Deming's 14 Points for Management Explained
Summary
TLDRThis lesson introduces Deming's 14 Points for Management, essential practices for improving an organization's quality, processes, and services. It emphasizes the importance of continuous improvement, reducing variation, and creating a culture of leadership and collaboration. The points guide businesses to prioritize quality, focus on long-term goals, and foster a supportive environment for employees. By following these principles, organizations can reduce costs, increase market share, and enhance employee and customer satisfaction through systematic and sustainable transformation.
Takeaways
- ๐ง Deming's 14 Points are a set of management practices aimed at improving products, services, and processes through continuous improvement.
- ๐ Reducing variation in business processes helps minimize waste and unnecessary costs, leading to more efficiency and quality.
- ๐ Continuous improvement, not cost-cutting, should be a priority for long-term success, creating a virtuous cycle of quality and productivity.
- ๐ฏ The first point, 'Create Constancy of Purpose,' emphasizes long-term improvement as a core business goal rather than a short-term fix.
- ๐ก 'Adopt the New Philosophy' encourages striving for perfect quality and putting customer needs first, rejecting common tolerance for mistakes and inefficiencies.
- ๐ Avoid relying solely on inspections to catch defects; instead, build quality into the process to prevent issues from arising.
- ๐ค Deming advises focusing on total costs, not just price tags, by fostering long-term relationships with single suppliers to reduce hidden costs and improve consistency.
- ๐ Continuous improvement is an ongoing, never-ending process, exemplified by Demingโs PDCA (Plan, Do, Check, Act) cycle.
- ๐ Training is crucial to reduce variation and enable employees to take pride in their work, with leadership focused on removing barriers for employees.
- ๐ซ Eliminate fear and unclear slogans in the workplace, replacing them with concrete actions that improve processes and foster collaboration across departments.
Q & A
What is the main purpose of Deming's 14 Points for management?
-Deming's 14 Points aim to improve an organization's products, services, and processes by focusing on reducing variation and implementing continuous quality improvement across all levels of the business.
How does Deming view variation in business processes, and why is it important to reduce it?
-Deming sees variation as the 'scourge of business' because it increases waste and unnecessary costs. Reducing variation leads to more consistent quality, fewer mistakes, and a more efficient use of resources.
What is the significance of the first point, 'Create constancy of purpose,' in Deming's philosophy?
-The first point emphasizes the need for long-term commitment to continuous improvement, rather than making improvements only when convenient. It involves allocating permanent resources and focusing on future-oriented goals.
How does Deming suggest businesses should approach quality control, according to point three?
-Deming argues against relying on inspections to improve quality because inspections occur too late in the process. Instead, businesses should build quality into their processes from the start, preventing defects rather than detecting them afterward.
Why does Deming recommend using a single supplier for any one item, as stated in point four?
-Deming believes that sourcing from a single supplier helps reduce hidden costs associated with managing multiple suppliers, such as variations in quality, communication issues, and managing larger inventories.
What is the PDCA cycle, and how does it support continuous improvement?
-The PDCA (Plan-Do-Check-Act) cycle is a tool for continuous improvement. It encourages organizations to regularly plan, test, and adjust their processes to improve quality over time through small, incremental changes.
How does Demingโs concept of 'institute leadership' differ from traditional management?
-Deming's idea of leadership focuses on removing barriers for employees and working on sources of improvement, rather than simply setting targets and holding people accountable. Leaders should understand the work, provide guidance, and create a supportive environment for continuous improvement.
What does Deming mean by 'drive out fear' in the workplace, and how does this affect quality?
-Driving out fear means creating an environment where employees feel safe to share ideas, raise concerns, and admit mistakes without fear of ridicule or punishment. A fearless culture improves communication, product quality, and employee retention.
How does Deming suggest eliminating unclear slogans, and why are they considered detrimental?
-Deming argues that slogans like 'Take pride in your work' are ineffective because they put the onus on employees rather than addressing the underlying systemic issues. Instead, management should focus on improving processes to enable better work outcomes.
Why is it important for organizations to 'remove barriers to work pride,' according to Deming?
-Removing barriers to work pride allows employees to take ownership of their work and make improvements to the processes they use. This helps boost morale, increases quality, and encourages employees to contribute to continuous improvement efforts.
Outlines
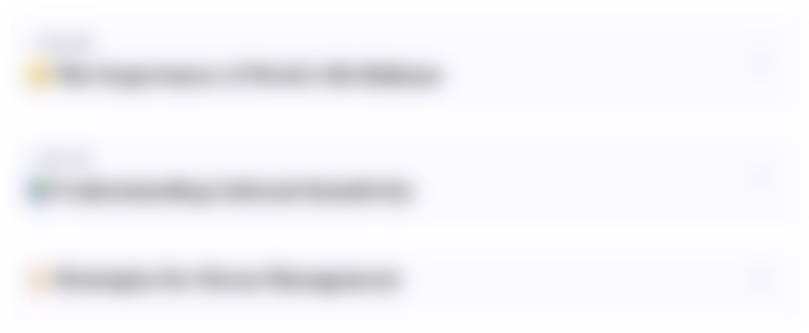
This section is available to paid users only. Please upgrade to access this part.
Upgrade NowMindmap
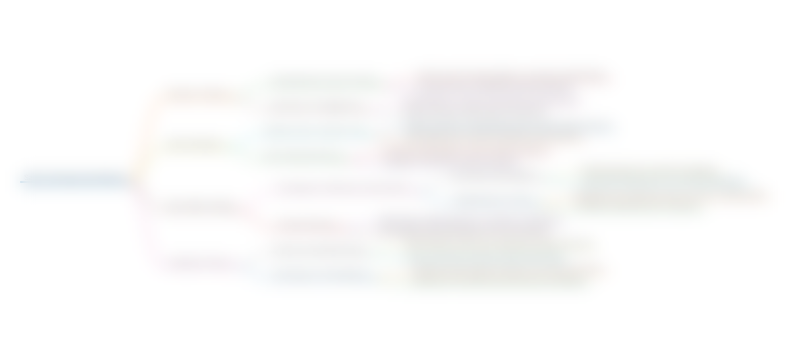
This section is available to paid users only. Please upgrade to access this part.
Upgrade NowKeywords
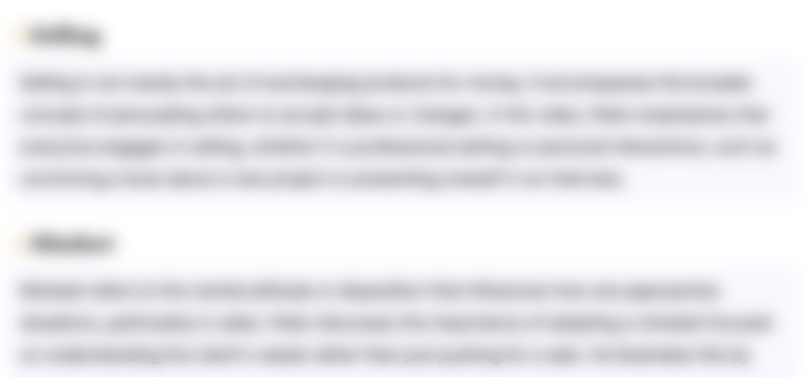
This section is available to paid users only. Please upgrade to access this part.
Upgrade NowHighlights
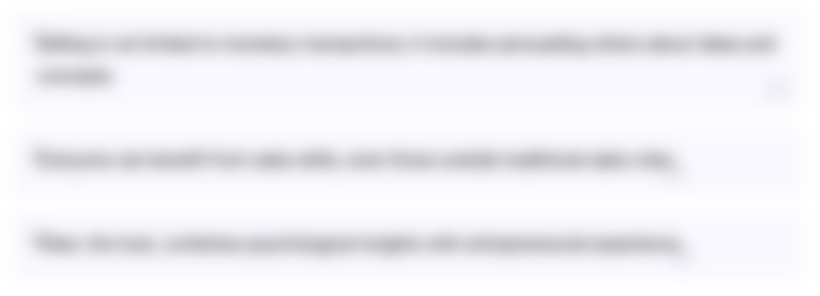
This section is available to paid users only. Please upgrade to access this part.
Upgrade NowTranscripts
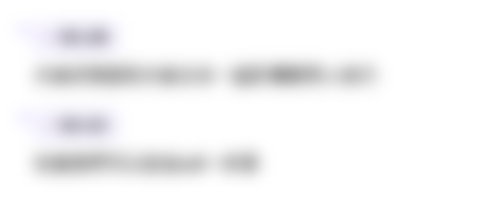
This section is available to paid users only. Please upgrade to access this part.
Upgrade NowBrowse More Related Video

W. Edwards Deming: The 14 Points
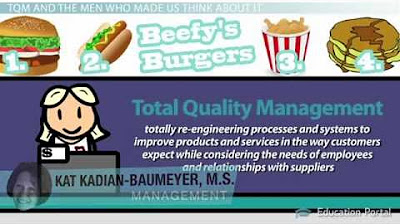
Deming, Juran & Crosby: Contributors to TQM (Total Quality Management)
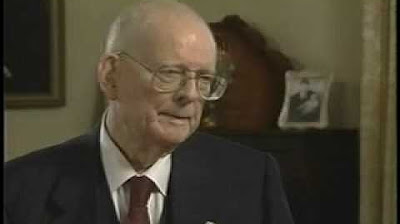
W. Edwards Deming - Part 2

Total Quality Management - Deming Way (Part 1/2)

CompTIA Security+ SY0-701 Course - 1.3 Explain The Importance of Change Management Processes PART A

What Does an ISO 55000 Asset Management System Look Like?
5.0 / 5 (0 votes)