Lecture 6 Process Selection and Facility Layout
Summary
TLDRThis lecture covers process selection and facility layout, highlighting different types of processing systems such as job shops, batch, repetitive, and continuous processes. It explains the need for layout planning to ensure efficient operation, reduce bottlenecks, and enhance safety. Various layout types like product, process, and fixed-position layouts are discussed, along with examples from industries like food service, manufacturing, and healthcare. The lecture concludes with a line-balancing example to demonstrate efficient task distribution across workstations for improved productivity and reduced idle time.
Takeaways
- 🔧 Process selection is crucial for system design, involving capacity planning and aligning processes with required capacity.
- 🏭 There are four types of processing: job shop, batch, repetitive/assembly line, and continuous. Each has its advantages and disadvantages in terms of customization, flexibility, cost, and scheduling complexity.
- 📈 Planning for layout is essential to avoid inefficiencies, bottlenecks, safety hazards, and to accommodate changes in product design, output, methods, environmental or legal requirements, and employee morale.
- 🎯 The primary design objective for layout is to ensure a smooth flow of work, materials, and information through the system.
- 🛠️ Different types of layouts include product layouts for repetitive processes, process layouts for non-repetitive processes, fixed position layouts where the work is stationary, and combination layouts that mix elements of the others.
- 🏥 Examples of service layouts include warehouse storage, retail, and office layouts, which are characterized by the degree of customer contact and customization.
- 🔄 Line balancing is the method of assigning tasks to workstations to equalize the time requirements, aiming for efficient use of labor and equipment and fairness among workstations.
- ⏱️ Cycle time is the maximum time allowed at each workstation and is calculated based on operating time per day and desired output per day.
- 📊 Positional weight is a key factor in task assignment, determined by the sum of task times that must follow a particular task in the process.
- 📉 Efficiency in a balanced line is calculated by considering idle time and is expressed as a percentage, where higher values indicate better utilization of resources.
Q & A
What are the four types of processing mentioned in the lecture?
-The four types of processing mentioned are job shop, batch, repetitive or assembly line, and continuous processing.
What is a job shop and what are its disadvantages?
-A job shop is a type of processing where very specific and customized jobs are handled, like an auto repair shop. Its disadvantages include slow pace, high cost per unit, and complex planning and scheduling.
What are the advantages of batch processing?
-Batch processing allows for flexibility, ease of adding or changing products and services, and has a moderate cost per unit compared to job shops, with moderate scheduling complexity.
How does repetitive or assembly line processing differ from continuous processing?
-Repetitive or assembly line processing involves standardized goods and services where the same task is performed repeatedly, while continuous processing is highly standardized with very high volume and efficiency but lacks variety and has high costs associated with downtime.
Why is it important to plan for layout in a facility?
-Planning for layout is important to ensure efficient operations, avoid high costs, prevent bottlenecks, reduce accidents or safety hazards, and adapt to changes in product or service design, output, methods, environmental or legal requirements, and to improve employee morale.
What are the basic objectives of facility layout design?
-The basic objective of facility layout design is to achieve a smooth flow of work, materials, and information through the system, which can lead to improved quality, efficient use of workers and space, avoidance of bottlenecks, minimization of material handling costs, and ensuring safety.
Can you explain the concept of line balancing in the context of the lecture?
-Line balancing is the process of assigning tasks to workstations so that the workstations have approximately equal time requirements, aiming for equal time allocation to ensure efficient use of labor and equipment and to avoid fairness issues.
What is the significance of cycle time in line balancing?
-Cycle time is the maximum time allowed at each workstation to complete its set of tasks and establishes the rate of output. It is calculated as the operating time per day divided by the desired output per day.
How is the number of workstations determined in line balancing?
-The number of workstations is determined by the desired output and is calculated by summing all task times to find a theoretical minimum number of stations, ensuring each station does not exceed the cycle time.
What is the method for assigning tasks to workstations as described in the lecture?
-Tasks are assigned to workstations starting with the task that has the most following tasks, then considering the greatest positional weight, and ensuring that the time required for tasks at each workstation does not exceed the cycle time.
How is the efficiency of a workstation line calculated?
-The efficiency is calculated as 100% minus the percentage of idle time, which is the idle time per cycle divided by the cycle time. The idle time is the difference between the cycle time and the actual time used at each workstation.
Outlines
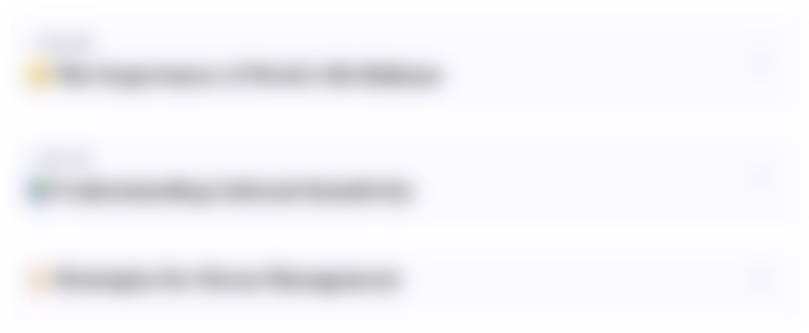
This section is available to paid users only. Please upgrade to access this part.
Upgrade NowMindmap
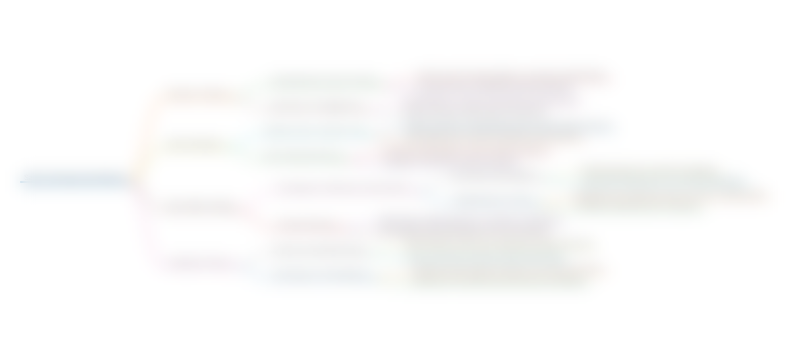
This section is available to paid users only. Please upgrade to access this part.
Upgrade NowKeywords
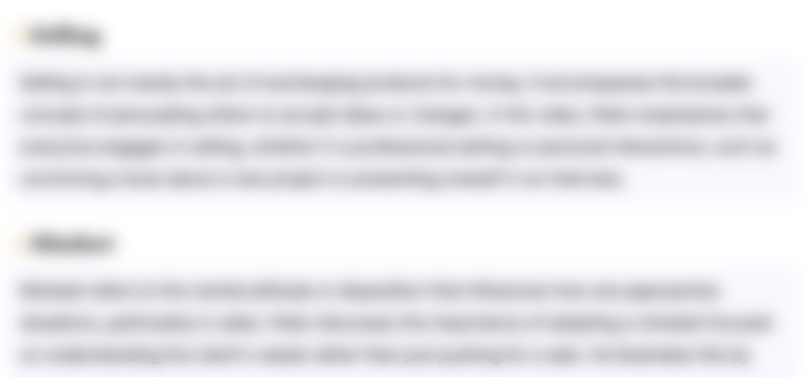
This section is available to paid users only. Please upgrade to access this part.
Upgrade NowHighlights
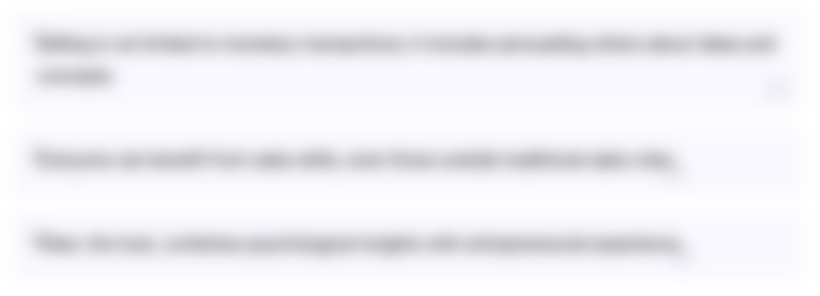
This section is available to paid users only. Please upgrade to access this part.
Upgrade NowTranscripts
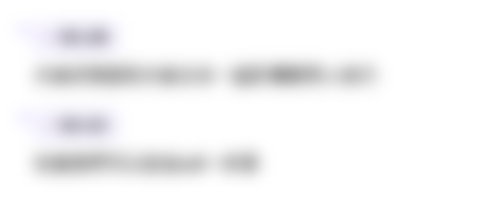
This section is available to paid users only. Please upgrade to access this part.
Upgrade NowBrowse More Related Video
5.0 / 5 (0 votes)