Why Use Model Predictive Control? | Understanding MPC, Part 1
Summary
TLDRThis video introduces Model Predictive Control (MPC), a feedback control algorithm that predicts future system behavior using a model to optimize control actions. MPC excels in handling multi-input, multi-output systems, managing constraints, and providing preview capabilities to improve performance. It’s especially beneficial for systems with interactions between inputs and outputs, like autonomous cars, where constraints such as speed limits and safety are crucial. While MPC offers significant advantages, it requires powerful processors and large memory due to its complex optimization tasks. The video also sets the stage for a deeper dive into MPC's inner workings in the next episode.
Takeaways
- 😀 MPC stands for Model Predictive Control, a popular control method used by engineers.
- 😀 MPC predicts future outputs of a system using a model and selects the optimal control action.
- 😀 An analogy for MPC: driving a car and predicting your future trajectory based on control actions.
- 😀 MPC works with multi-input multi-output (MIMO) systems and accounts for interactions between variables.
- 😀 Traditional PID controllers may struggle with MIMO systems due to their independent control loops.
- 😀 One of MPC's advantages is its ability to handle constraints, such as safety limits or physical constraints.
- 😀 MPC can ensure that constraints like speed limits and safe distances are respected in systems such as autonomous cars.
- 😀 MPC has preview capability, which allows it to incorporate future information to improve performance, like anticipating a corner while driving.
- 😀 The use of MPC has expanded from the process industry to other sectors, thanks to advancements in computing power.
- 😀 A key drawback of MPC is that it requires powerful processors with large memory to solve optimization problems in real-time.
- 😀 In summary, MPC uses system models to predict behavior, solve optimization problems, and control multi-variable systems while respecting constraints.
Q & A
What does MPC stand for?
-MPC stands for Model Predictive Control, which is a feedback control algorithm that uses a model to predict future outputs of a process.
Why is MPC considered useful in control systems?
-MPC is useful because it can handle multi-input multi-output (MIMO) systems, manage interactions between system variables, and handle constraints such as safety or physical limits.
What is the main function of a Model Predictive Controller?
-The main function of an MPC is to predict the future behavior of a system using a model and to select the optimal control action to bring the system's output as close as possible to the desired reference.
How does the analogy of driving help explain MPC?
-In the driving analogy, you use a model of your car's behavior (such as speed and turning) to predict your future trajectory and select the optimal action to keep the car in the lane. This mirrors how MPC works by predicting future outputs and selecting optimal control actions.
What challenges arise when using PID controllers for MIMO systems?
-PID controllers would struggle with MIMO systems because they treat each control loop independently without considering the interactions between multiple inputs and outputs. This would make designing and tuning PID controllers more complex and less effective in such systems.
What are some of the advantages of MPC over PID controllers?
-MPC has several advantages over PID controllers, including the ability to handle multi-input multi-output systems, manage system interactions, handle constraints, and incorporate future reference information into control actions.
How does MPC handle constraints in a system?
-MPC can handle constraints by incorporating them directly into the control process, ensuring that the control actions remain within acceptable bounds, such as safety limits or physical limitations of the system.
Can you explain the preview capability of MPC?
-The preview capability of MPC is similar to feedforward control. It allows the controller to anticipate future events, such as a sharp curve in the road, and take proactive actions (like braking early) to improve performance and safety.
What role does the model of the system play in MPC?
-The model of the system is used by MPC to predict future outputs. This prediction is then used to calculate the optimal control actions that drive the system toward the desired reference while respecting any constraints.
What is the main challenge when implementing MPC?
-The main challenge of implementing MPC is that it requires a powerful and fast processor with large memory, as it solves an online optimization problem at each time step.
Outlines
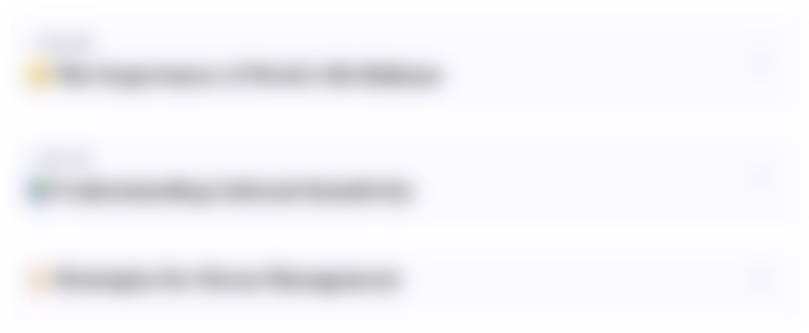
هذا القسم متوفر فقط للمشتركين. يرجى الترقية للوصول إلى هذه الميزة.
قم بالترقية الآنMindmap
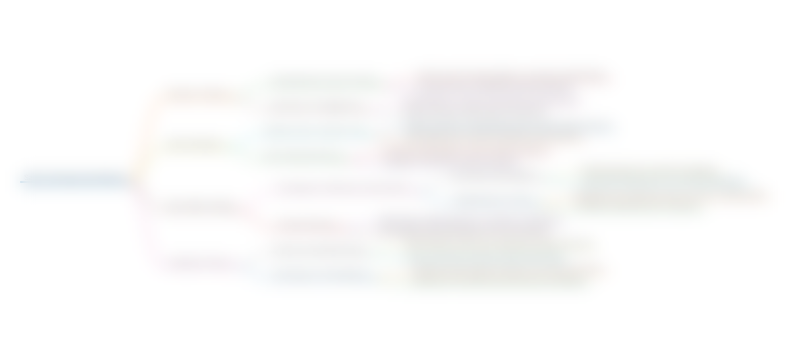
هذا القسم متوفر فقط للمشتركين. يرجى الترقية للوصول إلى هذه الميزة.
قم بالترقية الآنKeywords
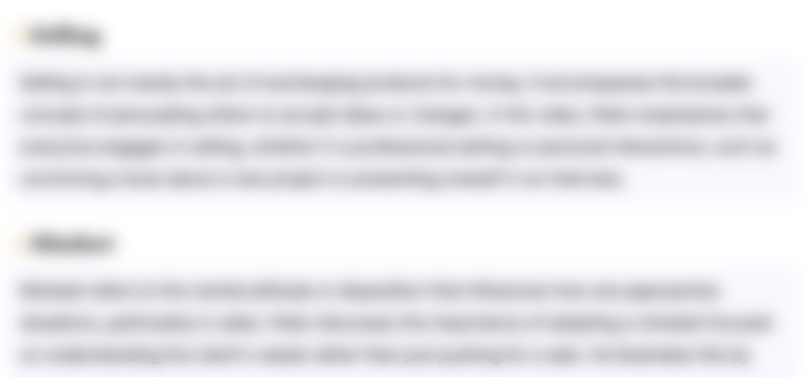
هذا القسم متوفر فقط للمشتركين. يرجى الترقية للوصول إلى هذه الميزة.
قم بالترقية الآنHighlights
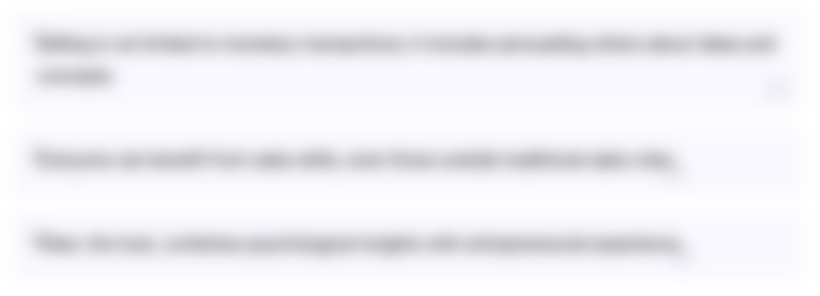
هذا القسم متوفر فقط للمشتركين. يرجى الترقية للوصول إلى هذه الميزة.
قم بالترقية الآنTranscripts
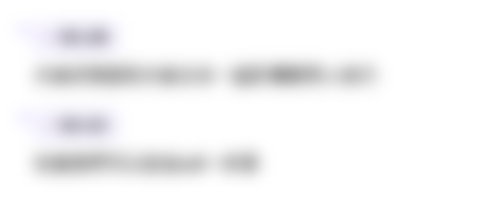
هذا القسم متوفر فقط للمشتركين. يرجى الترقية للوصول إلى هذه الميزة.
قم بالترقية الآنتصفح المزيد من مقاطع الفيديو ذات الصلة
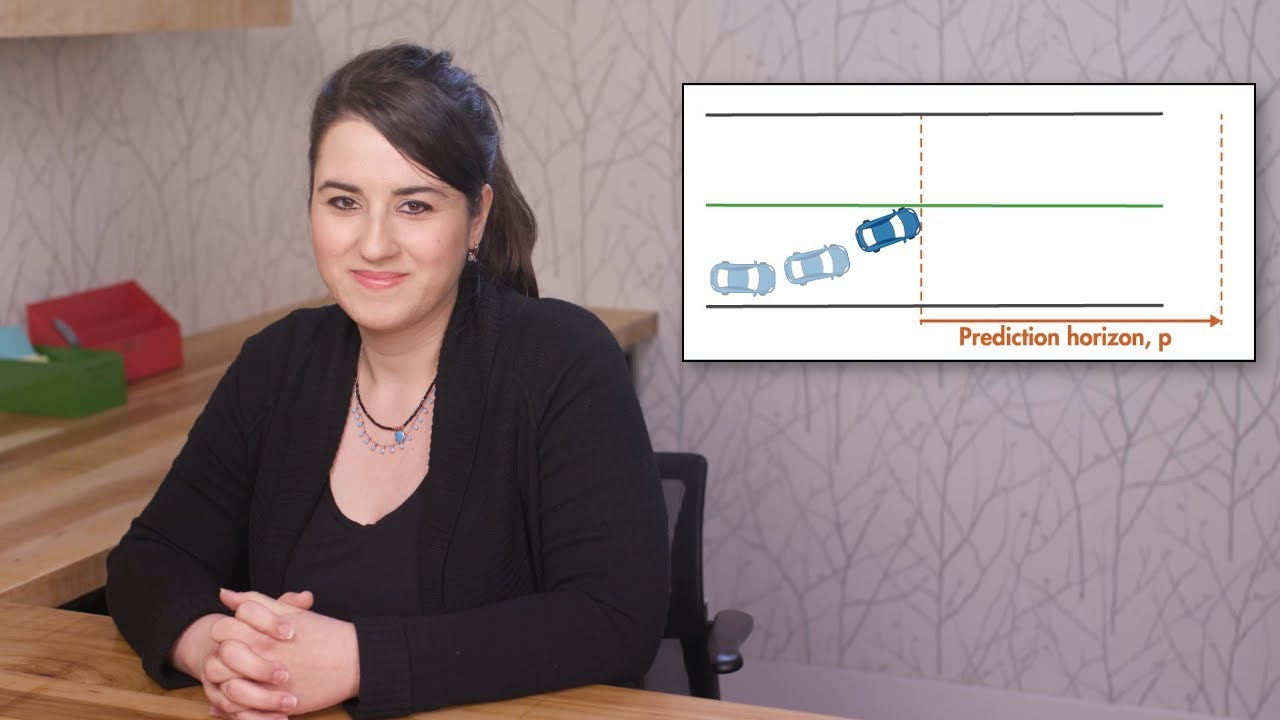
What is Model Predictive Control? | Understanding MPC, Part 2
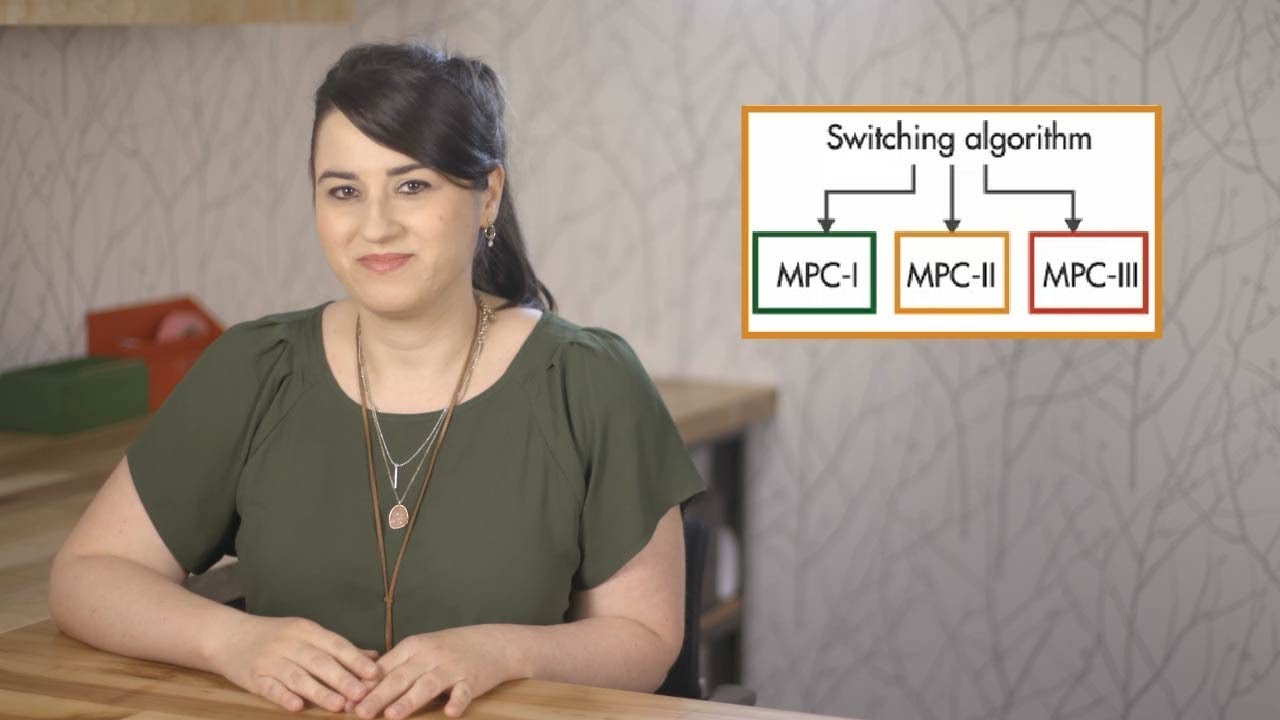
Adaptive, Gain-Scheduled and Nonlinear Model Predictive Control | Understanding MPC, Part 4

How To Run Model Predictive Control Faster | Understanding MPC, Part 5
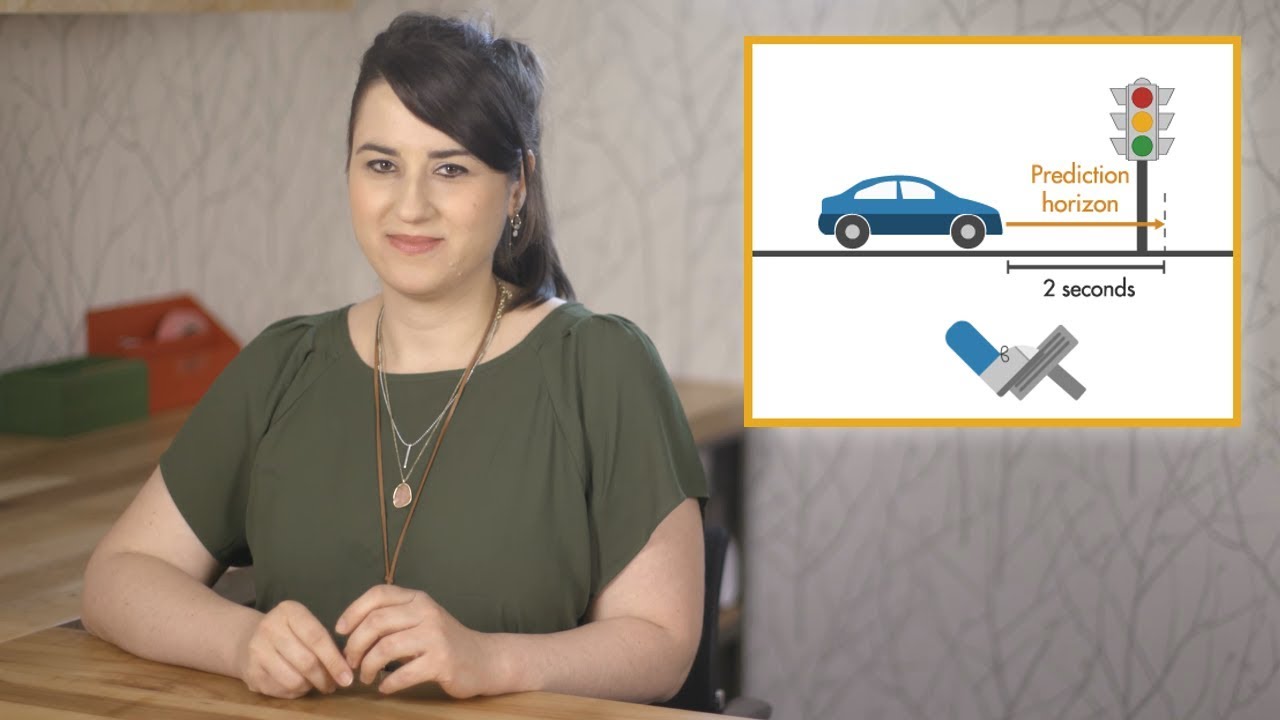
Model Predictive Control Design Parameters | Understanding MPC, Part 3
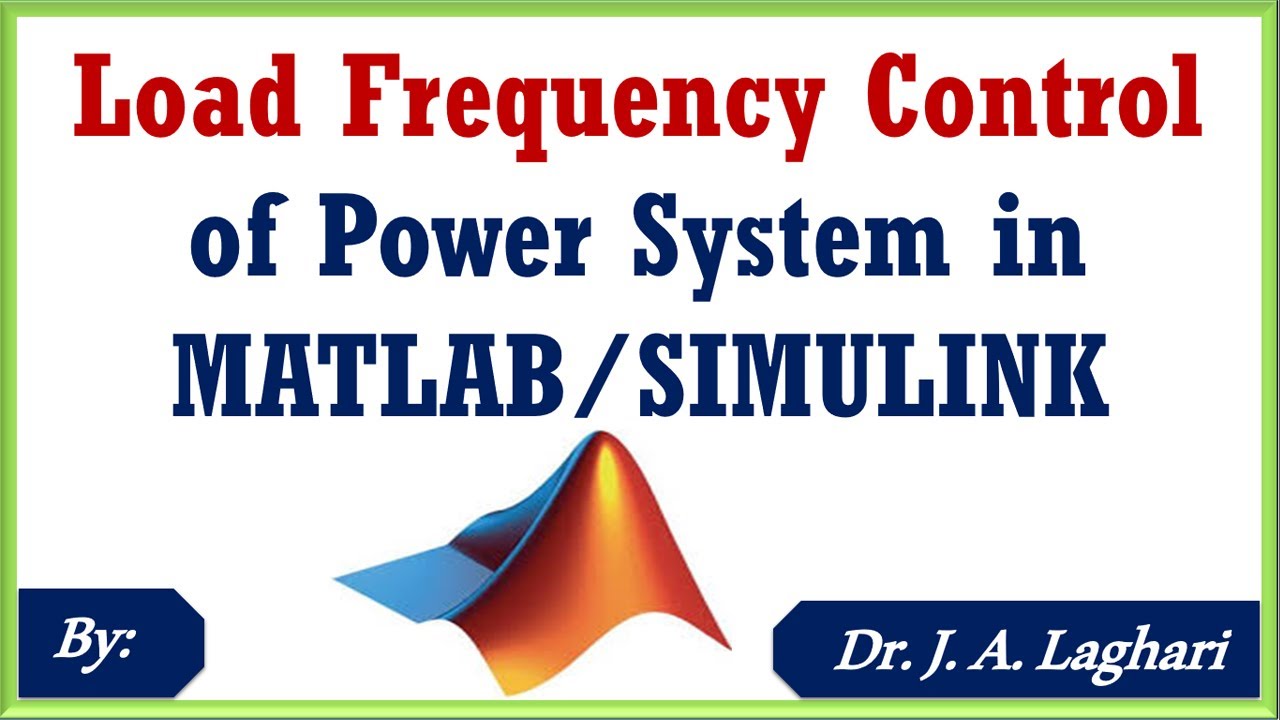
How to Design Load Frequency Control using Simulink ? | Dr. J. A. Laghari
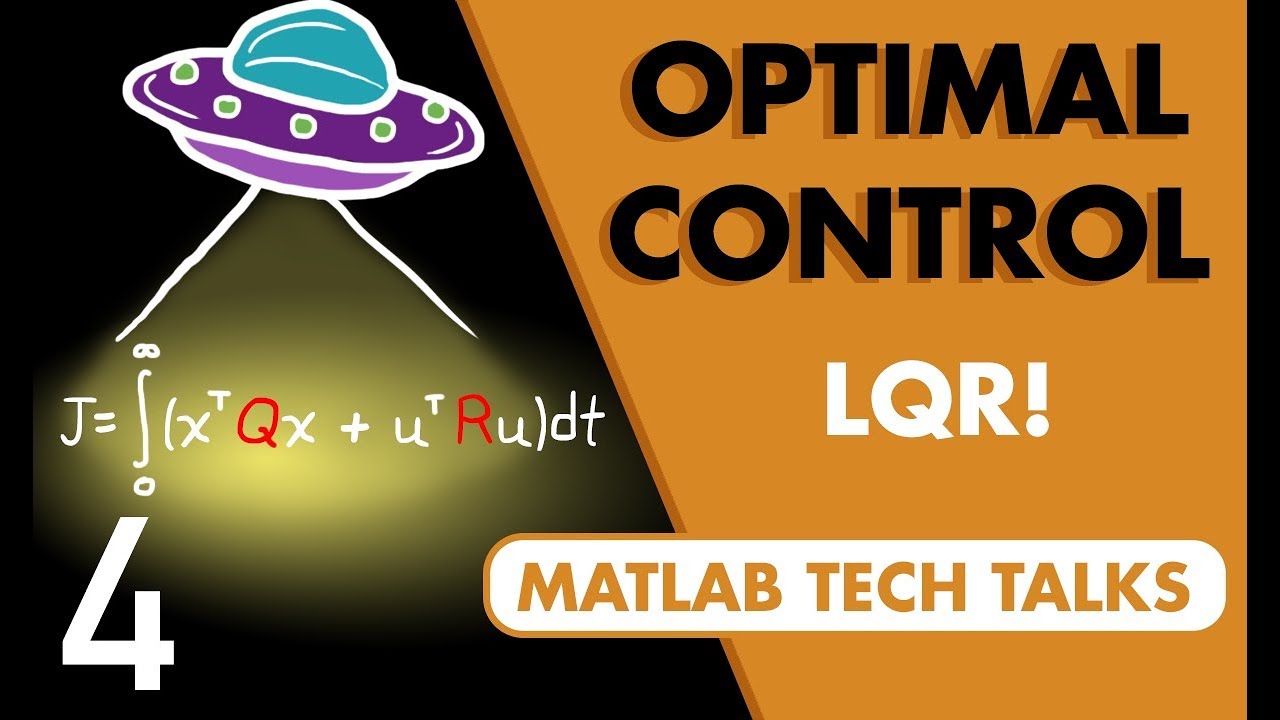
What Is Linear Quadratic Regulator (LQR) Optimal Control? | State Space, Part 4
5.0 / 5 (0 votes)