Orçamento de Produção
Summary
TLDRThe video explains the process of budgeting and cost calculation in production. It begins with determining monthly production needs based on sales forecasts, followed by calculating raw material costs, direct labor, and indirect costs. The production cost is then broken down for each product type, considering material usage, labor hours, and cost allocations. The importance of accurate calculations is emphasized, particularly in ensuring unit costs are precise. Finally, the video concludes with a summary table that consolidates all the cost components and the final unit production cost for each product, highlighting the significance of careful budgeting in manufacturing.
Takeaways
- 😀 The production budget starts by determining how much to produce based on sales quantities and desired inventory levels.
- 😀 To calculate monthly production, sales quantity is divided by 12 to get the monthly production volume.
- 😀 Inventory policy is important; for example, a three-month inventory of finished products is required by the end of the production period.
- 😀 To determine the required production, sales for 12 months and the desired 3 months of inventory must be accounted for, leading to a yearly production estimate.
- 😀 Raw material costs are calculated by determining the amount of material needed to produce one unit of product and multiplying by the unit cost of the raw material.
- 😀 Direct labor costs are calculated based on the number of hours required to produce each product and the hourly labor cost.
- 😀 For product A, 2 hours of labor are required per unit, while product B needs 4 hours per unit.
- 😀 Indirect costs must be apportioned based on each product’s share of total revenue, with the total indirect cost multiplied by the product’s percentage share.
- 😀 To check the allocation of indirect costs, it's important to verify that the sum of the apportioned indirect costs equals the total indirect costs.
- 😀 A summary table is created to consolidate raw material costs, labor costs, and indirect costs for both products, allowing for easy comparison.
- 😀 The unit cost of each product is derived by dividing the total production cost by the number of units produced, with results typically expressed to four decimal places to avoid rounding errors.
Q & A
What is the first step in the production process mentioned in the transcript?
-The first step is to create the production budget, which involves determining how much needs to be produced in order to meet the sales goals.
How is the monthly production quantity calculated?
-The monthly production quantity is calculated by taking the total annual sales quantity and dividing it by 12.
What is the desired inventory policy for finished products?
-The desired inventory policy is to have an initial inventory of zero and to end with three months' worth of sales.
How is the annual production quantity determined?
-The annual production quantity is calculated by taking the sales for 12 months and adding the inventory required for 3 months, resulting in 15 months of sales.
How are the raw material costs for each product determined?
-The raw material costs are determined by calculating the quantity of materials needed for each product and multiplying the units used by the cost per unit of each material.
What is the significance of the raw material and labor costs in the production process?
-The raw material and labor costs are crucial for determining the total cost of producing each product. These costs must be accurately calculated to ensure proper budgeting and cost control.
How is direct labor cost calculated for the production of each product?
-The direct labor cost is calculated by determining the number of hours required to produce each unit of a product, multiplying that by the hourly wage, and then multiplying by the total number of units produced.
How are indirect manufacturing costs allocated to each product?
-Indirect manufacturing costs are allocated based on the percentage participation of each product in the overall revenue. These percentages are applied to the total indirect costs to determine each product's share.
What is the importance of checking the calculations for indirect costs?
-Checking the calculations for indirect costs ensures that the allocation of costs is accurate and that there are no discrepancies or errors in the overall cost distribution.
How is the unit cost for each product calculated?
-The unit cost for each product is calculated by dividing the total cost for the product by the quantity produced. This gives the cost per unit produced.
Outlines
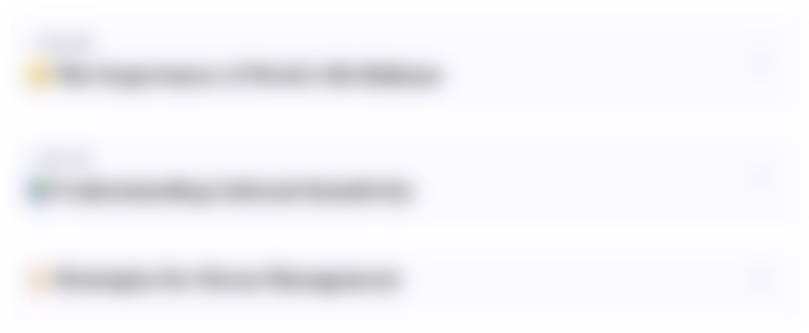
This section is available to paid users only. Please upgrade to access this part.
Upgrade NowMindmap
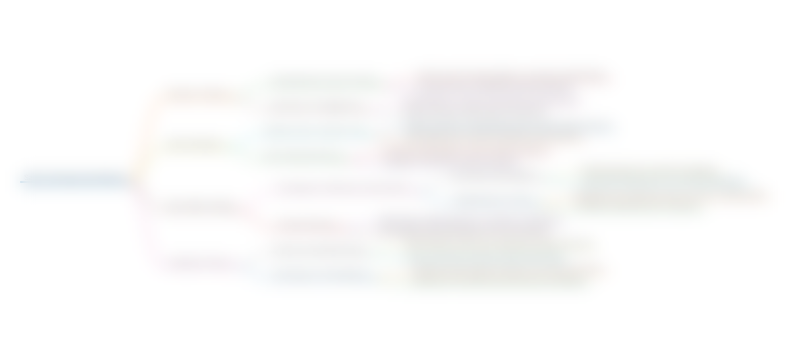
This section is available to paid users only. Please upgrade to access this part.
Upgrade NowKeywords
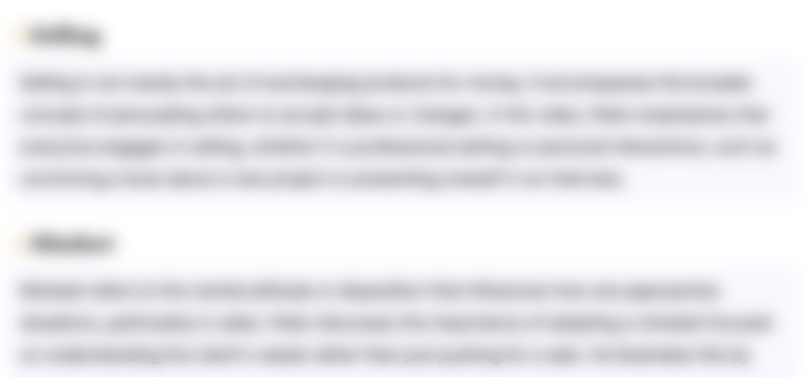
This section is available to paid users only. Please upgrade to access this part.
Upgrade NowHighlights
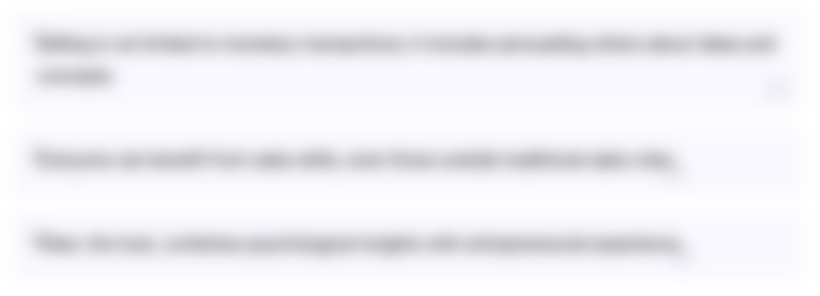
This section is available to paid users only. Please upgrade to access this part.
Upgrade NowTranscripts
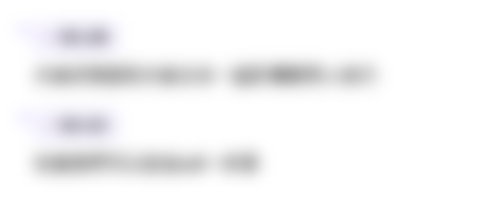
This section is available to paid users only. Please upgrade to access this part.
Upgrade NowBrowse More Related Video
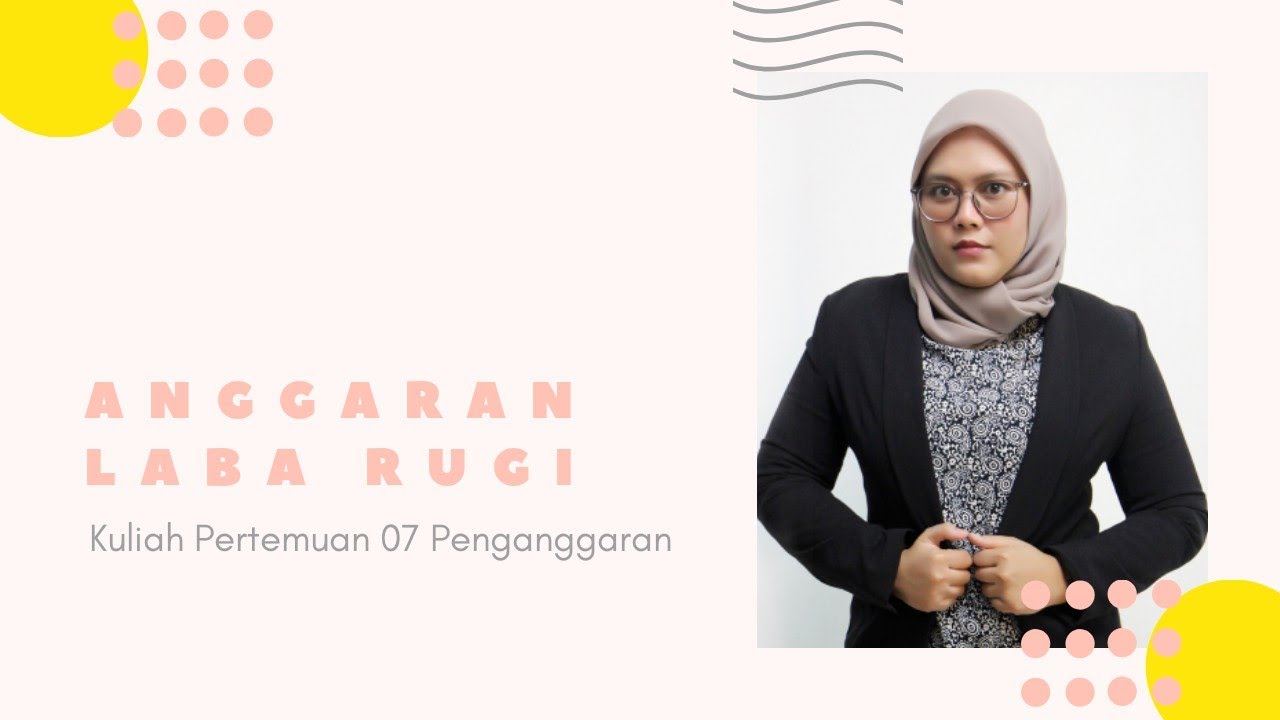
[MEET 7] PENGANGGARAN - ANGGARAN LABA RUGI

Orçamento série do zero aos 50 mil na serralheria

Tugas vidio Presentasi Kelompok 4 (Anggaran Tenaga Kerja) Mata kuliah Budgeting
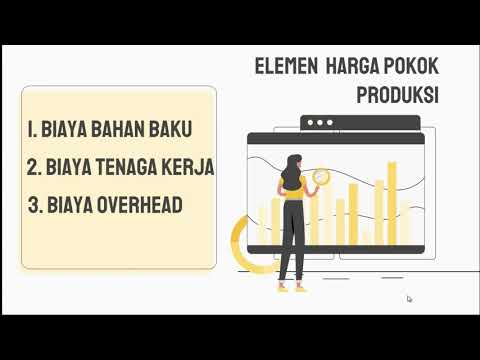
MENGHITUNG HARGA POKOK PRODUKSI + CONTOH
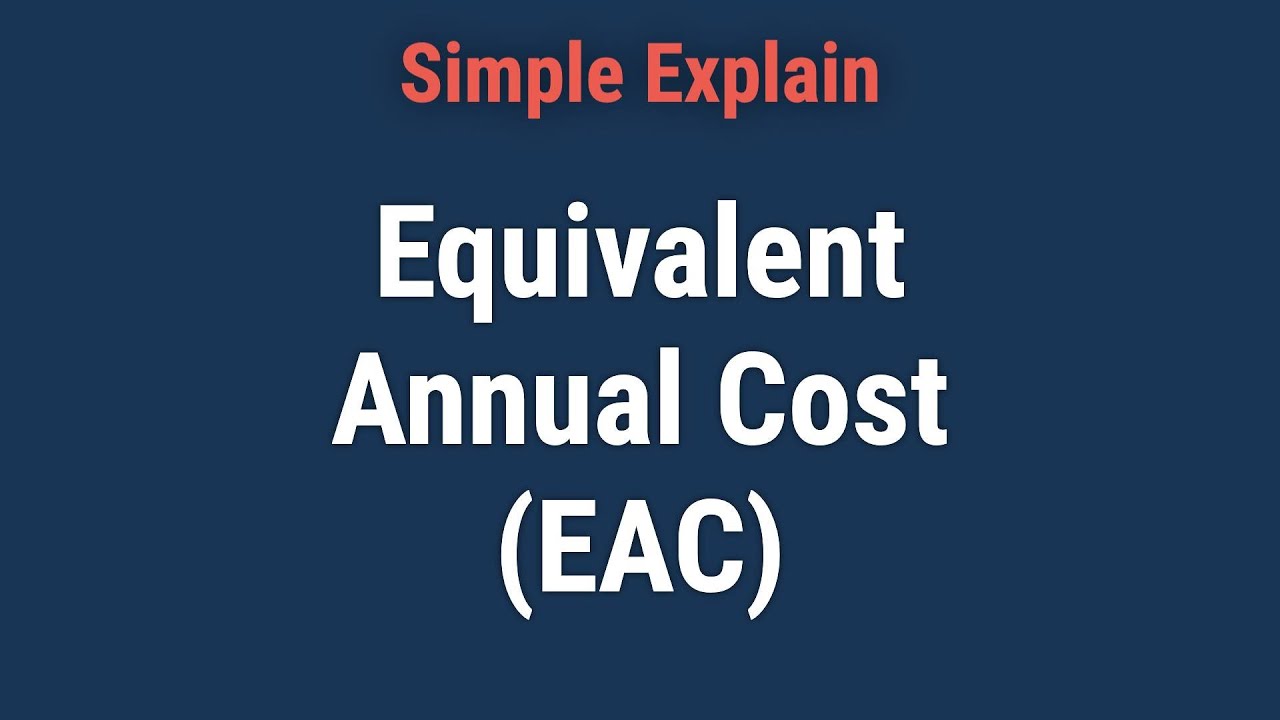
What Is the Equivalent Annual Cost (EAC)?

VIDEO TERBAIK - PENYUSUNAN LAPORAN BIAYA PRODUKSI - Metode Rata Rata dan FIFO - AKUNTANSI BIAYA
5.0 / 5 (0 votes)