I Built the Red Hood Bulletproof Armored Suit (And YOU can too)
Summary
TLDRIn this detailed tutorial, the creator demonstrates how to make a bullet-resistant Red Hood chest plate using a fiberglass and nanoparticle epoxy infusion. The process includes crafting a 3D printed mold, applying multiple layers of fiberglass with alternating weaves for strength, and using vacuum bagging to ensure a smooth, durable finish. The plate is tested against 9mm and 10mm rounds, showing excellent resistance with only minor deformation. This video provides both an educational and hands-on guide to creating cosplay armor with enhanced ballistic properties.
Takeaways
- 😀 The video demonstrates the process of making a bullet-resistant molded Red Hood chest plate using nanoparticle-infused epoxy and fiberglass.
- 😀 The new chest plate design is lighter (2.4 lbs) and thinner than previous models, making it more affordable and repeatable while still being effective at stopping 9mm rounds.
- 😀 Fiberglass is preferred over Kevlar for creating ballistic backer panels due to its stability, availability, and superior strength when combined with epoxy.
- 😀 The process involves using a 3D printed mold to create the chest plate and applying multiple layers of fiberglass with alternating weave orientations (90° and 45°) for strength.
- 😀 Proper mold release is achieved with PVA wax and a heat gun or hair dryer to ensure smooth separation of the mold from the fiberglass once it hardens.
- 😀 Epoxy degassing is crucial for nanoparticle-infused resin to prevent bubbles from compromising the material's strength during curing.
- 😀 A vacuum bagging process is used to apply pressure to the mold and ensure uniform epoxy saturation, minimizing air pockets and increasing the strength of the final plate.
- 😀 The plate's design and structure are optimized by layering different weaves of fiberglass and using fillers, though the testing and optimization process is complex and involves trial and error.
- 😀 When creating the plate, experts recommend carefully monitoring epoxy mixing and laying up fiberglass layers in a controlled manner to avoid introducing bubbles and ensure full resin saturation.
- 😀 After curing for 24 hours, the final product is removed from the mold, trimmed, and polished using tools like a Dremel and multi-tool to achieve a clean, smooth finish.
- 😀 The video includes testing of the finished plate with multiple rounds of 9mm ammunition to demonstrate its ability to stop bullets, though a 10mm round eventually penetrates the armor, proving its limits.
Q & A
What is the main difference between the bullet-resistant chest plate being made in this video and the one shown in previous videos?
-The new chest plate is made using a nanoparticle infill, making it thinner, lighter, and more bullet-resistant compared to the older version. It weighs just under 3 lbs, whereas the older version weighed 2.4 lbs.
Why is fiberglass preferred over Kevlar for this project?
-Fiberglass is preferred because it offers better stability and is more available. Kevlar doesn't perform as well when used with epoxy due to the fibers not being able to deflect, leading to more delamination. Fiberglass provides stronger backer panels in comparison.
What role does Kevlar play in the construction of the chest plate?
-Kevlar is used in soft layers draped in front of the fiberglass backer. It helps the bullet 'ball up' on the surface as it tries to break through the hard fiberglass, offering additional resistance without compromising the structure.
How can viewers replicate the 3D printed mold for this chest plate?
-The mold design file is available on the creator’s Patreon. Viewers can download it and scale it according to their needs if they want a larger or smaller plate.
What is the purpose of PVA wax in this project?
-PVA wax is used as a mold release agent. It ensures that the resin does not stick to the 3D printed mold, making it easier to separate the finished plate from the mold.
Why is degassing the epoxy important when making this chest plate?
-Degassing is important because it removes air bubbles introduced during the mixing process. Air bubbles weaken the epoxy, and degassing ensures a cleaner, stronger resin base for the panel.
How does the vacuum bagging process contribute to the creation of the chest plate?
-Vacuum bagging helps to remove excess air and ensure that the fiberglass is fully saturated with epoxy. The pressure from the vacuum bag compresses the layers, removing any voids and ensuring a uniform resin distribution.
What is the significance of alternating the direction of the fiberglass weave in the chest plate construction?
-Alternating the direction of the fiberglass weave increases the panel's strength. The fibers' different orientations help distribute tensile forces more effectively, making the armor stronger against impacts.
Why is the epoxy mixed in small batches, and what is the risk of not doing so?
-Epoxy is mixed in small batches because it undergoes an exothermic reaction, meaning it heats up as it cures. Larger batches can accelerate this process, leading to thermal runaway, which can cause the epoxy to harden too quickly and become difficult to work with.
What testing is done to ensure the chest plate's effectiveness against bullets?
-The chest plate is tested by shooting it with multiple rounds of Full Metal Jacket 9mm ammunition and a 10mm round. The plate successfully stops the 9mm rounds with minimal backface deformation but fails when hit with the 10mm round.
Outlines
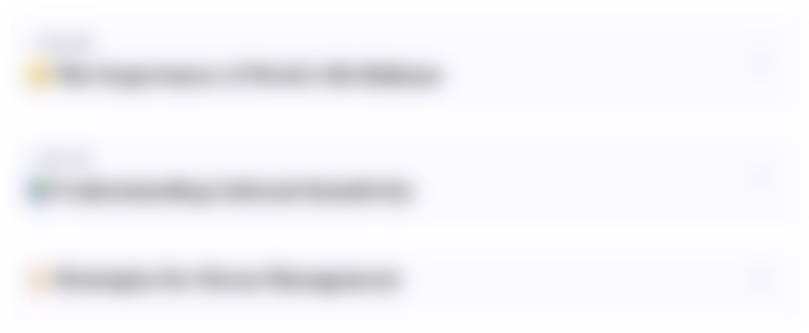
此内容仅限付费用户访问。 请升级后访问。
立即升级Mindmap
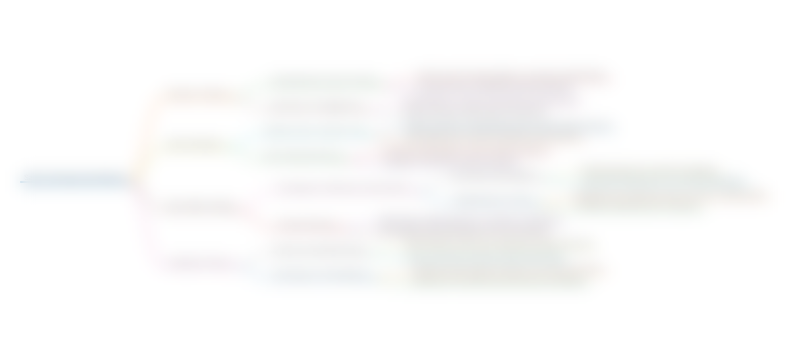
此内容仅限付费用户访问。 请升级后访问。
立即升级Keywords
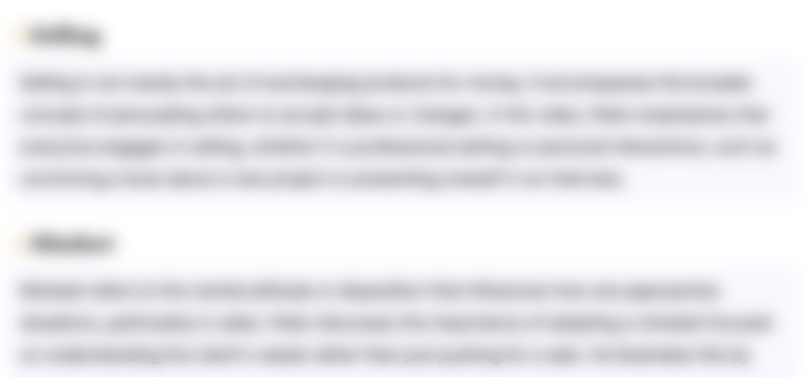
此内容仅限付费用户访问。 请升级后访问。
立即升级Highlights
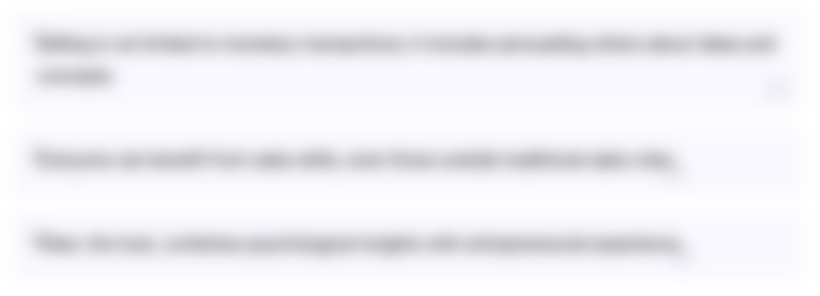
此内容仅限付费用户访问。 请升级后访问。
立即升级Transcripts
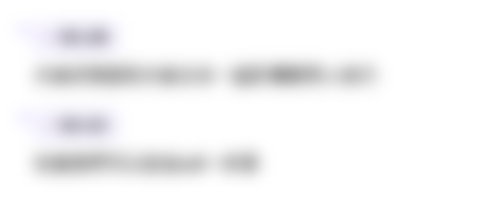
此内容仅限付费用户访问。 请升级后访问。
立即升级浏览更多相关视频
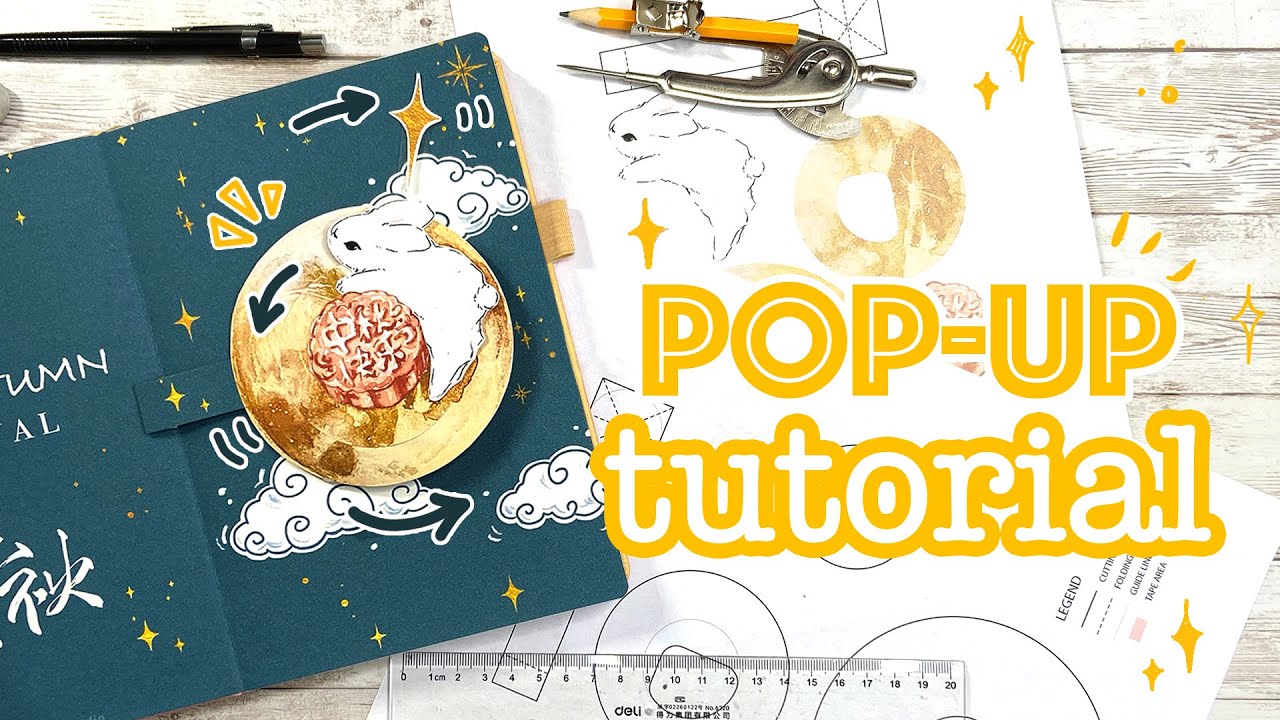
POP-UP tutorial | 3-layer Rotation Bunny on The Moon | OCT Mid-Autumn Theme Bullet Journal Coverpage

Fluffige Baguettes - Ich habe sie perfektioniert

Cara Membuat Batik Jumputan Teknik Shibori Motif Zigzag || Batik Ikat Celup || SBDP Kelas 5 Tema 9

How to Make Fiberglass Parts with the Bare Minimum Tools.

Cara Membuat Strawberry pudding Slime Mudah!! | Tutorial Slime

IDE KREATIF TAS TERBARU DARI BUNGKUS MIE SEDAAP
5.0 / 5 (0 votes)