What is a PID Controller?
Summary
TLDRThis video by RealPars introduces PID controllers, which stand for proportional, integral, and derivative control. PID controllers are crucial for maintaining constant variables, such as temperature, in automated processes by using control loop feedback. Examples include cruise control in cars and temperature controllers in manufacturing. The video explains how PIDs work, using both standalone units and PLC programming, and demonstrates their ability to regulate outputs like temperature based on input from sensors. The video concludes by encouraging viewers to explore further learning on PLC programming at realpars.com.
Takeaways
- 🔧 A PID controller stands for Proportional, Integral, Derivative, used for maintaining constant conditions like temperature.
- 🔄 It operates through a control loop feedback system, adjusting the output based on input from sensors to achieve a set point.
- 🚗 An everyday example of PID control is vehicle cruise control, which adjusts throttle to maintain a set speed.
- 🌡️ In industry, PID controllers are commonly used for temperature control, such as in heat tracing on process piping.
- ⚙️ The controller can be set up to turn heating on/off based on temperature readings from a thermocouple, exemplifying basic PID control.
- 🤖 For more advanced setups, a PID controller can be integrated with a PLC, utilizing the PLC's input and output cards.
- 💡 The PID within a PLC can perform calculations and make decisions based on programmed variables and set points.
- 🛠️ PID controllers come in various forms, including standalone units and as part of PLC programming, offering flexibility for different applications.
- 📈 They are essential for automated processes, helping to maintain constant conditions like temperature, pressure, or flow automatically.
- 👨🏫 The video is a resource for those looking to understand PID usage, especially in the context of PLC programming and automation.
Q & A
What does PID stand for in the context of automation and PLCs?
-PID stands for Proportional, Integral, and Derivative, which are the three control functions used in a PID controller.
What is the main purpose of a PID controller in an automated process?
-The main purpose of a PID controller is to maintain a process variable, such as temperature, pressure, or flow, at a constant value by using control loop feedback.
How does a PID controller use feedback to maintain a desired output?
-A PID controller uses control loop feedback from a sensor (such as a temperature sensor) to adjust the output, ensuring that the desired set point is maintained.
Can you give a real-world example of PID control in everyday life?
-An example of PID control in everyday life is cruise control in a car, which maintains a constant speed by adjusting the throttle based on feedback from a speed sensor.
How does a PID controller regulate temperature in industrial applications?
-In industrial applications, a PID controller regulates temperature by receiving feedback from a sensor, such as a thermocouple, and adjusting the heating element to maintain the set temperature.
What is an example of a standalone PID controller used in manufacturing?
-A common standalone PID controller used in manufacturing is a temperature controller, which can regulate the temperature of equipment like heat tracing on process piping.
How can PID controllers be integrated with PLCs?
-PID controllers can be integrated with PLCs by using input and output cards. The process variable is wired to the input card, and the output being controlled is wired to the output card. The PLC then handles the PID calculations and control.
What is a basic form of PID control?
-A basic form of PID control is on-off control, where the system turns on or off when the process variable crosses certain thresholds, such as heating turning off at 202°F and turning back on at 198°F.
What are the key components of a PID control loop?
-The key components of a PID control loop are the process variable (sensor input), the set point (desired output), and the control output (adjustment made to maintain the set point).
Why are PIDs considered useful in automated processes?
-PIDs are considered useful because they automatically adjust the control outputs to maintain consistent process variables, reducing the need for manual intervention and improving system efficiency.
Outlines
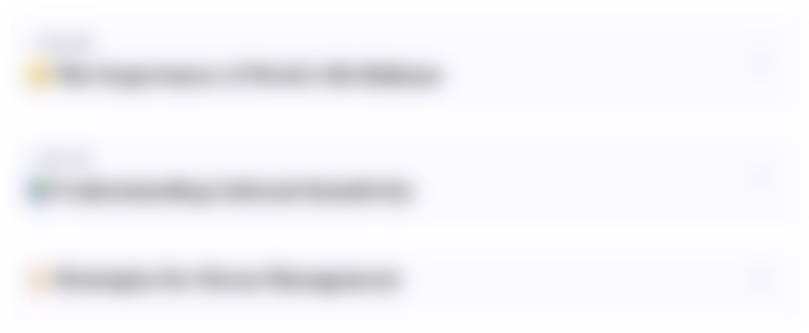
هذا القسم متوفر فقط للمشتركين. يرجى الترقية للوصول إلى هذه الميزة.
قم بالترقية الآنMindmap
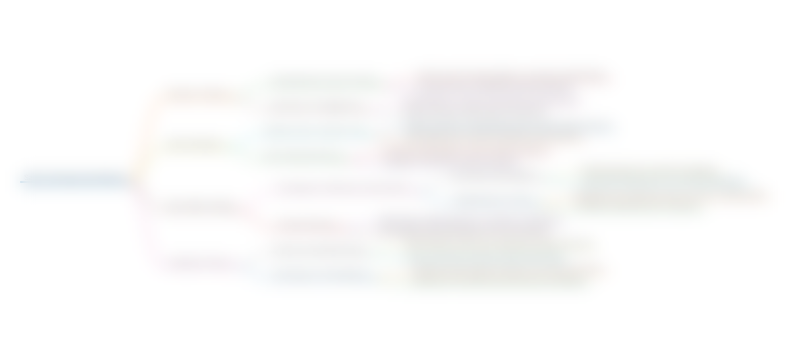
هذا القسم متوفر فقط للمشتركين. يرجى الترقية للوصول إلى هذه الميزة.
قم بالترقية الآنKeywords
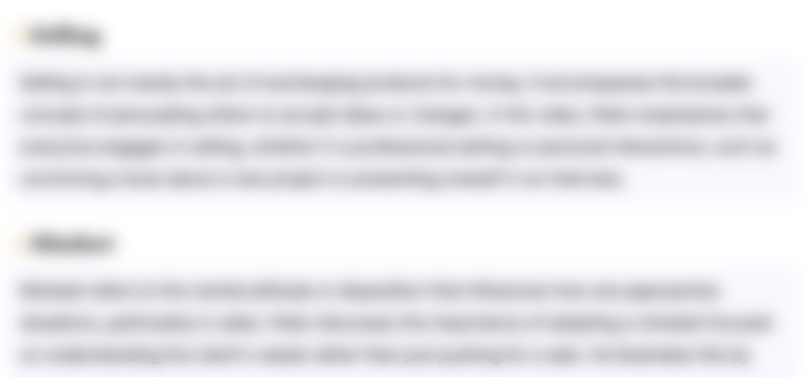
هذا القسم متوفر فقط للمشتركين. يرجى الترقية للوصول إلى هذه الميزة.
قم بالترقية الآنHighlights
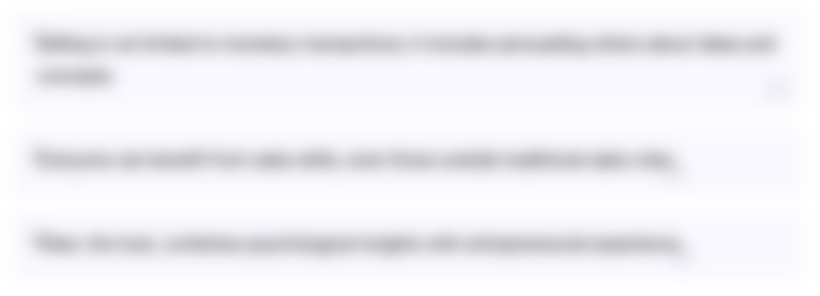
هذا القسم متوفر فقط للمشتركين. يرجى الترقية للوصول إلى هذه الميزة.
قم بالترقية الآنTranscripts
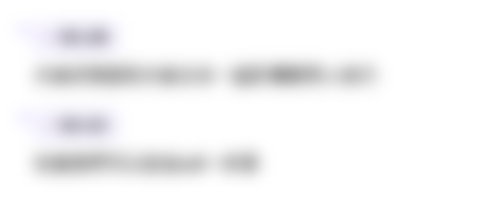
هذا القسم متوفر فقط للمشتركين. يرجى الترقية للوصول إلى هذه الميزة.
قم بالترقية الآن5.0 / 5 (0 votes)