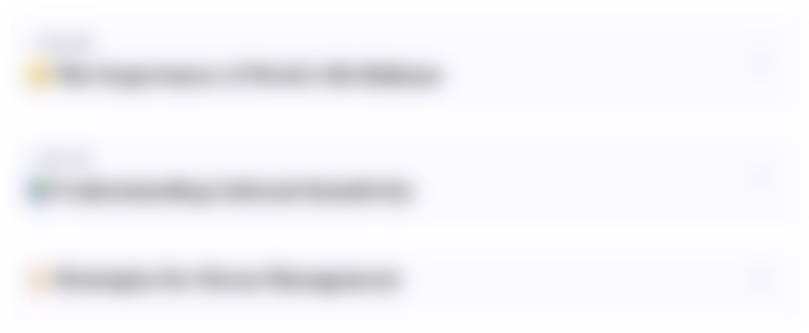
Dieser Bereich ist nur für Premium-Benutzer verfügbar. Bitte führen Sie ein Upgrade durch, um auf diesen Abschnitt zuzugreifen.
Upgrade durchführenMindmap
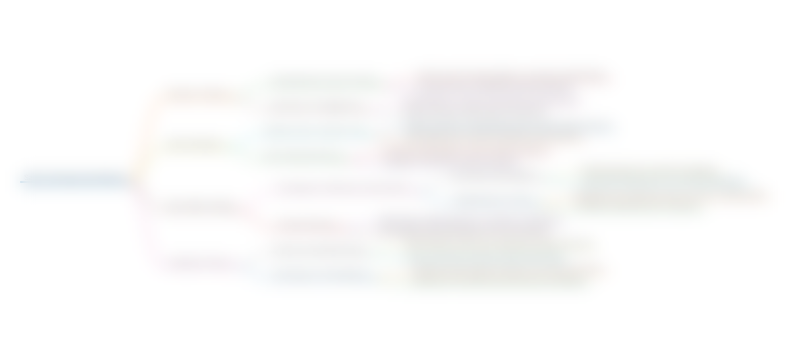
Dieser Bereich ist nur für Premium-Benutzer verfügbar. Bitte führen Sie ein Upgrade durch, um auf diesen Abschnitt zuzugreifen.
Upgrade durchführenKeywords
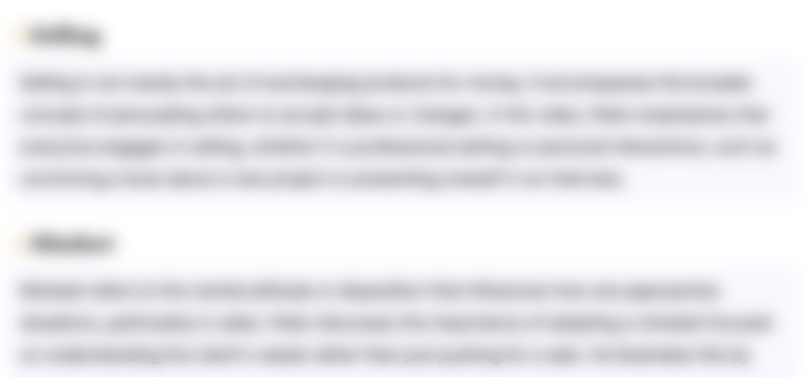
Dieser Bereich ist nur für Premium-Benutzer verfügbar. Bitte führen Sie ein Upgrade durch, um auf diesen Abschnitt zuzugreifen.
Upgrade durchführenHighlights
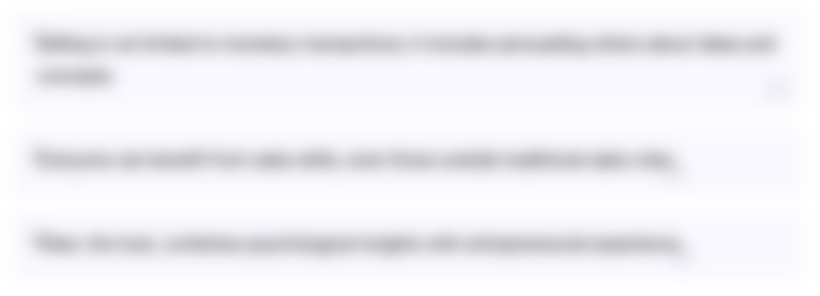
Dieser Bereich ist nur für Premium-Benutzer verfügbar. Bitte führen Sie ein Upgrade durch, um auf diesen Abschnitt zuzugreifen.
Upgrade durchführenTranscripts
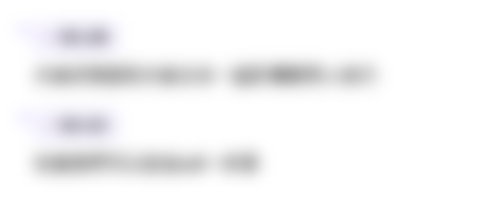
Dieser Bereich ist nur für Premium-Benutzer verfügbar. Bitte führen Sie ein Upgrade durch, um auf diesen Abschnitt zuzugreifen.
Upgrade durchführenWeitere ähnliche Videos ansehen

Plastic bricks in Kenya - NZAMBI MATEE - Young Champion of the Earth 2020 for Africa

Plastic Pollution: How Humans are Turning the World into Plastic

A radical plan to end plastic waste | Andrew Forrest
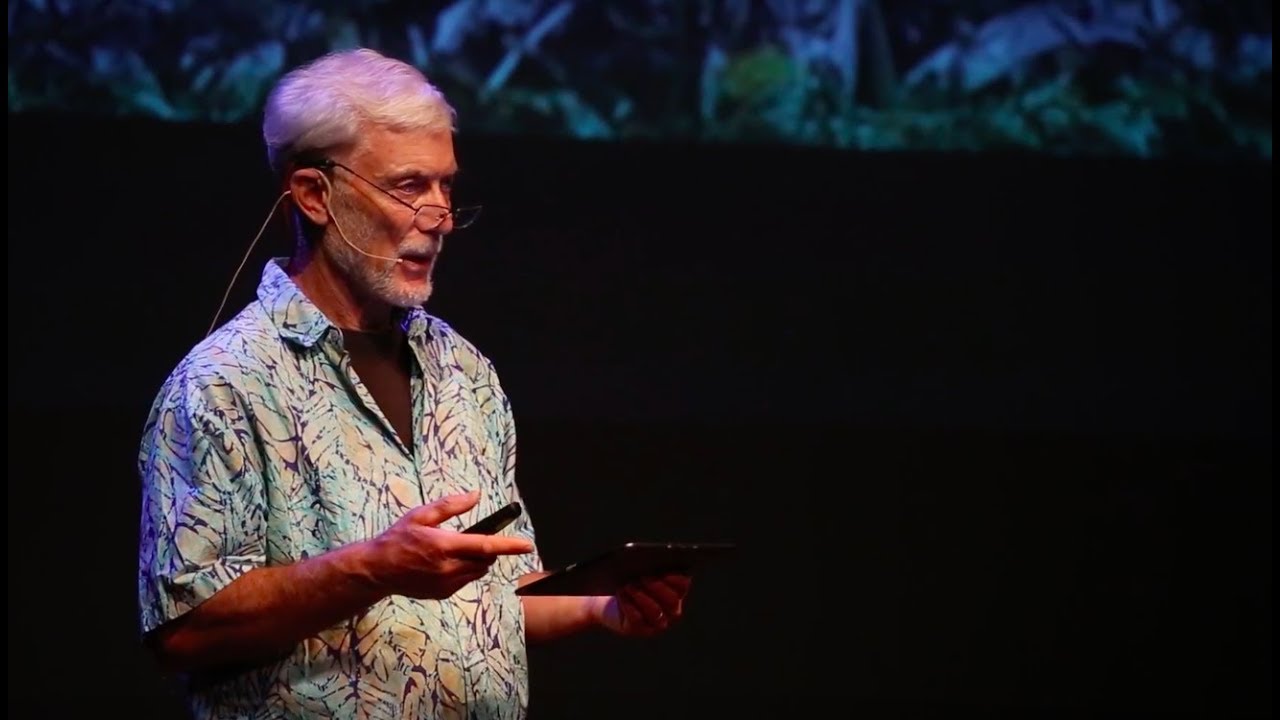
How we can stop the flow of plastic pollution into our oceans? | Tim Niemier | TEDxMeritAcademy

Tutorial Pembuatan Ecobrick

Di Mana Ujung Perjalanan Sampah Plastik yang Kamu Buang?
5.0 / 5 (0 votes)