Materiais e Processos de Fabricação para Engenharia de Produção - Processos de Laminação
Summary
TLDRThis video lecture dives into mechanical forming processes, focusing on lamination in material engineering. It covers the principles of plastic deformation, where metals are shaped without breaking, and the process of lamination, where metal is compressed between rotating cylinders. The video explains key concepts like cold and hot working, strain hardening, and the equations for lamination force, deformation, and power. Detailed calculations and examples demonstrate how sheet thickness and speed are adjusted during lamination, emphasizing material flow and mass conservation. The lecture also touches on lamination configurations, different types of rollers, and applications in primary and finishing lamination.
Takeaways
- 😀 Lamination is a mechanical forming process where metal is forced between two rotating cylinders, creating direct compression to reshape the material.
- 😀 Plastic deformation is key to lamination, where the material deforms permanently without breaking, as opposed to cutting or shearing.
- 😀 Hot and cold working are the two primary conditions for lamination, with hot working occurring above half the material's melting temperature and cold working below it.
- 😀 Cold working results in work hardening (encruamento), increasing material hardness as it is deformed.
- 😀 Lamination allows the creation of structural profiles, metal sheets, and bars from simpler metallic elements like ingots and billets.
- 😀 The reduction in material thickness during lamination is known as 'desbaste', which has a maximum limit determined by the radius of the cylinder and material properties.
- 😀 The force used during lamination is calculated using the formula involving the yield stress of the material, the width of the piece, and the contact arc between the rollers.
- 😀 True strain (deformação verdadeira) is calculated using the logarithmic relationship between the initial and final thickness of the material.
- 😀 The torque in the lamination process depends on the lamination force and the contact arc, and it can be calculated using the force and arc length.
- 😀 The principle of mass conservation is applied in lamination, ensuring that the volume of material entering the rollers equals the volume of material exiting, adjusting the width and speed accordingly.
- 😀 The lamination process involves different configurations of cylinders, including setups with multiple cylinders for better dimensional control and stability.
Q & A
What is the primary objective of mechanical deformation processes in production engineering?
-The primary objective is to permanently deform a material without it breaking, typically to achieve a desired final shape, using processes like lamination, which involve compressing the material between rotating rolls.
What is meant by plastic deformation in the context of material forming?
-Plastic deformation refers to the permanent change in the shape of a material when it is subjected to stress, such that the material does not return to its original shape once the stress is removed.
How does lamination differ from other forming processes like cutting or shearing?
-Unlike cutting or shearing, lamination is a forming process where the material is compressed between two rolls, and the focus is on shaping or reducing thickness without causing the material to break or fracture.
What are the key parameters involved in the lamination process?
-Key parameters include the force applied to the material, the speed of the rolls, the material's initial and final thickness, the radius of the rolls, and the arc of contact between the material and the rolls.
What is the difference between hot and cold lamination?
-Hot lamination occurs at temperatures above half of the material's melting point, whereas cold lamination occurs below that temperature, which can lead to work hardening (encruamento) of the material.
What is the phenomenon of encruamento, and how does it affect the material in cold lamination?
-Encruamento refers to the hardening of the material due to the strain applied during cold lamination, which increases the material's hardness and strength.
How is the reduction in material thickness calculated during lamination?
-The reduction in thickness (or 'desbaste') is the difference between the initial thickness (T0) and the final thickness (TF), and it can be calculated using the formula for reduction based on the radius of the rolls and the material being laminated.
What is the formula for calculating the force applied during lamination?
-The force is calculated using the formula: F = τ × W × L, where τ is the average flow stress, W is the width of the material, and L is the contact length between the rolls and the material.
How does the speed of the material change during lamination, and why?
-The speed of the material increases as the thickness decreases, due to the conservation of mass and material flow, meaning the volume entering and exiting the lamination process remains constant.
What are the components of a typical lamination setup, and what are their functions?
-A typical lamination setup includes the cage (gaiola) to support the rolls, the rolls themselves, which are the primary tools for compressing the material, and the supporting structure to hold the rolls and manage the force applied to the material during the process.
Outlines
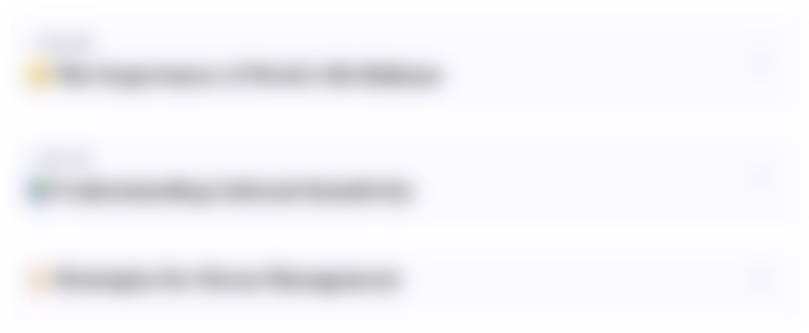
此内容仅限付费用户访问。 请升级后访问。
立即升级Mindmap
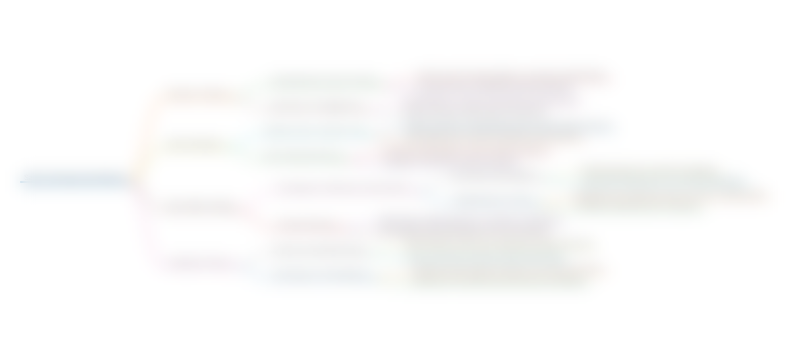
此内容仅限付费用户访问。 请升级后访问。
立即升级Keywords
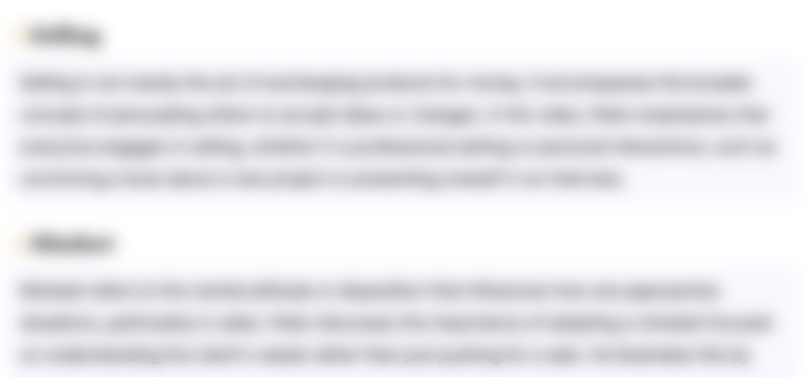
此内容仅限付费用户访问。 请升级后访问。
立即升级Highlights
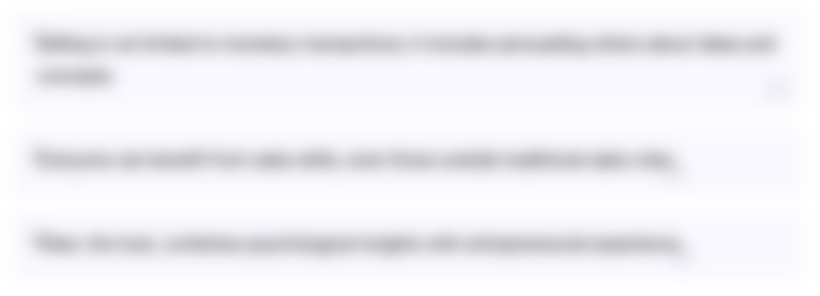
此内容仅限付费用户访问。 请升级后访问。
立即升级Transcripts
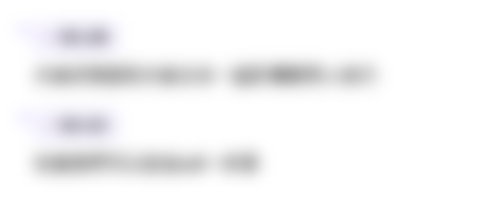
此内容仅限付费用户访问。 请升级后访问。
立即升级浏览更多相关视频
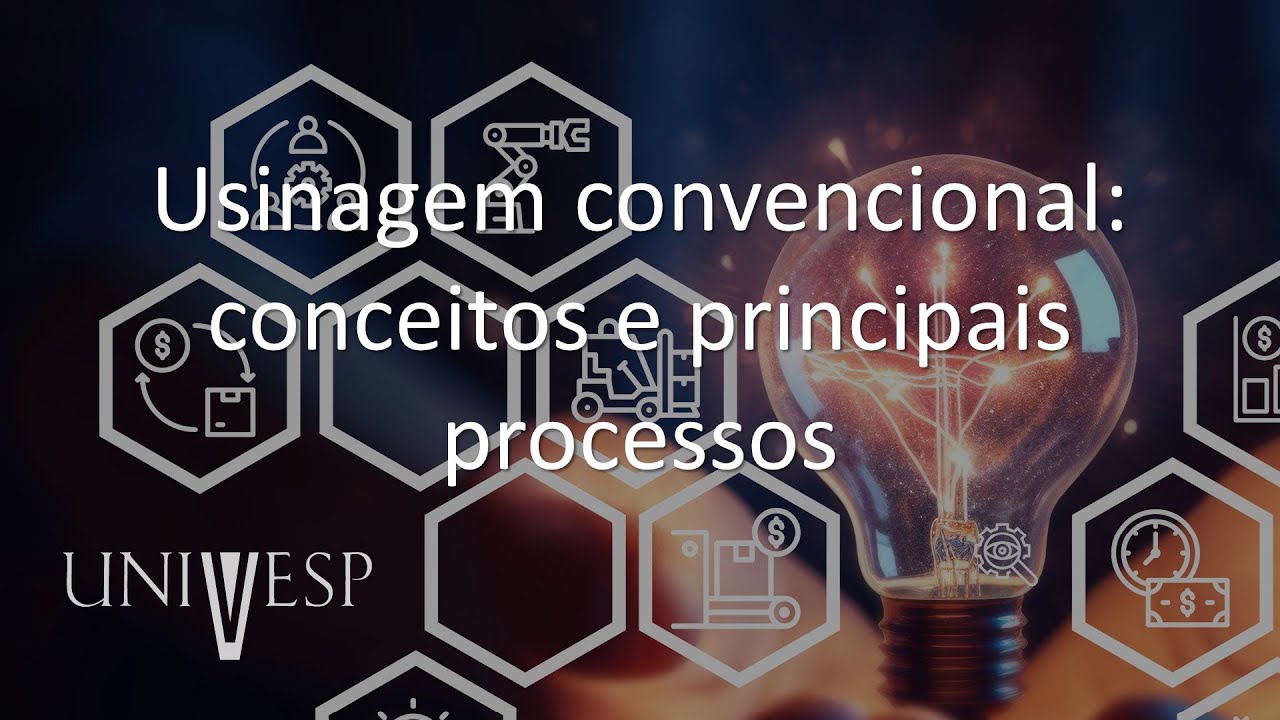
Materiais e Processos de Fabricação para Engenharia de Produção - Usinagem convencional: conceitos
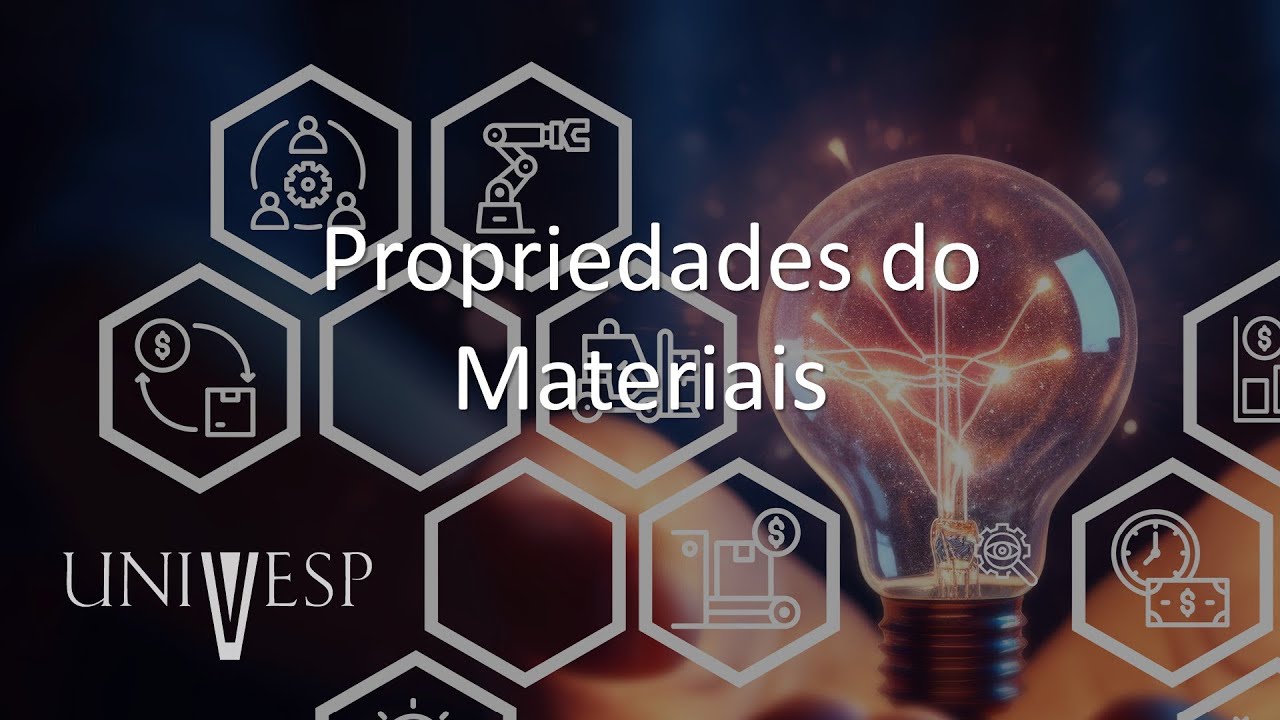
Materiais e Processos de Fabricação para Engenharia de Produção - Propriedades do Materiais

Introduction to spring and types of spring in Gujarati | DME | GTU
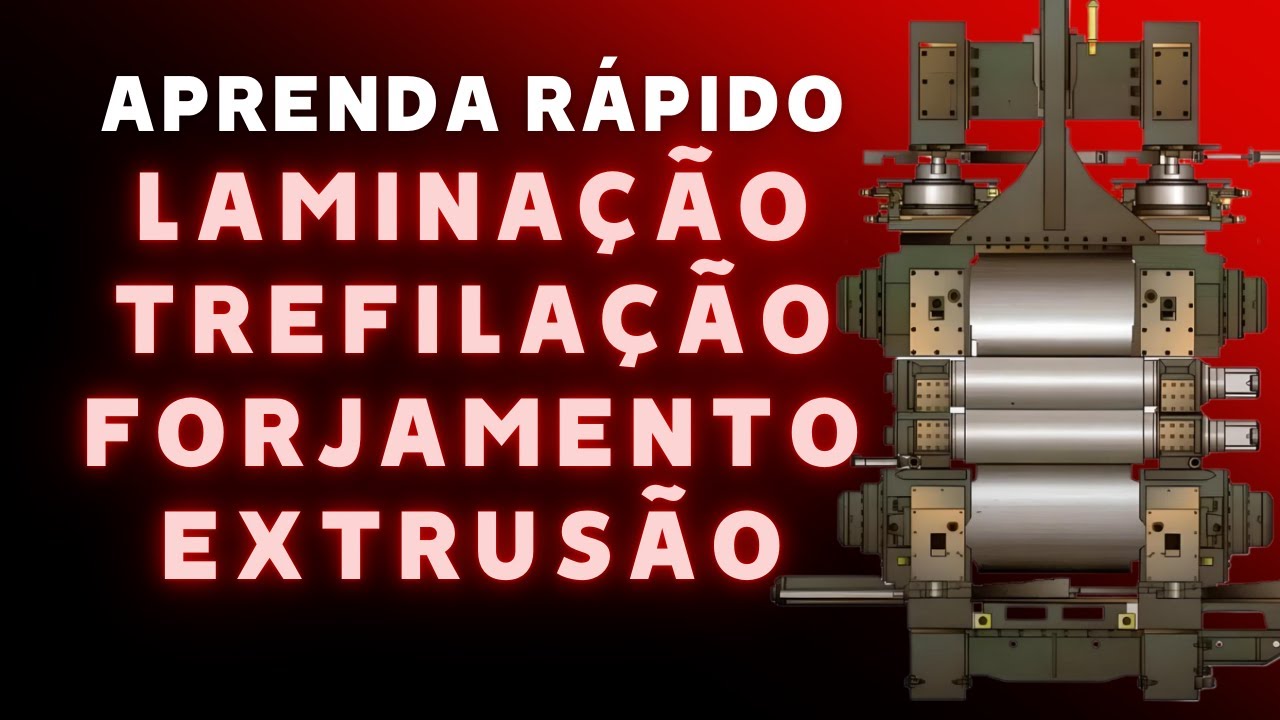
Aprenda os processos de CONFORMAÇÃO / FABRICAÇÃO - Laminação, trefilação, extrusão e forjamento

Telecurso 2000 - Processos de Fabricação - 07 E depois da fundição?
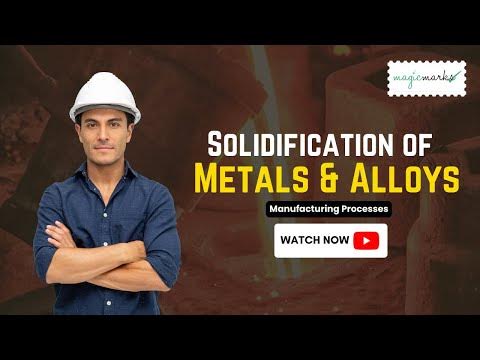
Explanation of Solidification of Metals & Alloys | Manufacturing Processes
5.0 / 5 (0 votes)