Machine Vision Basics 06 - Camera Selection
Summary
TLDRThis video script delves into the intricacies of machine vision for quality control, emphasizing the importance of camera and lighting selection. It covers the factors influencing camera choice, such as product size, defect detection, accuracy thresholds, and process speed. The script introduces two types of camera systems: smart cameras with integrated tools and algorithms, and vision system processors that handle image processing separately. It also highlights the capabilities of these systems in performing OCR and barcode reading, showcasing their versatility in industrial applications.
Takeaways
- 📐 Camera Selection: The process of selecting a camera for machine vision applications involves considering product size, defect size, accuracy requirements, and process speed.
- 🔍 Accuracy Threshold: It's important to determine whether the inspection process needs to be 100% accurate or if a 90% accuracy is sufficient for the application.
- 🔄 Process Speed: The number of objects inspected per minute is a critical factor in camera selection, which can range from 30 to 300 or more.
- 🌈 Color vs Grayscale: The need for a color camera versus a grayscale camera is determined by the type of inspection and application requirements.
- 🛠️ Smart Camera vs Vision System Processor: There are two types of camera systems - smart cameras with built-in tools and algorithms, and vision system processors that handle the processing while cameras relay images.
- 🔌 Smart Camera Setup: Smart cameras have power and Ethernet cords and come with different lens sizes, filters, and built-in lighting.
- 🖼️ Vision System Processor Layout: Vision system processors manage multiple cameras, with each camera connected via Ethernet and powered over Ethernet, acting as 'dummy' cameras.
- 📊 Real-time Monitoring: Data Logic's machine vision software offers real-time monitoring and statistics, including pass and fail rates, through a display module or software interface.
- 🔤 OCR Capabilities: The machine vision cameras are capable of performing optical character recognition (OCR), useful for reading barcodes and characters on objects.
- 🔢 Barcode Reading: While barcode readers are preferred for barcode-only tasks, machine vision cameras are useful for simultaneous object inspection and barcode reading.
- 📈 Data Presentation: The script mentions the use of pie charts and other statistics to represent the total counts, passes, and fails in the inspection process.
Q & A
What are the common factors to consider when selecting a machine vision camera?
-When selecting a machine vision camera, one should consider the product size, minimum defect size, required accuracy, threshold for passing, process speed, and whether a color or grayscale camera is needed.
What is the importance of accuracy in machine vision applications?
-Accuracy in machine vision is crucial as it determines the reliability of the inspection process. It can vary from needing to be 100% correct to being acceptable at 90% accuracy, depending on the application requirements.
How does the inspection speed affect the choice of machine vision system?
-The inspection speed, measured in objects inspected per minute, influences the choice of system. Higher speeds may require more advanced or multiple cameras to maintain accuracy and efficiency.
What is the difference between a smart camera and a vision system processor?
-A smart camera has all the tools and algorithms built-in, with power and Ethernet coming directly to the camera. A vision system processor, on the other hand, handles the processing while the cameras act as 'dumb' relays of images back to the processor.
Why would one choose a smart camera over a vision system processor?
-A smart camera might be chosen for its simplicity and self-contained operation, which can be beneficial for applications where a compact and integrated solution is preferred.
What are the capabilities of the new vision processor mentioned in the script?
-The new vision processor can support up to eight different cameras, allowing for more complex and multifaceted machine vision applications to be managed from a single processing unit.
How does a machine vision system with a processor display and monitor the inspection process?
-The system can display the inspection process on a floor module or through machine vision software, showing real-time monitoring, statistics, and historical image data for analysis.
What is OCR and how are machine vision cameras capable of performing it?
-OCR stands for Optical Character Recognition. Machine vision cameras capable of OCR can read and interpret text within images, which is useful for applications that require reading barcodes or other characters on objects.
Why would a barcode reader be preferred over a machine vision camera for reading barcodes?
-A barcode reader is typically preferred for just reading barcodes due to its simplicity and efficiency. Machine vision cameras are more versatile for applications where both object inspection and barcode reading are required simultaneously.
What additional insights can the provided script offer regarding machine vision applications?
-The script provides insights into the decision-making process for selecting camera types, the importance of accuracy and speed in inspections, the capabilities of smart cameras and vision processors, and the role of OCR in machine vision systems.
Outlines
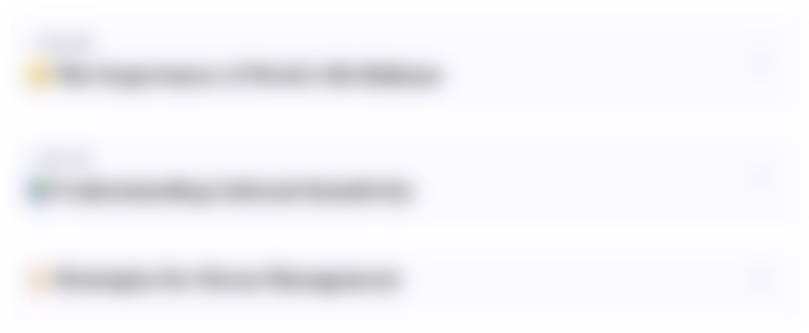
هذا القسم متوفر فقط للمشتركين. يرجى الترقية للوصول إلى هذه الميزة.
قم بالترقية الآنMindmap
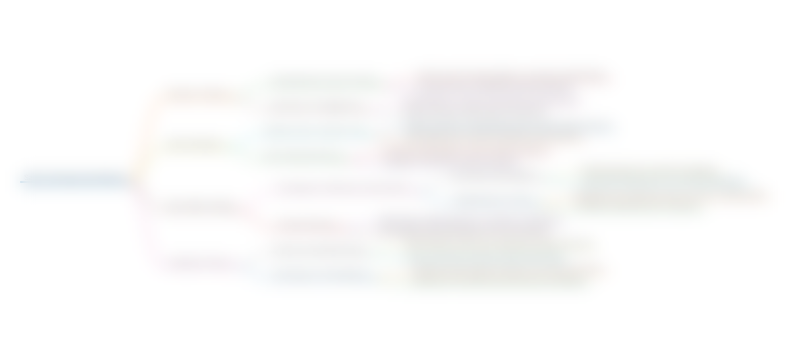
هذا القسم متوفر فقط للمشتركين. يرجى الترقية للوصول إلى هذه الميزة.
قم بالترقية الآنKeywords
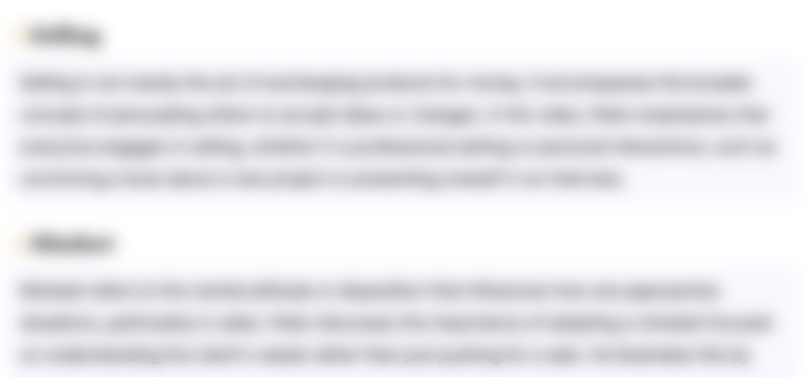
هذا القسم متوفر فقط للمشتركين. يرجى الترقية للوصول إلى هذه الميزة.
قم بالترقية الآنHighlights
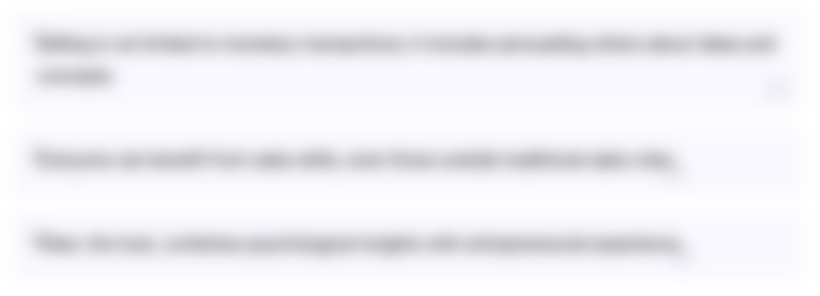
هذا القسم متوفر فقط للمشتركين. يرجى الترقية للوصول إلى هذه الميزة.
قم بالترقية الآنTranscripts
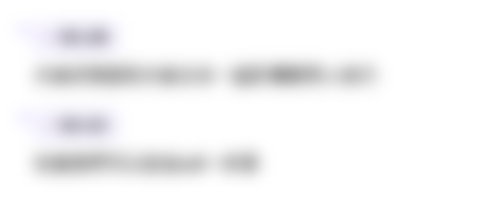
هذا القسم متوفر فقط للمشتركين. يرجى الترقية للوصول إلى هذه الميزة.
قم بالترقية الآنتصفح المزيد من مقاطع الفيديو ذات الصلة
5.0 / 5 (0 votes)