Airframes & Aircraft Systems #1 - Aircraft Structures - Loads Applied to the Airframe
Summary
TLDRThis lesson in the airframe structures series explores the various loads on aircraft structures, including tensile, compressive, and shear loads, and their effects on materials. It delves into the significance of stress, strain, and Young's modulus of elasticity in aircraft design. The concept of design limit and ultimate loads, along with safety factors, is discussed to ensure aircraft safety. The video also covers failsafe and damage-tolerant structures, explaining how they manage loads and prevent catastrophic failures. Additionally, it touches on the importance of aircraft's safe life and maintenance to mitigate fatigue and corrosion.
Takeaways
- ✈️ Aircraft structures experience various loads like tensile, compressive, and shear, which are critical in design and construction.
- 🔍 Tensile loads stretch structural members, while compressive loads shorten them; these are resisted by ties and struts respectively.
- 🔧 Riveted joints and adhesive bonding processes are used to resist shear forces, important in aircraft construction.
- 🔄 Bending, torsion, and buckling involve a combination of tensile, compressive, and shear loads, affecting the integrity of the structure.
- 📏 Stress is the internal force resisting an external load, and strain measures the deformation caused by this stress.
- 📐 Young's modulus of elasticity describes the relationship between stress and strain within the elastic limit of materials.
- 🚀 The design limit load for aircraft is based on the load factor, and structures are built to withstand design ultimate loads with a safety factor.
- 🛠️ Aircraft structures are designed to be failsafe or damage tolerant, with multiple load paths or damage-tolerant designs to ensure safety.
- ⏳ The safe life of aircraft components is monitored through cycles, such as flying hours or pressurization cycles, to prevent catastrophic failure.
- 📍 Aircraft components are identified by reference lines like fuselage station numbers, wing station numbers, and water lines, ensuring precise maintenance and repairs.
Q & A
What are the various loads applied to aircraft structures?
-Aircraft structures are subjected to tensile, compressive, and shear loads. Tensile loads stretch structural members, compressive loads shorten them, and shear forces slide one face of the material over another.
What is the function of stringers in modern aircraft fuselages?
-Stringers in modern aircraft fuselages are designed to resist tensile loads, particularly those produced by pressurization.
How do landing gear struts contribute to an aircraft's structural integrity?
-Landing gear struts, such as the oleo pneumatic strut, resist compressive loads during landing, ensuring the aircraft's structural integrity under impact forces.
What is the difference between a tensile stress and a compressive stress?
-Tensile stress is the internal force that resists a force that tends to stretch a structural member, while compressive stress resists a force that tends to shorten a structural member.
How is strain measured in aircraft structures?
-Strain is measured as the ratio of the change in a material's length to its original length, indicating the deformation of a loaded structure.
What is Young's Modulus of Elasticity and how is it discovered?
-Young's Modulus of Elasticity is a constant that describes the relationship between stress and strain for an elastic material within its elastic limit. It was discovered by the 18th-century English physicist Thomas Young.
What is the significance of the design limit load in aircraft design?
-The design limit load is the maximum load that a designer expects an airframe or component to experience in service, defined as a load factor, which is the ratio of the lift of an aircraft to its weight.
How does the safety factor relate to the design ultimate load?
-The design ultimate load is the design limit load multiplied by a safety factor, which is a minimum of 1.5 as specified in design requirements, ensuring the structure can withstand this load without collapse.
What are fail-safe and damage-tolerant structures in aircraft design?
-Fail-safe structures incorporate component redundancy and multiple load paths, allowing loads to be shared by adjacent members if one part fails. Damage-tolerant structures are designed to withstand a certain amount of damage before failure occurs, spreading the loading over a larger area.
How do pressurized aircraft fuselages handle stress from pressurization?
-Pressurized aircraft fuselages handle stress from pressurization through axial (longitudinal) and hoop (radial) stresses. Hoop stresses, which tend to expand the fuselage cross-section, are of greater significance than axial stresses.
What is the purpose of using reference lines in aircraft design for maintenance?
-Reference lines are used in aircraft design to locate components for maintenance and repairs. They identify positions fore-and-aft, left and right, and from top to bottom, using station numbers and datum lines.
Outlines
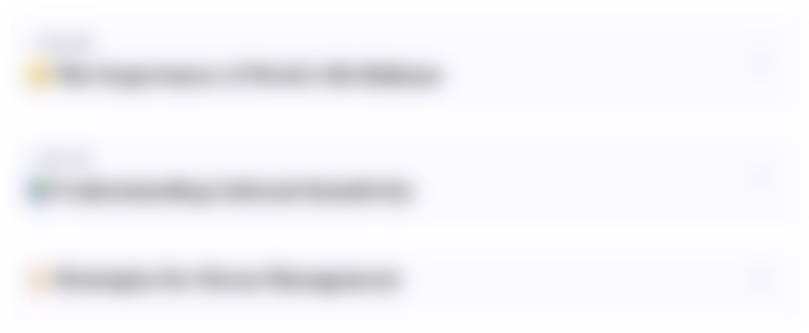
هذا القسم متوفر فقط للمشتركين. يرجى الترقية للوصول إلى هذه الميزة.
قم بالترقية الآنMindmap
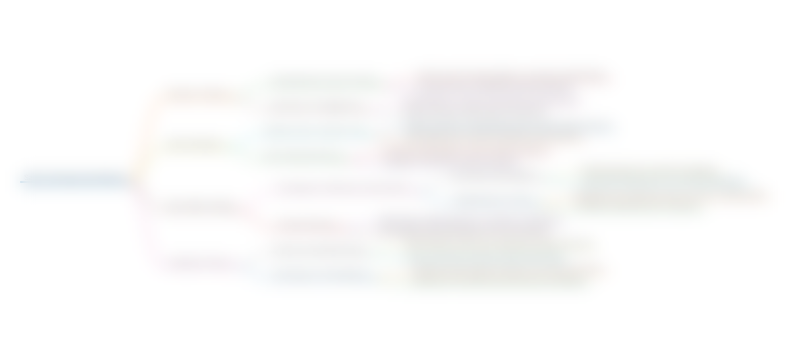
هذا القسم متوفر فقط للمشتركين. يرجى الترقية للوصول إلى هذه الميزة.
قم بالترقية الآنKeywords
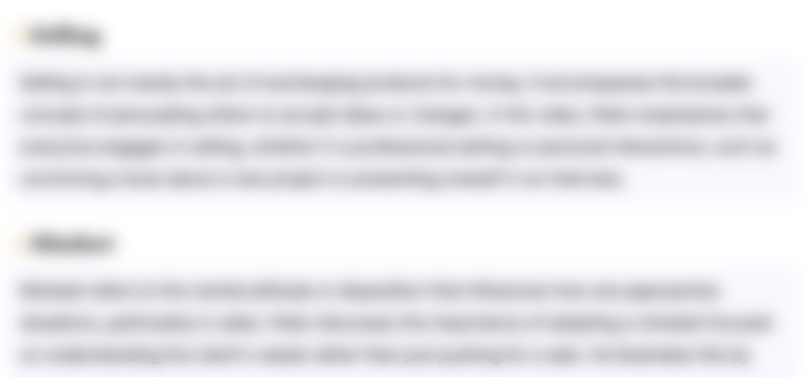
هذا القسم متوفر فقط للمشتركين. يرجى الترقية للوصول إلى هذه الميزة.
قم بالترقية الآنHighlights
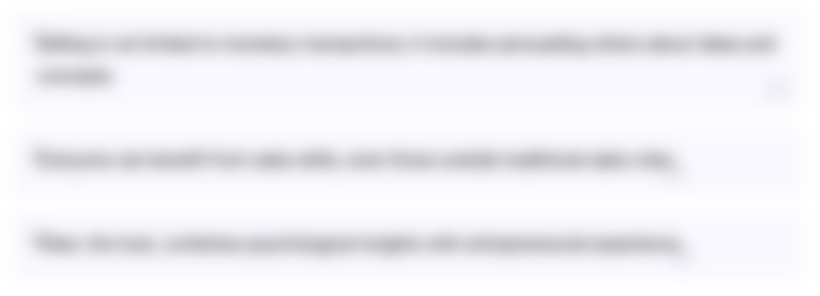
هذا القسم متوفر فقط للمشتركين. يرجى الترقية للوصول إلى هذه الميزة.
قم بالترقية الآنTranscripts
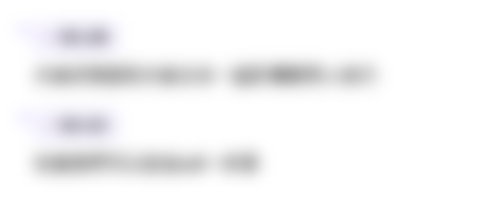
هذا القسم متوفر فقط للمشتركين. يرجى الترقية للوصول إلى هذه الميزة.
قم بالترقية الآنتصفح المزيد من مقاطع الفيديو ذات الصلة

Propriedades mecânicas
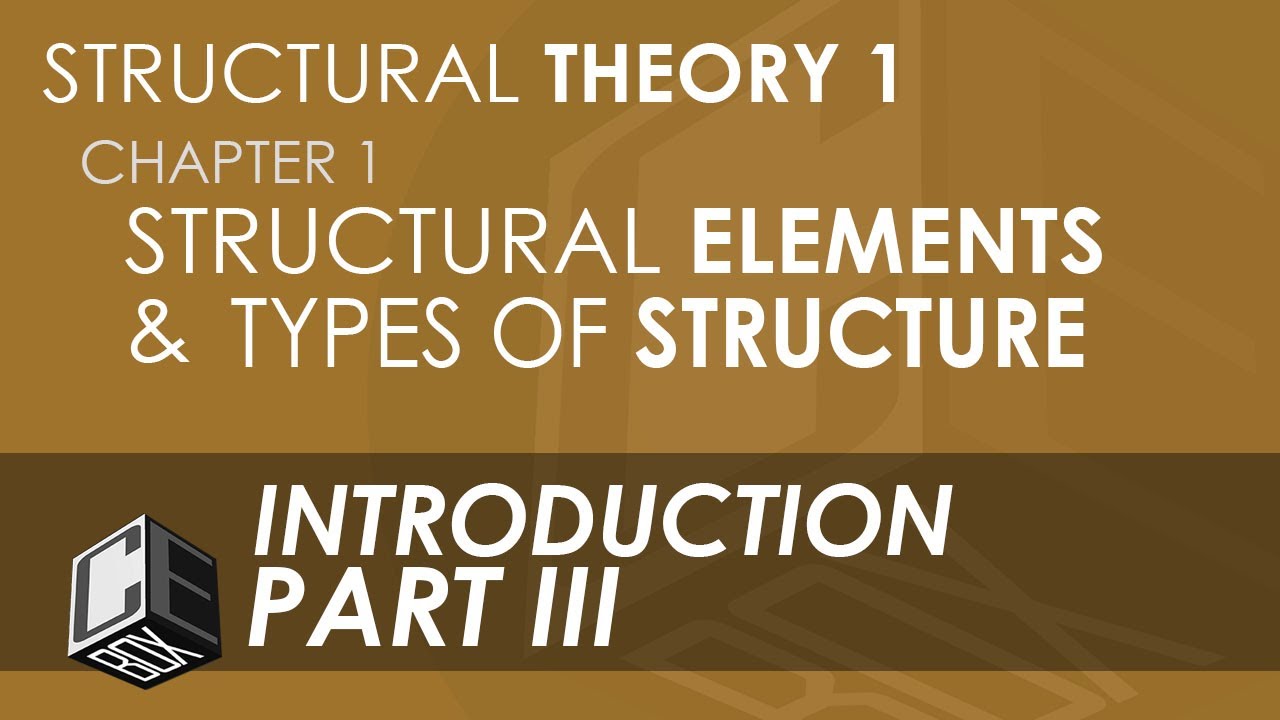
Structural Theory 1 Chapter 1 Part III (with Subtitles)

Structural Theory 1 Chapter 1 Structural Elements & Types of Structure Part 1 (with Subtitles)
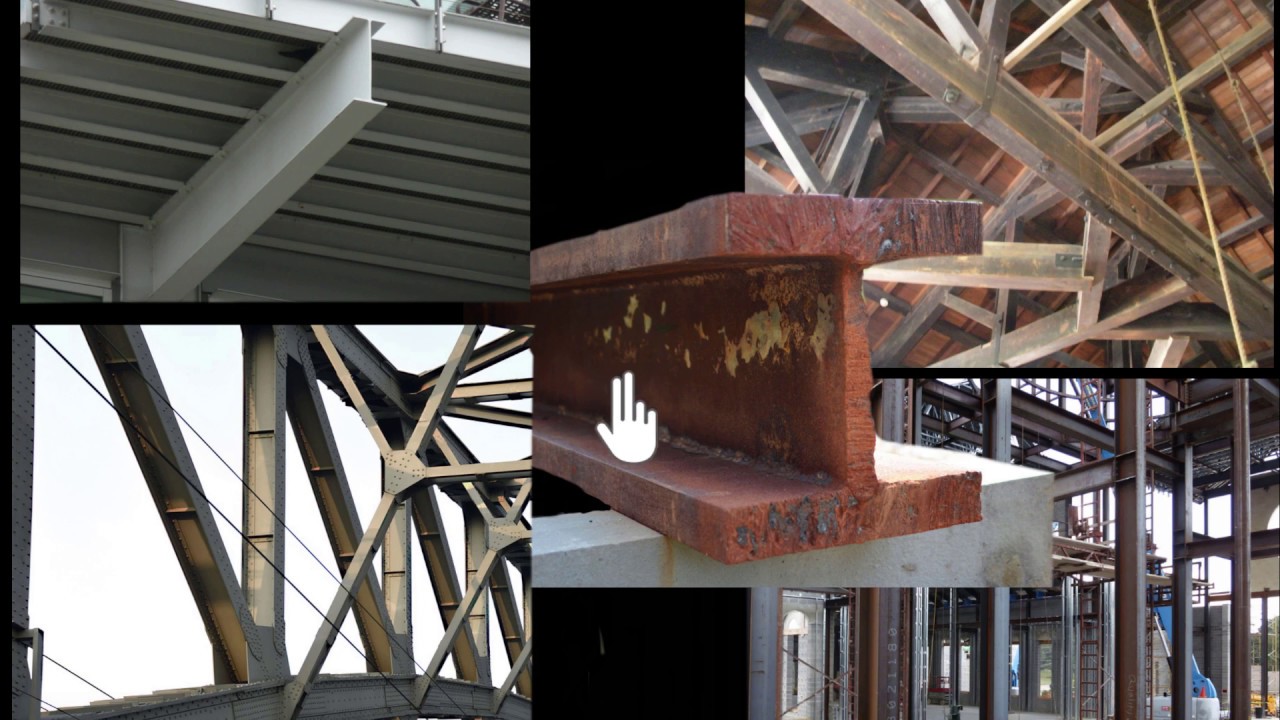
Why use I beams in construction? | Class 11 (India) | Physics | Khan Academy

Chapter 7 Transverse shear applications
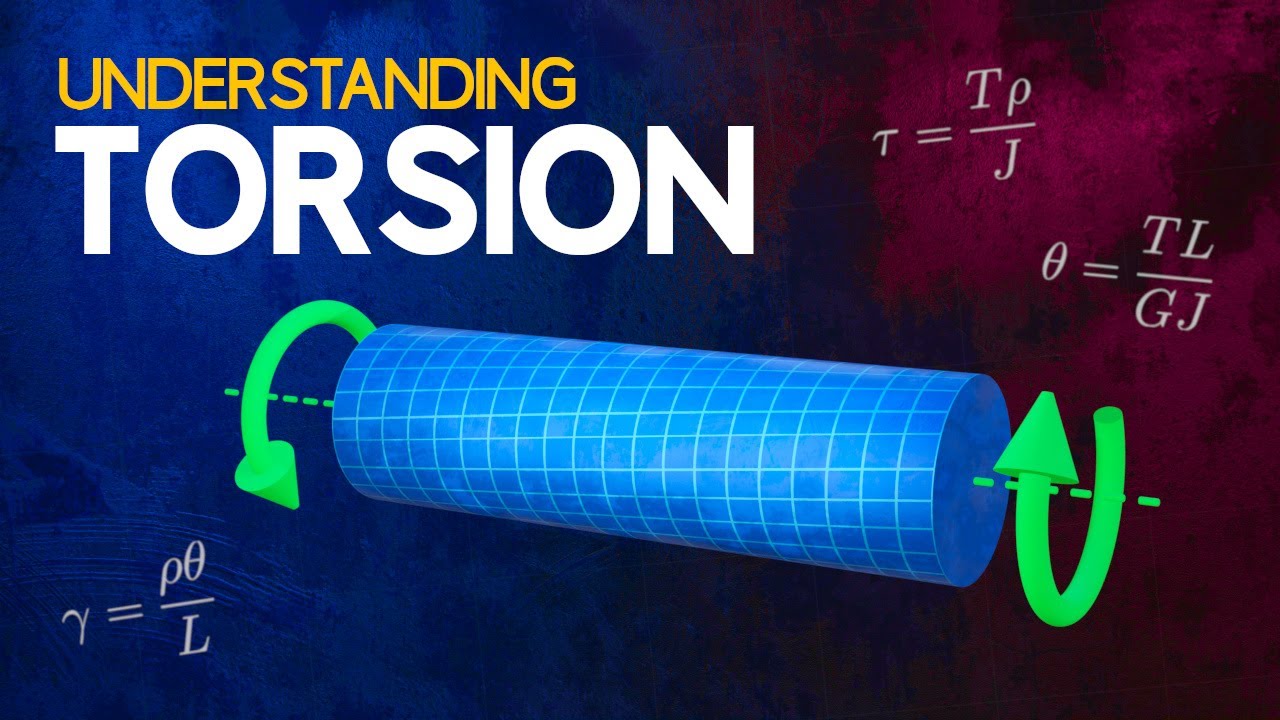
Understanding Torsion
5.0 / 5 (0 votes)