Teknik Pembentukan Logam (Forging)
Summary
TLDRThis video explains the forging process in metallurgy, detailing the various methods used to shape metal through impact and pressure. It covers key techniques such as open die forging, closed die forging, and flashless forging, emphasizing the importance of temperature control and precision. The video also discusses specialized processes like coining and upsetting, highlighting the use of mechanical hammers and hydraulic presses. Design considerations, including parting lines and draft angles, are explained to ensure successful forging. This comprehensive guide is essential for understanding the complexities and applications of metal forging.
Takeaways
- 😀 Forging is a process of deformation on a workpiece using two molds and involves impact and pressure to shape the material.
- 😀 There are two main types of forging based on temperature: hot forging and cold forging. Hot forging is used for more complex shapes, while cold forging is used for specific products.
- 😀 Open die forging involves reducing the height or increasing the diameter of the workpiece, with the goal of forming a simpler shape.
- 😀 Friction during open die forging can lead to imperfections, especially when the die surface has high friction, causing deformation issues in the workpiece.
- 😀 Closed die forging (also known as impression die forging) requires precise design, and the flash formed during this process must be removed after the process is complete.
- 😀 Flashless forging, also known as precision forging, does not allow for flash formation and requires strict control over material volume and mold space.
- 😀 The coining process is a type of forging that uses high pressure to form detailed surface features and tight tolerances on the workpiece.
- 😀 Hammering is a key method in forging, where a drop hammer applies a repeated impact to shape the material, often used for mass production.
- 😀 Hydraulic presses and mechanical presses provide controlled, gradual force to shape materials, offering consistent and precise results in forging.
- 😀 The design of the forging mold is critical and involves five key factors: parting line, draft, ribs, flash, and filling to ensure optimal material flow and ease of removal from the mold.
Q & A
What is the forging process?
-Forging is a deformation process where a workpiece is shaped using two dies, applying impact and pressure to mold the material into the desired form.
How is forging classified?
-Forging can be classified into several types, primarily based on temperature: hot forging, warm forging, and cold forging, each with different material properties and applications.
What is the difference between hot forging and cold forging?
-Hot forging involves high temperatures, making the material more malleable, while cold forging occurs at or near room temperature, often used for creating precise parts with improved surface finish.
What happens when there is friction during the open die forging process?
-If friction occurs during open die forging, it prevents perfect deformation. The result can be an imperfect shape, such as a concave shape instead of a straight cylinder, due to the resistance to the metal flow.
What are the three main types of forging mentioned in the script?
-The three main types of forging mentioned are open die forging, closed die forging (also known as impression die forging), and flash forging.
What is flash forging, and how is it different from closed die forging?
-Flash forging involves creating a flash (extra material) during the forging process, which is later trimmed off. It differs from closed die forging, where the mold is closed and no flash is created.
What is coining in the context of forging?
-Coining is a specific forging technique used to create detailed surface patterns on the workpiece. It requires high pressure to ensure precise shape and surface finish.
How does a drop hammer work in forging?
-A drop hammer applies repeated impact to a workpiece to form it into the desired shape. The hammer falls due to gravity and hits the material, typically used for mass production of certain parts.
What is the role of the forging die in the process?
-The forging die is crucial for shaping the material. It must be designed with precision, including considerations for flash, draft angles, and parting lines, to ensure successful deformation and efficient production.
What are some of the limitations when designing a forging die?
-Key limitations in designing a forging die include ensuring proper parting lines, controlling flash formation, managing draft angles for ease of removal, and accounting for material flow and pressure during forging.
Outlines
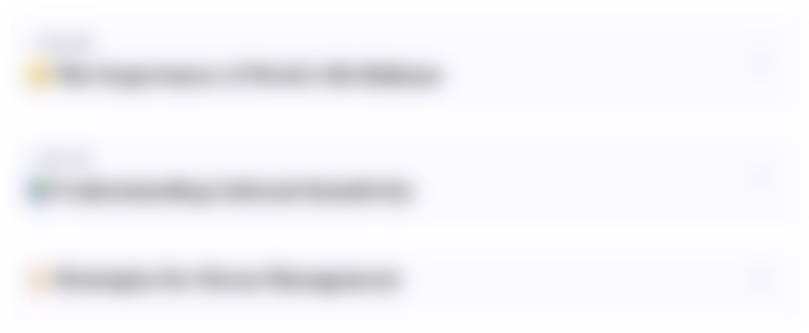
このセクションは有料ユーザー限定です。 アクセスするには、アップグレードをお願いします。
今すぐアップグレードMindmap
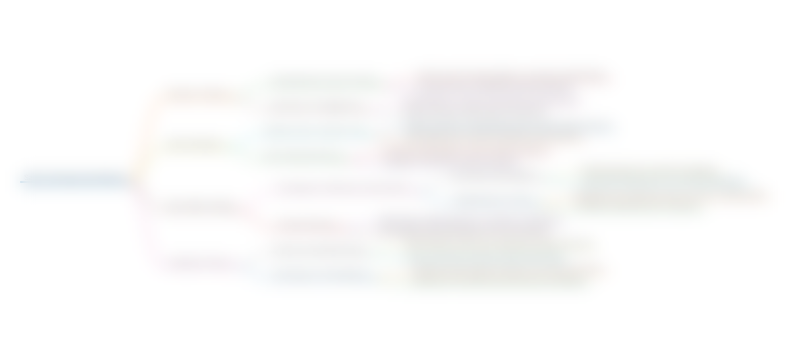
このセクションは有料ユーザー限定です。 アクセスするには、アップグレードをお願いします。
今すぐアップグレードKeywords
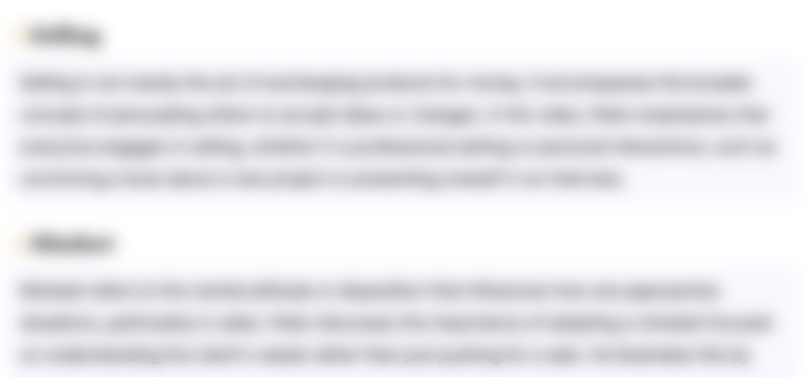
このセクションは有料ユーザー限定です。 アクセスするには、アップグレードをお願いします。
今すぐアップグレードHighlights
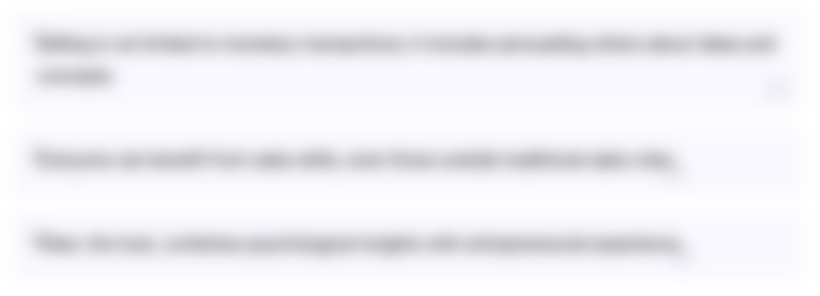
このセクションは有料ユーザー限定です。 アクセスするには、アップグレードをお願いします。
今すぐアップグレードTranscripts
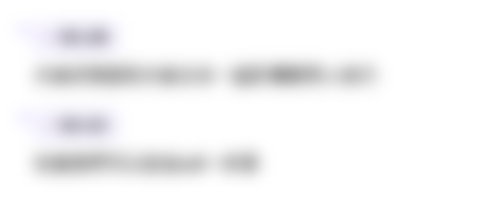
このセクションは有料ユーザー限定です。 アクセスするには、アップグレードをお願いします。
今すぐアップグレード関連動画をさらに表示
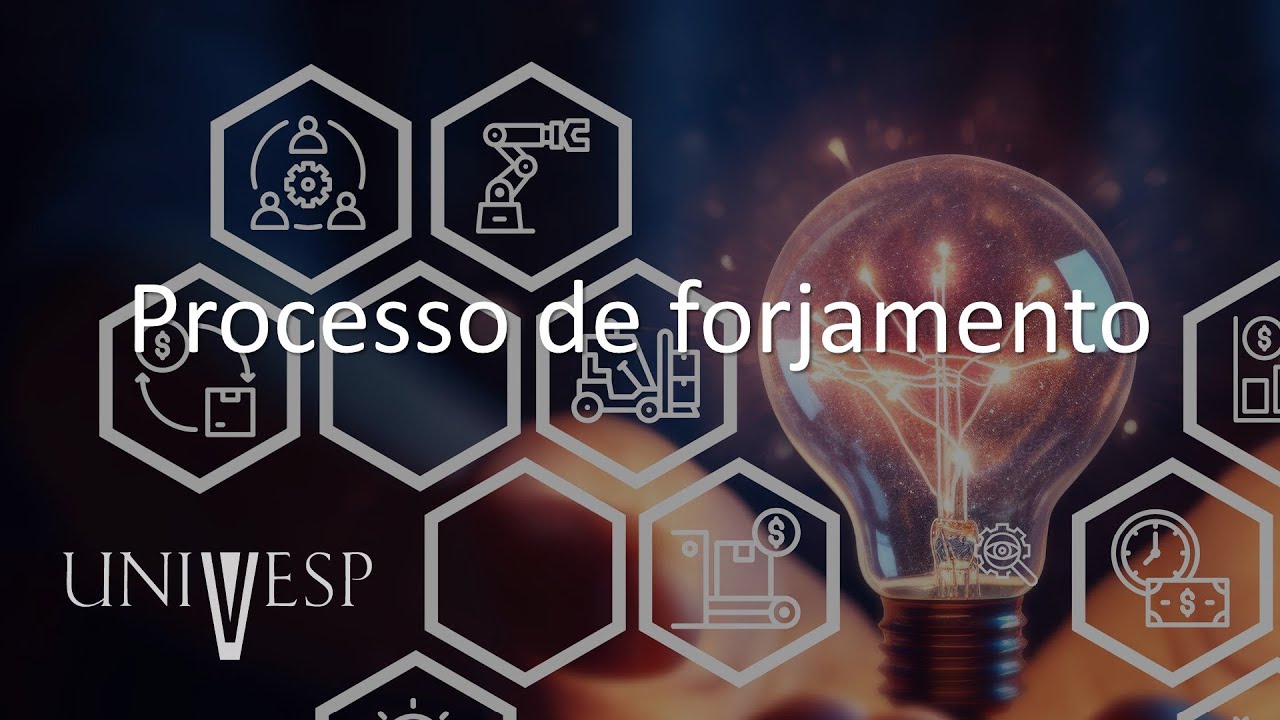
Materiais e Processos de Fabricação para Engenharia de Produção - Processo de forjamento
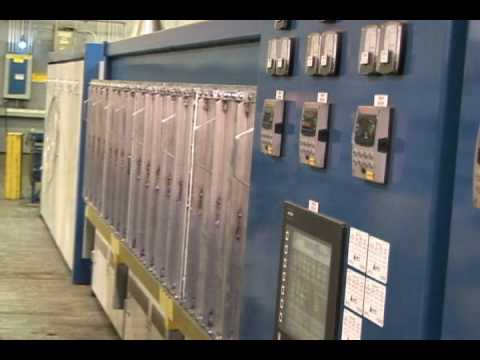
Powder Metallurgy Touches Your Life, Part 2

What Are The Common Types Of Metal Casting Process In Engineering and Industry?

Weld Meta l- Chemical reaction
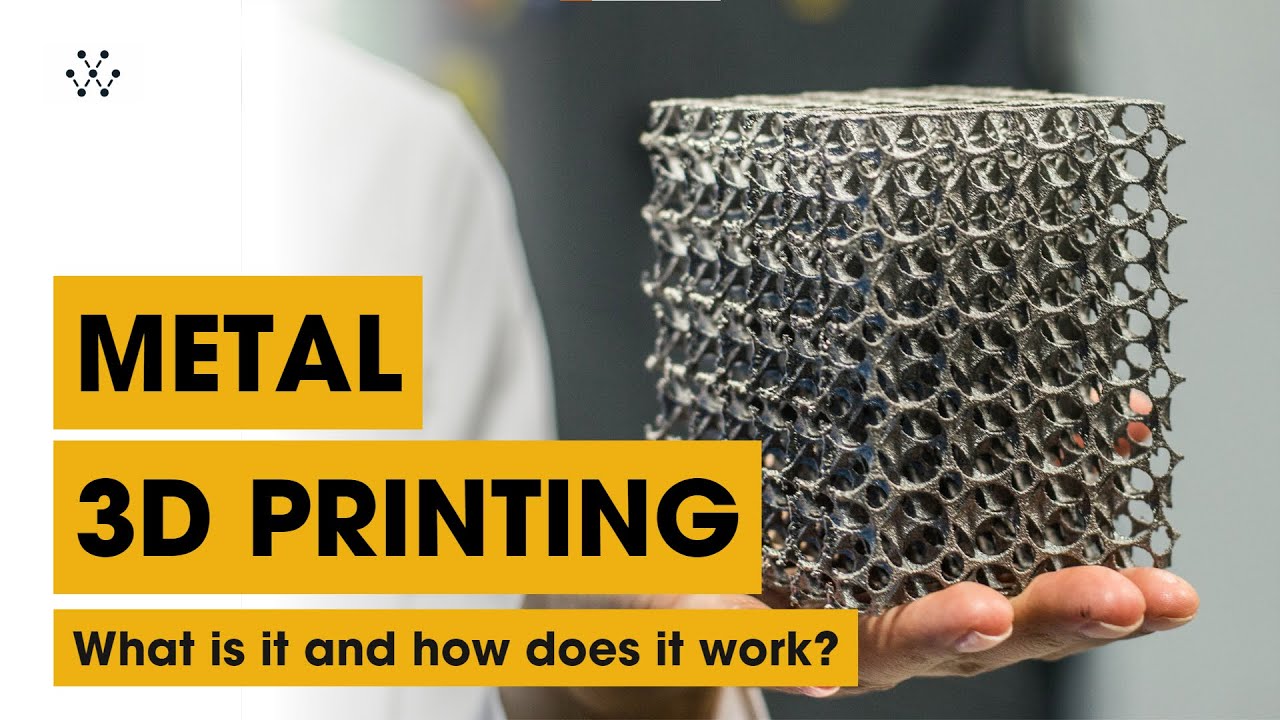
METAL 3D PRINTING | What is it and how does it work ?
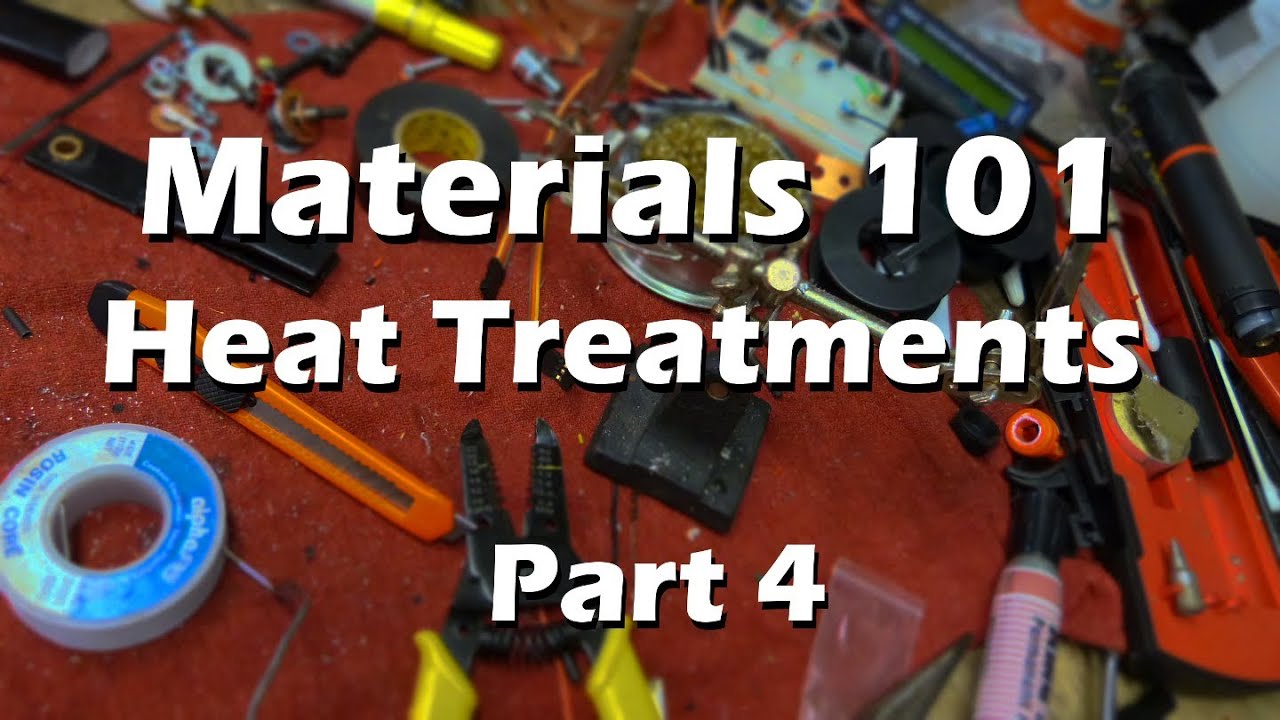
Materials Science Mechanical Engineering - Part 4 Heat Treatment Explained
5.0 / 5 (0 votes)