Frito Lay - Continuous Improvement
Summary
TLDRFred Delay's company has been perfecting its continuous improvement processes for 20 years, incorporating autonomous maintenance, lean Six Sigma, and Team Ford methodologies. However, with the increasing complexity of these processes, they recognized the need for simplification. In response, they've developed the CI performance model, a streamlined approach that combines the best of their tools, empowering frontline teams to solve problems efficiently without being overwhelmed by processes. This new model aims to make the company more agile and competitive, leveraging employee knowledge to drive success.
Takeaways
- 🔄 Continuous Improvement is a core philosophy at Fred Delay, aimed at enhancing problem-solving and performance.
- 🛠️ The company has integrated various improvement methodologies like Autonomous Maintenance, Lean Six Sigma, and Team Ford Building over the years.
- 🗣️ Feedback from the field indicated that the multitude of improvement tools and processes had become overly complex.
- 🤔 There was a realization that the focus might have shifted from solving problems to managing the complexity of the processes themselves.
- 👥 A team of field leaders developed a streamlined approach called the CI Performance Model to simplify and consolidate the improvement efforts.
- 🛡️ The CI Performance Model amalgamates the best elements of existing tools, making them more accessible and less cumbersome.
- 💡 The new model emphasizes empowering frontline teams with problem-solving skills rather than overwhelming them with process.
- 📈 The CI Performance Model is designed to make problem-solving more efficient, allowing those closest to the issues to address them directly.
- 🔧 If escalation is needed, the model ensures that resources are available to support the frontline teams in their problem-solving efforts.
- 📈 The company plans to roll out the CI Performance Model across all teams, aiming to make the organization more agile and competitive.
Q & A
What is the main focus of Fred Delay's continuous improvement processes?
-Fred Delay's continuous improvement processes focus on addressing and eliminating problems, enhancing performance, and adapting to a changing marketplace.
How long has Fred Delay been using continuous improvement processes?
-Fred Delay has been using continuous improvement processes for 20 years.
What additional processes have been integrated into Fred Delay's operations?
-Fred Delay has integrated autonomous maintenance, lean Six Sigma, and Team Ford building into their operations.
Why did Fred Delay's teams feel overwhelmed?
-The teams felt overwhelmed because they had to manage multiple problem-solving processes, systems of escalation, and attend numerous meetings for each tool.
What was the feedback from the front lines regarding the improvement processes?
-The feedback was that the teams had become too focused on the process of problem-solving rather than actually finding solutions.
What is the Design Approach developed by the team of field leaders?
-The Design Approach is a process that leverages the best elements of their tools and simplifies them for easier use, aiming to enable teams with problem-solving skills without being bogged down by complex processes.
What is the CI performance model and how does it work?
-The CI performance model is a streamlined process that combines the best of continuous improvement, autonomous maintenance, lean Six Sigma, and team forward, allowing those who understand the problem to solve it, with escalation resources available if needed.
How does the CI performance model empower the front-line workers?
-The CI performance model empowers front-line workers by trusting and honoring their problem-solving skills and knowledge, giving them less to juggle and more focus on finding solutions.
What is the expected outcome of rolling out the CI performance model?
-The expected outcome is to simplify processes, increase the ability of teams to solve problems, and leverage the knowledge of the people to implement a model that drives success.
How does Fred Delay plan to engage its front-line workers with the new CI performance model?
-Fred Delay plans to engage its front-line workers by rolling out the CI performance model across all teams, providing new skills, and helping the entire company become more nimble and competitive.
What is the ultimate goal of the new approach mentioned in the script?
-The ultimate goal of the new approach is to honor the past while embracing the future, ensuring the company remains successful by simplifying processes and empowering problem-solving at all levels.
Outlines
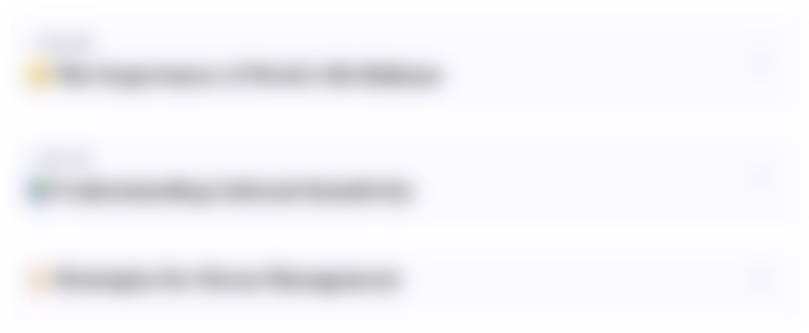
هذا القسم متوفر فقط للمشتركين. يرجى الترقية للوصول إلى هذه الميزة.
قم بالترقية الآنMindmap
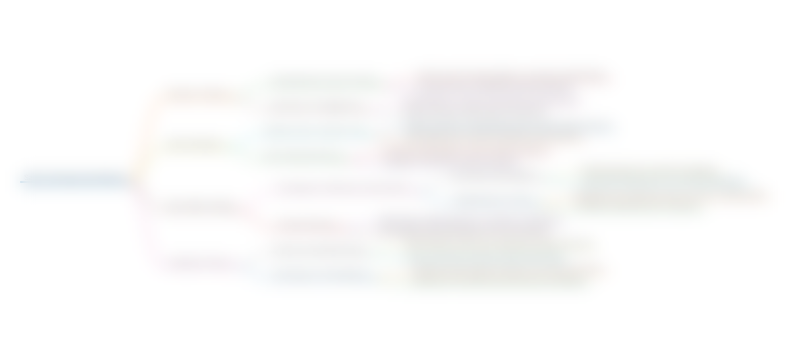
هذا القسم متوفر فقط للمشتركين. يرجى الترقية للوصول إلى هذه الميزة.
قم بالترقية الآنKeywords
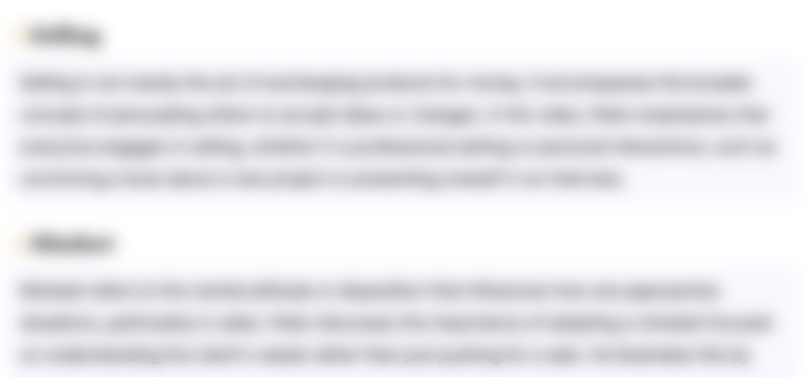
هذا القسم متوفر فقط للمشتركين. يرجى الترقية للوصول إلى هذه الميزة.
قم بالترقية الآنHighlights
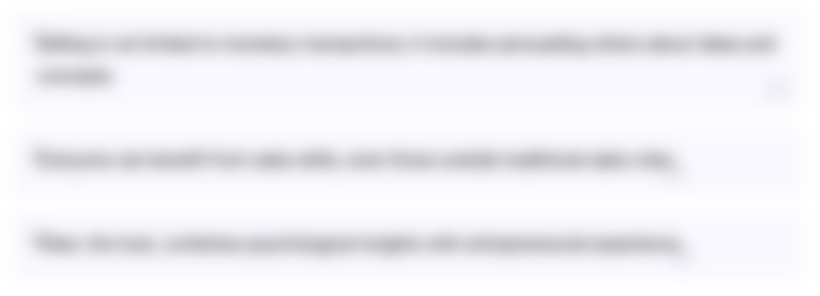
هذا القسم متوفر فقط للمشتركين. يرجى الترقية للوصول إلى هذه الميزة.
قم بالترقية الآنTranscripts
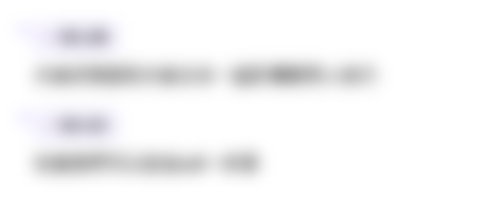
هذا القسم متوفر فقط للمشتركين. يرجى الترقية للوصول إلى هذه الميزة.
قم بالترقية الآنتصفح المزيد من مقاطع الفيديو ذات الصلة
5.0 / 5 (0 votes)