Dicas de transformação #9 Fechamento das injetoras
Summary
TLDRThis video tutorial explains how to configure the closing system of injection molding machines. It covers different types of closing systems, including hydraulic mechanical, hydraulic, and two-plate systems, and emphasizes the importance of adjusting parameters such as speed, pressure, course, and time. The tutorial demonstrates how to access and modify these settings via the machine’s control panel to ensure efficient operation and mold protection. Additionally, it highlights the use of real-time monitoring tools like the 'lupinha' function to track mold position and adjust parameters accordingly. The video provides essential insights for optimizing machine performance and preventing mold damage.
Takeaways
- 😀 Hydraulic and mechanical systems are the most commonly used for closing injection molding machines, offering benefits like speed, energy efficiency, and reliability.
- 😀 The dual-plate system is a more modern solution, using smaller pistons to reduce space and energy consumption while maintaining efficient mold locking.
- 😀 Mold protection is essential during the mold closing process, helping to avoid damage by carefully controlling speed, pressure, stroke, and timing.
- 😀 Proper mold closing involves a variable parameter approach, allowing adjustment of speed, pressure, and stroke, rather than following a rigid, fixed rule.
- 😀 In the mold closing process, the machine initially closes quickly, but once the mold is close to fully locked, the machine transitions to a slower speed to protect the mold.
- 😀 Machine panels, like the one demonstrated in the video, provide easy-to-use interfaces for adjusting parameters like speed, pressure, and stroke in real-time.
- 😀 Parameters such as pressure, speed, and stroke are adjustable for both closing and opening, which allows fine-tuning of machine performance to avoid alarms and errors.
- 😀 Monitoring mold position with a 'magnifying glass' tool on the machine panel allows users to adjust parameters precisely for correct mold locking and protection.
- 😀 The mold protection setting can be fine-tuned by adjusting the time it takes for the mold to reach its closing position, typically a balance between 0.64 seconds and 5 seconds.
- 😀 The machine's speed and pressure values are variable and can be scaled during the closing and opening phases to ensure smooth operation without mold damage.
- 😀 Understanding how to adjust the mold protection and closing parameters on the panel can directly impact factory operations, reducing errors and improving efficiency.
Q & A
What is the main focus of the video tutorial?
-The video tutorial focuses on how to parametrize the closing system of injection molding machines, covering parameters like speed, pressure, stroke, and mold protection.
What are the three types of closing systems discussed in the video?
-The video discusses three types of closing systems: 1) Mechanical Hydraulic Closing, 2) Hydraulic Closing System, and 3) Dual Plate System.
Why is the mechanical hydraulic closing system commonly used in factories?
-The mechanical hydraulic closing system is commonly used because it offers good speed, energy efficiency, and is one of the most familiar systems in factory settings.
How does the hydraulic closing system operate to control the mold's height?
-In the hydraulic closing system, the mold's height is controlled by the stroke of the hydraulic piston, which moves the mold into position.
What is the primary function of the mold protection system?
-The mold protection system ensures that the mold is not damaged during the closing and opening process by regulating speed and pressure to avoid impact forces.
How can the closing system's parameters be adjusted?
-The closing system's parameters—such as speed, pressure, and stroke—can be adjusted through the machine's control panel, where users can select desired settings using a touch interface.
What role does the 'lupinha' (magnifying glass) icon play in the control panel?
-The 'lupinha' (magnifying glass) icon is used to monitor the mold's position during the closing process, helping the user identify when the mold has reached the necessary position for locking in place.
How does the system ensure that the mold is closed properly without causing damage?
-The system ensures safe mold closure by starting with a fast approach, then decelerating as it reaches the critical positions, with pressure adjustments applied to avoid damaging the mold during final closure.
What happens if the mold does not reach the set position in the allotted time?
-If the mold does not reach the set position within the allotted time (e.g., 5 seconds), the system triggers an alarm and automatically opens to prevent damage.
What parameters can be adjusted for the extraction (extrator) process, and how are they monitored?
-The extraction process parameters, such as speed, pressure, and stroke, can be adjusted similarly to the closing process. The 'lupinha' icon is also used to monitor the extrator's position and ensure it achieves the desired result.
What additional content is promised in the future video tutorials?
-The future video tutorials will focus on parametrizing the injection system, including detailed instructions on accessing and understanding the injection system's settings and parameters.
Outlines
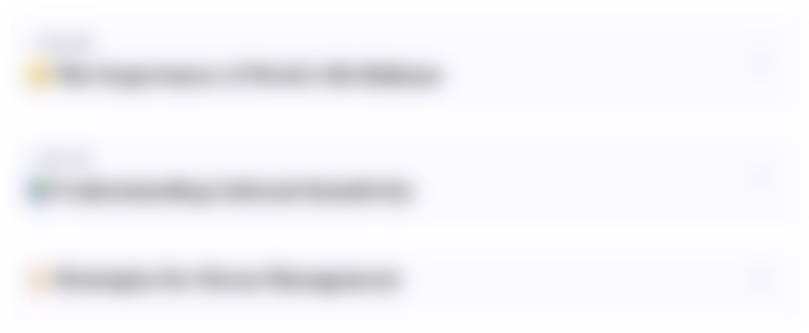
此内容仅限付费用户访问。 请升级后访问。
立即升级Mindmap
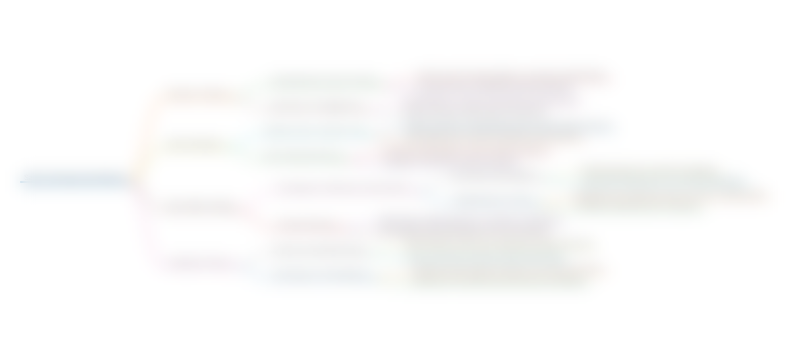
此内容仅限付费用户访问。 请升级后访问。
立即升级Keywords
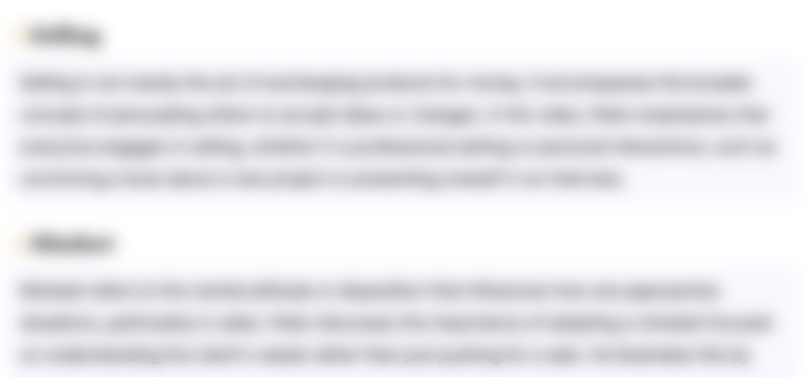
此内容仅限付费用户访问。 请升级后访问。
立即升级Highlights
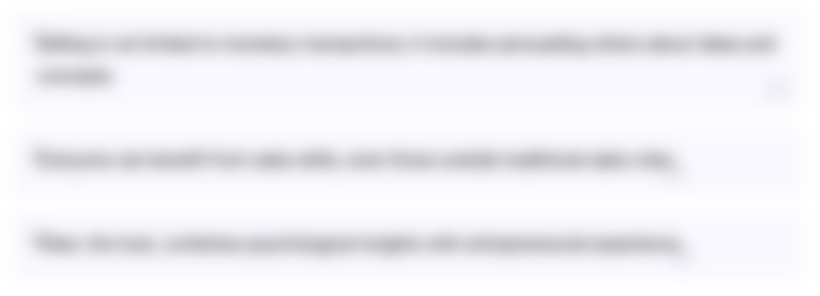
此内容仅限付费用户访问。 请升级后访问。
立即升级Transcripts
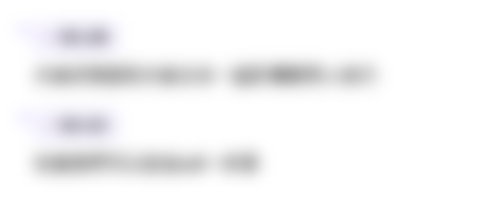
此内容仅限付费用户访问。 请升级后访问。
立即升级浏览更多相关视频
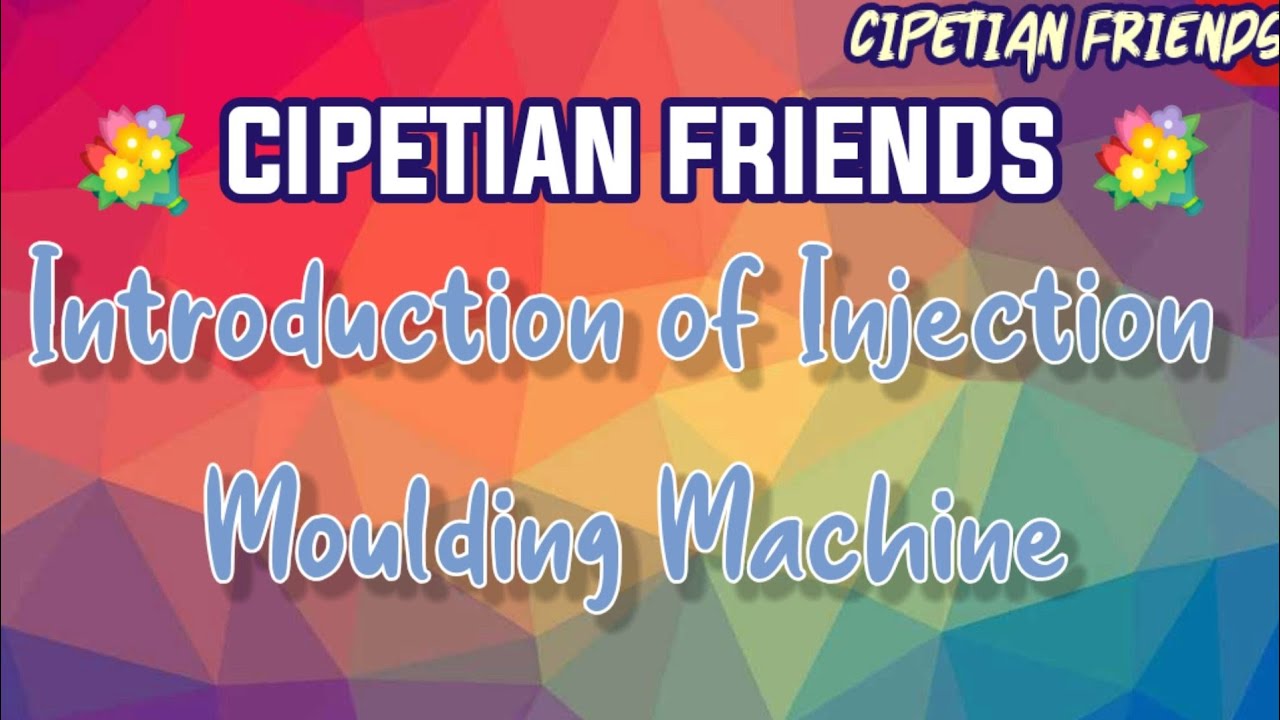
Introduction Of Injection Moulding Machine

Colchão: o que é, para que serve, quando usar e como calcular!

Cara Mengoperasikan Mesin Injection Molding #polibatam #LabInjectionmolding
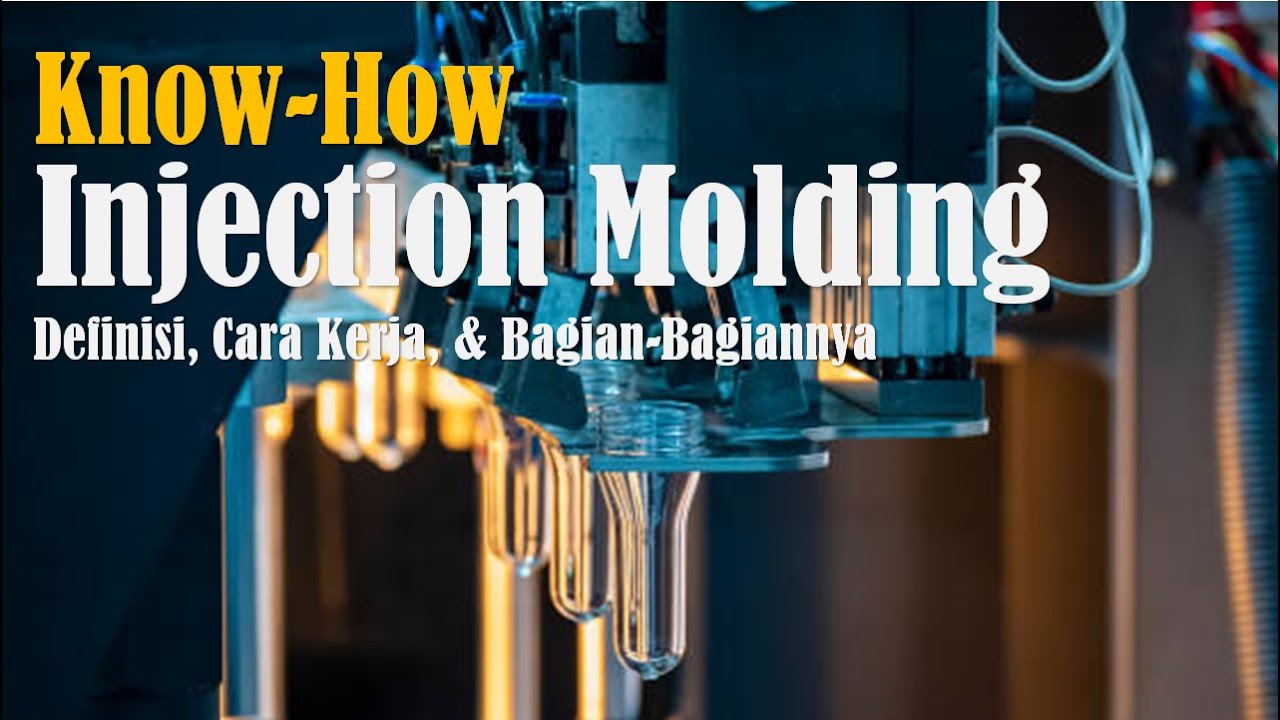
INJECTION MOLDING - DEFINISI, CARA KERJA, DAN BAGIAN-BAGIAN MESIN INJECTION MOLDING
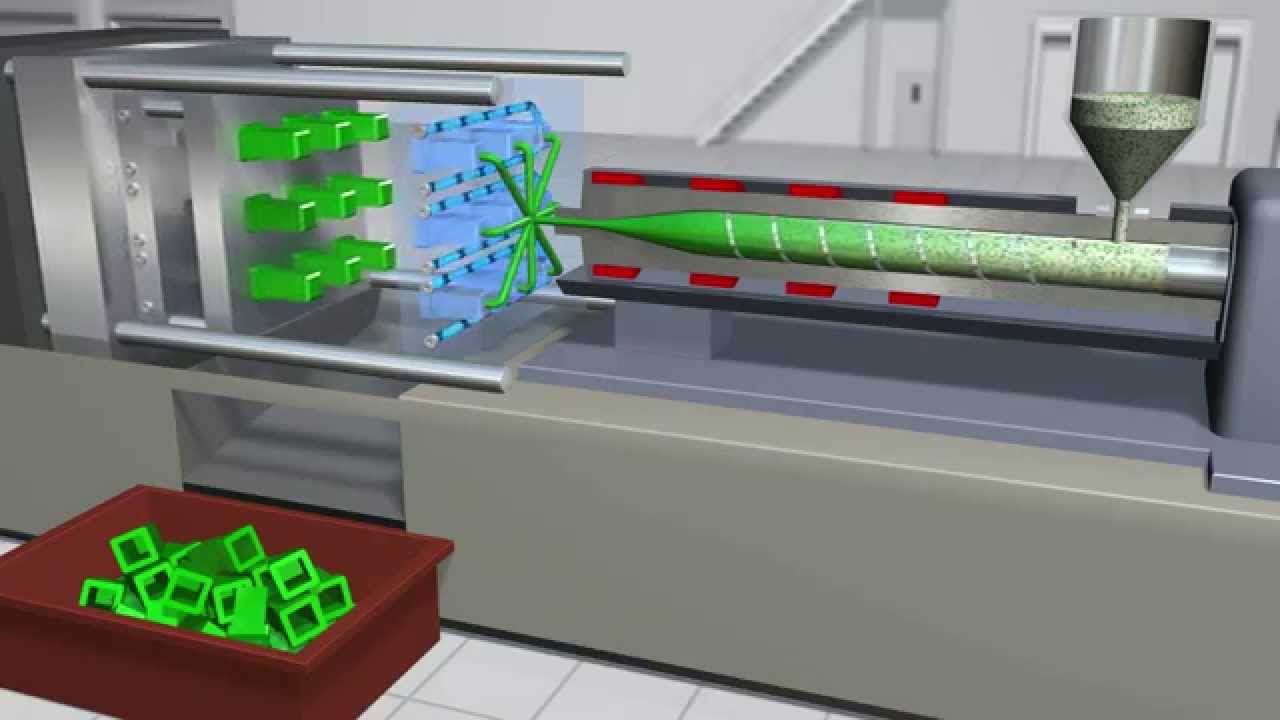
Plastic Processing Overview

How to Install KVM on Ubuntu 22.04
5.0 / 5 (0 votes)