Työtapaturmien taloudelliset vaikutukset
Summary
TLDRIn Finland, approximately 250,000 work-related accidents occur annually, affecting around 10% of the workforce. These incidents result in over €330 million in costs for employers, including medical expenses and lost workdays. Accidents not only disrupt production but also incur indirect costs such as overtime and reputational damage. The importance of proactive risk assessment is highlighted through two case studies, demonstrating how safety measures can prevent severe accidents. Investing in workplace safety not only safeguards employees but also enhances organizational efficiency and helps attract talent. Ensuring a safe work environment is essential for long-term success and sustainability.
Takeaways
- 😀 Workplace accidents in Finland total approximately 250,000 annually, affecting up to 10% of employees.
- 😀 Over 100,000 of these accidents result in costs that are covered by employer accident and occupational disease insurance, amounting to over 330 million euros each year.
- 😀 Even accidents that don't result in direct insurance claims lead to additional costs such as absenteeism, disruptions, extra work, delays, and damage to reputation.
- 😀 The cost of one employee’s sick day is estimated to be three times their salary, factoring in production slowdowns, replacement labor, and overtime costs.
- 😀 On average, a full workday missed due to an accident costs an employer over 400 euros, and over 2,000 euros for a full workweek.
- 😀 Costs related to accident management, such as medical treatment and administrative work, are not included in the above estimates.
- 😀 When considering long-term absenteeism, recruitment and training of replacements further increase costs significantly.
- 😀 An example of a fall accident resulting in severe injury cost the employer 30,000 euros just for absentee days.
- 😀 Predicting the duration and long-term impact of an injury is difficult, but accidents could often be prevented with relatively low-cost safety measures, like a 1,000-euro railing.
- 😀 Another example highlights a workplace accident where an employee was severely injured after being struck by a heavy object, leading to permanent disability and significant insurance claims.
- 😀 Prevention of such accidents can be achieved through joint risk assessment between contractors and clients, particularly during the planning phase of work.
- 😀 Prioritizing safety means making sure work is only done when risks are fully assessed and managed, ensuring a safe environment for employees.
- 😀 Analyzing near-miss incidents can be as effective as studying accidents after they occur, providing insights without the losses associated with actual incidents.
- 😀 Ensuring worker safety is a fundamental right, and organizations that prioritize workplace safety are more attractive employers, helping secure future workforce availability.
Q & A
What is the estimated number of workplace accidents in Finland each year?
-There are approximately 250,000 workplace accidents in Finland annually, affecting about 10% of the workforce.
How much does it cost employers annually due to workplace accidents in Finland?
-The total annual cost of workplace accidents for employers is over 330 million euros, which includes medical and other related expenses covered by workers' compensation insurance.
What are the indirect costs of workplace accidents beyond insurance claims?
-In addition to direct insurance claims, workplace accidents lead to absenteeism, disruptions, additional work, delays, and potential damage to the company's reputation.
How much does one day of employee absence cost an employer in Finland?
-One day of employee absence is estimated to cost an employer three times the employee's daily wage, considering factors like production slowdown, the need for replacement labor, and overtime costs.
What is the cost of a full workday and workweek in Finland due to an employee absence?
-With the average Finnish salary, a full workday absence costs more than 400 euros, while a full workweek absence costs over 2,000 euros.
What additional costs are not included in the estimates of workplace accident-related expenses?
-The estimates do not include time spent on handling and investigating the accident or the costs of recruiting and training replacements for long-term absences.
How can an organization reduce the costs of workplace accidents?
-Organizations can reduce costs by proactively assessing and managing risks during the planning phase, ensuring that work is performed only when it is safe to do so.
What was the first example of a workplace accident discussed in the transcript?
-The first example involved an employee falling and sustaining serious injuries, leading to a cost of 30,000 euros solely for the lost workdays.
How could the first accident have been prevented, according to the transcript?
-The first accident could have been prevented by installing a safety railing that would have cost around 1,000 euros.
What was the second example of a workplace accident, and how severe were the consequences?
-The second example involved an employee being hit on the head by a heavy object, resulting in a permanent disability and lifelong incapacity to work. The insurance compensation for the incident amounted to hundreds of thousands of euros.
How could the second accident have been avoided?
-The second accident could have been avoided through a joint risk assessment between the client and the contractor, followed by appropriate preventive measures.
What is the best approach to prevent workplace accidents according to the transcript?
-The best approach is to assess risks during the planning phase of work, ensuring that safety measures are in place before starting any task.
How do organizations benefit from focusing on workplace safety?
-Organizations that prioritize workplace safety are attractive to employees and ensure a steady workforce by safeguarding their well-being, which is vital for future recruitment.
Outlines
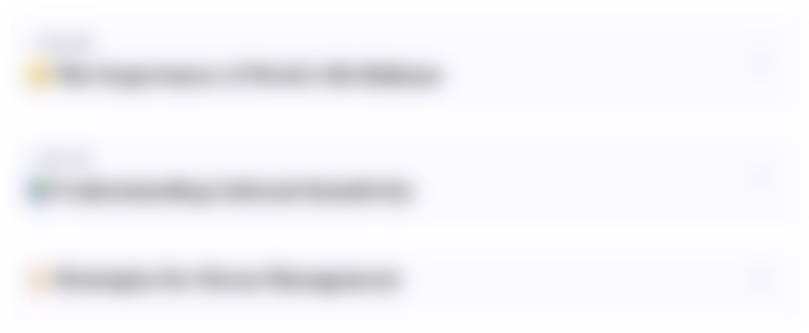
This section is available to paid users only. Please upgrade to access this part.
Upgrade NowMindmap
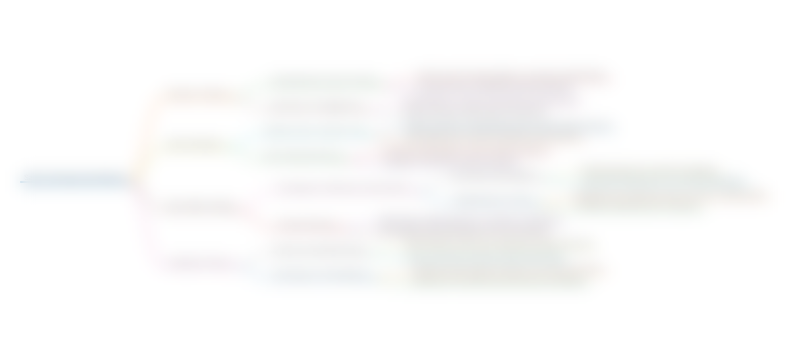
This section is available to paid users only. Please upgrade to access this part.
Upgrade NowKeywords
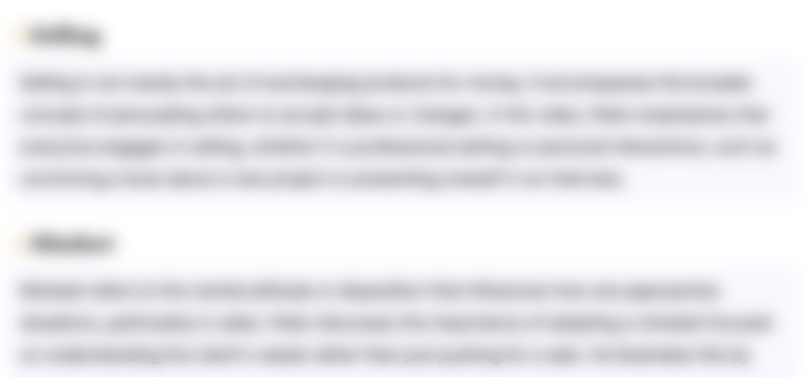
This section is available to paid users only. Please upgrade to access this part.
Upgrade NowHighlights
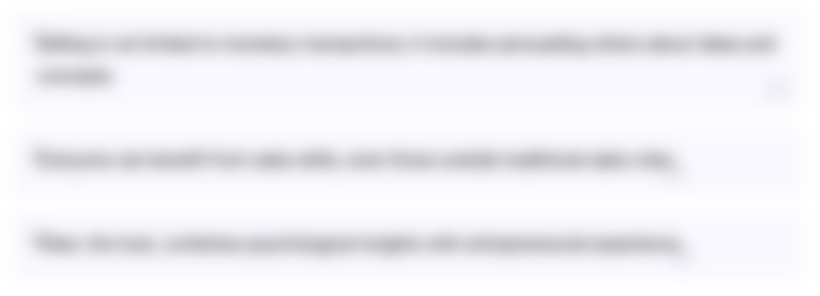
This section is available to paid users only. Please upgrade to access this part.
Upgrade NowTranscripts
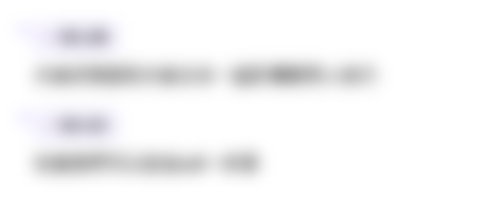
This section is available to paid users only. Please upgrade to access this part.
Upgrade NowBrowse More Related Video
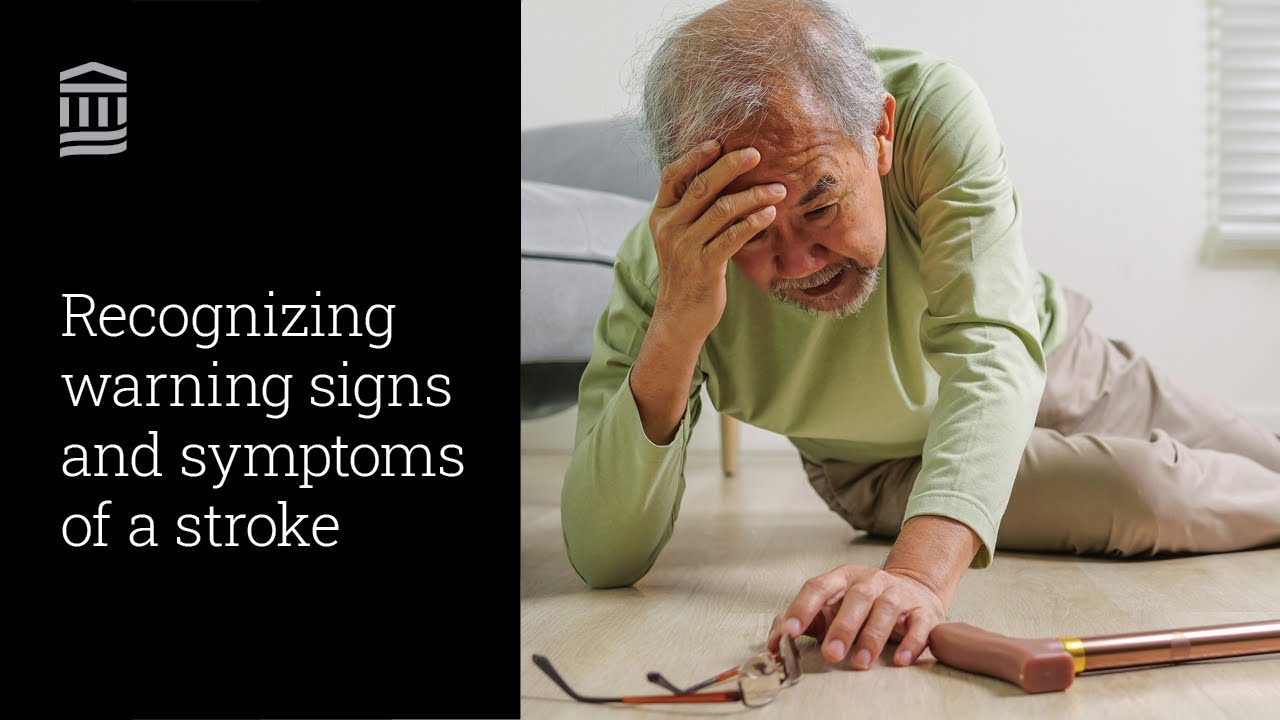
Recognizing Warning Signs and Symptoms of a Stroke | In Case of Emergency | Mass General Brigham

MEMAHAMI K3 DI BENGKEL PERMESINAN

Acidente do trabalho - Conceito prevencionista

Angka Pengangguran Mencapai 8,4 Juta Orang | NEWS SCREEN 27/02

Video Dokumenter Isu Kontemporer Pengelolaan Wilayah Pesisir - Kasus: Sampah di Pantai Peunagan Pasi
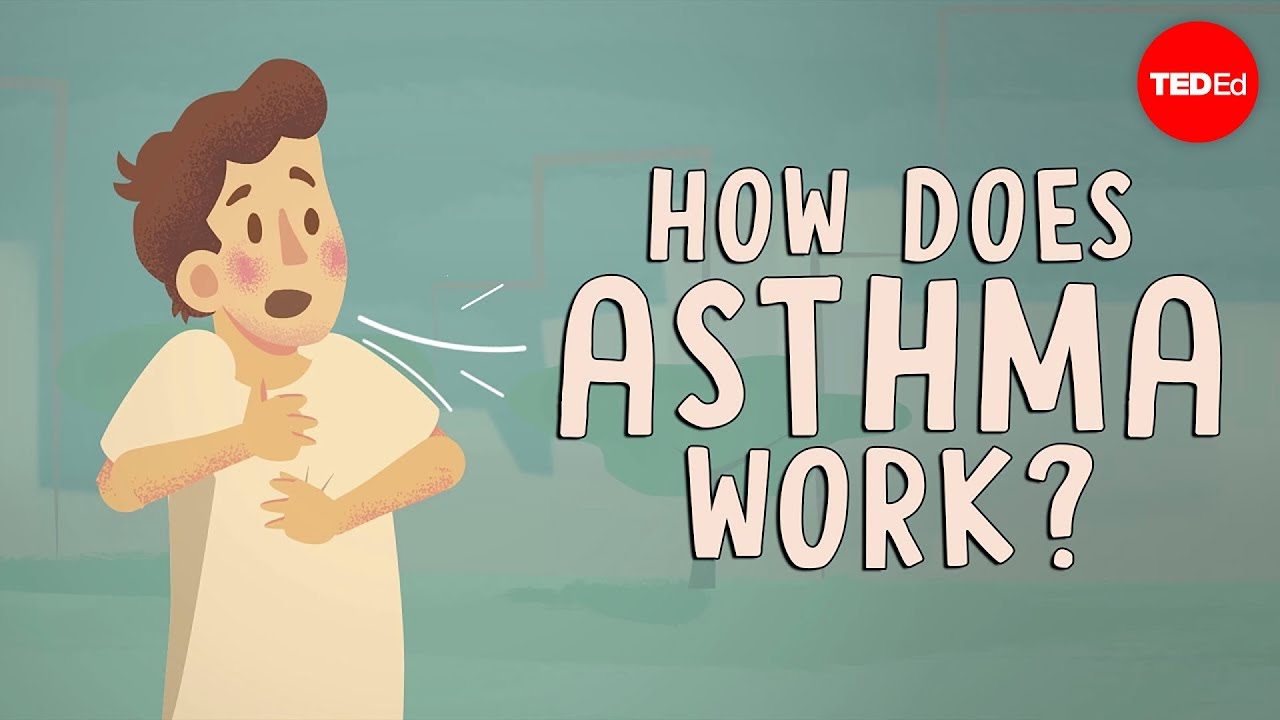
How does asthma work? - Christopher E. Gaw
5.0 / 5 (0 votes)