Sharpen Your Stanley Spokeshave Blade
Summary
TLDRIn this video, the host demonstrates how to sharpen a Stanley 151 spoke shave blade, a flat blade used for non-wooden spokes. Techniques include using a marker to flatten the blade, honing the bevel with a specific grip, and progressing through various grits of stones. The video also covers adjusting the blade on the Stanley 151 and using a homemade jig for sharpening with a Tormac.
Takeaways
- 🔪 The video is about sharpening a Stanley 151 spoke shave blade, which is a flat blade used for non-wooden spoke shaves.
- 📏 The first step is to flatten the back of the blade using a rough stone, such as a 300-grit stone, to remove all marks and achieve a shiny surface.
- ⏱️ Flattening the back can take up to 5 minutes or even half an hour if the blade is severely out of flatness.
- 📏 For the bevel part, the presenter uses a marker to mark the blade and then sharpens it using a specific grip, with the thumbnail acting as a guide.
- 👍 A proper grip is crucial to avoid over-tilting the blade while sharpening, ensuring a consistent bevel.
- 🔍 The presenter suggests using progressively finer grits, starting from 300 grit and moving up to 1000 grit, then to 6000 grit, to refine the bevel.
- 💧 A 15,000-grit ceramic stone is recommended for achieving a glassy smooth finish, which the presenter found to make a significant difference.
- 🛠️ The presenter demonstrates how to adjust the blade on a Stanley 151 using an adjustable wheel, ensuring the blade protrudes just enough for proper shaving.
- 🔍 Checking the sole of the plane for any hollow or unevenness is important for achieving a consistent shave, and the presenter shows how to flatten the sole using a marker and a rough stone.
- 🛠️ The video also covers how to sharpen the blade using a jig, specifically with a Tormac or similar tool, by creating a simple jig with a bar and a block of wood.
- 🎥 The presenter mentions that the next video will discuss different types of spoke shaves and will reveal their favorite type.
Q & A
What is the purpose of the video?
-The purpose of the video is to demonstrate how to sharpen a Stanley 151 spoke shave blade, which is a flat blade used for modern non-wooden spoke shaves.
What is a common issue with using jigs for sharpening the Stanley 151 blade?
-A common issue is that jigs are often designed for blades that protrude more, which may not accommodate the shorter blades of the Stanley 151.
What is the first step in sharpening the blade as shown in the video?
-The first step is to flatten out the back of the blade using a rough stone, such as a 300-grit stone.
Why is it important to flatten the blade before sharpening the bevel?
-Flattening the blade ensures that the entire length of the blade is even and ready for the bevel to be sharpened properly, preventing uneven sharpening.
What technique is used to determine the bevel angle when sharpening the blade?
-The video demonstrates using the thumbnail as a wedge to eyeball the bevel angle, ensuring that the blade is held at the correct angle against the sharpening stone.
Why is it recommended to not use the very end part of the blade when sharpening?
-The very end part of the blade is typically not used because it may be more difficult to sharpen evenly, and the rest of the blade is usually sufficient for the intended use.
What is the significance of using different grits of stones in the sharpening process?
-Using different grits of stones helps to progressively refine the sharpening process, starting with a rough grit to shape the bevel and finishing with a finer grit to polish and refine the edge.
What is the purpose of using a 15,000-grit stone or ceramic stone in the sharpening process?
-A 15,000-grit stone or ceramic stone is used to achieve a very fine and smooth edge, almost like glass, which can make a significant difference in the sharpness and performance of the blade.
How can the blade be adjusted on the Stanley 151 spoke shave?
-The blade can be adjusted by loosening the screw, positioning the blade so that it protrudes just enough, and then tightening the screw to secure it in place.
What is the purpose of the jig shown in the video for sharpening tools like the Torx or a miter trimmer?
-The jig is used to hold the tool at a consistent angle against the sharpening stone, ensuring a precise and even sharpening process without the need for expensive commercial jigs.
What additional tip is given for sharpening carving gouges using the same technique?
-The video suggests using the same sharpening technique and jig setup to sharpen carving gouges, using the handle of the tool as a reference for the bevel angle.
Outlines
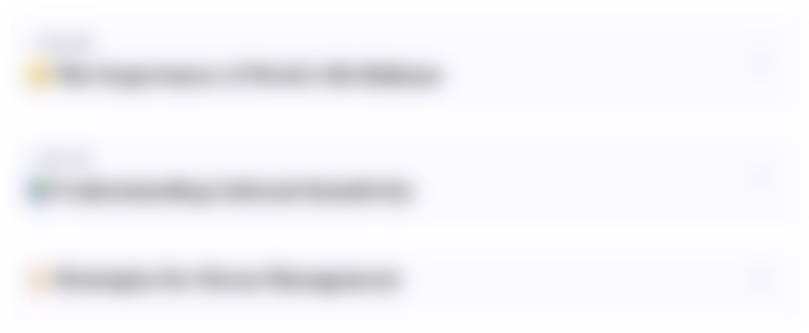
هذا القسم متوفر فقط للمشتركين. يرجى الترقية للوصول إلى هذه الميزة.
قم بالترقية الآنMindmap
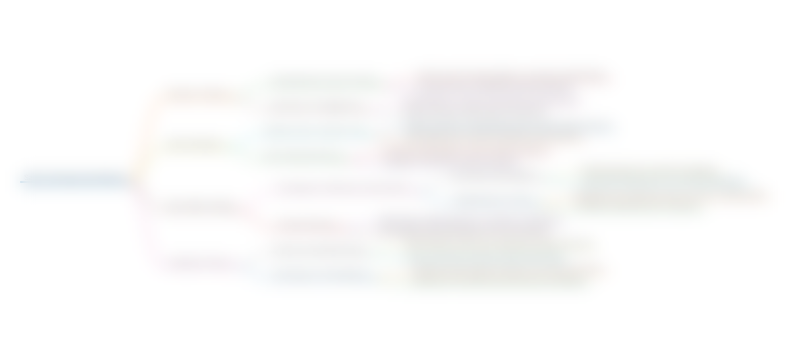
هذا القسم متوفر فقط للمشتركين. يرجى الترقية للوصول إلى هذه الميزة.
قم بالترقية الآنKeywords
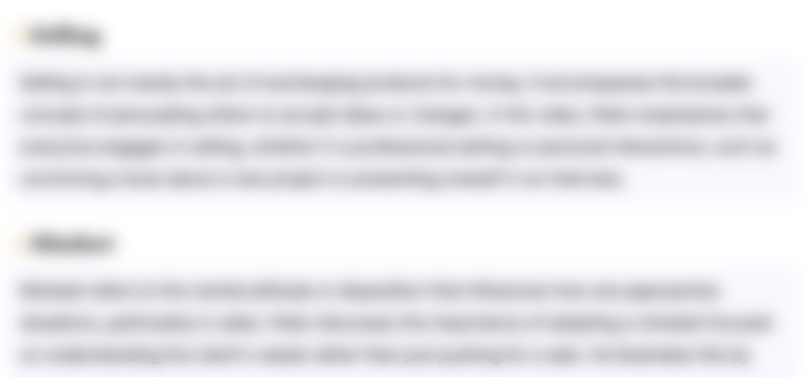
هذا القسم متوفر فقط للمشتركين. يرجى الترقية للوصول إلى هذه الميزة.
قم بالترقية الآنHighlights
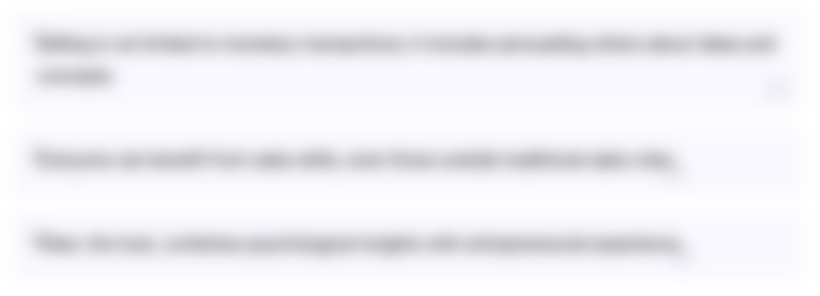
هذا القسم متوفر فقط للمشتركين. يرجى الترقية للوصول إلى هذه الميزة.
قم بالترقية الآنTranscripts
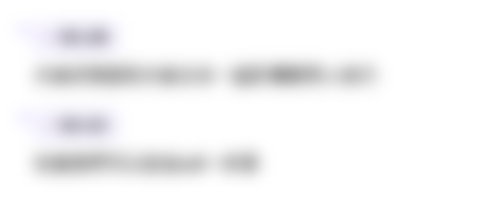
هذا القسم متوفر فقط للمشتركين. يرجى الترقية للوصول إلى هذه الميزة.
قم بالترقية الآن5.0 / 5 (0 votes)