Job Hazard Analysis (JHA) | Your ACSA Safety Training
Summary
TLDRA Job Hazard Analysis (JHA) is a critical risk assessment tool for health and safety programs, identifying and controlling job hazards. It should be conducted by a knowledgeable team including workers and supervisors. The process involves breaking tasks into steps, identifying potential health and safety hazards, assessing risks, and recommending mitigation strategies. JHAs are essential for establishing safe work procedures, training new employees, and investigating incidents, ensuring ongoing safety and reducing the risk of injury or environmental harm.
Takeaways
- 🔍 A Job Hazard Analysis (JHA) is a critical part of health and safety programs, used to identify and control job-related hazards.
- 👷♂️ JHA helps establish proper operating procedures and offers recommendations to prevent or eliminate hazards.
- 🚨 Many injuries or fatalities occur due to a lack of knowledge about the correct steps or potential job hazards.
- 👥 JHA should be conducted by a team including workers, supervisors, and relevant experts or specialists.
- 🔗 Involving a team reduces the chance of overlooking steps or hazards.
- 📝 The process begins by breaking the job into small, correctly ordered steps, ideally fewer than 10.
- ⚠️ Each step must be analyzed for potential health and safety hazards, which can be physical, chemical, biological, psychological, or conditions that endanger worker safety.
- 📊 Assessing the risk involves evaluating both the severity and the likelihood of each hazard occurring.
- 🛠️ Recommendations for hazard mitigation should be made immediately, considering elimination, substitution, or control measures like engineering, administrative controls, or PPE.
- 🔄 JHA is essential for communicating job hazards, forming the basis for safe work practices, and providing training for new employees.
- 🔄 Regular JHA reviews and updates are necessary for new tasks or when changes occur, ensuring ongoing safety and effectiveness of control methods.
Q & A
What is a Job Hazard Analysis (JHA)?
-A Job Hazard Analysis (JHA) is a risk assessment tool used in health and safety programs to identify and control job-related hazards.
Why is it important to conduct a JHA?
-Conducting a JHA is important because it helps establish proper operating procedures and provides recommendations for preventing or eliminating hazards, reducing the risk of injury or death among workers.
Who should be involved in conducting a JHA?
-A JHA should be conducted by a team familiar with the task, including one or more workers familiar with the job, supervisors, and any other relevant experts or specialists.
How should a job be broken down for a JHA?
-A job should be broken down into small steps, each representing a part of the operation necessary to advance the work, with a focus on not making the steps too general or too detailed.
What is the recommended maximum number of steps for a JHA?
-It is recommended to describe the job in fewer than 10 steps for a JHA.
What are the two types of hazards identified in a JHA?
-The two types of hazards identified in a JHA are health hazards, which may cause ill health effects, and safety hazards, which may endanger the immediate safety of workers.
How should potential hazards be assessed in a JHA?
-Potential hazards should be assessed by identifying what could lead to injury, illness, or environmental harm, and then ranking each hazard based on severity and probability of occurrence.
What recommendations should be made for each identified hazard?
-Recommendations should focus on eliminating the hazard, substituting it with something less dangerous, or controlling the hazard through engineering, administrative controls, or personal protective equipment (PPE).
How often should JHAs be conducted or reviewed?
-JHAs should be conducted for each new task and reviewed at regular intervals or when a change in the task has occurred.
What is the purpose of a JHA in terms of employee safety and training?
-A JHA serves to communicate job hazards, form the basis for safe work practices and procedures, and provide step-by-step training for new employees. It also aids in investigations in case of injuries or illnesses.
Why is it necessary to continually monitor tasks and confirm the effectiveness of control methods after a JHA?
-Continual monitoring ensures that control methods are implemented and effective, helping to maintain employee safety and reduce the chances of injury, illness, and environmental damage.
Outlines
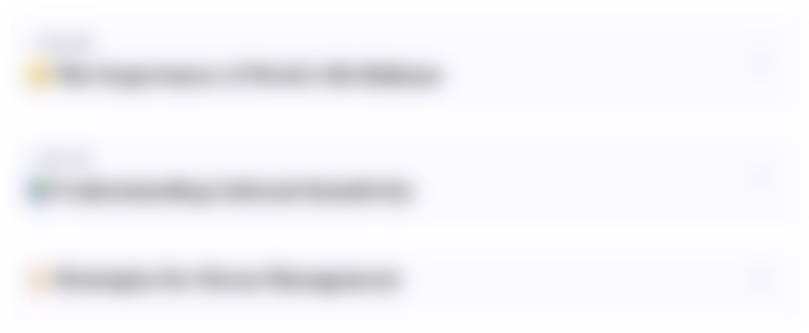
Dieser Bereich ist nur für Premium-Benutzer verfügbar. Bitte führen Sie ein Upgrade durch, um auf diesen Abschnitt zuzugreifen.
Upgrade durchführenMindmap
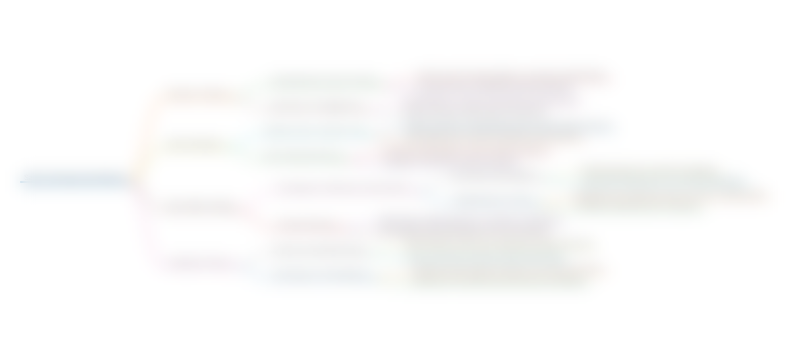
Dieser Bereich ist nur für Premium-Benutzer verfügbar. Bitte führen Sie ein Upgrade durch, um auf diesen Abschnitt zuzugreifen.
Upgrade durchführenKeywords
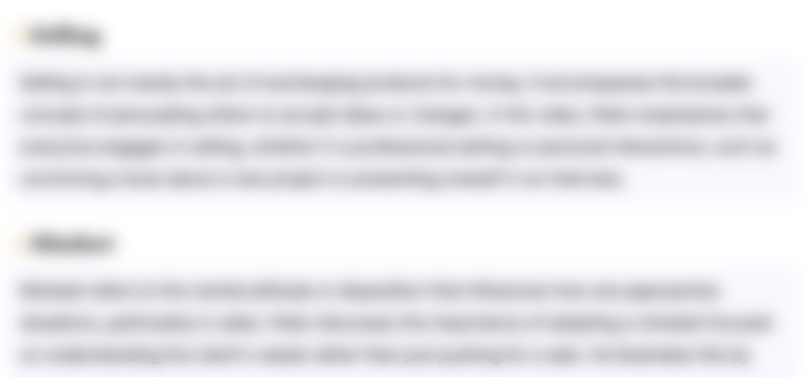
Dieser Bereich ist nur für Premium-Benutzer verfügbar. Bitte führen Sie ein Upgrade durch, um auf diesen Abschnitt zuzugreifen.
Upgrade durchführenHighlights
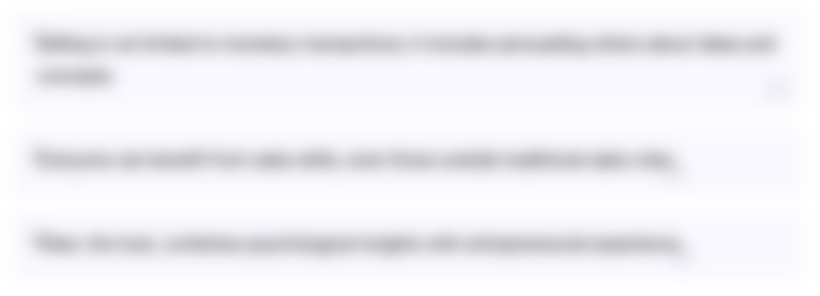
Dieser Bereich ist nur für Premium-Benutzer verfügbar. Bitte führen Sie ein Upgrade durch, um auf diesen Abschnitt zuzugreifen.
Upgrade durchführenTranscripts
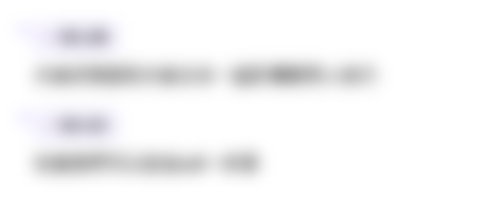
Dieser Bereich ist nur für Premium-Benutzer verfügbar. Bitte führen Sie ein Upgrade durch, um auf diesen Abschnitt zuzugreifen.
Upgrade durchführenWeitere ähnliche Videos ansehen

Cara Membuat Job Safety Analysis
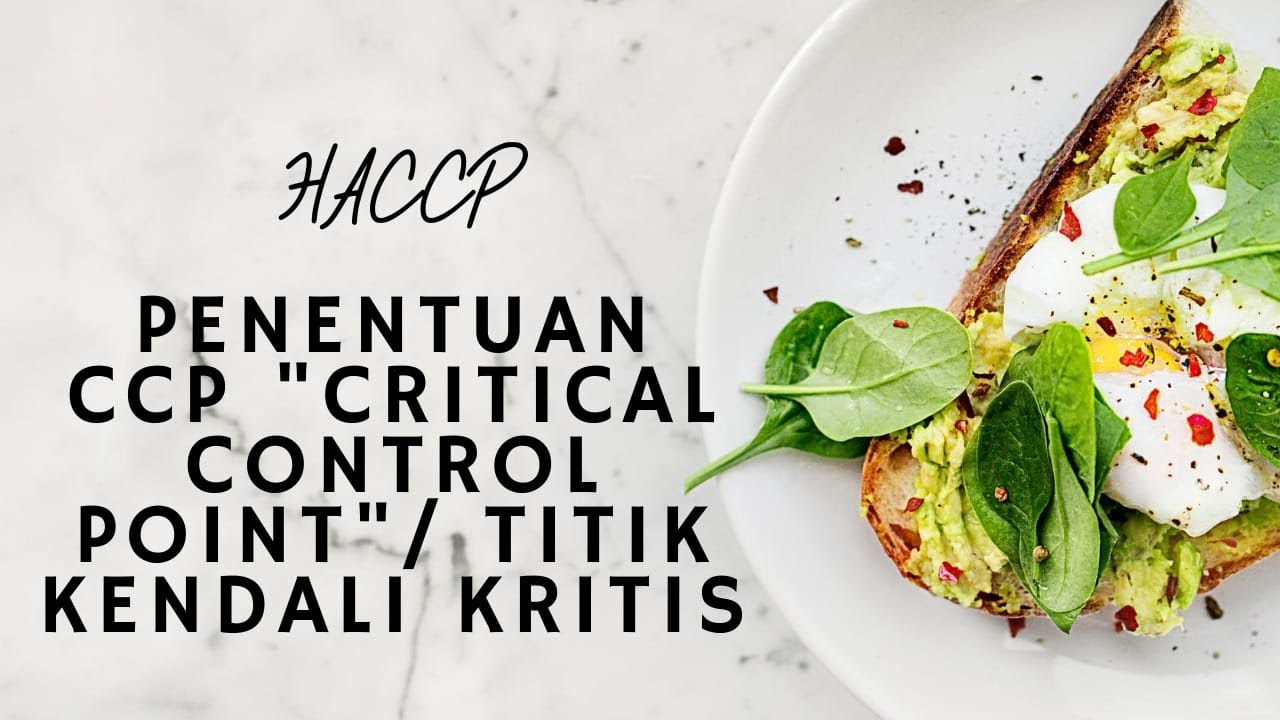
Penentuan CCP dalam HACCP

Lesson 2:Six steps of disaster risk assessment
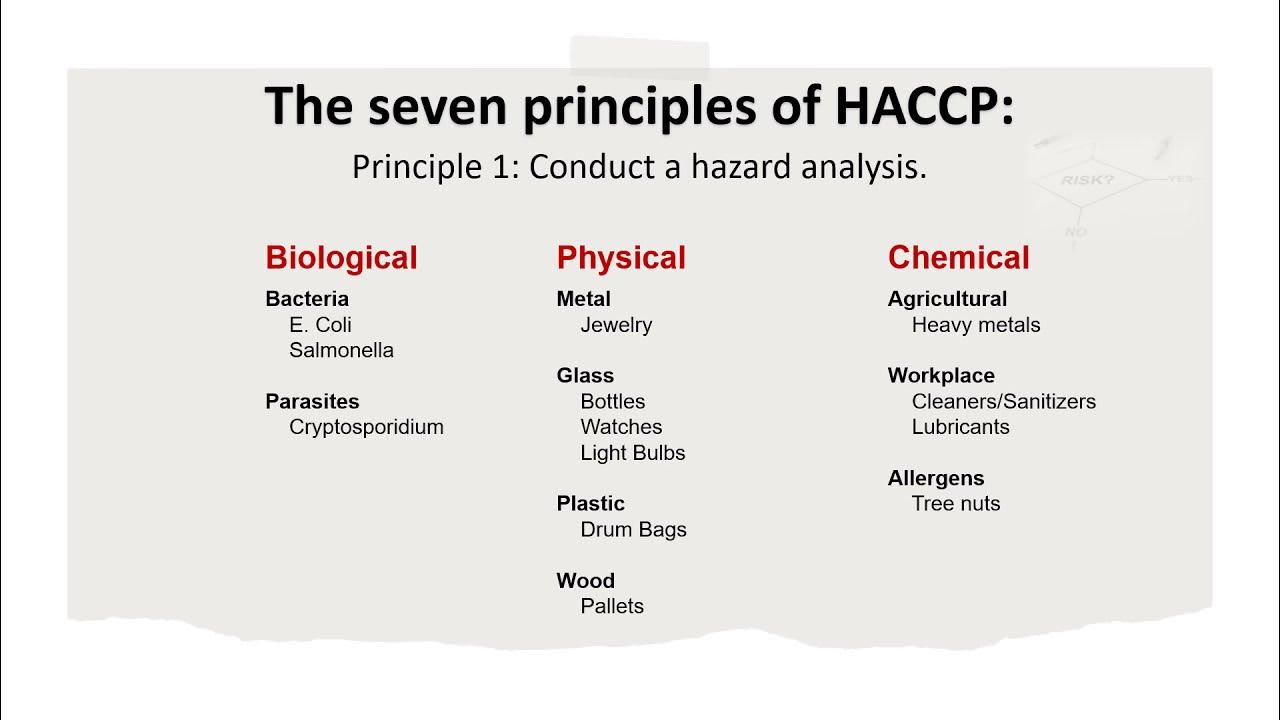
What is HACCP and what are the seven HACCP principles? HACCP Explained │ Food Safety

Hazard Analysis Framework

Definition Hazard Sources, Hazards, Harm and Risks in OHS | Occupational Health and Safety
5.0 / 5 (0 votes)