Process Improvement: Six Sigma & Kaizen Methodologies
Summary
TLDRIn this video, Devin Deen from ProjectManager.com compares two well-established process improvement methodologies: Kaizen and Six Sigma. Kaizen, originating post-WWII in Japan, focuses on continuous, company-wide cultural change through small, incremental improvements. In contrast, Six Sigma, developed by Motorola in the 1980s, uses a statistical, project-based approach to eliminate defects, aiming for 3.4 defects per million products. While Kaizen fosters holistic collaboration and gradual progress, Six Sigma is centered on precise, data-driven solutions to improve quality and efficiency. Both methodologies offer unique approaches for businesses seeking to enhance their processes and products.
Takeaways
- 😀 Kaizen and Six Sigma are two well-established process improvement methodologies that focus on improving efficiency and quality within organizations.
- 😀 Kaizen emphasizes continuous, small improvements across all levels of an organization, fostering a culture of involvement from everyone, from the CEO to the janitorial staff.
- 😀 Six Sigma is a data-driven, statistical methodology designed to reduce defects to 3.4 per million products, often applied on a project-by-project basis.
- 😀 Kaizen originated in post-World War II Japan, influenced by American consultants helping Japan rebuild its industrial base.
- 😀 Six Sigma was developed in the 1980s by Motorola to address quality control issues and improve profitability through rigorous statistical analysis.
- 😀 Kaizen uses the PDAC cycle (Plan, Do, Analyze, Change), a repeatable process for incremental improvement, which is applied iteratively over time.
- 😀 Six Sigma utilizes two primary processes: DMAIC (Define, Measure, Analyze, Improve, Control) for process improvement and DMADV (Define, Measure, Analyze, Design, Verify) for new process design.
- 😀 Kaizen is a cultural approach, focusing on a company-wide commitment to improvement, making it effective for long-term, gradual change.
- 😀 Six Sigma is a more structured, project-specific approach, with defined roles such as Black Belts (leaders) and Green Belts (supporters) responsible for driving improvements.
- 😀 Toyota's implementation of Kaizen is often cited as a model for how this methodology can be successfully adopted across industries, not just in manufacturing.
- 😀 Both Kaizen and Six Sigma offer valuable tools for organizations seeking to enhance efficiency and product quality, but they cater to different organizational needs and structures.
Q & A
What is the main focus of the Kaizen methodology?
-Kaizen focuses on continuous, incremental improvements across all levels of an organization, empowering every employee from the CEO to janitorial staff to contribute to process optimization.
How does Six Sigma differ from Kaizen in terms of approach?
-Six Sigma is more structured and project-based, focusing on statistical process improvement to reduce defects. In contrast, Kaizen is a cultural approach to continuous improvement, with a focus on small, ongoing changes.
What are the main principles of the Six Sigma methodology?
-Six Sigma focuses on defining, measuring, analyzing, improving, and controlling processes to eliminate defects, typically using tools like DMAIC (Define, Measure, Analyze, Improve, Control) or DMADV (Define, Measure, Analyze, Design, Verify).
What was the historical context in which Kaizen emerged?
-Kaizen originated in post-World War II Japan when American business consultants helped rebuild Japan's economy. It became popular as part of broader efforts like Total Quality Management (TQM) to improve manufacturing processes.
How did Six Sigma start, and what motivated its development?
-Six Sigma emerged in the mid-1980s, with its roots in the 1970s at Motorola. The company faced declining product quality and profitability, prompting a focus on quality control and process improvement, eventually formalizing Six Sigma in 1986.
What are the key roles within a Six Sigma initiative?
-In Six Sigma, key roles include Black Belts, who lead projects and drive improvements, and Green Belts, who support these initiatives at the operational level. Other color belts represent varying levels of expertise and involvement in Six Sigma projects.
How does Kaizen empower its workforce?
-Kaizen empowers the workforce by involving everyone in the improvement process. It emphasizes the idea that every employee, regardless of their role, contributes to making small but meaningful improvements in the organization.
What is the PDAC cycle, and how is it used in Kaizen?
-The PDAC cycle stands for Plan, Do, Analyze, and Change. It is an iterative process used in Kaizen to make small, continuous improvements by planning, executing, analyzing the results, and making necessary changes before repeating the cycle.
What is the significance of the Six Sigma goal of 3.4 defects per million products?
-The Six Sigma goal of 3.4 defects per million products reflects a highly rigorous standard for quality control. Achieving this level of precision and minimal defects is the ultimate objective for processes within a Six Sigma framework.
What type of industries can benefit from Kaizen, according to the video?
-Kaizen is not limited to manufacturing. It can be applied across various industries, including finance (as shown with a bank using Kaizen for process improvement), as its principles focus on improving efficiency and quality in any organizational setting.
Outlines
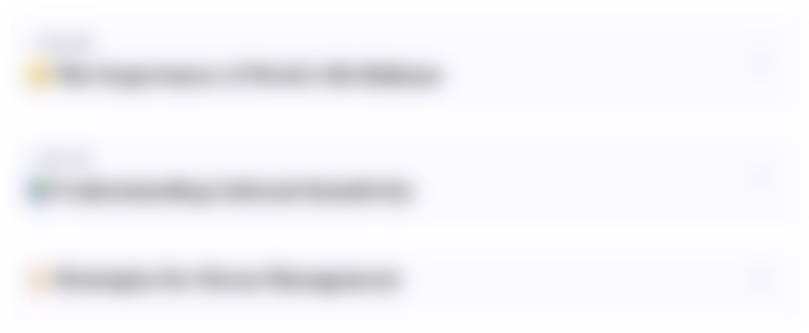
هذا القسم متوفر فقط للمشتركين. يرجى الترقية للوصول إلى هذه الميزة.
قم بالترقية الآنMindmap
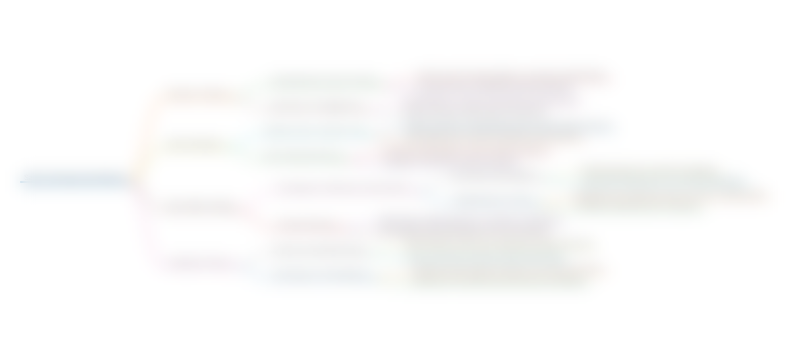
هذا القسم متوفر فقط للمشتركين. يرجى الترقية للوصول إلى هذه الميزة.
قم بالترقية الآنKeywords
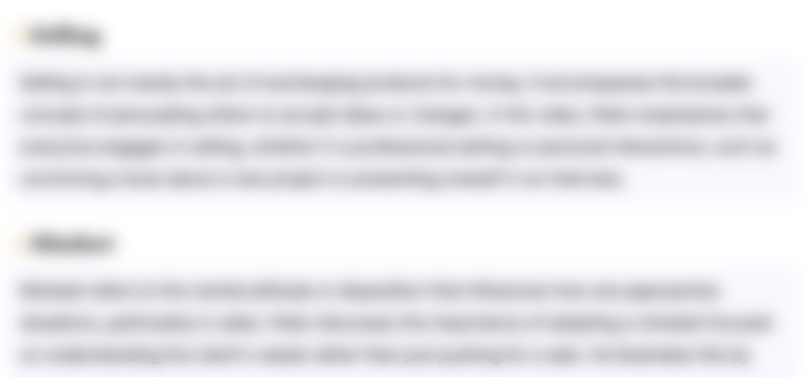
هذا القسم متوفر فقط للمشتركين. يرجى الترقية للوصول إلى هذه الميزة.
قم بالترقية الآنHighlights
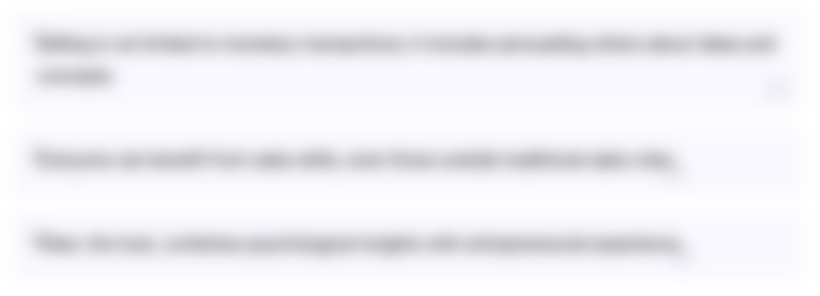
هذا القسم متوفر فقط للمشتركين. يرجى الترقية للوصول إلى هذه الميزة.
قم بالترقية الآنTranscripts
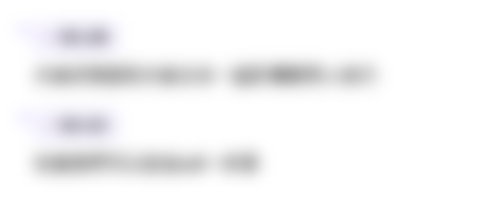
هذا القسم متوفر فقط للمشتركين. يرجى الترقية للوصول إلى هذه الميزة.
قم بالترقية الآنتصفح المزيد من مقاطع الفيديو ذات الصلة
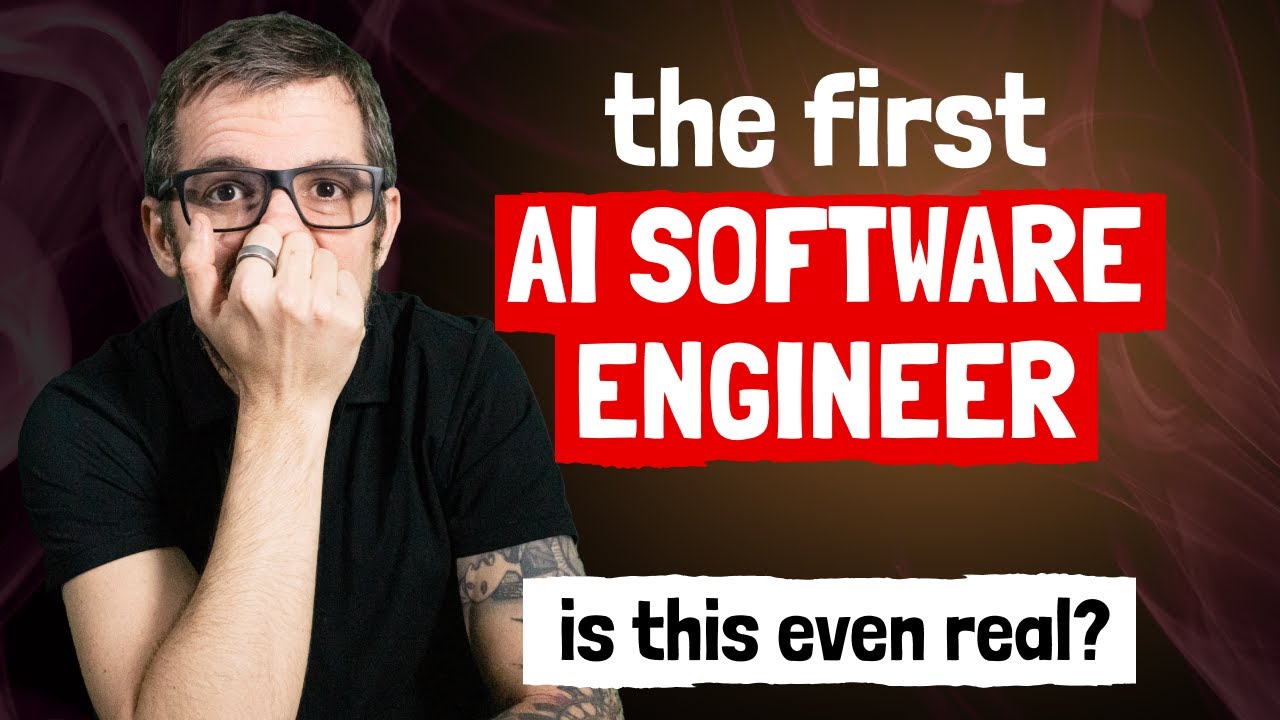
I used the first AI Software Engineer for a week. This is happening.
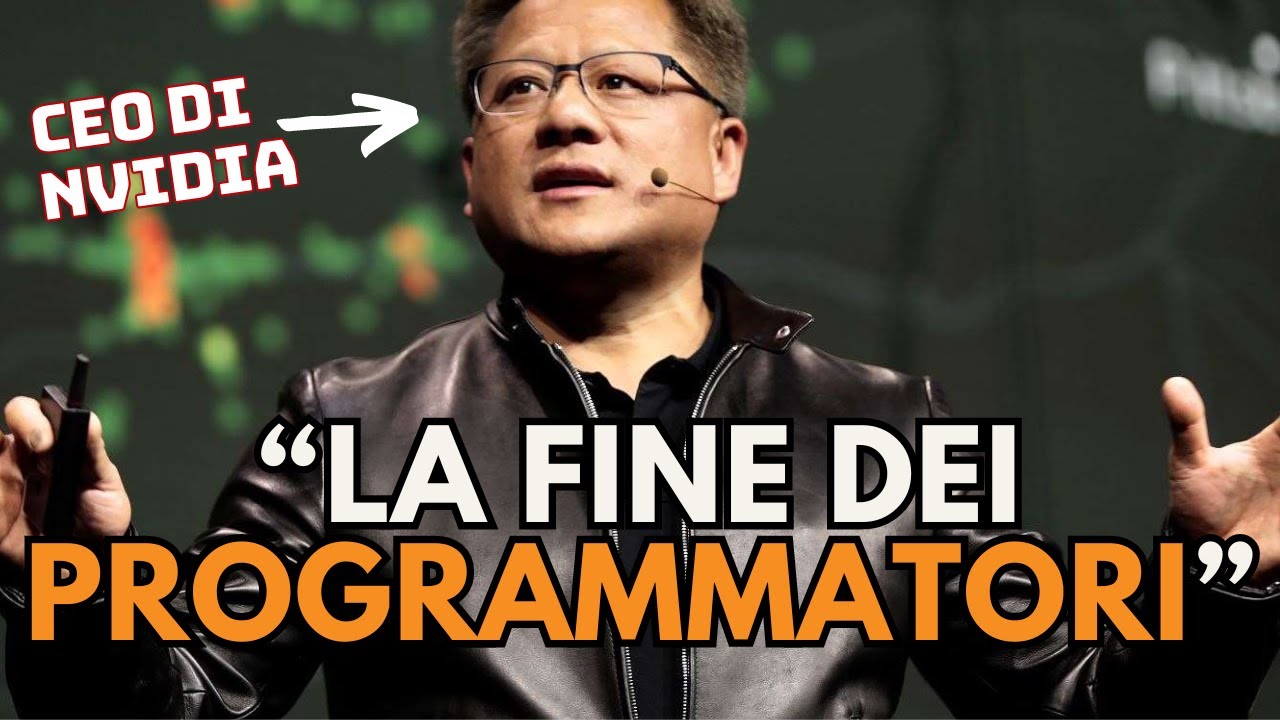
Devin: l'AI che sostituirà i programmatori [Reaction]
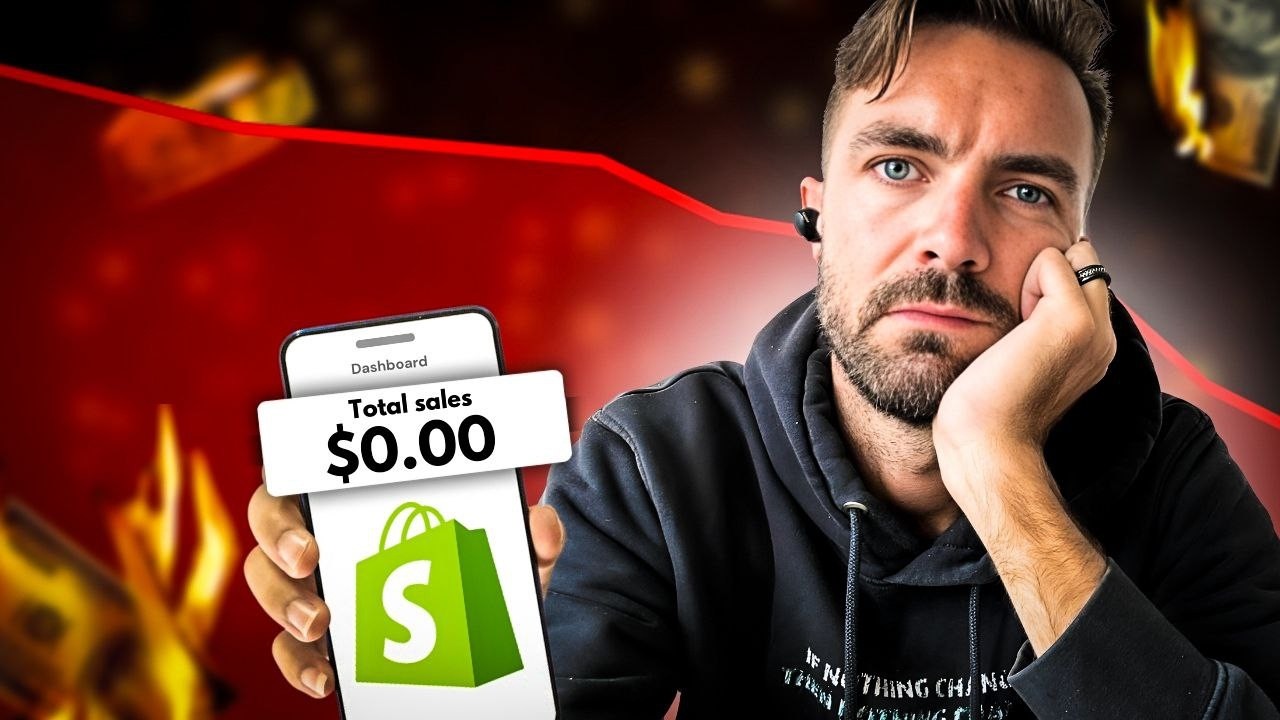
You'll NEVER Make Sales On Shopify (Unless You Fix This)

Devin Was a Lie! - The Big Expose (AI Scam) 😡

How to use Retinol like a Dermatologist | Dr Davin Lim
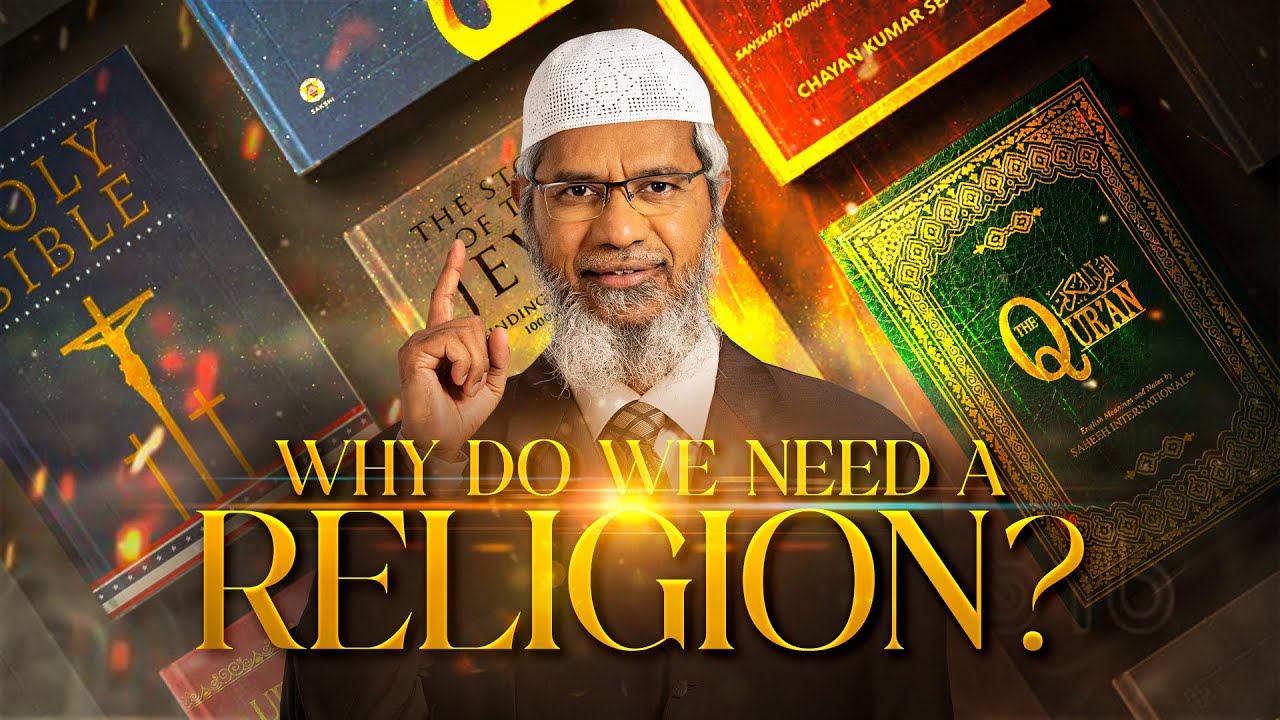
Why do we need a Religion? - Dr Zakir Naik
5.0 / 5 (0 votes)