How did Toyota beat FORD & GM using its GENIUS Supply Chain Model?
Summary
TLDRThis script tells the story of Toyota's rise to success despite numerous challenges, including scarce resources, natural disasters, and fierce competition. It highlights Toyota's innovative approach to manufacturing, known as the 'just-in-time' system, which revolutionized supply chain management by eliminating waste and streamlining production. The script also offers insights for entrepreneurs on how to apply Toyota's principles of efficiency and risk management to their own businesses.
Takeaways
- 🌟 Toyota's success is remarkable given the numerous obstacles it faced, including limited natural resources, a small population, frequent natural disasters, and post-WWII economic devastation.
- 🏭 Despite the challenges, Toyota became the world's largest car manufacturer in 2008 and had a market capitalization in 2016 that surpassed Ford, General Motors, and Honda combined.
- 🚀 The key to Toyota's success was its innovative business strategy, particularly the development of the lean manufacturing system, which focused on efficiency.
- 🔍 Toyota identified four major inefficiencies in the traditional manufacturing process: overproduction, excessive inventory, unnecessary capital investment, and wasteful resource allocation.
- 🛠️ The company revolutionized supply chain management by introducing the just-in-time (JIT) system, which eliminated the need for demand forecasting and inventory.
- ⏱️ JIT production allowed Toyota to respond quickly to customer orders, reducing waste and lead times, and increasing profit margins significantly.
- 🌐 The JIT system not only transformed the automobile industry but also became a global standard for supply chain management across various fields.
- 📈 Toyota's growth was exponential, with a 2,000% increase in production from 1955 to 1965, demonstrating the effectiveness of their supply chain strategy.
- 💡 Entrepreneurs can learn from Toyota's approach by understanding that adversity can drive innovation and that copying competitors' systems is not always the best strategy.
- 📚 For deeper insights, the speaker recommends studying Toyota's risk mitigation strategies during crises and exploring additional Toyota principles like Kanban, Kaizen, and Jidoka.
Q & A
What were the significant challenges Toyota faced in its early years?
-Toyota faced numerous challenges in its early years, including being based in a small country with limited natural resources and a high cost of raw materials and labor. Japan's susceptibility to natural disasters like earthquakes and tsunamis also posed a threat. Additionally, the company had to navigate the aftermath of World War II, which left Japan's economy in ruins, and compete with established American automotive giants like General Motors and Ford.
How did Toyota's financial situation impact its ability to compete with American manufacturers?
-Toyota was in a very poor financial condition, which prevented it from purchasing the latest Western production machinery needed to improve production efficiency and scale up. This financial constraint, coupled with Japan's post-war capital and foreign exchange scarcity, made it impossible for Toyota to compete with American companies on the basis of capital and machinery.
What was the key aspect in which Toyota believed it could outperform American manufacturers?
-Despite the financial and machinery disadvantages, Toyota identified efficiency as the key aspect in which it could outperform American manufacturers. This led to the development of the lean manufacturing system, which focused on eliminating waste and optimizing production processes.
What is the lean manufacturing system and how did it help Toyota?
-The lean manufacturing system is a method that focuses on minimizing waste within a manufacturing system without sacrificing productivity. It helped Toyota by allowing it to compete with larger, more capital-intensive manufacturers by optimizing its production processes, reducing waste, and increasing efficiency.
How did Toyota's visit to the Ford Rouge plant influence its approach to manufacturing?
-After visiting the Ford Rouge plant, Toyota's top managers realized that simply copying and improving the Rouge system would not work for them due to financial constraints and the need for a system that could be implemented with limited resources. This led to the development of the lean manufacturing system.
What were the four major inefficiencies identified by the Toyota team in the traditional manufacturing process?
-The four major inefficiencies identified were: 1) Excessive resource allocation due to inaccurate demand forecasting, leading to unnecessary hiring, equipment purchases, and inventory stockpiling. 2) Overproduction, which wasted resources and increased costs. 3) Excessive inventory of final products, leading to high maintenance, labor, and transportation costs. 4) Unnecessary capital investment, which resulted in high interest costs and other administrative expenses without any return on investment.
How did Toyota's just-in-time (JIT) system revolutionize supply chain management?
-Toyota's just-in-time system revolutionized supply chain management by eliminating the need for demand forecasting and inventory. It focused on producing goods only as they were needed, which reduced waste, minimized storage costs, and increased efficiency across the entire supply chain.
What were the three superpowers that Toyota gained from implementing the just-in-time production system?
-The three superpowers gained from JIT were: 1) Minimal damage from reduced demand or disruptions due to lower component stock and near-zero inventory. 2) Elimination of waste, leading to extreme cost-cutting and increased profit margins. 3) Rapid production growth, with Toyota experiencing a significant increase in the number of vehicles produced over the years.
What lessons can entrepreneurs learn from Toyota's approach to innovation and efficiency?
-Entrepreneurs can learn that adversity often breeds innovation, the importance of not simply copying competitors' systems but adapting them to their own constraints, and the value of developing strategies that mitigate risk and enhance efficiency.
What additional strategies did Toyota employ alongside the JIT principle to ensure success?
-Besides the JIT principle, Toyota also employed the Kanban system for inventory control, the Kaizen model for continuous improvement, and the Jidoka method for automation with a human touch. These strategies, along with JIT, contributed to Toyota's resilience and success.
How did Toyota's response to the 1997 Aisin Seiki fire and the 2016 Kumamoto earthquake demonstrate its risk mitigation strategies?
-Toyota's response to these events showcased its ability to quickly adapt and recover from supply chain disruptions. The company's just-in-time approach, though initially causing some disruption, was complemented by other risk mitigation strategies that allowed it to minimize long-term impacts and maintain operations.
Outlines
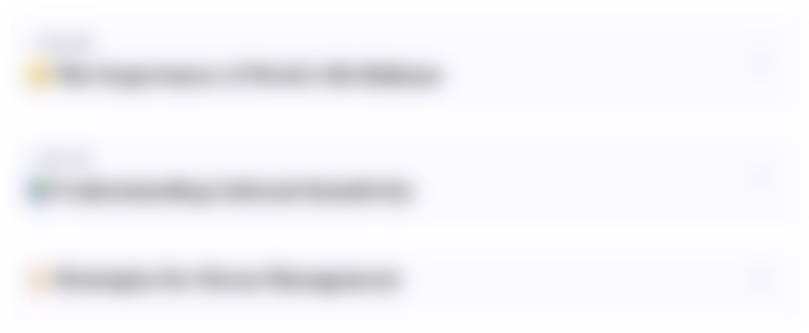
هذا القسم متوفر فقط للمشتركين. يرجى الترقية للوصول إلى هذه الميزة.
قم بالترقية الآنMindmap
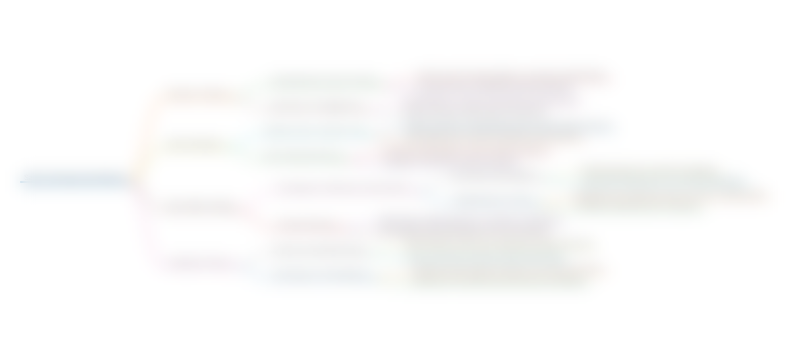
هذا القسم متوفر فقط للمشتركين. يرجى الترقية للوصول إلى هذه الميزة.
قم بالترقية الآنKeywords
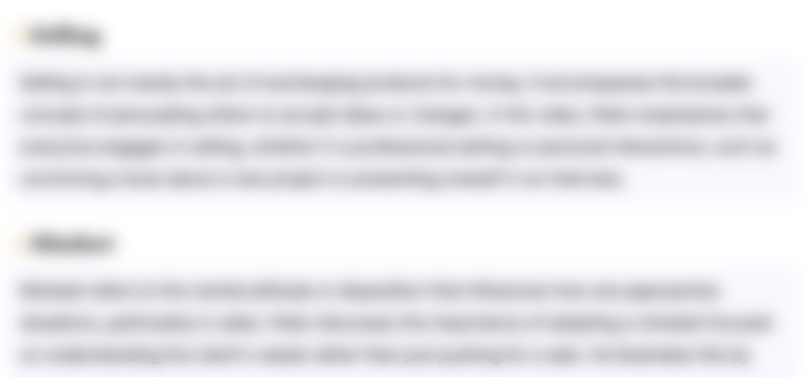
هذا القسم متوفر فقط للمشتركين. يرجى الترقية للوصول إلى هذه الميزة.
قم بالترقية الآنHighlights
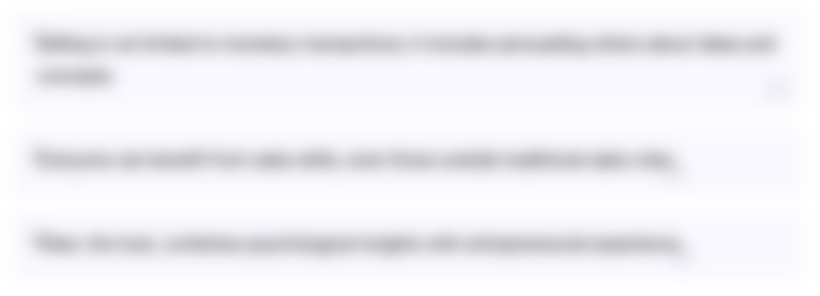
هذا القسم متوفر فقط للمشتركين. يرجى الترقية للوصول إلى هذه الميزة.
قم بالترقية الآنTranscripts
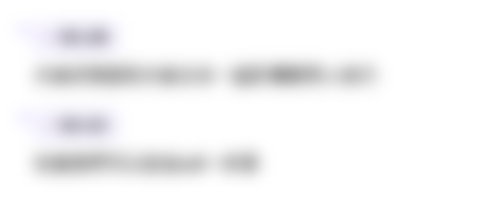
هذا القسم متوفر فقط للمشتركين. يرجى الترقية للوصول إلى هذه الميزة.
قم بالترقية الآنتصفح المزيد من مقاطع الفيديو ذات الصلة
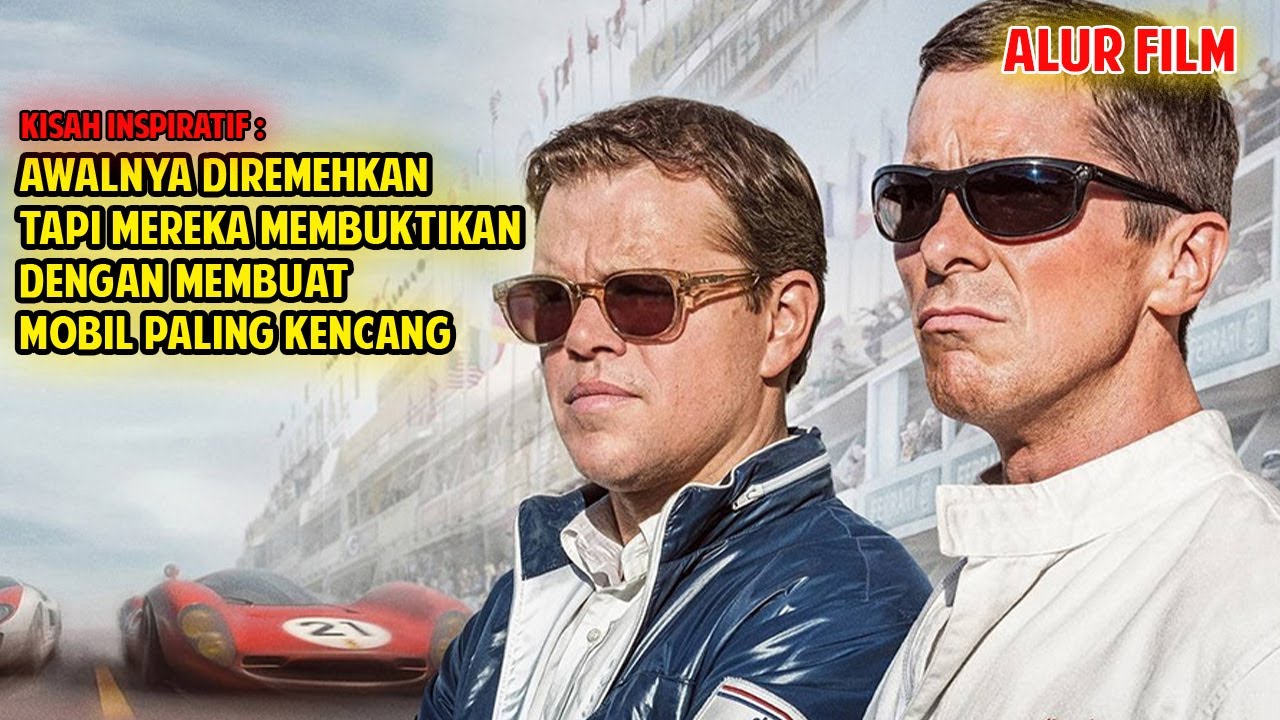
KISAH NYATA - PERSAINGAN DUA PERUSAHAAN MOBIL CEPAT (FERRARI vs FORD) | Alur Cerita Film
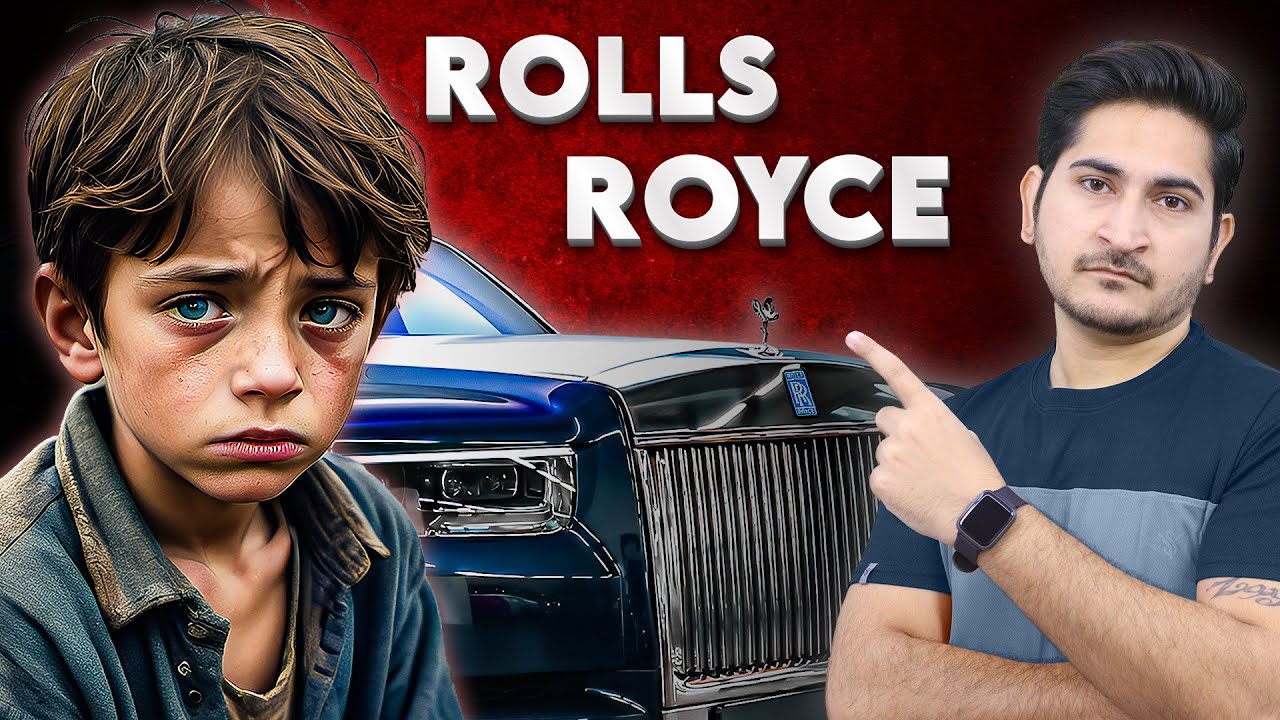
How A Poor Boy Created World's Most Expensive Car I Rolls Royce Case study
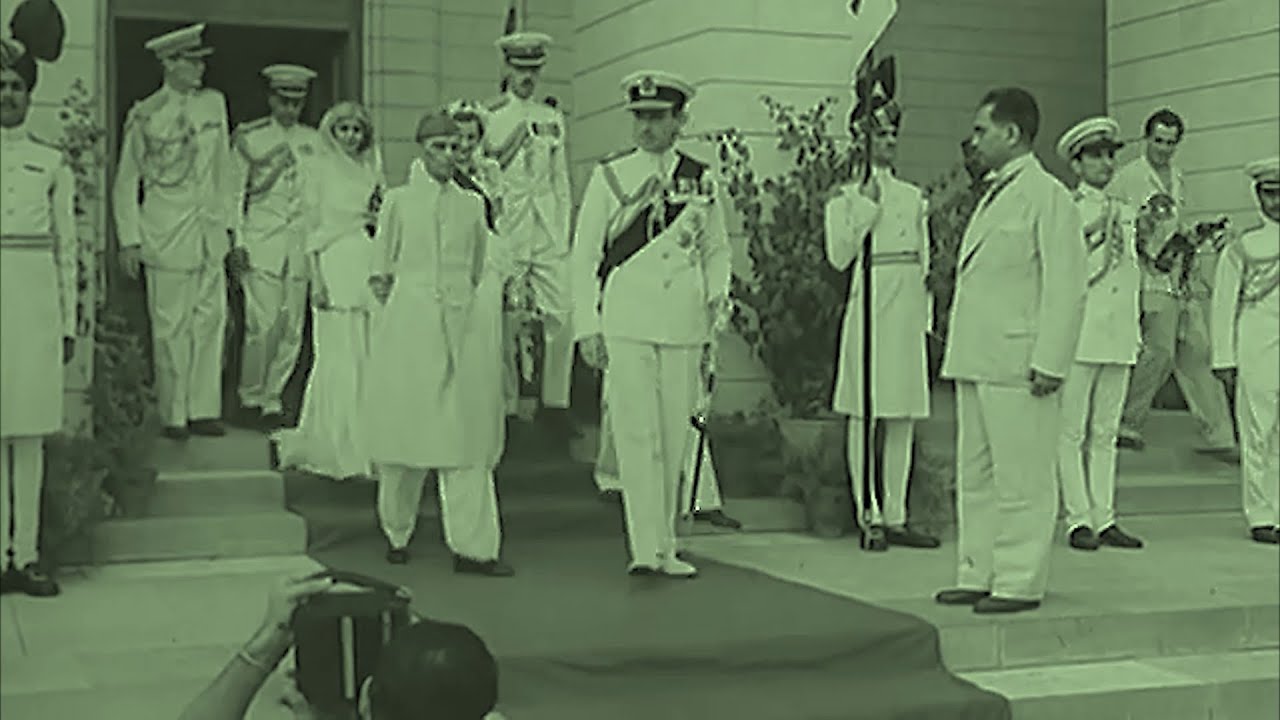
Story of Pakistan | Documentary on Pakistan's 75 years of Independence Diamond Jubilee | #ptdc
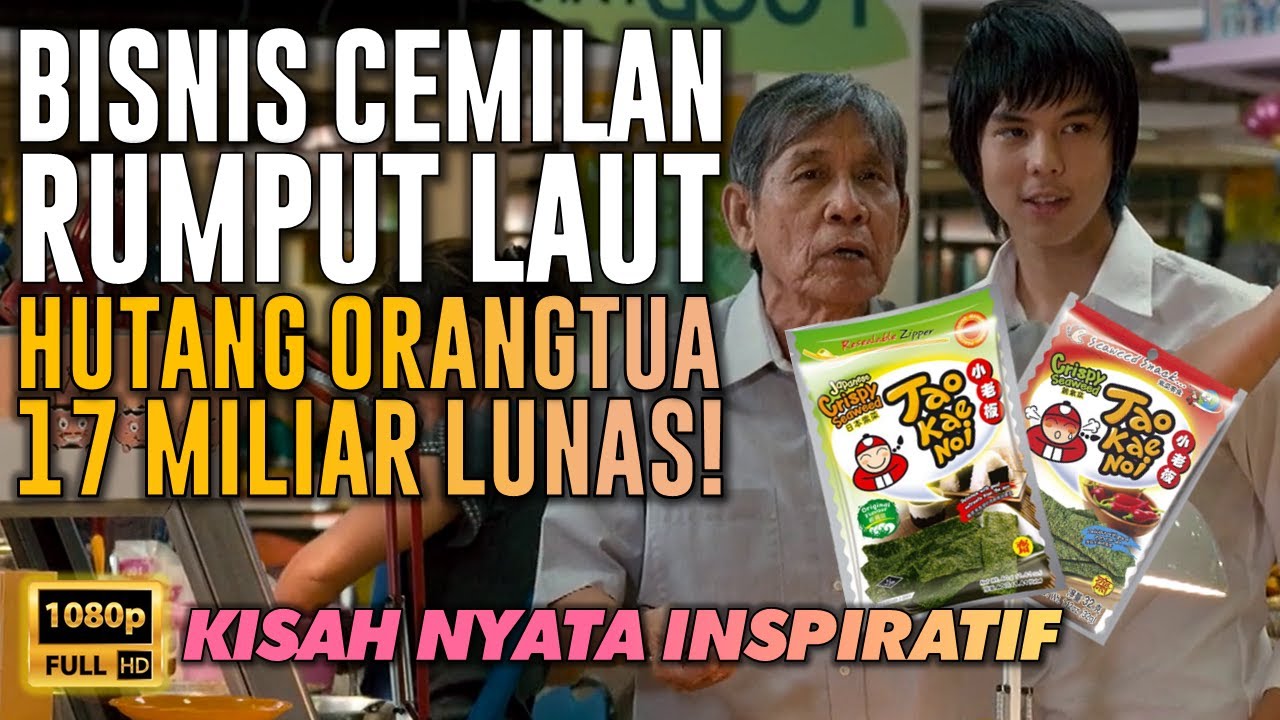
Kisah Inspiratif Miliarder Muda Thailand yang Jualan Cemilan - Alur Cerita Film

As Olimpíadas na Grécia Antiga

Letak Geografis Indonesia yang Terbaik Namun Juga Mengerikan
5.0 / 5 (0 votes)