PowerFlex 520 Series PID Demo
Summary
TLDRIn this ESN TV video, VFD specialist Mark Garner explains the use of the PowerFlex 520 series' P mode with trim capabilities. The P mode, integral for maintaining process feedback like pressure or flow, operates by generating an error value based on the difference between the PID feedback and a reference. Garner distinguishes between the single P control loop in the PowerFlex 523 and the two available in the PowerFlex 525, which can only be used one at a time. He illustrates exclusive control in a pumping application and trim control in a winder application, demonstrating how the P mode adjusts motor speed to maintain set points. The video concludes with a practical demonstration using CCW software and emphasizes the importance of consulting the user manual for optimal P tuning.
Takeaways
- 🔧 The Powerflex 520 series drives feature a P (Proportional, Integral, Derivative) control loop designed for maintaining process feedback like pressure, flow, or tension at a set point.
- 🔄 The P Loop operates by calculating the error between the PID feedback and the reference, adjusting the frequency output to minimize this error.
- 📈 Powerflex 523 has one P control loop, while Powerflex 525 has two, though only one can be used at a time.
- 🎛️ Two common configurations for the P Loop are exclusive control and trim control, each serving different automation needs.
- 🚰 In exclusive control, the P output becomes the sole frequency command, as seen in pumping applications where system pressure is the focus.
- 📏 Trim control adds the PID output to the speed reference, useful in applications like winders where tension is managed against a master speed reference.
- 🛠️ Demonstration of P with trim control is shown using CCW software, where the setup includes selecting P1 output, P set point, and analog input for feedback.
- ⚙️ Keypad frequency is adjustable and trims the motor speed in response to changes in analog input voltage, within set limits.
- 📚 P tuning can be complex and may require trial and error; consulting the Powerflex 525 user manual and application notes is advised for optimal setup.
- 🤝 For further assistance or to understand P control theory better, reaching out to a local ESN account manager or automation specialist is recommended.
Q & A
What does 'P' stand for in the context of the PowerFlex 520 series drives?
-In the context of the PowerFlex 520 series drives, 'P' stands for Proportional, Integral, Derivative, which are control loop features built into the drives.
How does the P Loop in the PowerFlex 520 series work?
-The P Loop works by subtracting the PID feedback from a reference and generating an error value. It then reacts to this error based on the P gains and outputs a frequency to reduce the error value to zero.
What is the difference between PowerFlex 523 and PowerFlex 525 in terms of P control loops?
-The PowerFlex 523 has one P control loop, while the PowerFlex 525 has two P control loops, but they can only be used one at a time.
What are the two basic configuration examples where the P Loop may be used?
-The two basic configuration examples where the P Loop may be used are exclusive control and trim control.
In a pumping application, how does the P Loop maintain the desired system pressure set point?
-In a pumping application, the P reference equals the desired system pressure set point, and the pressure transducer signal provides PID feedback to the drive. Fluctuations in actual system pressure due to changes in flow result in a PID error value, and the drive adjusts the output frequency to correct the P error value, thus maintaining the desired system pressure set point.
How does trim control work in a winder application using the P Loop?
-In a winder application, the PID output is added to the speed reference. The P reference equals the equilibrium set point, and the dancer potentiometer signal provides PID feedback to the drive. As tension increases or decreases during the winding, the speed reference is trimmed to compensate, maintaining tension near the equilibrium set point.
What is the purpose of the setup wizard in the CCW software for configuring P with trim control?
-The setup wizard in the CCW software is used to configure P with trim control by setting up parameters such as speed reference, P set point, P feedback select, and keypad frequency.
What is the minimum and maximum frequency limits when using P with trim control in the demonstration?
-In the demonstration, the minimum frequency limit is 37 Hertz, which is three Hertz below the base frequency of 40 Hertz, and the maximum frequency limit is 43 Hertz.
Why is it recommended to consult the PowerFlex 525 user manual and application notes for setting up PID control?
-It is recommended to consult the PowerFlex 525 user manual and application notes for setting up PID control because P tuning can be complex and might require trial and error to achieve optimal results. The manual and notes provide detailed instructions specific to the application.
What is the importance of understanding P control theory for achieving effective and stable control of processes?
-Understanding P control theory is important for achieving effective and stable control of processes because it helps in setting up the correct parameters and understanding how the P Loop reacts to errors and adjusts the output frequency accordingly.
Outlines
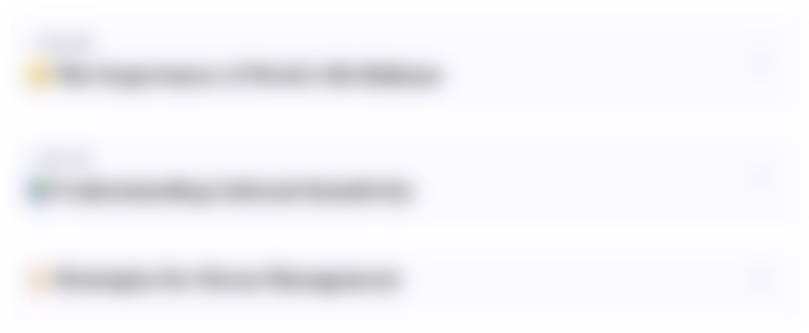
Dieser Bereich ist nur für Premium-Benutzer verfügbar. Bitte führen Sie ein Upgrade durch, um auf diesen Abschnitt zuzugreifen.
Upgrade durchführenMindmap
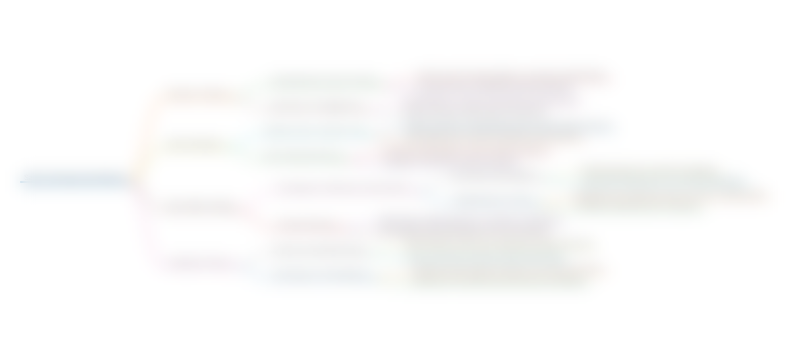
Dieser Bereich ist nur für Premium-Benutzer verfügbar. Bitte führen Sie ein Upgrade durch, um auf diesen Abschnitt zuzugreifen.
Upgrade durchführenKeywords
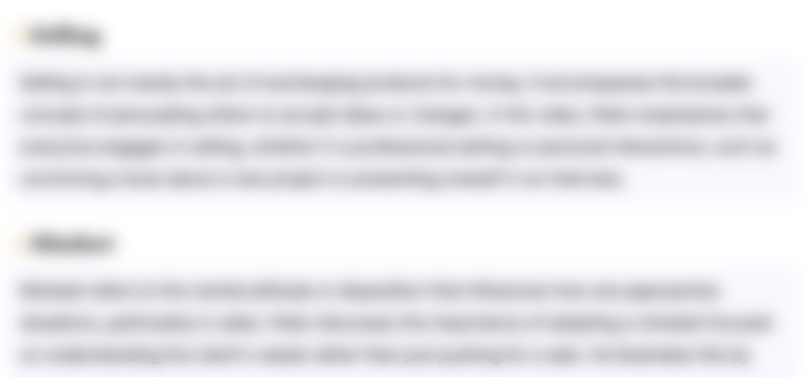
Dieser Bereich ist nur für Premium-Benutzer verfügbar. Bitte führen Sie ein Upgrade durch, um auf diesen Abschnitt zuzugreifen.
Upgrade durchführenHighlights
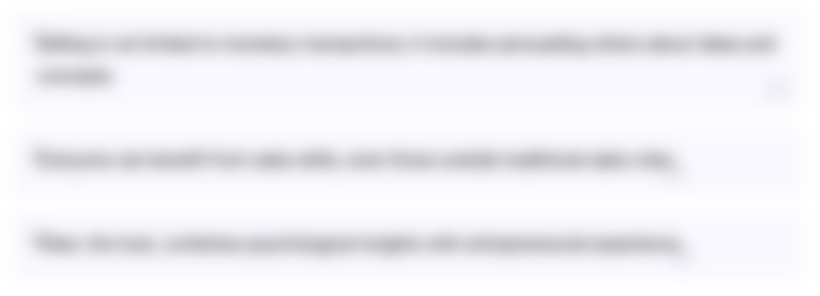
Dieser Bereich ist nur für Premium-Benutzer verfügbar. Bitte führen Sie ein Upgrade durch, um auf diesen Abschnitt zuzugreifen.
Upgrade durchführenTranscripts
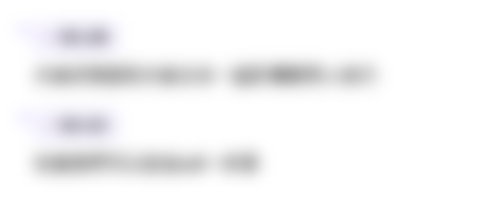
Dieser Bereich ist nur für Premium-Benutzer verfügbar. Bitte führen Sie ein Upgrade durch, um auf diesen Abschnitt zuzugreifen.
Upgrade durchführen5.0 / 5 (0 votes)