How to Make Prepreg Carbon Fibre Parts (XPREG® XC110)
Summary
TLDRIn this video, Paul from Easy Composites provides a comprehensive introduction to working with the XPREG XC110 out-of-autoclave prepreg carbon fiber system. He demonstrates the step-by-step process of templating, cutting, laminating, vacuum bagging, and oven curing a complex engine cover. Key topics include the storage and handling of prepregs, essential tools and techniques for lamination, and the importance of proper vacuum bagging and curing. The video highlights how the XPREG XC110 delivers autoclave-quality results, offering a reliable and efficient solution for both structural and cosmetic composite components.
Takeaways
- 😀 Prepreg carbon fibre, like XPREG XC110, is pre-impregnated with resin, making it easier to laminate without handling wet resins.
- 😀 The XPREG XC110 system is designed for out-of-autoclave processing, offering results comparable to autoclave systems without the need for pressurized equipment.
- 😀 Prepreg should be stored frozen in sealed bags and has a shelf life of 4 weeks out of the freezer. Improper handling can lead to resin curing prematurely.
- 😀 Templating is an essential part of prepreg work, allowing precise cutting and alignment of the material in the mould to ensure proper fit and minimize waste.
- 😀 Using masking tape for templating ensures accurate cut lines, especially around negative features and corners, reducing the chances of bridging during lamination.
- 😀 Proper mould selection is crucial. XPREG prepreg is compatible with specific mould materials like high-temperature epoxy, metals, and certain glass types, but not polyester or polyurethane tools.
- 😀 Laminating prepreg involves ensuring intimate contact with the mould surface. A systematic approach using tools like rollers helps press the material down effectively.
- 😀 Debulking is an optional but useful step to reduce pinholes and bridging, especially on larger or multi-ply structures, using perforated release film and a vacuum bag.
- 😀 The backing ply is essential for building part thickness, and using a heavier carbon fibre material for the backing is more cost-effective than using the same material throughout.
- 😀 The curing process involves a two-stage temperature cycle to ensure optimal resin flow and full mechanical properties. Following the recommended cure cycles is critical for achieving high-quality results.
- 😀 The final part, once cured, should be demoulded carefully to avoid sharp edges. Trimming and finishing are essential for safe handling and achieving a high-quality finish.
Q & A
What is prepreg carbon fibre and how is it different from conventional dry reinforcement?
-Prepreg carbon fibre is a type of dry reinforcement that has been pre-impregnated with a resin containing hardener. This contrasts with conventional dry reinforcement, which requires the addition of resin during the manufacturing process.
Why is XPREG XC110 considered an ideal choice for out-of-autoclave processing?
-The XPREG XC110 system is designed to achieve results comparable to those produced using an autoclave. It is developed to be processed in an oven and helps minimize issues like pinholes and voids, which are common in oven-cured prepregs.
What is the recommended storage condition for prepreg materials?
-Prepreg materials should be kept frozen in a sealed bag to prevent contamination. A standard domestic freezer or a larger cold storage facility can be used, and the material must remain frozen until ready for use.
What is the 'out-life' of the XPREG XC110 prepreg, and why is it important?
-The XPREG XC110 prepreg has a working time or out-life of 4 weeks at room temperature. This is important as it defines the period during which the resin remains viable for use before it starts to deteriorate.
What is the purpose of creating templates when working with prepreg?
-Templates are used to accurately mark the shapes of the pieces of prepreg material that will be laminated into the mould. They help ensure the correct fit and alignment of the material, reducing the risk of bridging and voids during the laminating process.
How does the choice of cut placement in negative features benefit the laminating process?
-Placing cuts in negative features, such as corners, helps make the laminating process easier. It reduces the risk of bridging, allowing the material to conform more smoothly into intricate mould shapes and minimizing voids in these areas.
What should be done to ensure proper adhesion during the laminating phase?
-To ensure proper adhesion, the prepreg must be pressed into full contact with the mould surface, starting from a center point and working outward. Using a methodical approach and tools like rollers or custom-made tools is essential to achieve consistent coverage.
What is 'debunking' and when is it necessary?
-Debulking is a process used to remove trapped air and improve consolidation in the laminate, especially important in larger or more complex structures. It involves using a perforated release film, breather, and vacuum bagging to apply pressure and remove air pockets.
What is the recommended cure cycle for the XPREG XC110 system?
-The recommended cure cycle for the XPREG XC110 system involves a 2-step process: starting at a lower temperature for optimal resin flow and then increasing the temperature to fully cure the resin, ensuring the part achieves its maximum mechanical properties.
What types of mould materials are compatible with the XPREG system?
-The XPREG system is compatible with materials like epoxy tooling, metals (aluminium, stainless steel), and flat glass moulds. Moulds made from polyester or polyurethane should be avoided due to temperature limitations and potential compatibility issues that could lead to imperfections.
Outlines
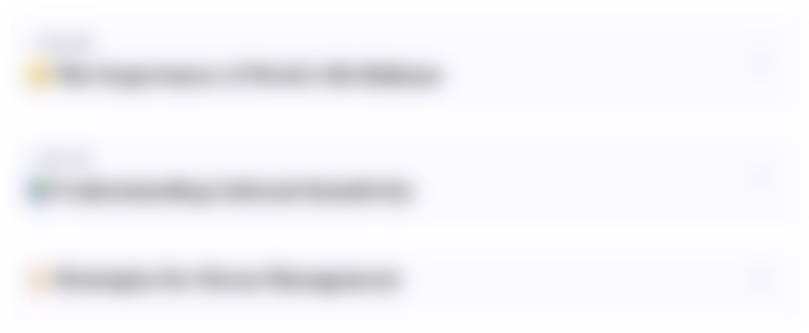
This section is available to paid users only. Please upgrade to access this part.
Upgrade NowMindmap
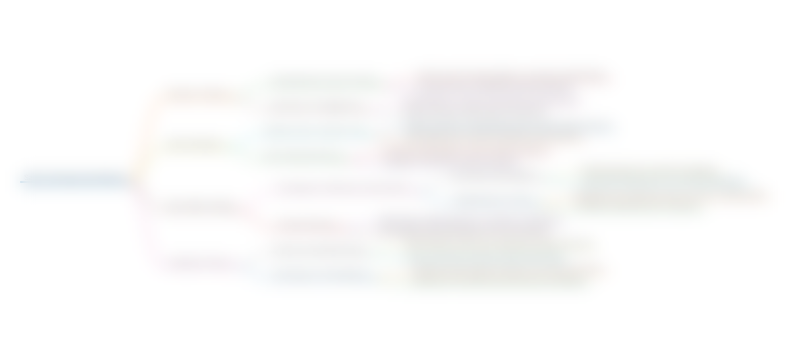
This section is available to paid users only. Please upgrade to access this part.
Upgrade NowKeywords
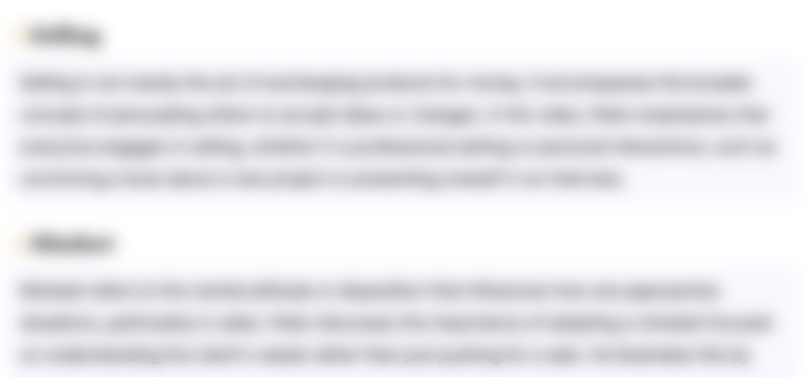
This section is available to paid users only. Please upgrade to access this part.
Upgrade NowHighlights
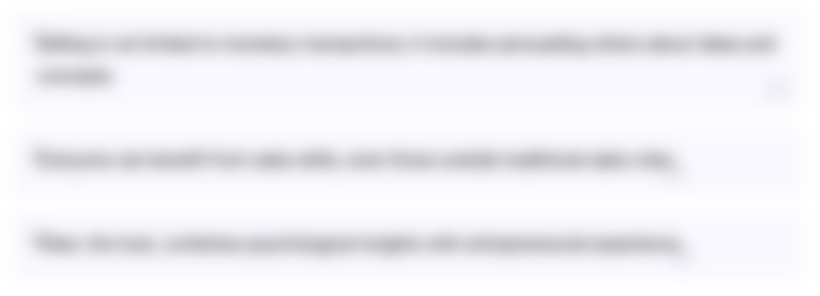
This section is available to paid users only. Please upgrade to access this part.
Upgrade NowTranscripts
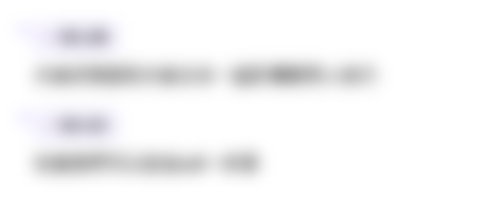
This section is available to paid users only. Please upgrade to access this part.
Upgrade Now5.0 / 5 (0 votes)