Lost Wax and Lost Resin Casting Burnout Process | How to get good casting results| Casting 3D Prints
Summary
TLDRThis video dives into the intricate burnout process in investment casting, emphasizing key steps like pre-burnout setup, temperature control, and avoiding common mistakes such as thermal shock. The host stresses the importance of using the right equipment, such as a reliable kiln and proper ventilation, for successful casting. Viewers are guided through the critical stages of burnout, including the gradual ramp-up in temperature and cooling procedures before pouring the metal. The video also highlights the importance of adjusting burnout times and temperatures based on the size of the flask and the type of investment being used for both wax and resin models.
Takeaways
- 😀 Proper investment is crucial for casting, ensuring accurate powder-to-water measurements and thorough mixing.
- 🔥 The burnout process is essential in creating an empty cavity for metal to fill, but it's more challenging with lost resin compared to wax.
- ⏱️ The burnout cycle is sensitive to temperature changes, so following the correct ramp-up and hold times is crucial to avoid issues like cracking or uneven casting.
- 🔬 The burnout process should be done in a reliable kiln, and not in makeshift setups like a home oven or gas forge, as this can lead to poor results.
- ⚖️ For best results, adhere to manufacturer guidelines for kiln temperature and timing to prevent issues such as thermal shock or improper burnout.
- 🔧 Always check that your kiln’s temperature is accurate, as faulty temperature readings can lead to failed burnout and casting.
- 💡 For lost resin, increasing the burnout duration can often yield better results than just raising the maximum temperature.
- 🌡️ When pouring metal into the mold, ensure the temperature of the flask is 1000°F below the metal's melting point for proper fluidity and detail.
- 🧯 Ventilation during the burnout process is important, especially in urban environments, to manage fumes and avoid disturbing neighbors.
- 🛠️ Reliable, compact equipment is key to efficient casting, so consider optimizing your setup to minimize time between the burnout and metal pouring steps.
- 👕 New merch and community support are available, with opportunities to engage and ask questions on the casting process through various channels.
Q & A
What is the burnout process in investment casting?
-The burnout process is the phase where the model, which has been properly invested, is burned away to create an empty cavity for the metal to fill. This is crucial for forming the final casting.
Why is the burnout process more challenging with resin compared to wax?
-Resin is more difficult to burn out than wax because it transitions from a solid to a gas without a liquid phase in between, whereas wax melts at a lower temperature and evacuates more easily.
How does the burnout process differ between wax and resin models?
-In the lost wax process, the wax model melts and evaporates at lower temperatures, making the burnout straightforward. However, resin requires higher temperatures due to its transition to gas, and the process can be trickier.
What is the ideal temperature ramp for a kiln during the burnout phase?
-The kiln should be preheated to 300°F and gradually raised to 1,350°F in specific stages. For example, the temperature should rise from 300°F to 700°F in 1-2 hours, and then from 700°F to 1,350°F in 2-3 hours.
Why is it important to follow manufacturer guidelines during the burnout process?
-Following the manufacturer guidelines is essential to avoid issues like thermal shock, cracking in the investment, or other casting defects. Ignoring these guidelines could lead to poorly executed casts.
What can happen if the kiln temperature is too high or too low during burnout?
-If the kiln is too hot, it can cause cracking or fins in the cast. If the temperature is too low, the model may not burn out properly, affecting the final casting quality.
How does the size of the flask affect the burnout process?
-The size of the flask directly impacts the burnout time. Larger flasks require more time in the kiln, while smaller flasks may need less time for the burnout phase.
What is the role of air flow in the burnout process?
-Airflow is critical in ensuring a good burn during the burnout process. Without sufficient airflow, the material inside the flask won't burn out properly, leading to a failed casting.
What is the recommended temperature to pour the metal during casting?
-The recommended temperature for pouring the metal is around 1,000°F below its melting point. For example, if casting silicon bronze, which melts at about 2,100°F, you would pour it at around 1,100°F.
What are some factors to consider when cooling the flask after pouring the metal?
-After pouring, the flask should be allowed to cool for about 10 minutes or until the button (the metal reservoir) solidifies. Quenching the flask in water can help remove the investment material more easily, but it's important to avoid letting the flask cool too much before quenching.
Outlines
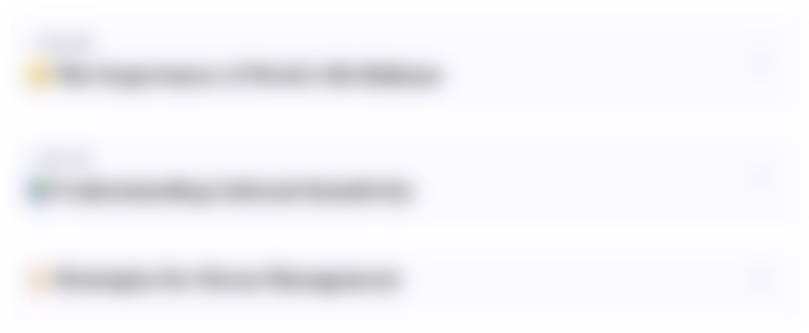
هذا القسم متوفر فقط للمشتركين. يرجى الترقية للوصول إلى هذه الميزة.
قم بالترقية الآنMindmap
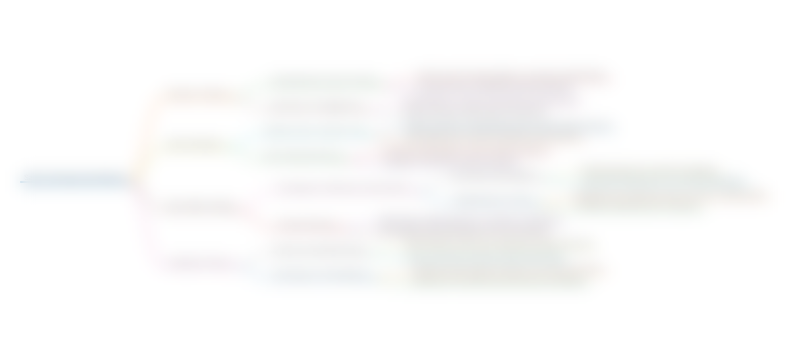
هذا القسم متوفر فقط للمشتركين. يرجى الترقية للوصول إلى هذه الميزة.
قم بالترقية الآنKeywords
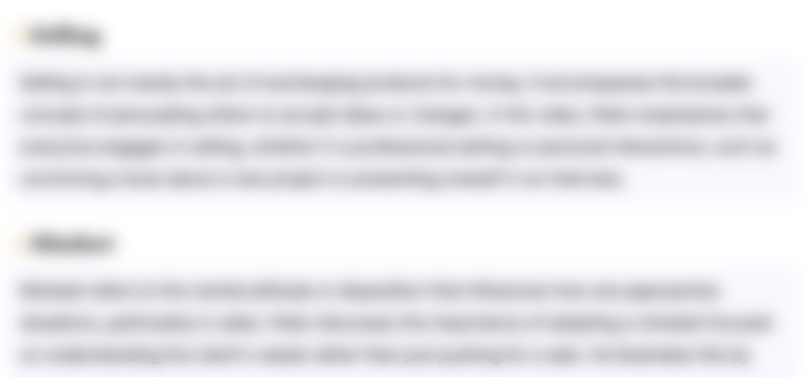
هذا القسم متوفر فقط للمشتركين. يرجى الترقية للوصول إلى هذه الميزة.
قم بالترقية الآنHighlights
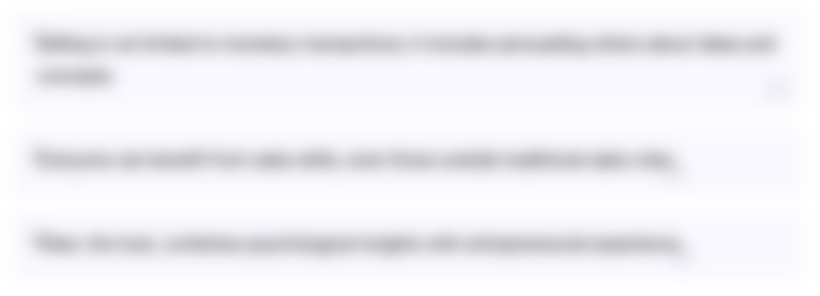
هذا القسم متوفر فقط للمشتركين. يرجى الترقية للوصول إلى هذه الميزة.
قم بالترقية الآنTranscripts
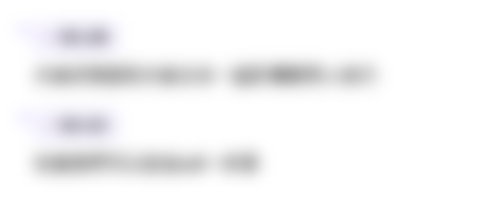
هذا القسم متوفر فقط للمشتركين. يرجى الترقية للوصول إلى هذه الميزة.
قم بالترقية الآنتصفح المزيد من مقاطع الفيديو ذات الصلة

Casting Defects | Dental Materials | Super Simple
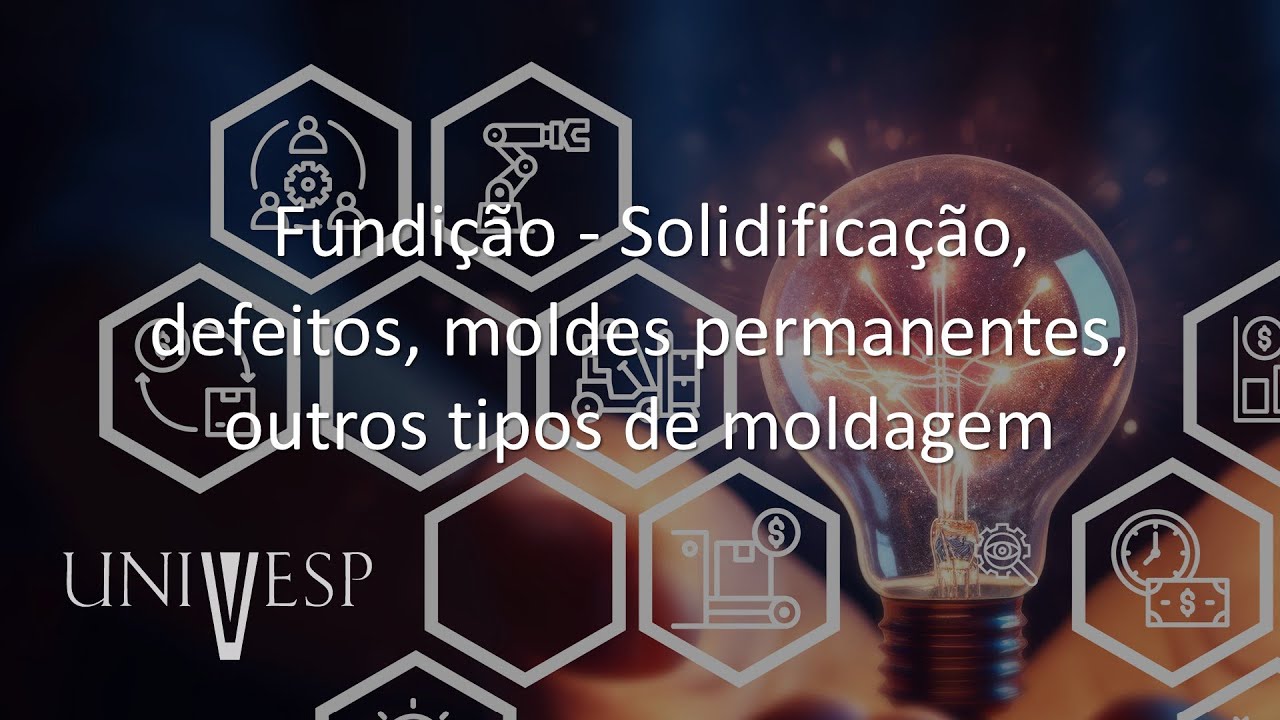
Materiais e Processos de Fabricação para Engenharia de Produção - Fundição - Solidificação, defeitos

Proses Pengecoran

Pekerjaan Struktur Beton Bertulang // Quality Control Pekejaan Beton part1

3 signs that you’ve hit clinical burnout and should seek help | Laurie Santos
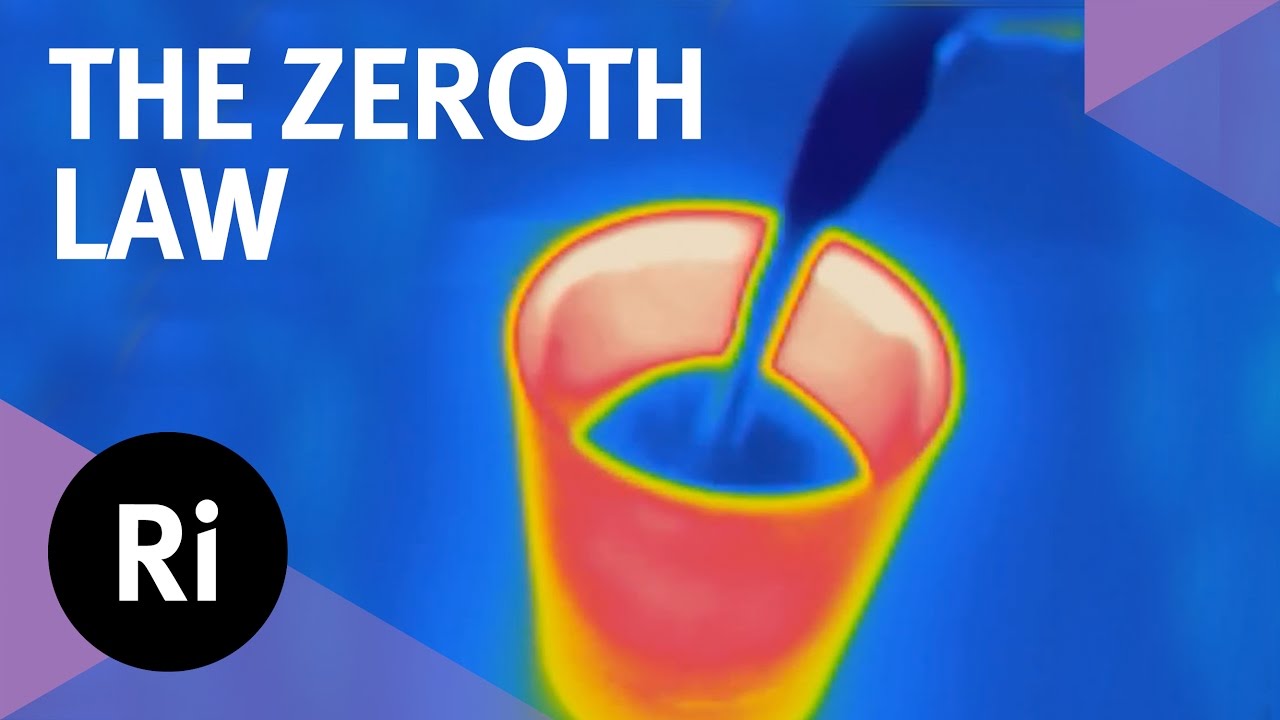
What is the Zeroth Law of Thermodynamics?
5.0 / 5 (0 votes)