The Danger of Popcorn Polymer: Incident at the TPC Group Chemical Plant
Summary
TLDROn November 27, 2019, a catastrophic explosion at TPC Group's chemical plant in Port Neches, Texas, released flammable butadiene, causing extensive damage and injuries. The incident resulted from uncontrolled popcorn polymer formation in a 'dead leg' of piping, highlighting the need for better hazard recognition and control measures. The Chemical Safety Board's investigation identified key safety issues, including the lack of effective procedures to manage dead legs and popcorn polymer, and the absence of remotely operated emergency isolation valves, underscoring the importance of robust safety practices in the petrochemical industry.
Takeaways
- 🔥 On November 27, 2019, a catastrophic incident occurred at the TPC Group chemical plant in Port Neches, Texas, involving the release of highly flammable butadiene.
- 💥 The explosion was felt up to 30 miles away and resulted in significant damage to the facility, nearby homes, and businesses, as well as injuries to workers and the public.
- 🚨 The incident was caused by the accumulation of popcorn polymer, a known hazard, which was poorly managed and controlled within the facility.
- 🏭 TPC is a petrochemical manufacturing company that produces butadiene, a highly reactive chemical used in the production of synthetic rubber and other products.
- 🚧 The primary pump in the butadiene unit was shut down for maintenance, creating a 'dead leg' in the piping system, which allowed popcorn polymer to accumulate over 114 days.
- 🚨 The lack of proper procedures to identify and control dead legs in high-purity butadiene service contributed to the disaster.
- 🔍 The Chemical Safety Board (CSB) investigation identified four key safety issues: dead leg identification and control, process hazard analysis, action item implementation, and control and prevention of popcorn polymer.
- 📚 Existing industry guidance on managing popcorn polymer formation was found to be insufficient, leading to gaps in understanding and preventing such incidents.
- 🛠️ The CSB recommended that TPC develop and implement a process to identify and control or eliminate dead legs in high-purity butadiene service.
- 🚫 TPC failed to effectively control or prevent the buildup of popcorn polymer, despite experiencing its formation previously and conducting operational trials.
- 🛑 The lack of remotely operated emergency isolation valves in the butadiene process meant that the release could not be stopped quickly, exacerbating the incident's severity.
Q & A
What incident occurred at the TPC group chemical plant in Port Neches, Texas on November 27, 2019?
-A release of highly flammable butadiene led to a series of explosions that could be felt up to 30 miles away, causing the destruction of a portion of the TPC facility, damage to nearby homes and businesses, and mandatory evacuations within a four-mile radius.
What is butadiene and why is it significant in the TPC incident?
-Butadiene is a highly reactive chemical used as a building block in the production of various products, most commonly synthetic rubber. Its improper management can lead to serious hazards, such as the formation of popcorn polymer, which was a key factor in the TPC incident.
What is a 'dead leg' in the context of chemical plant operations?
-A 'dead leg' refers to an area of piping that is open to the process but does not have any material flowing through it. It can lead to the accumulation of substances like popcorn polymer, posing a significant hazard.
What happened on August 4th, 2019, that contributed to the TPC incident?
-A worker shut down a primary pump during a routine operation, which later failed to restart and was sent for repair. This created a significant dead leg, leading to the formation and accumulation of popcorn polymer over the next 114 days.
What was the immediate cause of the explosion at the TPC facility on November 27th?
-Excessive popcorn polymer buildup caused the dead leg piping to suddenly rupture, releasing approximately six thousand gallons of liquid butadiene, which vaporized and formed a flammable cloud that ignited, causing the explosion.
What were the four key safety issues identified by the Chemical Safety Board (CSB) in their investigation of the TPC incident?
-The four key safety issues were: 1) Dead leg identification and control, 2) Process Hazard Analysis (PHA) action item implementation, 3) Control and prevention of popcorn polymer, and 4) The use of remotely operated emergency isolation valves.
Why was the primary pump's repair initially prioritized but later changed to routine?
-The repair was initially prioritized due to its importance in the butadiene production process. However, the presence of a spare pump led to a reassessment, changing the urgency and allowing a dead leg to exist for an extended period.
What recommendation did the CSB make to TPC Group regarding dead legs in high purity butadiene service?
-The CSB recommended that TPC Group develop and implement a process to identify, control, or eliminate dead legs in high purity butadiene service to prevent similar incidents.
What was the status of the PHA recommendation from 2016 regarding equipment out of service for maintenance?
-The PHA recommendation from 2016, which suggested flushing lines monthly when equipment is out of service, was accepted by TPC management but was never implemented, contributing to the popcorn polymer buildup.
What steps did TPC take prior to the incident that may have contributed to the popcorn polymer formation?
-TPC began a series of operational trials in April 2019, which included removing a problematic piece of equipment and reducing the amount of popcorn polymer inhibitor in the production stream, leading to increased popcorn polymer formation.
What was the role of the American Chemistry Council's butadiene product stewardship guidance manual in the TPC incident?
-The manual provided general information on popcorn polymer but lacked specific guidance on the potential consequences of dead legs and how to identify, control, or prevent them, which the CSB believes could have helped prevent the incident.
What was the final outcome of the fires caused by the initial explosion at the TPC facility?
-The fires burned for over a month, and it was not until January 4th, 2020, that the TPC incident command confirmed all fires were finally out.
Outlines
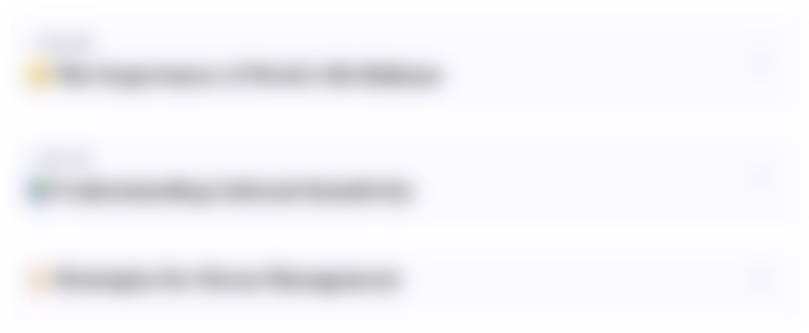
此内容仅限付费用户访问。 请升级后访问。
立即升级Mindmap
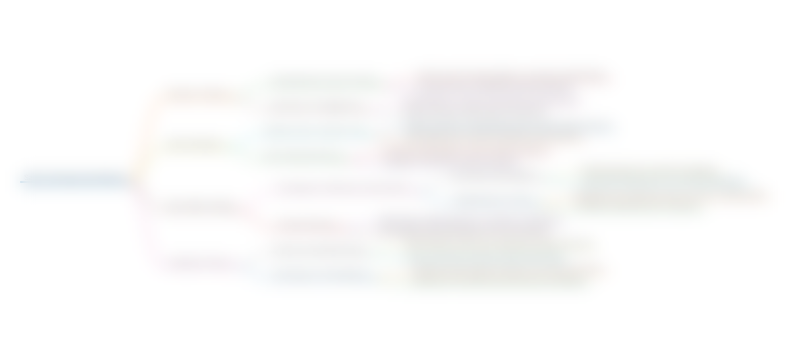
此内容仅限付费用户访问。 请升级后访问。
立即升级Keywords
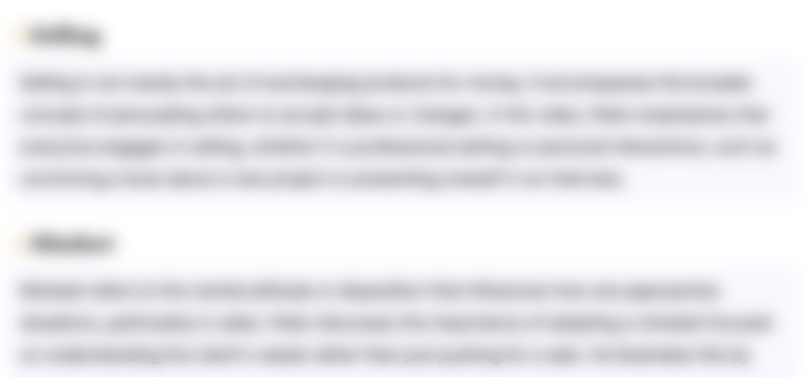
此内容仅限付费用户访问。 请升级后访问。
立即升级Highlights
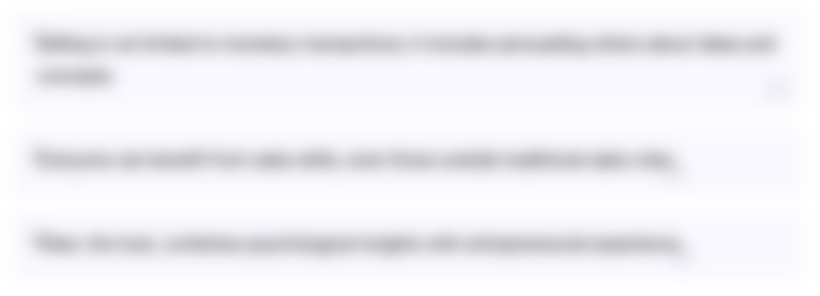
此内容仅限付费用户访问。 请升级后访问。
立即升级Transcripts
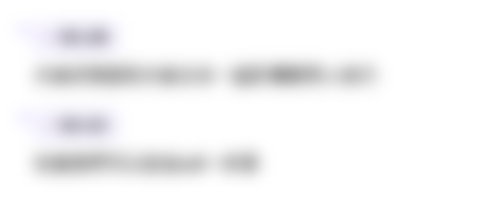
此内容仅限付费用户访问。 请升级后访问。
立即升级5.0 / 5 (0 votes)