CR Masterclass 3 - World Class GET Manufacturing
Summary
TLDRJames De Ru, Operations Manager at CR Mining's Maryborough Foundry in Australia, presents a master class on maximizing cast lip and GT manufacturing. The foundry, with over a century of history, specializes in producing high-quality castings for excavators and other heavy machinery. Leveraging cutting-edge technologies like Magma software for casting simulation and additive manufacturing for pattern making, the facility ensures optimal production processes. The video highlights the importance of steel making, heat treatment, and non-destructive testing in achieving world-class castings that meet stringent quality standards.
Takeaways
- 🏭 James Deru, Operations Manager at CR Mining's Maryborough Foundry, presents a master class on maximizing cast lip in GT manufacturing.
- 🌟 The foundry has a rich history of over 100 years and specializes in producing high-quality GT and car slips for over 40 years.
- 💹 CR Mining has made significant investments in state-of-the-art technologies to ensure future production excellence.
- 🔩 The facility manufactures a wide range of car slips, from small excavators to the largest 800-ton excavators, wheel loaders, rope shovels, and drag lines.
- 👨🔬 The site employs 112 personnel, including foundry specialists such as methods engineers, metallurgists, and welding engineers, who are crucial for consistent high-quality castings.
- 🔧 The manufacturing process begins with casting simulation using Magma software to optimize the casting process and identify potential defects.
- 🛠️ Patterns are produced by CNC machining and additive manufacturing technologies, like 3D printing, to provide tight dimensional tolerances and rapid results.
- ⚙️ On-site, a hard sand process using the furane resin system is employed, along with automated core blowers for producing cores.
- 🔩 CR has invested over 1.5 million dollars in mold and core making capabilities, enhancing the quality and efficiency of casting production.
- 🔥 Steel making is a critical step, with two electric arc furnaces used for special refining processes to ensure high-quality steel for castings.
- 🛡️ Advanced steel analysis techniques, including optical emission spectrometers and hydrogen analysis, are used to ensure steel meets strict specifications.
- 🌡️ Post-steel making, molten steel is poured into sand molds and later heat-treated in gasified stoves to modify the steel's microstructure for optimal mechanical properties.
- 📏 Gauging and dimensional assessments, or metrology, are critical for quality assurance, ensuring all components fit smoothly and safely in the field.
- 🔎 Non-destructive testing (NDT) techniques such as magnetic particle inspection (MPI), ultrasonic testing (UT), and hardness testing are employed to assess casting quality and compliance.
Q & A
Who is the speaker in the video and what is his role at CR Mining's Maryborough Foundry?
-The speaker is James Deru, who is the Operations Manager at CR Mining's Maryborough Foundry.
What is the main topic of the master class presented by James Deru?
-The main topic of the master class is how to maximize cast lip in GT manufacturing for customization needs.
How long has CR Mining's Maryborough Foundry been in operation?
-CR Mining's Maryborough Foundry has over 100 years of history.
What types of equipment does the foundry produce?
-The foundry produces a range of equipment including GT and car slips, excavators, wheel loaders, rope shovels, and drag lines.
What is the significance of the personnel employed at the site?
-The site employs 112 personnel, including foundry specialists such as methods engineers, metallurgists, and welding engineers, who are essential for producing consistent high-quality castings.
What software does CR use for casting simulation and why is it important?
-CR uses Magma software for casting simulation to optimize the casting process and identify possible defects like shrinkage and hot spots, ensuring optimal manufacturing solutions.
How does CR Mining's foundry ensure tight dimensional tolerances in pattern production?
-CR employs CNC machining for pattern production, which allows for the tightest dimensional tolerances and can be completed on different pattern materials.
What is the role of the hard sand process in mold and core production at the foundry?
-The hard sand process using the furane resin system and various types of sands is used to provide different mold properties, and cores are produced on automated core blowers.
How does CR Mining's foundry ensure the quality of steel used in castings?
-The foundry uses electric arc furnaces for steel making, allowing for special refining processes to remove impurities and gases detrimental to steel quality.
What technologies does the foundry use to assess the steel quality and ensure it meets specifications?
-The foundry uses optical emission spectrometers, including a market-leading ISPAC 8820, and a hydrous unit for hydrogen analysis to ensure steel quality.
How does the foundry enhance the steel quality after it is tapped into the pouring ladle?
-The foundry employs clean steel technology, which involves the induction injection of calcium wire and purging with argon gas to remove and modify inclusions in the steel.
What is the purpose of heat treatment in the casting process at CR Mining's foundry?
-Heat treatment is used to modify the microstructure of the steel to provide the final mechanical properties, which is essential for producing high-quality castings that meet customer needs.
How does the foundry ensure dimensional accuracy and compliance of castings?
-The foundry uses state-of-the-art metrology equipment, such as 3D scanners and furrow arms, to measure critical dimensions and ensure castings are compliant with tight dimensional requirements.
What non-destructive testing (NDT) techniques are employed to assess castings for defects?
-NDT techniques such as magnetic particle inspection (MPI), ultrasonic testing (UT), and hardness testing are used to assess for defects and validate heat treatment compliance.
Outlines
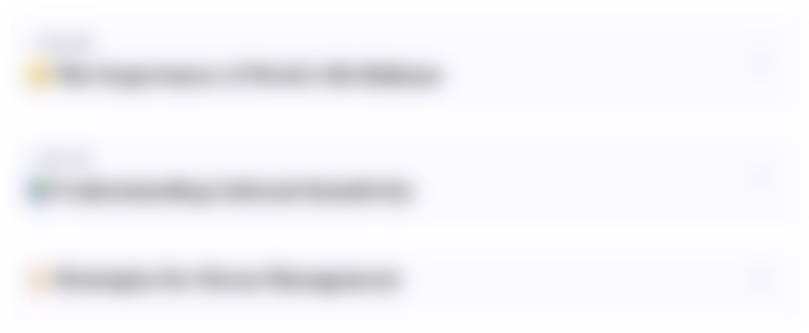
هذا القسم متوفر فقط للمشتركين. يرجى الترقية للوصول إلى هذه الميزة.
قم بالترقية الآنMindmap
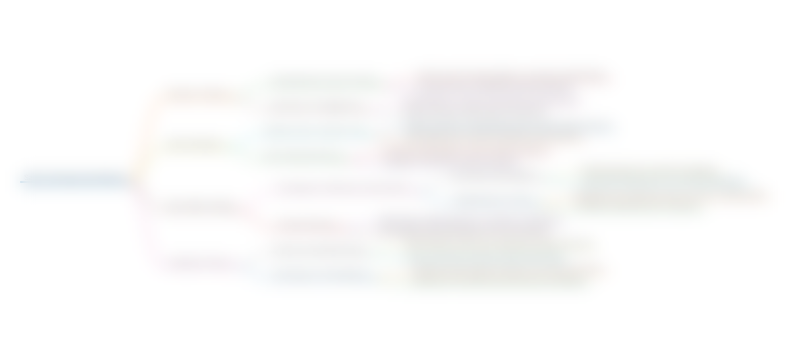
هذا القسم متوفر فقط للمشتركين. يرجى الترقية للوصول إلى هذه الميزة.
قم بالترقية الآنKeywords
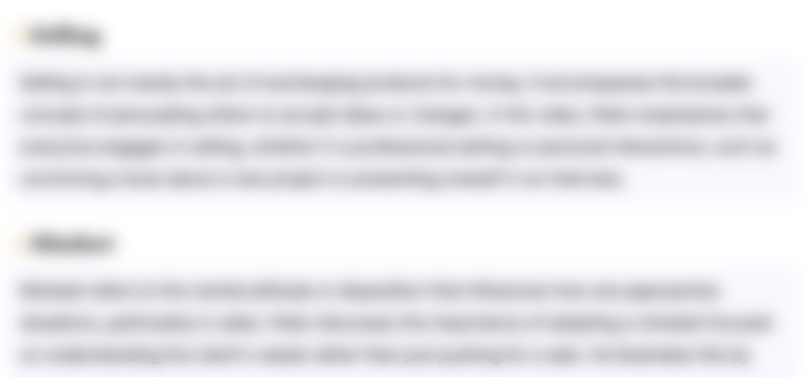
هذا القسم متوفر فقط للمشتركين. يرجى الترقية للوصول إلى هذه الميزة.
قم بالترقية الآنHighlights
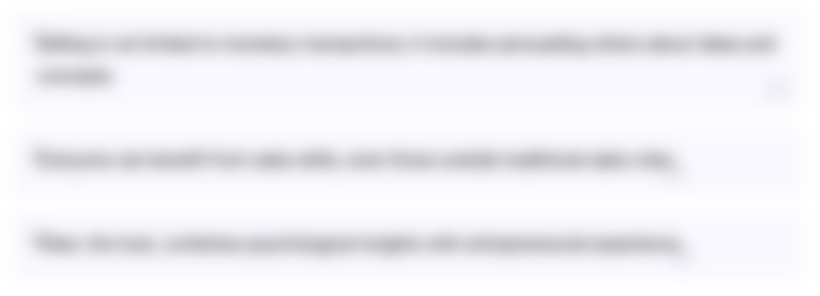
هذا القسم متوفر فقط للمشتركين. يرجى الترقية للوصول إلى هذه الميزة.
قم بالترقية الآنTranscripts
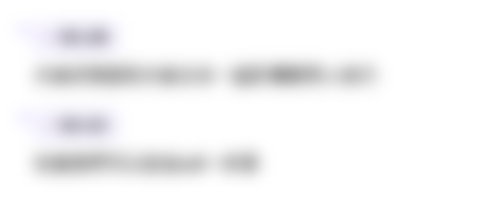
هذا القسم متوفر فقط للمشتركين. يرجى الترقية للوصول إلى هذه الميزة.
قم بالترقية الآنتصفح المزيد من مقاطع الفيديو ذات الصلة

CR Masterclass 1 - GET Improvement

Meet Our Experts – Dr Renusha Athugala | Innovating games beyond entertainment | RMIT Vietnam
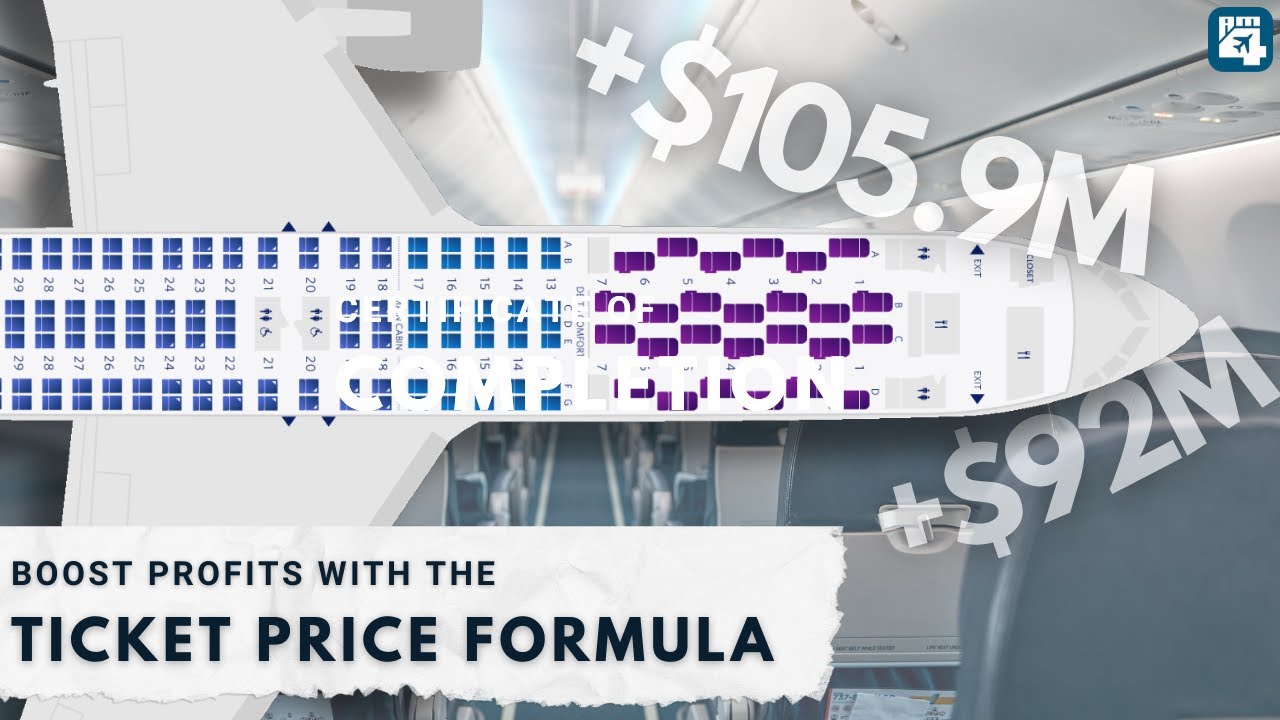
How to Set the PERFECT Ticket Prices in Airline Manager 4

Azure EmbodiedAI Sample Lip Sync Visemes
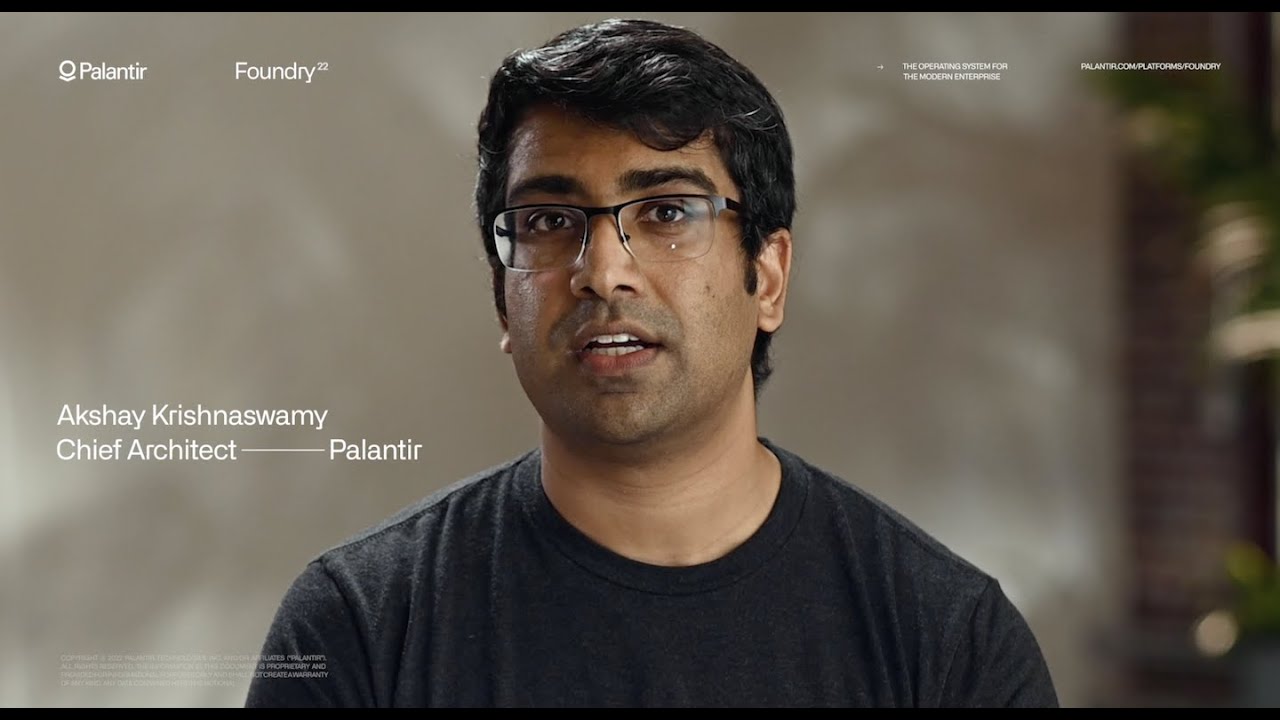
Palantir Explained: Chief Architect on Foundry in 2022

Demystifying Business Operations: Your Ultimate Guide to Efficiency and Success! 🌐💼
5.0 / 5 (0 votes)