What is Lean manufacturing? 5 functions of Lean Manufacturing | Lean Production
Summary
TLDRThis video introduces lean manufacturing, a production philosophy that maximizes productivity while minimizing waste. It covers the five principles: value, value stream mapping, flow, pull, and perfection. The script also discusses the eight wastes to eliminate, the benefits like time and cost savings, and potential drawbacks such as employee safety and hindering future development. Well-known lean manufacturers include Toyota, Intel, John Deere, and Nike.
Takeaways
- 🔧 Lean manufacturing is a production process that maximizes productivity while minimizing waste.
- 🚀 The ultimate goal of lean manufacturing is to sustainably deliver value to the customer.
- 🏢 Companies like Toyota, Intel, John Deere, and Nike use lean principles to optimize their operations.
- 📚 The book 'Lean Thinking' outlines five key principles: value, value stream, flow, pull, and perfection.
- 💰 Value in lean manufacturing is determined from the customer's perspective and waste is eliminated to meet optimal pricing.
- 🌐 Value stream mapping analyzes the entire lifecycle of a product to identify and eliminate waste.
- 🔄 Creating flow in lean manufacturing involves eliminating functional barriers to ensure smooth process execution.
- 📈 A pull system in lean manufacturing reacts to demand, reducing inventory costs and improving customer satisfaction.
- 🛠️ Perfection in lean is achieved through continuous improvement, known as kaizen.
- 🚨 The eight wastes of lean include defects, overproduction, waiting, non-utilized talent, transportation, inventory, motion, and excess processing.
- ⏱️ Lean manufacturing saves time and money by streamlining workflows and resource allocation.
- 🌿 It is environmentally friendly by reducing unnecessary processes and energy use.
- 🎖️ Improved customer satisfaction is achieved by delivering products or services efficiently and at the right cost.
- 🚨 Employee safety can be compromised by the relentless focus on waste reduction and streamlining.
- 🚧 Overemphasis on cutting waste might hinder future development and innovation.
Q & A
What is lean manufacturing?
-Lean manufacturing is a production process that aims to maximize productivity while minimizing waste within a manufacturing operation. It focuses on delivering value to the customer by eliminating waste and optimizing processes.
What are the five principles of lean manufacturing?
-The five principles of lean manufacturing are: 1) Value - identifying what the customer is willing to pay for, 2) Map the Value Stream - analyzing materials and resources to identify waste, 3) Create Flow - eliminating functional barriers to ensure smooth processes, 4) Establish a Pull System - producing only when there is demand, and 5) Perfection - continually striving for process improvements.
What is the significance of the acronym 'DOWNTIME' in lean manufacturing?
-The acronym 'DOWNTIME' stands for the eight wastes of lean manufacturing: Defects, Overproduction, Waiting, Non-utilized Talent, Transportation, Inventory, Motion, and Excess Processing. It is a mnemonic to help remember and identify these wastes.
Which well-known companies use lean manufacturing principles?
-Well-known companies that use lean manufacturing principles include Toyota, Intel, John Deere, and Nike.
How does lean manufacturing save time and money?
-Lean manufacturing saves time and money by creating more efficient workflows, better resource allocation, and streamlined production processes. This leads to reduced lead times and a more effective workforce.
How does lean manufacturing improve customer satisfaction?
-Lean manufacturing improves customer satisfaction by delivering products or services at the right cost and at the right time, which is essential for business success as it encourages repeat business and referrals.
What are the potential disadvantages of lean manufacturing?
-Potential disadvantages of lean manufacturing include overlooking employee safety due to the focus on streamlining processes and the risk of halting future development by over focusing on cutting waste in the present.
What is the difference between a push system and a pull system in lean manufacturing?
-A push system produces inventory based on forecasts, which can lead to overproduction or underproduction. A pull system, on the other hand, only starts new work when there is demand, relying on flexibility and communication to meet customer needs.
What is the role of 'kaizen' in lean manufacturing?
-Kaizen, which means continuous improvement, is a core concept in lean manufacturing. It involves targeting the root causes of quality issues and eliminating waste across the value stream to achieve perfection.
How does lean manufacturing contribute to environmental friendliness?
-Lean manufacturing contributes to environmental friendliness by removing unnecessary processes, which saves energy and fuel use. It also encourages the use of more energy-efficient equipment, which can offer both environmental and cost benefits.
What is the importance of mapping the value stream in lean manufacturing?
-Mapping the value stream is important in lean manufacturing as it helps to analyze the entire lifecycle of a product from raw materials to disposal. This analysis identifies waste and areas for improvement, ensuring that only value-adding steps are included in the process.
Outlines
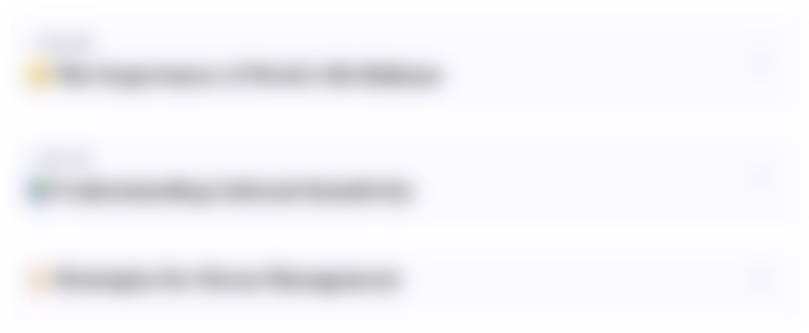
هذا القسم متوفر فقط للمشتركين. يرجى الترقية للوصول إلى هذه الميزة.
قم بالترقية الآنMindmap
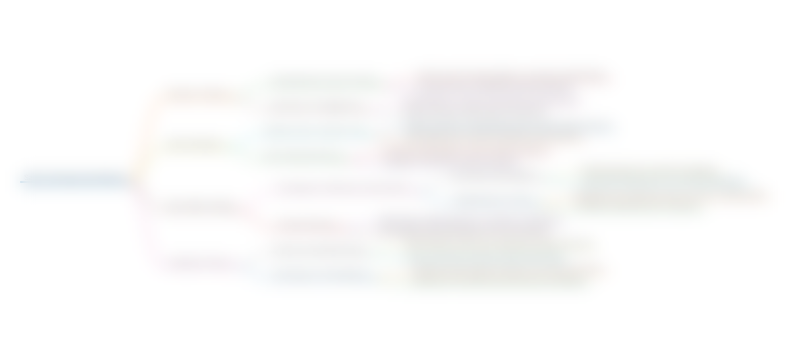
هذا القسم متوفر فقط للمشتركين. يرجى الترقية للوصول إلى هذه الميزة.
قم بالترقية الآنKeywords
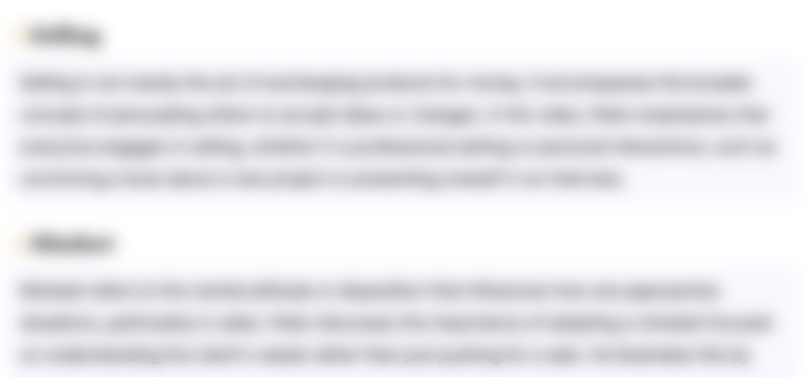
هذا القسم متوفر فقط للمشتركين. يرجى الترقية للوصول إلى هذه الميزة.
قم بالترقية الآنHighlights
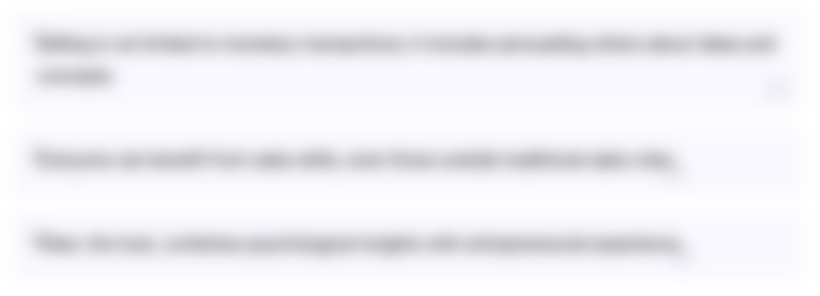
هذا القسم متوفر فقط للمشتركين. يرجى الترقية للوصول إلى هذه الميزة.
قم بالترقية الآنTranscripts
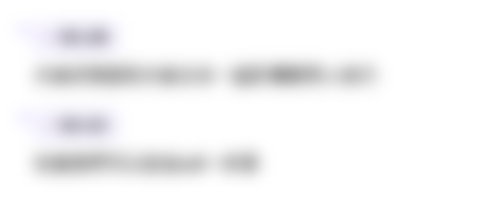
هذا القسم متوفر فقط للمشتركين. يرجى الترقية للوصول إلى هذه الميزة.
قم بالترقية الآنتصفح المزيد من مقاطع الفيديو ذات الصلة
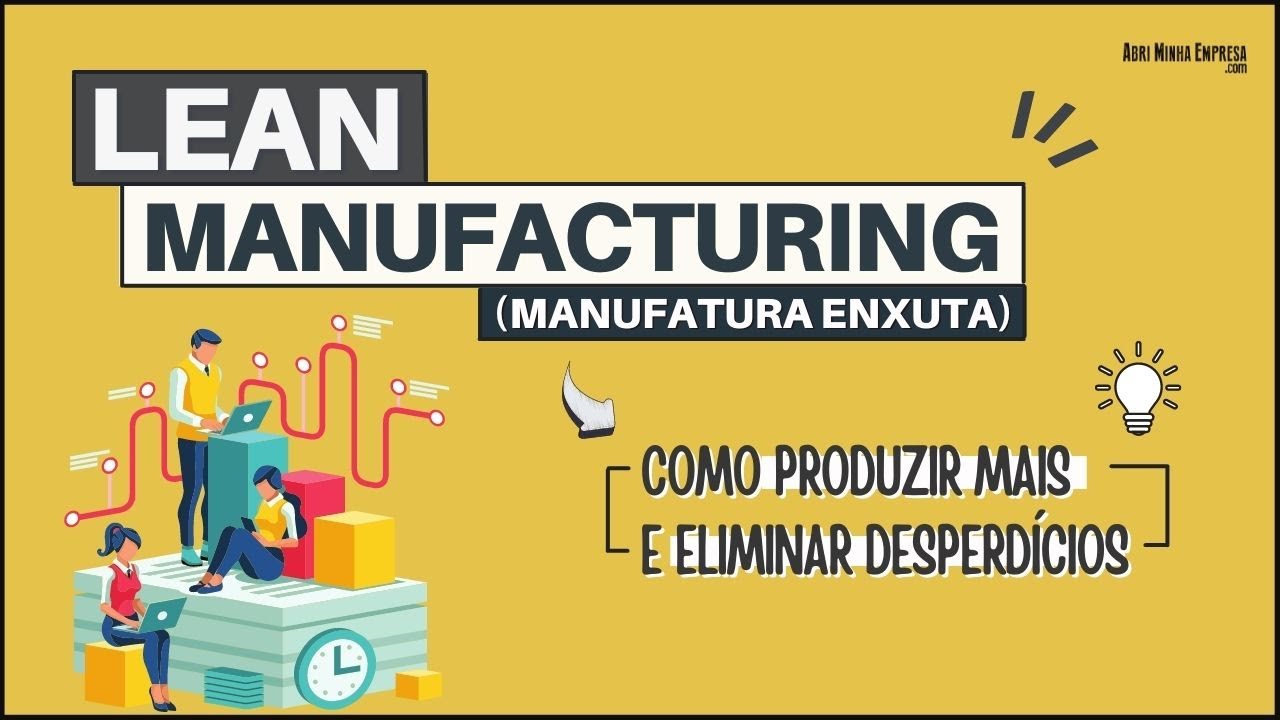
LEAN MANUFACTURING (Manufatura Enxuta) | Conheça os 8 Principais Tipos de Desperdícios
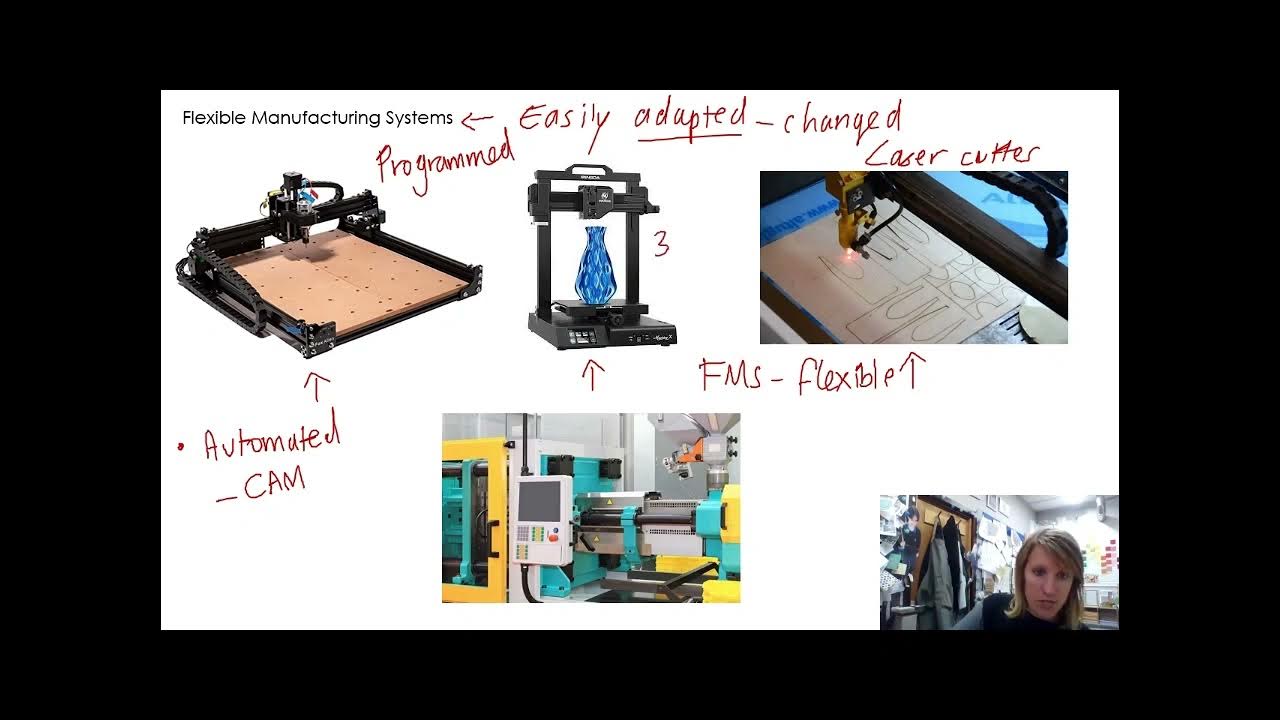
Video 2 - Flexible and Lean Manufacturing
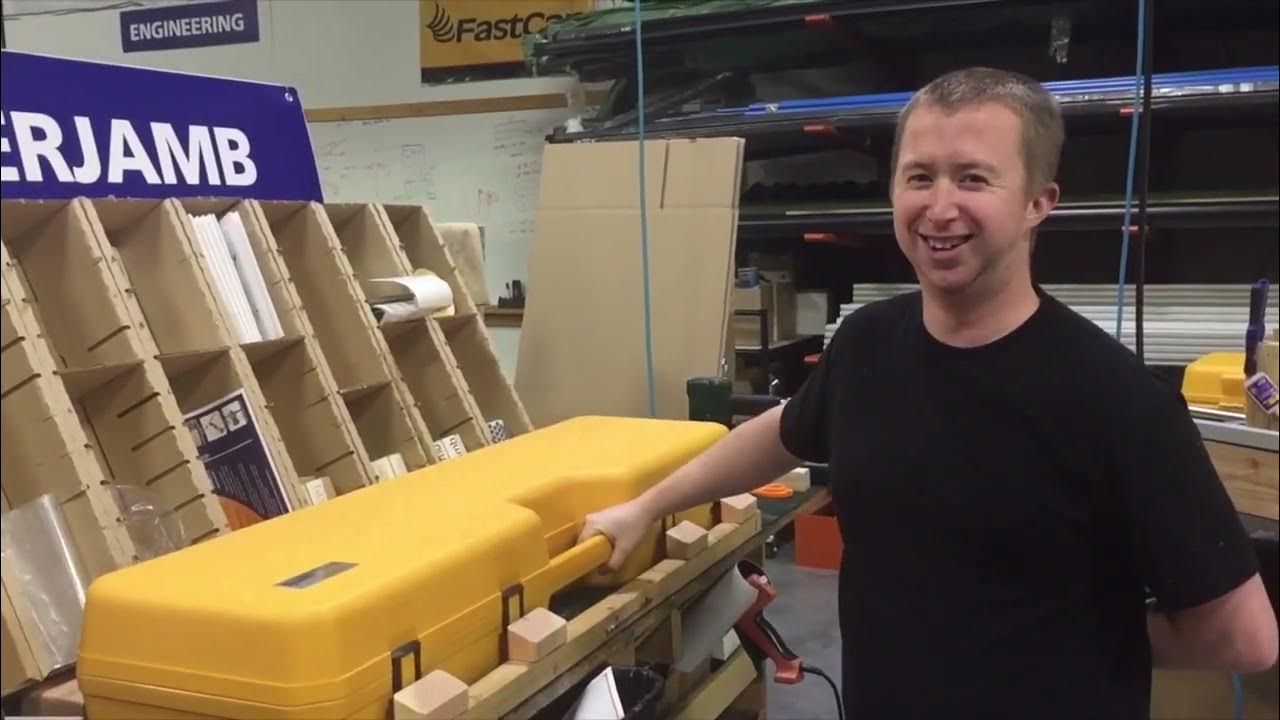
Ch3 - "One Piece Flow" - 2 SECOND LEAN Visual Audiobook

⚙ Lean Manufacturing | A pursuit of perfection
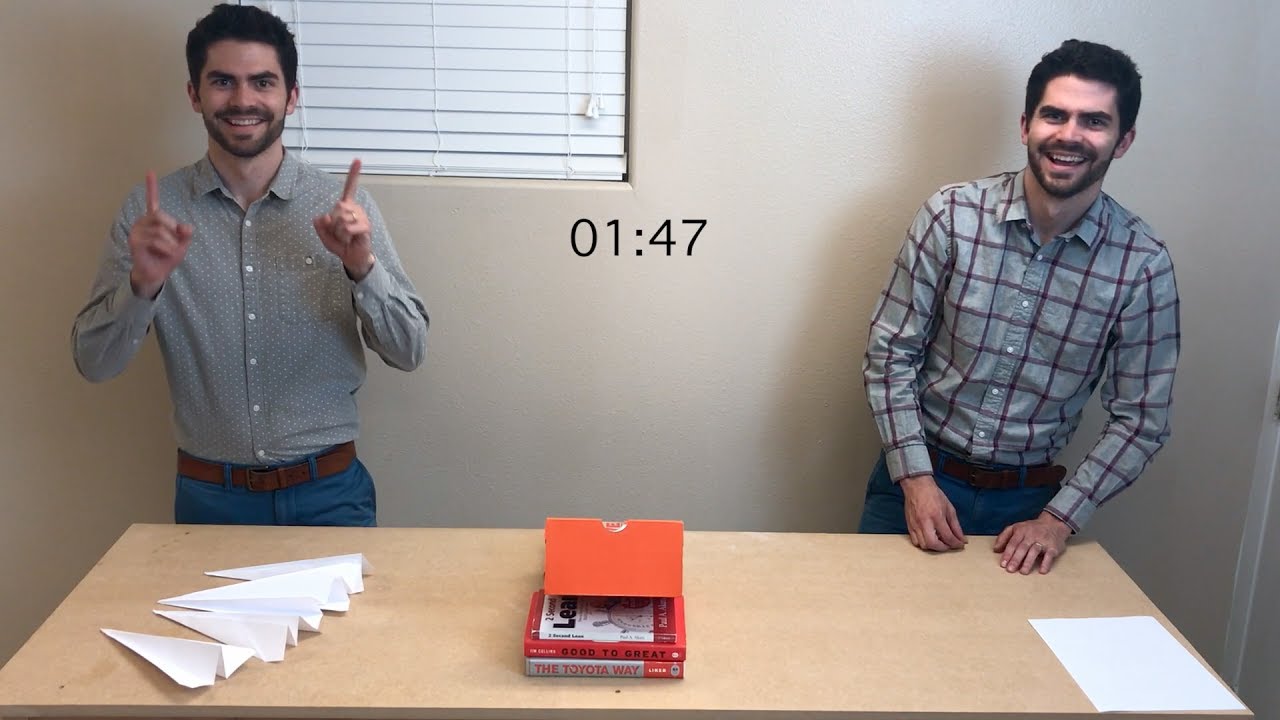
Lean Manufacturing One Piece Flow vs. Mass Production Paper Airplane Simulation (Lean Tip 005)

Essential Strategies for Increasing Production Efficiency
5.0 / 5 (0 votes)