İsdemir Fabrikasında Çelik Üretim Süreci
Summary
TLDRThis video provides an in-depth look at Turkey’s largest integrated iron and steel plant, highlighting its innovative processes in steel production. From the conversion of iron ore into molten steel, to advanced refining and alloying techniques, the plant demonstrates cutting-edge technology for creating high-quality steel products. Emphasizing sustainability, the plant efficiently manages waste heat and energy, ensuring minimal environmental impact. The video also showcases the meticulous attention to detail in every step, from raw material handling to the final steel products, cementing its role as a regional leader in the steel industry.
Takeaways
- 😀 Turkey's largest integrated iron and steel facility produces over 5.8 million tons of steel annually across 700+ steel grades.
- 😀 The steel production process begins with high furnaces, where iron ore is converted into molten iron before being processed into steel.
- 😀 Magnesium and lime are added to molten iron to remove sulfur, forming a slag layer that is discarded for cleaner steel.
- 😀 Steel quality is monitored through advanced tracking systems, ensuring precise control over every cast and its chemical composition.
- 😀 Recycled scrap materials are used in steel production, with rigorous checks for radioactivity to ensure safety and quality.
- 😀 High-pressure oxygen is blown into molten iron during steel refining to reduce carbon content, alongside the removal of unwanted elements like phosphorus and silica.
- 😀 The facility uses sophisticated systems to measure and control the temperature and chemical composition of the steel during production.
- 😀 Final steel products include flat products (e.g., x70, dp600) and long products (e.g., welding wire, carbon steel) that meet specific industry standards.
- 😀 The plant captures waste heat and uses it for energy generation, promoting sustainability and reducing environmental impact.
- 😀 Steel production is carefully documented and tracked through Level 2, 3, and 4 systems to ensure the quality and traceability of each product.
- 😀 The small casting unit produces special-quality billets up to 12 meters in length, using closed casting techniques and advanced cooling systems for superior quality.
Q & A
What is the primary product of the steel production facility described in the transcript?
-The primary product is steel, specifically flat and long steel products, with a production capacity of approximately 5.8 million tons annually.
What is the process for converting iron ore into liquid steel?
-Iron ore is first processed in high furnaces to produce liquid iron, which is then transported to the steelmaking process, where impurities are removed and the iron is converted into steel.
How is sulfur removed from the liquid iron during steel production?
-Sulfur is removed by adding magnesium and lime, which react with the sulfur to form slag that is separated from the molten iron.
What role does oxygen play in the steel production process?
-Oxygen is injected at high pressure into the liquid metal in the converter to reduce the carbon content and facilitate the removal of unwanted elements like phosphorus and silica.
What is the purpose of the slag in steelmaking?
-Slag helps to remove impurities such as sulfur, phosphorus, and carbon from the steel, and it is removed from the molten metal during the process to ensure cleaner steel production.
How are raw materials and additives handled during the steel production process?
-Raw materials, including scrap metal, are carefully weighed and added to the furnace. The additives, such as lime, magnesium, and calcium, are used to refine the steel and remove impurities.
What is the significance of controlling the temperature during steel production?
-Temperature control is crucial to ensure proper chemical reactions, homogeneity, and quality of the steel. It helps maintain the desired properties of the final product and ensures efficient processing.
How is steel quality ensured during the continuous casting process?
-Steel quality is monitored through precise temperature control, chemical analysis, and automated systems that track the entire casting process. This ensures uniformity in the final product.
What happens to the byproducts from the steel production process?
-Byproducts, including low-pressure steam and waste gases, are captured and sent to energy facilities for electricity generation, helping to recycle energy within the plant.
How does the plant ensure the steel products meet customer specifications?
-The plant uses various advanced processes and technologies to produce steel products with specific grades, such as X70, DP600, and S700, which meet the required customer specifications for different applications like construction and automotive.
Outlines
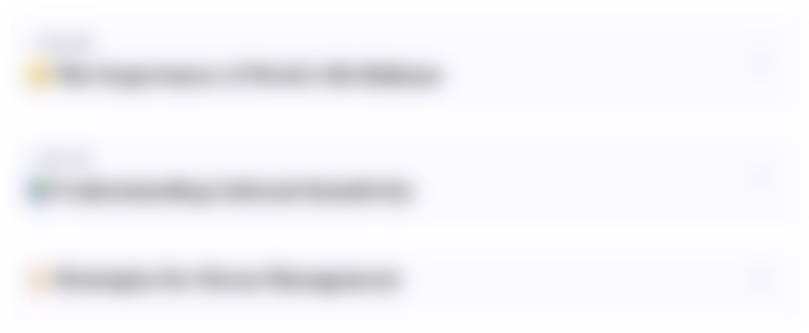
此内容仅限付费用户访问。 请升级后访问。
立即升级Mindmap
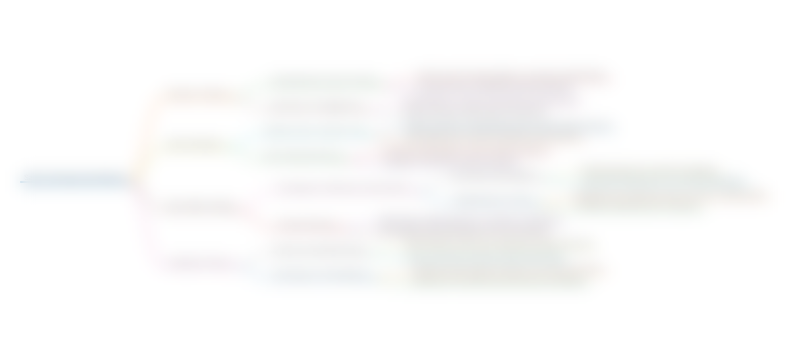
此内容仅限付费用户访问。 请升级后访问。
立即升级Keywords
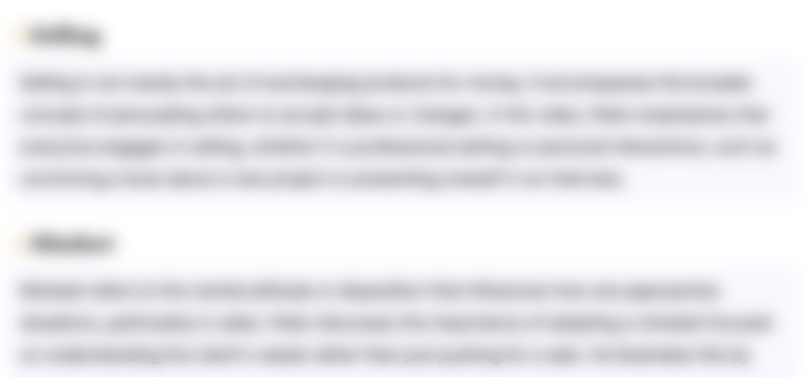
此内容仅限付费用户访问。 请升级后访问。
立即升级Highlights
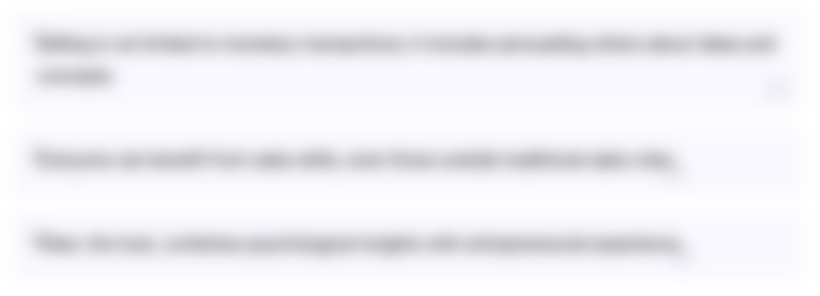
此内容仅限付费用户访问。 请升级后访问。
立即升级Transcripts
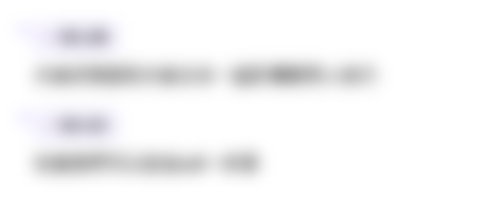
此内容仅限付费用户访问。 请升级后访问。
立即升级5.0 / 5 (0 votes)