Perbedaan Quality Control dan Quality Assurance di Industri Pangan
Summary
TLDRThis video explains the differences between Quality Assurance (QA) and Quality Control (QC). QA focuses on process stability and prevention, aiming to prevent defects before they occur, while QC is reactive, concentrating on detecting and correcting product defects. The two concepts together form Quality Management (QM), ensuring the delivery of high-quality products. The video also touches on how QA ensures processes meet standards, and QC ensures that final products meet the required specifications. Ultimately, both work hand-in-hand to ensure the quality of products and services delivered to customers.
Takeaways
- 😀 Quality control (QC) and quality assurance (QA) are often confused, but they serve different purposes in managing product quality.
- 😀 Quality is defined as a measure of a characteristic that is either accepted or rejected by the end-user (consumer or buyer).
- 😀 A product or service's quality determines how well it meets the expectations and needs of the customer.
- 😀 The price of a product or service can be influenced by its quality, with better quality often justifying a higher price.
- 😀 Quality management encompasses both QA and QC, with these two areas working together to ensure high-quality products.
- 😀 Quality assurance focuses on the process, ensuring that procedures follow established standards (SOPs) without deviations.
- 😀 Quality control is more focused on the product itself, inspecting and ensuring the product meets specifications after production.
- 😀 QA is proactive, emphasizing preventive measures to avoid quality issues before they arise.
- 😀 QC is reactive, detecting and correcting product deviations after they occur.
- 😀 While QA aims for process improvement to reduce defects, QC focuses on inspecting products to fix issues and deliver a defect-free product to the customer.
- 😀 Both QA and QC ultimately aim to ensure that the final product is free from defects and acceptable to the customer, whether it's through process management or corrective actions.
Q & A
What is the main difference between Quality Control (QC) and Quality Assurance (QA)?
-The main difference is that Quality Control (QC) focuses on the product, ensuring it meets standards, while Quality Assurance (QA) focuses on the process, ensuring that it is stable and consistent according to set procedures.
How does Quality Control (QC) operate in terms of prevention vs. detection?
-Quality Control is more reactive and focuses on detecting deviations or defects in the product after they occur, and then taking corrective actions to fix them.
What role does Quality Assurance (QA) play in preventing defects?
-Quality Assurance is proactive, focusing on preventing defects by ensuring that processes are stable, adhering to standard operating procedures (SOPs), and preventing any issues before they occur.
What is the goal of Quality Management?
-The goal of Quality Management is to ensure that the products or services delivered to customers are defect-free and meet the expected quality standards, combining both Quality Assurance and Quality Control practices.
What is the focus of Quality Assurance (QA)?
-Quality Assurance focuses on ensuring that the process used to produce a product is reliable, stable, and free from errors. It emphasizes process control and continuous improvement.
How does Quality Control (QC) handle defects in a product?
-Quality Control handles defects by inspecting products, detecting any discrepancies or non-conformities, and implementing corrective measures to rectify the defects.
What kind of industries or products benefit from Quality Management practices?
-Quality Management practices benefit a wide range of industries, especially manufacturing, food production, and other sectors where product defects can affect safety, reliability, and customer satisfaction.
What is the relationship between Quality Assurance and Quality Control within Quality Management?
-Quality Assurance and Quality Control work together as components of Quality Management. QA ensures the process is stable and effective, while QC focuses on inspecting and correcting defects in the product itself.
Why is preventing defects preferred over detecting defects in a quality system?
-Preventing defects is preferred because it reduces the risk of non-conformities, saves time and costs, and ensures a more efficient and reliable production process, minimizing potential customer dissatisfaction.
What specific types of defects might be prevented in food production through Quality Management?
-In food production, Quality Management aims to prevent defects such as contamination from bacteria, physical contaminants, or chemical substances that may pose risks to consumer health and safety.
Outlines
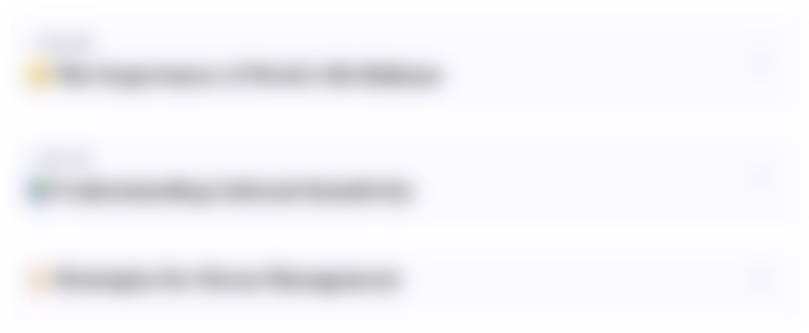
此内容仅限付费用户访问。 请升级后访问。
立即升级Mindmap
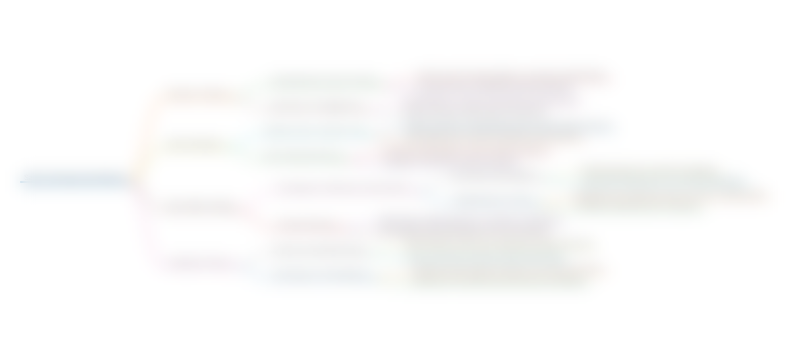
此内容仅限付费用户访问。 请升级后访问。
立即升级Keywords
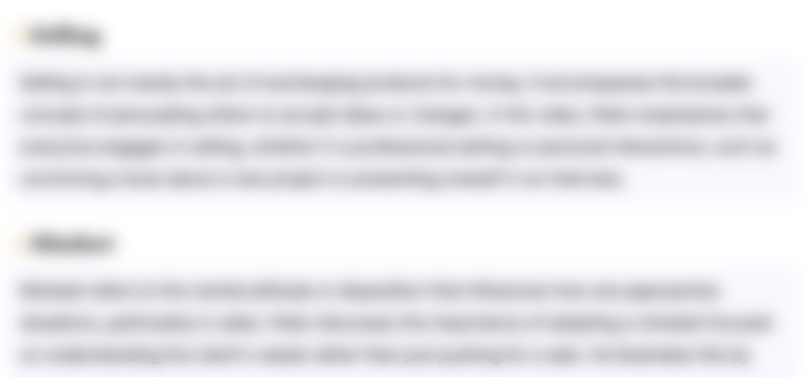
此内容仅限付费用户访问。 请升级后访问。
立即升级Highlights
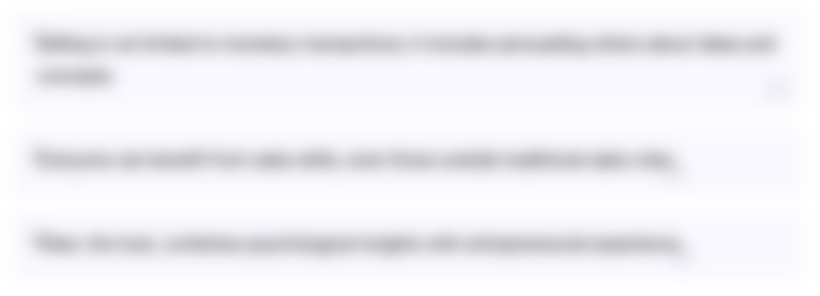
此内容仅限付费用户访问。 请升级后访问。
立即升级Transcripts
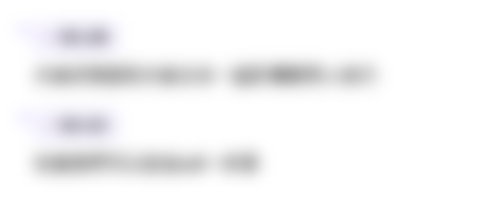
此内容仅限付费用户访问。 请升级后访问。
立即升级浏览更多相关视频

QA vs QC: Are You Making This Common Mistake?

QA vs. QC: Understanding the Key Difference
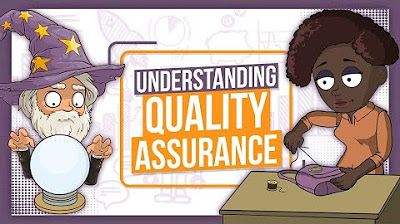
Understanding Quality Assurance - GCSE Business Studies Revision - OCR, Edexcel, AQA - BizzWizard

Ep. 2: Quality Management Systems, Quality Control and Quality Assurance | Kellerman Consulting
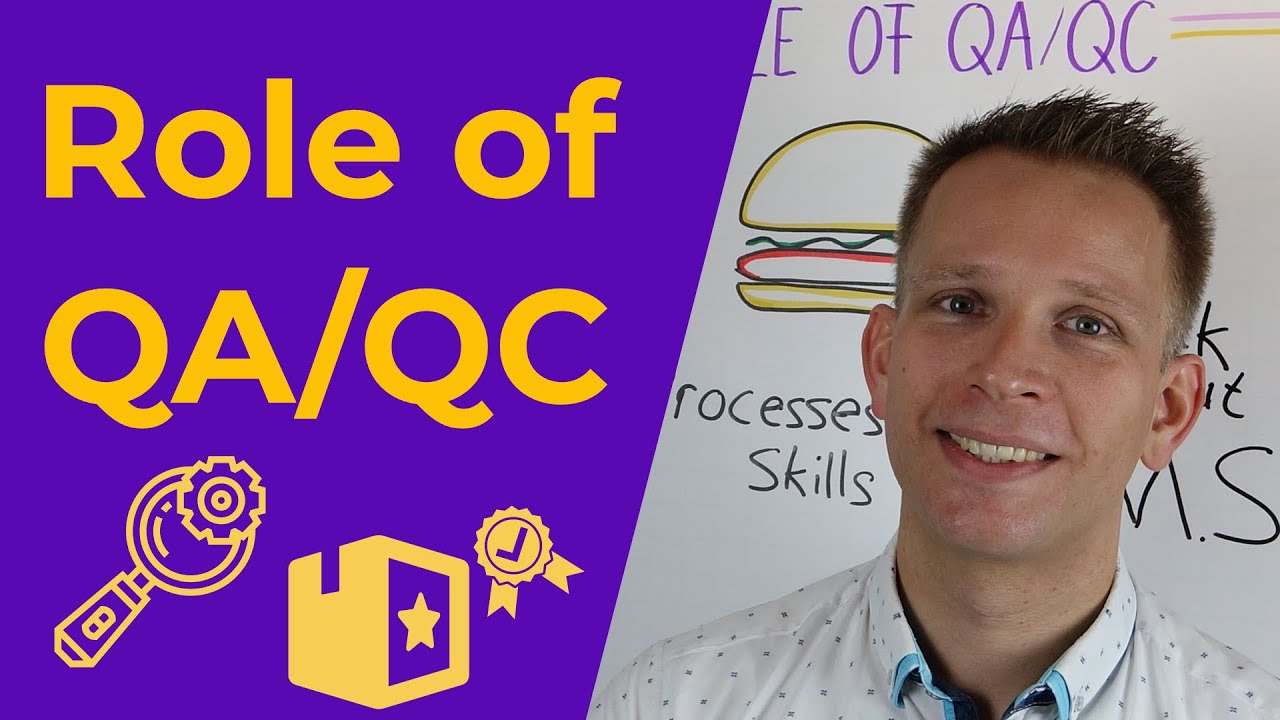
Role of QA and QC quality department functions
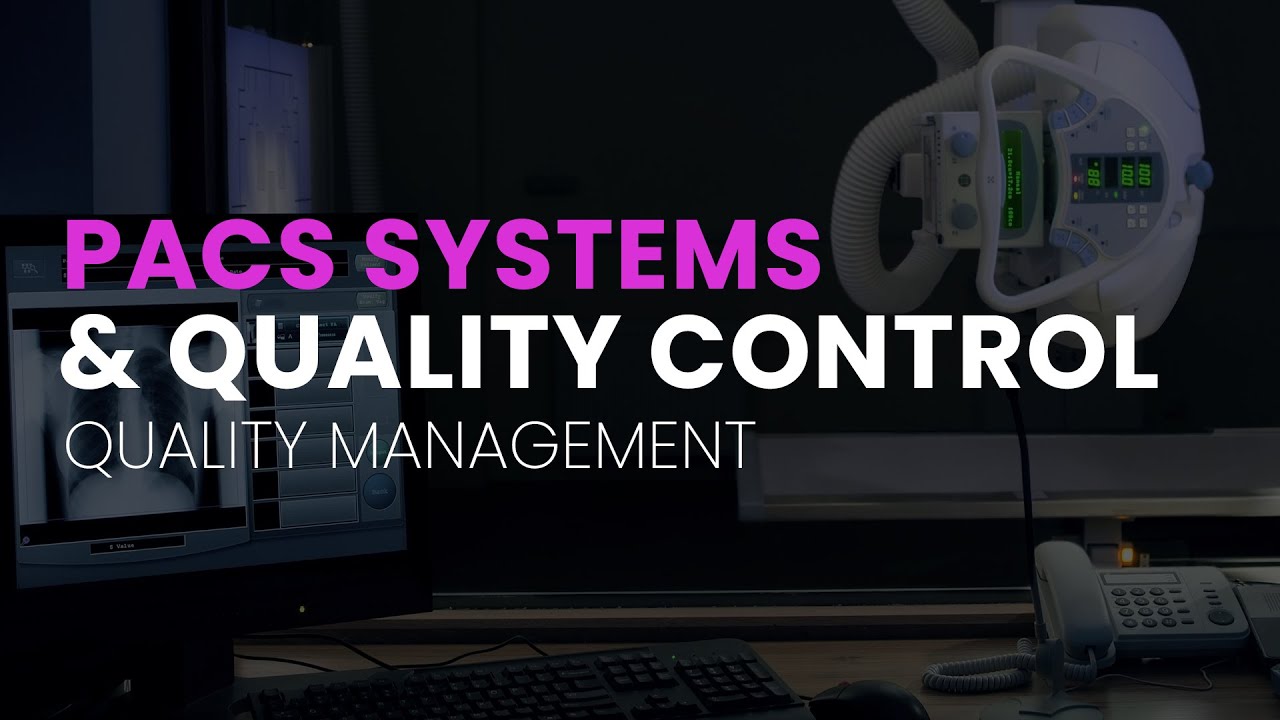
PACS Systems and Quality Control Part 3 - Quality Management
5.0 / 5 (0 votes)