✅ Qué son los CIRCULOS DE CALIDAD - ISO 9001
Summary
TLDRQuality Circles are a participative management tool where small groups of employees collaborate to identify and solve work-related problems, improving processes and product quality. Originating in Japan and China, these circles promote continuous improvement and employee engagement. They aim to enhance business performance by optimizing development, fostering teamwork, and boosting productivity. The success of Quality Circles relies on training, leadership, and consistent participation. However, challenges like lack of support, ineffective leadership, or poor teamwork can lead to failure. When implemented correctly, Quality Circles can significantly contribute to organizational success and employee growth.
Takeaways
- 😀 Quality circles involve employees in identifying and solving work-related issues to improve product quality, processes, and outcomes.
- 😀 These circles are small groups of employees from similar work functions who meet regularly to analyze and solve problems.
- 😀 The method originated in Japan and China and was first used to improve product quality and company reputation.
- 😀 Successful implementation of quality circles relies on employee participation, consistent meetings, and problem-solving using the PDCA (Plan, Do, Check, Act) cycle.
- 😀 Quality circles aim to create a proactive environment where employees can improve their work performance and the overall organization.
- 😀 They offer significant benefits such as improved product quality, increased employee productivity, and a more cohesive work environment.
- 😀 To form a quality circle, it is important that employees voluntarily participate and that their roles align with the issues being addressed.
- 😀 The success of quality circles is greatly influenced by leadership support and resource allocation to ensure effective participation.
- 😀 One of the main challenges is not properly training employees before they form quality circles, which may lead to confusion and lack of engagement.
- 😀 Quality circles should be integrated into the overall management system; if they operate in isolation, they are less effective.
- 😀 Key reasons for failure include lack of leadership, poor teamwork, and a lack of support from management, which can hinder the group's motivation and effectiveness.
Q & A
What are quality circles?
-Quality circles are small, organized groups of employees who meet regularly to identify, analyze, and solve work-related problems to improve processes, product quality, and overall performance.
How do quality circles contribute to continuous improvement?
-Quality circles follow the 'Plan-Do-Check-Act' cycle, which promotes ongoing evaluation and refinement of work processes. This helps employees consistently identify and address issues to improve efficiency and quality.
Why were quality circles initially adopted by Japan and China?
-Quality circles were introduced in Japan and China to improve the reputation of their products, which were initially considered low quality. The approach aimed to enhance product standards and reduce defects.
What are the key objectives of implementing quality circles in a company?
-The main objectives of quality circles are to optimize business development, create a healthier work environment, improve product quality, foster employee potential, and strengthen organizational image.
What benefits can businesses gain from quality circles?
-Benefits include improved product quality, increased employee productivity, better teamwork, and more effective management of workplace challenges, all of which contribute to better overall business performance.
How do quality circles affect employee engagement?
-Quality circles promote employee involvement by allowing them to take ownership of problems and solutions within their roles. This boosts engagement, as employees feel their input is valued in driving organizational improvements.
How should quality circles be structured for optimal effectiveness?
-Quality circles should consist of 5-10 voluntary members, all of whom perform similar tasks or work in the same area. Regular meetings are crucial to ensure continuous problem-solving and team collaboration.
What are the main factors that can lead to the failure of quality circles?
-Key factors that can cause failure include inadequate training, lack of integration with the company's overall management system, poor leadership, and a lack of teamwork or cooperation among members.
Why is leadership important in the success of quality circles?
-Effective leadership ensures that quality circles are well-coordinated, with regular meetings, proper training, and clear goal setting. Leaders motivate and guide the team toward achieving the objectives of the circle.
What role does employee expertise play in the success of quality circles?
-Employee expertise is crucial because each member of the circle is familiar with the specific challenges of their role. This expertise allows them to offer relevant solutions, prioritize issues, and drive improvements based on firsthand knowledge.
Outlines
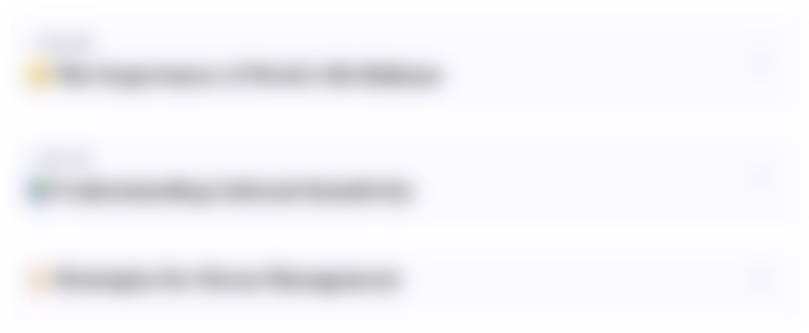
此内容仅限付费用户访问。 请升级后访问。
立即升级Mindmap
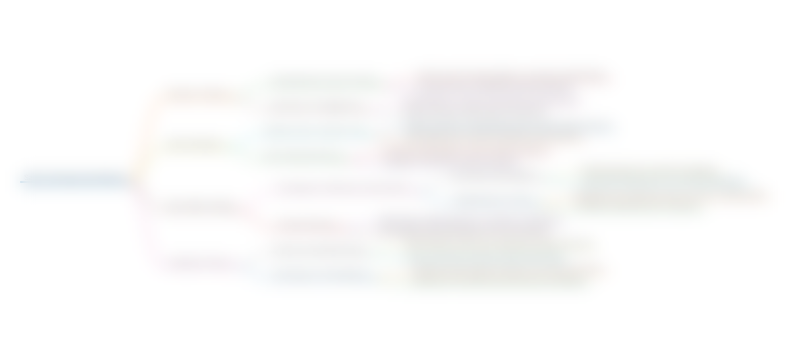
此内容仅限付费用户访问。 请升级后访问。
立即升级Keywords
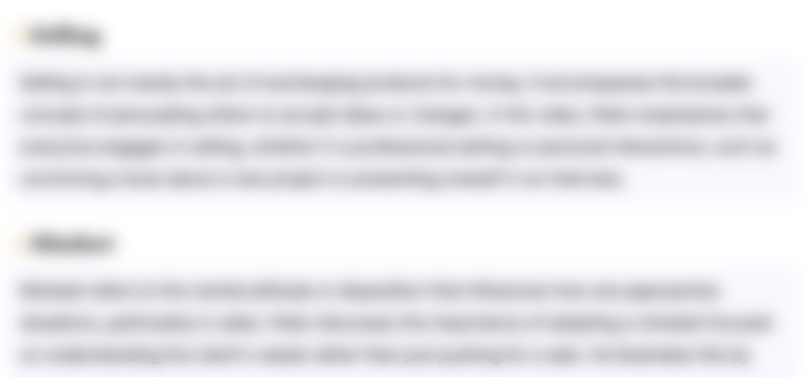
此内容仅限付费用户访问。 请升级后访问。
立即升级Highlights
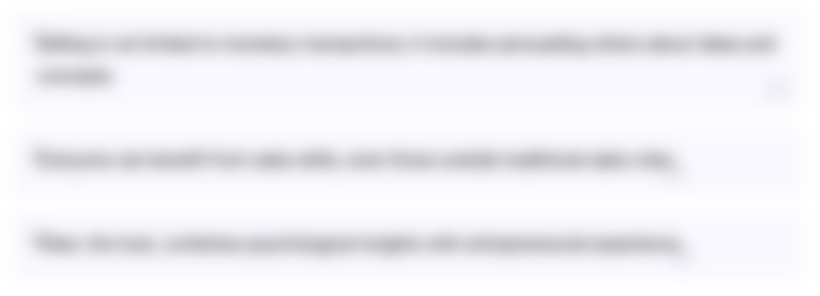
此内容仅限付费用户访问。 请升级后访问。
立即升级Transcripts
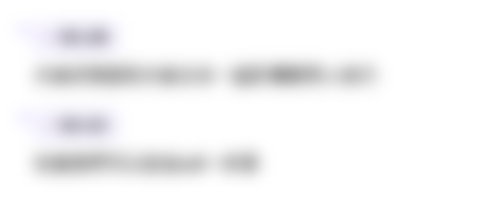
此内容仅限付费用户访问。 请升级后访问。
立即升级5.0 / 5 (0 votes)