Why Don’t Railroads Need Expansion Joints?
Summary
TLDRThis video explores the fascinating world of thermite welding in railway construction. It highlights the process of creating continuous welded rails (CWR), the testing of weld strength under extreme conditions, and the challenges of managing thermal expansion. The video delves into the technology behind thermite welding, the importance of balancing thermal and mechanical forces to prevent rail buckling, and the role of sleepers and ballast in maintaining track integrity. With millions of welds performed each year, thermite welding is a key element in building efficient, durable railways for faster trains and smoother rides.
Takeaways
- 😀 Thermite welding is a process used to join steel rails together using liquid steel, typically done in the field or on-site.
- 😀 The quality of thermite welds is thoroughly tested, with Goldschmidt performing extensive tests to ensure their durability and strength.
- 😀 Rail sections are tested to failure to measure the force required to break them and analyze the bending and hardness properties.
- 😀 During tests, welds are bent under increasing force to determine the weak spots, and it’s revealed that the heat-affected zone (not the weld itself) often breaks first.
- 😀 Thermite is used in over 2 million welds each year, with approximately half of those using Goldschmidt's technology, creating around 50 kilometers of railroad annually.
- 😀 Continuous welded rails don’t buckle in the summer due to a balance of thermal expansion and mechanical compression forces.
- 😀 The rail can expand or contract depending on temperature, and this change in length (strain) is compensated by mechanical stress applied by the sleepers and ballast.
- 😀 Sleepers and ballast keep the rail in place, allowing it to expand sideways rather than lengthwise, preventing rail buckling during heat.
- 😀 The neutral temperature of rail is kept as high as possible to avoid cracking in winter and buckling in summer, ensuring the rail’s longevity and functionality.
- 😀 Cracked rails are easier to detect through conductivity measurements compared to buckled rails, making monitoring and maintenance more efficient.
- 😀 The importance of mechanical stress in balancing thermal expansion is what allows trains to travel faster, with fewer vibrations, and with less frequent rail maintenance.
Q & A
What is the primary purpose of thermite welding in railroads?
-Thermite welding is used to fuse rail segments together to create continuous, welded rail (CWR). This method results in fewer joints, which improves ride quality, reduces maintenance, and minimizes track vibrations for faster trains.
How does the thermite welding process work?
-Thermite welding involves using a chemical reaction between aluminum and iron oxide to produce molten iron, which is then used to fuse two rail segments together. This creates a strong, seamless bond between the rails.
What are the critical factors tested when welding rails using thermite?
-When welding rails, factors such as chemistry, hardness, and bending strength are tested to ensure the quality and durability of the weld. Bending tests are conducted to see how much force is required to break the weld, ensuring it can withstand real-world stresses.
Why is it important to test rail welds for bending strength?
-Testing rail welds for bending strength ensures that the welded rail can endure the stresses of constant train traffic without failing. It helps identify weaknesses in the welds that could potentially cause rail fractures or other issues over time.
What happens during the bending test of a welded rail?
-During the bending test, the welded rail is placed in a machine where pressure is applied to bend the rail until it snaps. The amount of force and the speed of bending are measured to determine the weld's strength and resilience.
What is the typical result of the bending test for welded rails?
-Typically, the welded rail breaks under tension at the heat-affected zone adjacent to the weld. This zone is weaker than the weld itself, and the crack usually propagates upward from the bottom of the weld.
How does rail expansion and contraction affect rail systems in hot and cold weather?
-In hot weather, rails expand, and in cold weather, they contract. To manage this, railroads use mechanical stress to control the rail's length, preventing issues such as buckling in the summer or cracking in the winter.
What role do sleepers and ballast play in controlling rail expansion?
-Sleepers (also called ties) and ballast are used to apply compressive stress to the rails. Sleepers pin the rails in place, and ballast locks them in position. This allows the rail to expand laterally when heated, rather than lengthening excessively and potentially buckling.
Why do railroads prefer higher neutral temperatures for their rails?
-Railroads prefer higher neutral temperatures because rails that shrink too much in winter are more problematic than those that expand too much in summer. A rail that expands in the summer is easier to manage, as buckling can be avoided with mechanical stress.
How are rail cracks detected more easily than rail buckles?
-Rail cracks can be detected more easily using conductivity measurements, as cracks in the rail disrupt electrical conductivity. Buckled rails, however, are more challenging to detect because they don’t have a significant disruption in conductivity.
Outlines
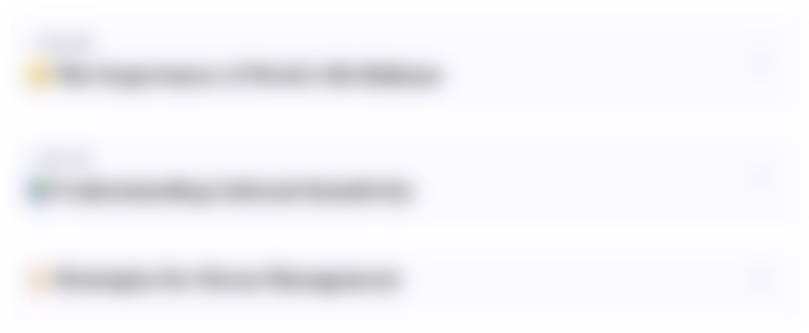
This section is available to paid users only. Please upgrade to access this part.
Upgrade NowMindmap
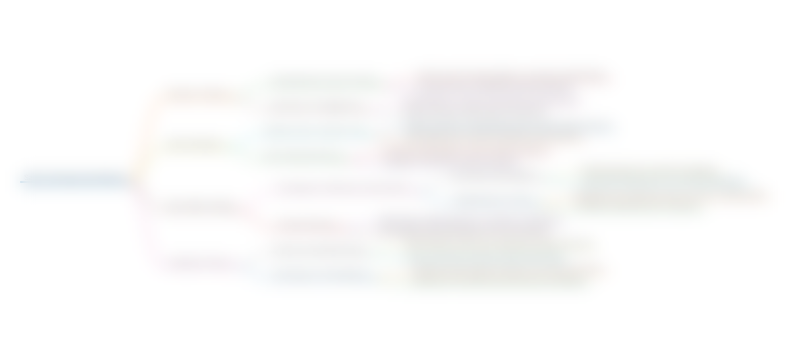
This section is available to paid users only. Please upgrade to access this part.
Upgrade NowKeywords
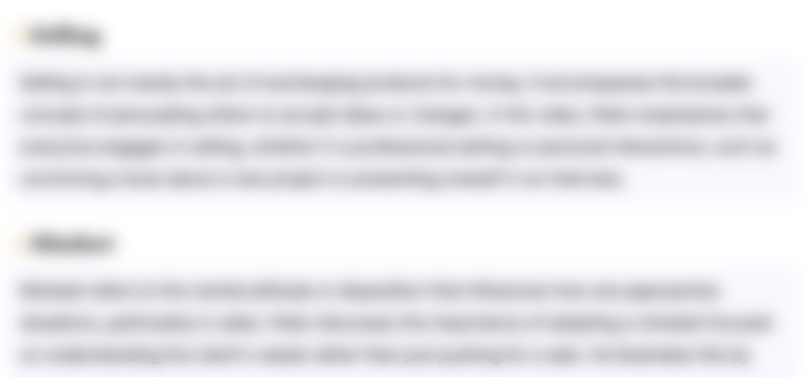
This section is available to paid users only. Please upgrade to access this part.
Upgrade NowHighlights
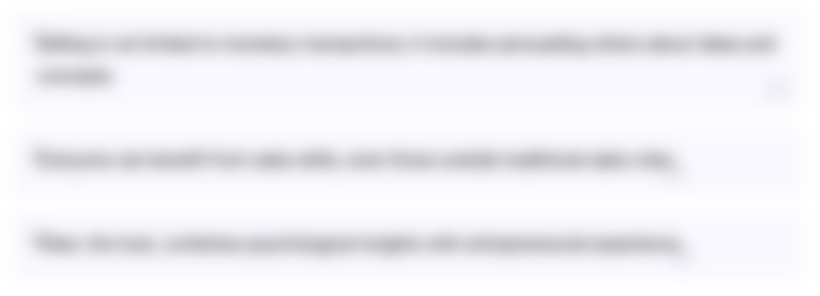
This section is available to paid users only. Please upgrade to access this part.
Upgrade NowTranscripts
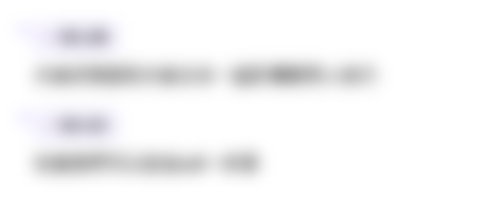
This section is available to paid users only. Please upgrade to access this part.
Upgrade NowBrowse More Related Video
5.0 / 5 (0 votes)