How To Make Custom Bifold Closet Doors // Woodworking | I Like To Make Stuff
Summary
TLDRIn this DIY project, Bob creates custom bi-fold doors for a uniquely sized closet. He starts with a door kit, modifies it by cutting MDF strips to the correct thickness and length, and assembles the frames. The doors are then fitted with inset panels, which are CNC-cut with a geometric pattern. Bob also shares a sponsored segment on Casper mattresses before detailing the installation process, including adjusting the track and hanging the doors. The video concludes with Bob expressing satisfaction with the cost-effective, customizable result.
Takeaways
- 😀 Bob shares his project of making custom bi-fold doors for a uniquely sized closet in his boy's room.
- 🛠️ The purchased kit for bi-fold doors includes a track and all necessary hardware, but requires custom door making.
- 🏡 Bob uses leftover pre-primed MDF wood to construct the door frames, cutting it down to the appropriate thickness and length.
- 🔩 To ensure the doors are sturdy and straight, Bob creates a frame structure with overlapping pieces and uses Brad nails for assembly.
- 🎨 The pre-primed MDF is sanded and painted to prepare it for the final look of the bi-fold doors.
- 🛠️ Bob uses a trim router with a rabbeting bit to create a rabbet on the backside of each door to accept the inset panel.
- 🛍️ The video features a sponsored segment for Casper mattresses, which Bob and his family use and recommend.
- 🚪 The bi-fold door assembly is straightforward with simple instructions and hardware provided in the kit.
- ✂️ Bob cuts down the door panels using white board material and designs a geometric pattern using a CNC machine.
- 🔨 Glaser points are used to attach the panels to the door frames, allowing for future removal and interchangeability.
- 🔩 The track is cut to size and installed to fit the closet opening, with the doors easily sliding into place for a custom fit.
Q & A
What was the main reason Bob decided to make custom bi-fold doors for his closet?
-Bob decided to make custom bi-fold doors because the kits available only come in a few styles and sizes, and the opening for his closet was uniquely sized.
What materials did Bob use to make the door frames?
-Bob used leftover pre-primed MDF to make the door frames.
Why did Bob need to cut down the MDF strips on a table saw?
-Bob needed to cut down the MDF strips on a table saw to reduce their thickness to fit the door kit's requirement of doors between 1 and 1 3/8 inches.
How did Bob ensure all the door frame pieces were cut to the correct length?
-Bob clamped all the pieces together and cut them at once to ensure they were all cut to the correct length.
What special feature did Bob add to the door frames to make them stronger?
-Bob made each door out of two frames that overlap in different directions, which helps keep the doors strong and straight over time.
How did Bob attach the door frames together while the glue dried?
-Bob used Brad nails to hold the door frames together while the glue dried.
What tool did Bob use to cut a rabbet on the backside of each door?
-Bob used a trim router with a rabbeting bit to cut a rabbet on the backside of each door to accept the inset panel.
What is the purpose of the round corners in the rabbets that Bob created?
-The round corners in the rabbets are part of the design to accommodate the inset panels and ensure a proper fit.
How did Bob prepare the door frames for painting after the glue-up?
-Bob used an orbital sander to clean up all the surfaces, remove any glue squeeze-out, and get the frames ready for painting.
What type of hardware did Bob use to connect the doors to the frame?
-Bob used a simple DIY set of instructions and hardware that included hinges that don't require mortising, which can be screwed directly into place.
How did Bob ensure the bi-fold doors were hung evenly?
-Bob adjusted the doors by sliding the top bracket and the bottom foot to ensure even gaps between the doors and along the sides.
What material did Bob use for the door panels, and why?
-Bob used white board material for the door panels because it was thin, lightweight, and had a thin coat of white on top, which allowed for a design to be CNC cut into it.
How did Bob ensure the panels could be easily swapped out in the future?
-Bob used Glaser points, which are metal points that get knocked into the backside of the frame, to attach the panels so they could be easily removed and swapped out.
Outlines
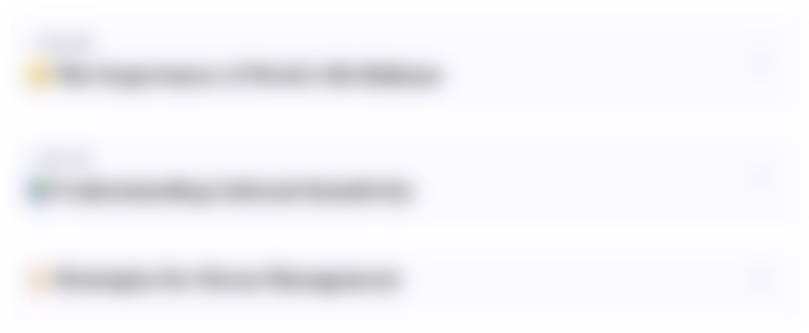
Dieser Bereich ist nur für Premium-Benutzer verfügbar. Bitte führen Sie ein Upgrade durch, um auf diesen Abschnitt zuzugreifen.
Upgrade durchführenMindmap
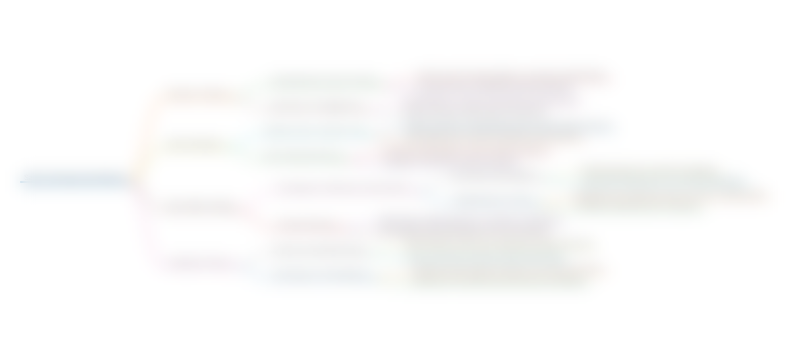
Dieser Bereich ist nur für Premium-Benutzer verfügbar. Bitte führen Sie ein Upgrade durch, um auf diesen Abschnitt zuzugreifen.
Upgrade durchführenKeywords
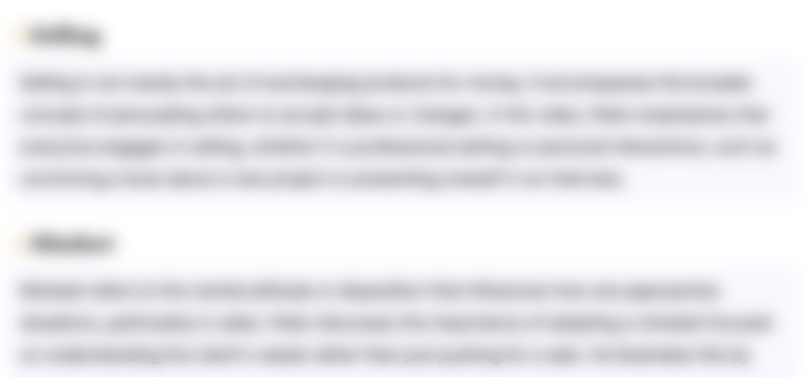
Dieser Bereich ist nur für Premium-Benutzer verfügbar. Bitte führen Sie ein Upgrade durch, um auf diesen Abschnitt zuzugreifen.
Upgrade durchführenHighlights
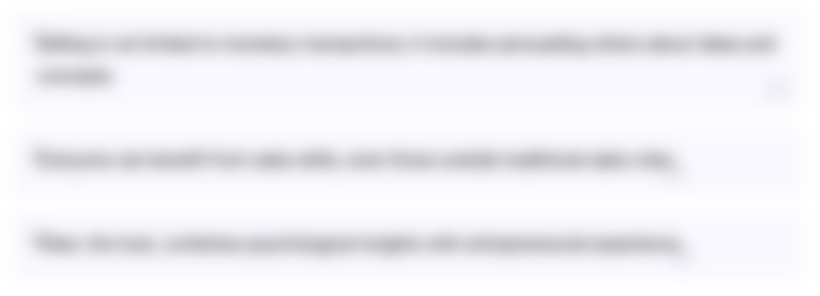
Dieser Bereich ist nur für Premium-Benutzer verfügbar. Bitte führen Sie ein Upgrade durch, um auf diesen Abschnitt zuzugreifen.
Upgrade durchführenTranscripts
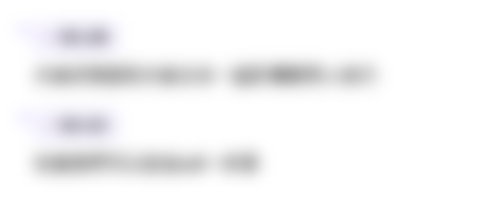
Dieser Bereich ist nur für Premium-Benutzer verfügbar. Bitte führen Sie ein Upgrade durch, um auf diesen Abschnitt zuzugreifen.
Upgrade durchführenWeitere ähnliche Videos ansehen

Armadio a muro fai da te con ante IKEA pax
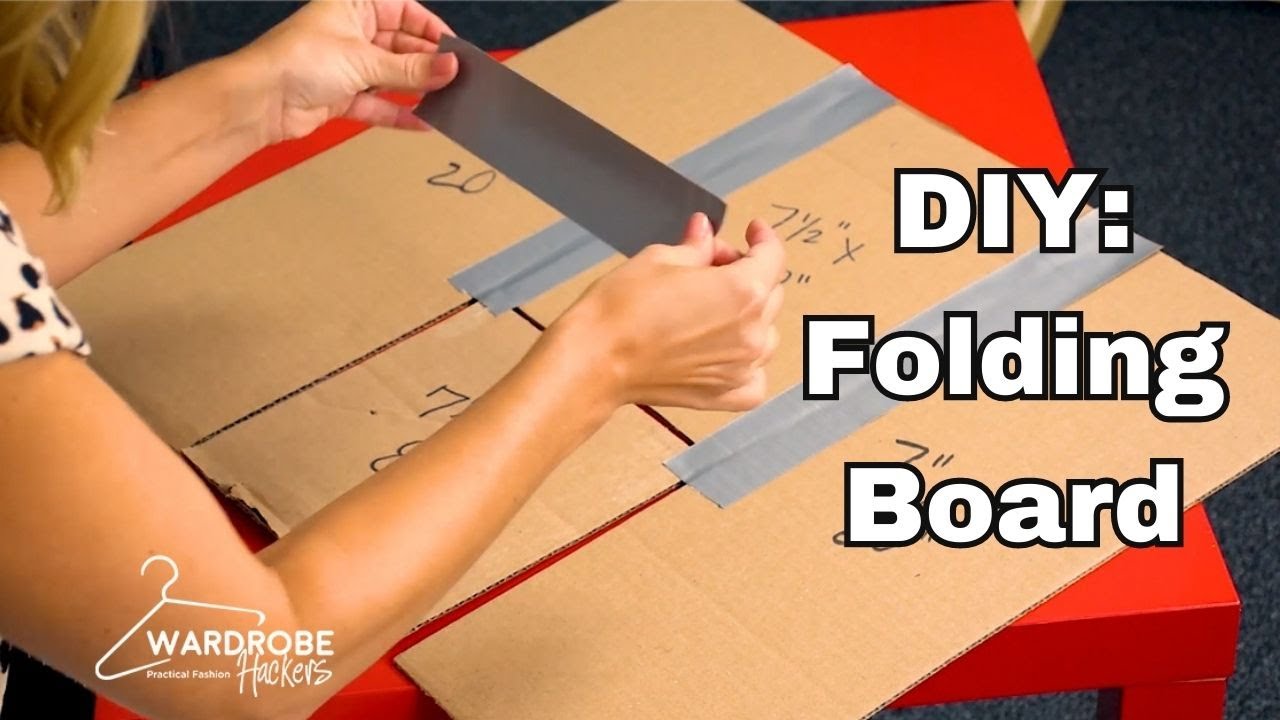
How to Make a DIY Kids Shirt Folding Board for Super Cheap

Orderan Langka ! Ampe 3Jt ... Bikin Papan Nama Ruangan / Kelas Untuk SMP Lab
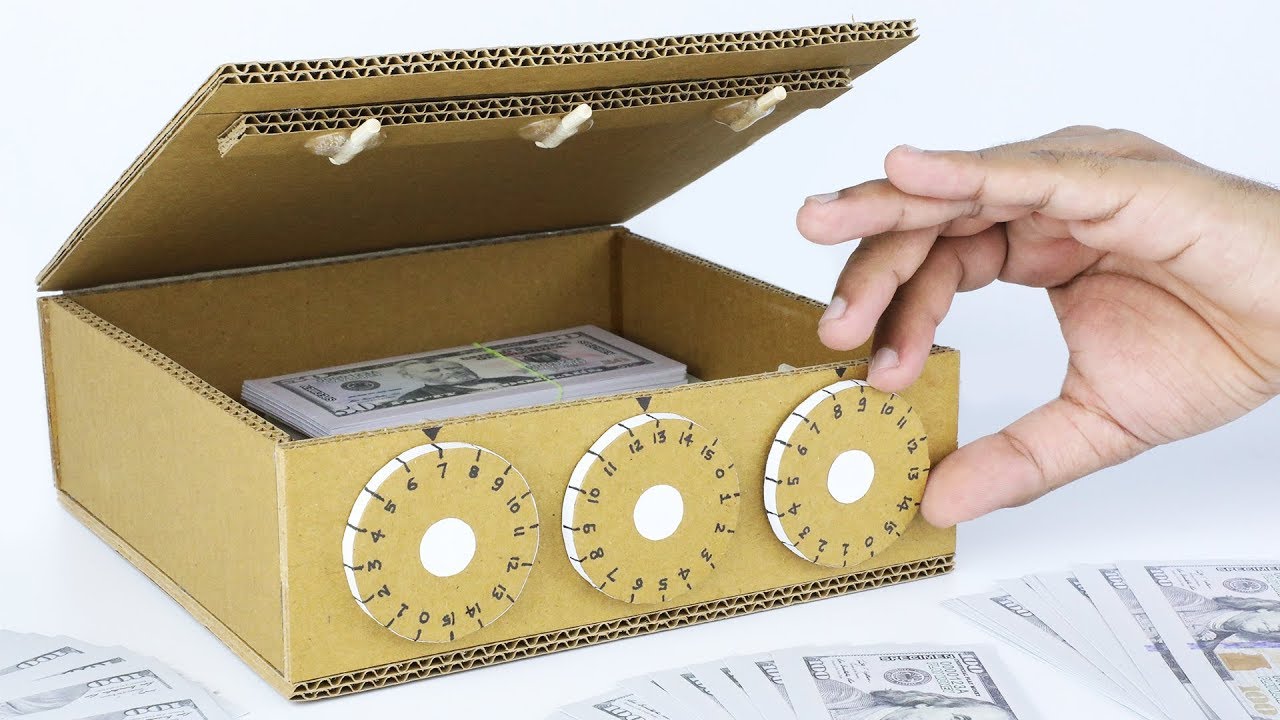
How to make safe using Cardboard
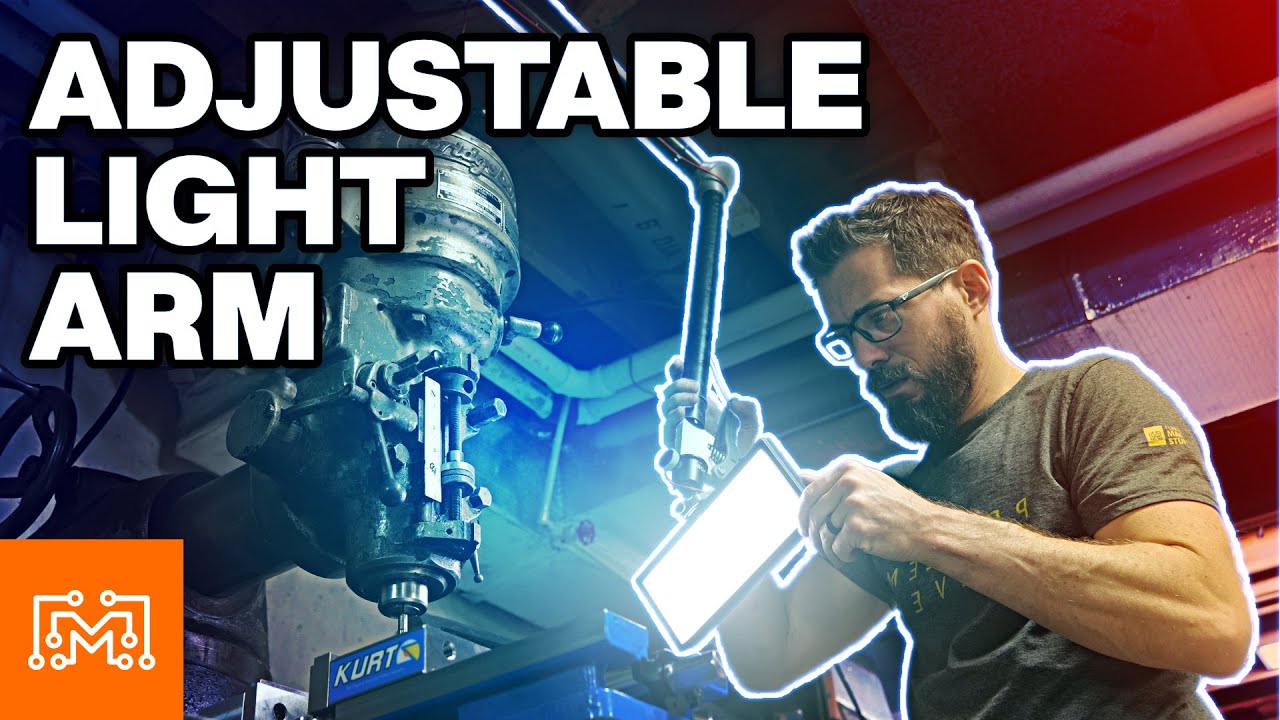
Adjustable Work Light Arm | I Like To Make Stuff
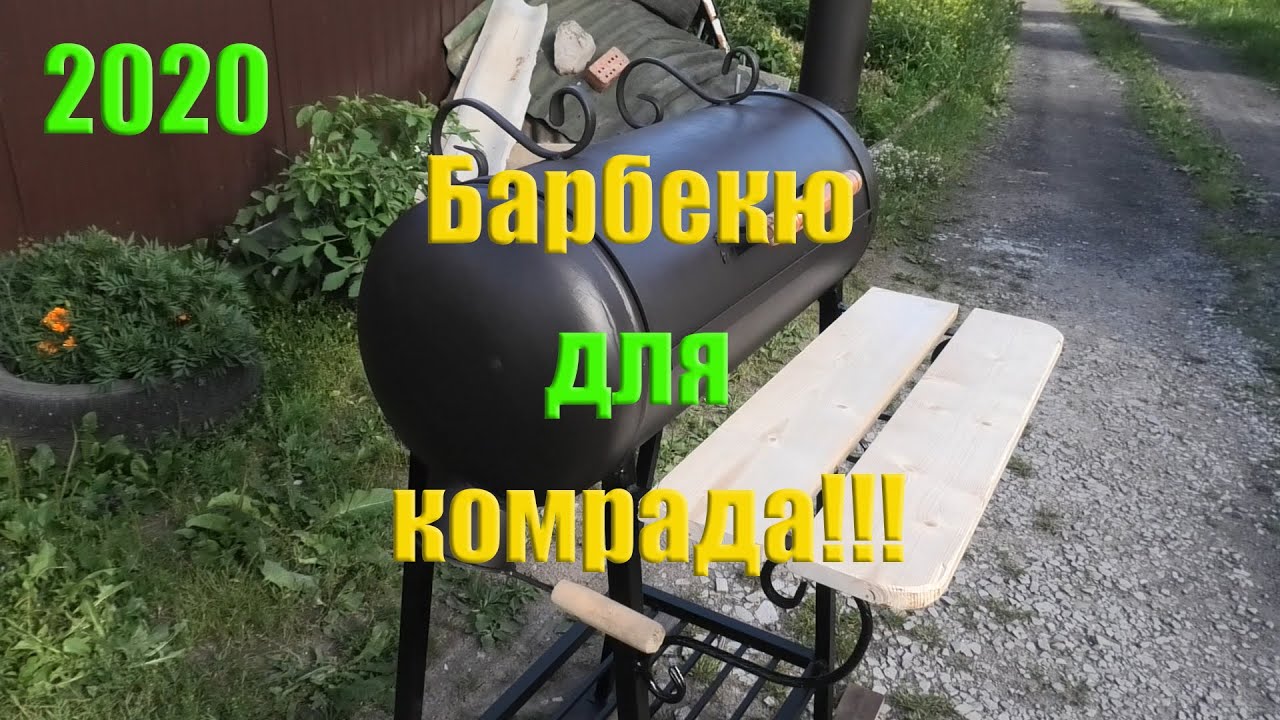
Барбекю смокер, из пропанового баллона, своими руками. 2020
5.0 / 5 (0 votes)