Runaway: Explosion at T2 Laboratories
Summary
TLDROn December 19, 2007, T2 Laboratories in Jacksonville, Florida, experienced a catastrophic explosion due to a runaway chemical reaction in a reactor producing MCMT, a gasoline additive. The blast resulted in fatalities, injuries, and significant property damage. The incident highlighted the importance of understanding and managing reactive chemical hazards, effective emergency pressure relief systems, and the need for comprehensive training in chemical engineering to prevent such tragedies.
Takeaways
- 🔥 On December 19, 2007, a catastrophic explosion and fire at T2 Laboratories in Jacksonville, Florida, resulted in fatalities and injuries, highlighting the dangers of runaway chemical reactions.
- 🏭 T2 Laboratories produced methylcyclopentadienyl manganese tricarbonyl (MCMT), a gasoline additive, using a 2500-gallon reactor with a computerized control system.
- ⚠️ The explosion was caused by a malfunctioning cooling system during an exothermic reaction, leading to a temperature and pressure spike in the reactor.
- 👨🔬 The company's co-owners were killed in the incident, emphasizing the severity of the consequences of not managing chemical processes correctly.
- 🏢 The blast had a significant impact, damaging buildings over 1500 feet away and causing debris to travel up to a mile, showcasing the power of the explosion.
- 📊 A CSB study identified 167 serious accidents due to uncontrolled chemical reactions between 1980 and 2001, resulting in 108 deaths and substantial property damage.
- 🔬 T2 scaled up their MCMT process directly from a one-liter reactor to full production without addressing the increased challenges in cooling and controlling the reaction.
- 🚨 The company's lack of a comprehensive cooling system and absence of a backup plan for malfunctions contributed to the disaster.
- 📚 The CSB emphasized the importance of education and awareness in recognizing and controlling reactive hazards, which was lacking in T2's operations.
- 🛠️ To prevent such accidents, the CSB recommended that companies implement emergency pressure relief systems, design safeguards, effective operating procedures, and training programs.
Q & A
What event is described in the video script?
-The video script describes a powerful explosion and fire that occurred at T2 Laboratories in Jacksonville, Florida on December 19, 2007.
What was the cause of the explosion at T2 Laboratories?
-The explosion was caused by a runaway chemical reaction in the reactor due to a malfunctioning cooling system, leading to a loss of temperature control.
What chemical was being produced at T2 Laboratories when the explosion occurred?
-T2 Laboratories was producing methylcyclopentadienyl manganese tricarbonyl (MCMT), a gasoline additive.
What were the consequences of the explosion in terms of fatalities and injuries?
-The explosion resulted in the death of the co-owner and the operator in the control room, and two other operators died from flying debris. Additionally, 32 other people were injured, including 28 at nearby businesses.
How far did the blast impact reach?
-The blast damaged buildings over 1500 feet away and debris was found up to a mile from the explosion site.
What was the scale-up process like for T2 Laboratories' MCMT production?
-T2 Laboratories developed its MCMT process using a one-liter reactor and then scaled up directly to a full production volume in a 2500-gallon reactor without a gradual scale-up.
What safety issues were identified in the company's handling of the MCMT production process?
-T2 Laboratories had only a simple cooling system without a backup, and they did not fully investigate causes of temperature control issues during production runs. The company also lacked proper training on reactive hazards.
What recommendations were made by the CSB to prevent similar accidents in the future?
-The CSB recommended that companies identify and evaluate reactive hazards, implement emergency pressure relief systems and design safeguards, develop effective operating procedures and training programs, and plan for possible accidents including evacuation drills and emergency response exercises.
What was the role of education and awareness in the context of the T2 Laboratories accident?
-Education and awareness were highlighted as crucial in understanding and managing reactive chemistry hazards. The CSB noted that many incidents occur due to a lack of awareness among those operating the processes about the existence and potential consequences of reactive hazards.
What was the significance of the study completed by the CSB in 2002 regarding reactive chemical hazards?
-The CSB's 2002 study identified 167 serious accidents involving uncontrolled chemical reactions between 1980 and 2001, causing 108 deaths and significant property damage, emphasizing the need for better control and understanding of reactive chemical hazards.
Outlines
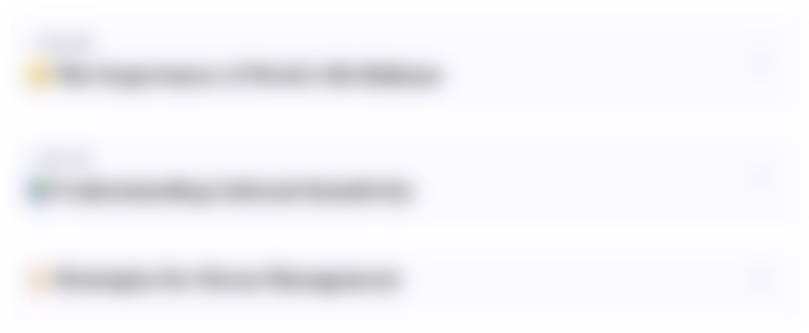
このセクションは有料ユーザー限定です。 アクセスするには、アップグレードをお願いします。
今すぐアップグレードMindmap
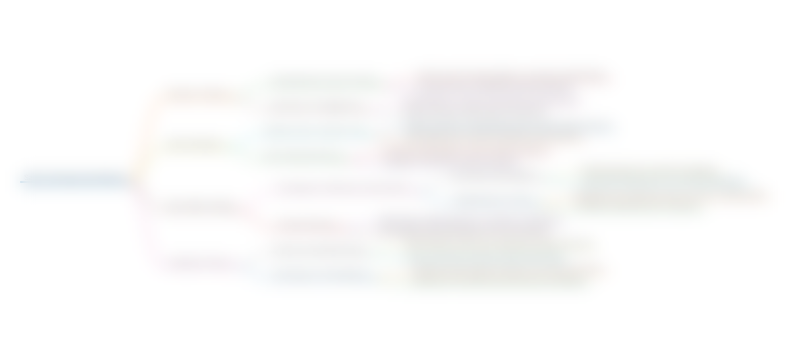
このセクションは有料ユーザー限定です。 アクセスするには、アップグレードをお願いします。
今すぐアップグレードKeywords
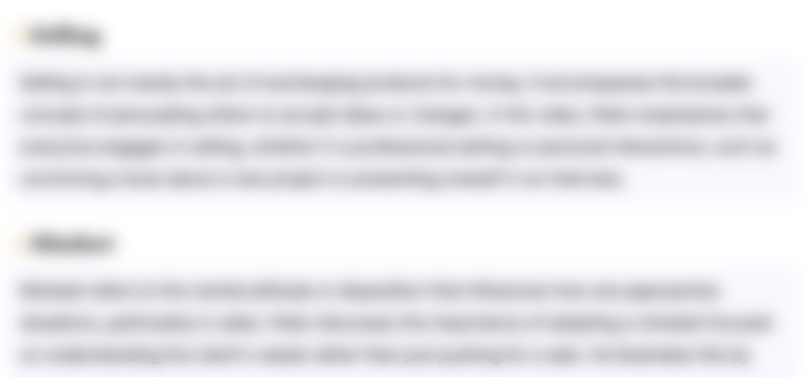
このセクションは有料ユーザー限定です。 アクセスするには、アップグレードをお願いします。
今すぐアップグレードHighlights
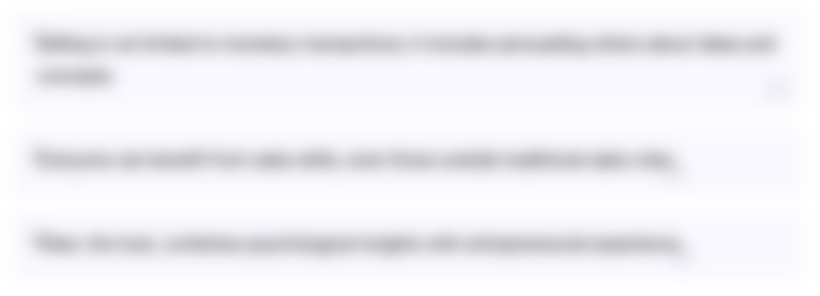
このセクションは有料ユーザー限定です。 アクセスするには、アップグレードをお願いします。
今すぐアップグレードTranscripts
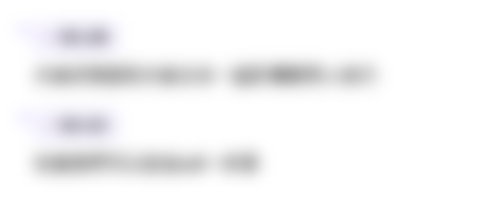
このセクションは有料ユーザー限定です。 アクセスするには、アップグレードをお願いします。
今すぐアップグレード関連動画をさらに表示

Incompatible Chemicals: Explosion at AB Specialty Silicones

Simulation of cumene (Isopropyl Benzene) production | Aspen Hysys V10

Chemical Reaction Engineering - Lecture # 4 - Design Equations for Batch Reactor, CSTR, PFR & PBR
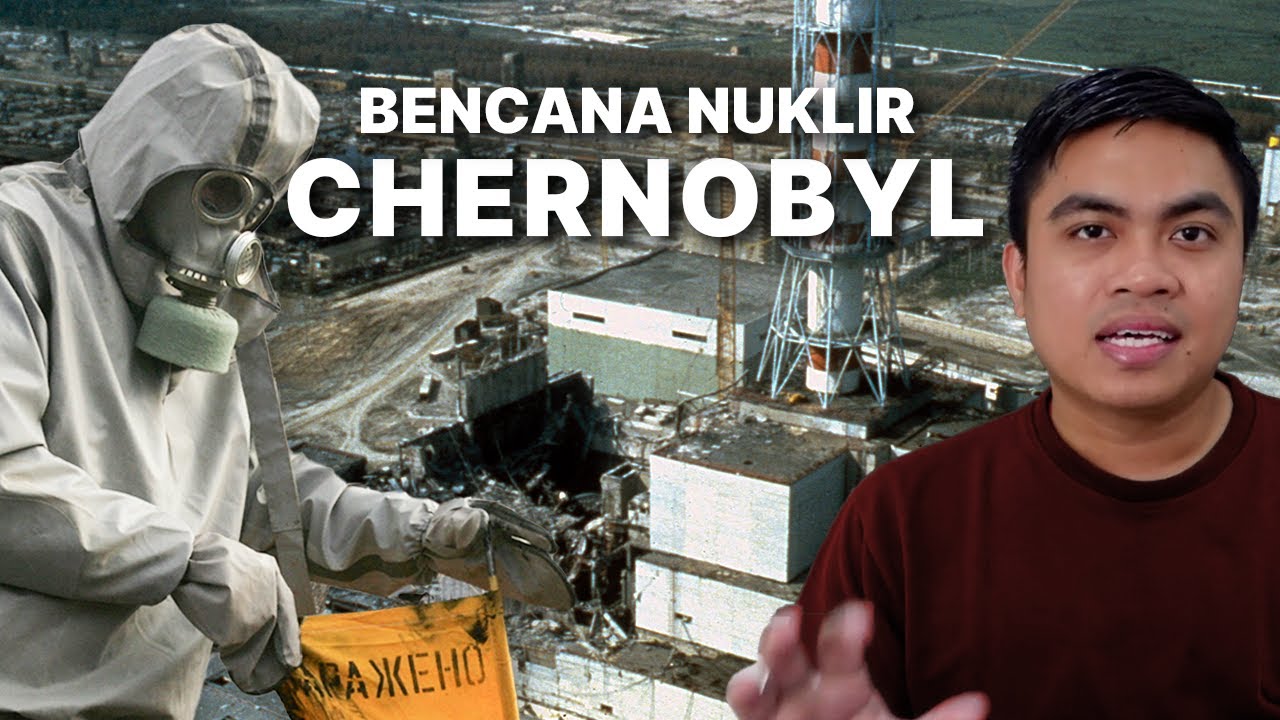
Bagaimana Kecelakaan Nuklir Terbesar di Dunia Terjadi (Chernobyl)

Praktikum Ledakan dengan Pemutih
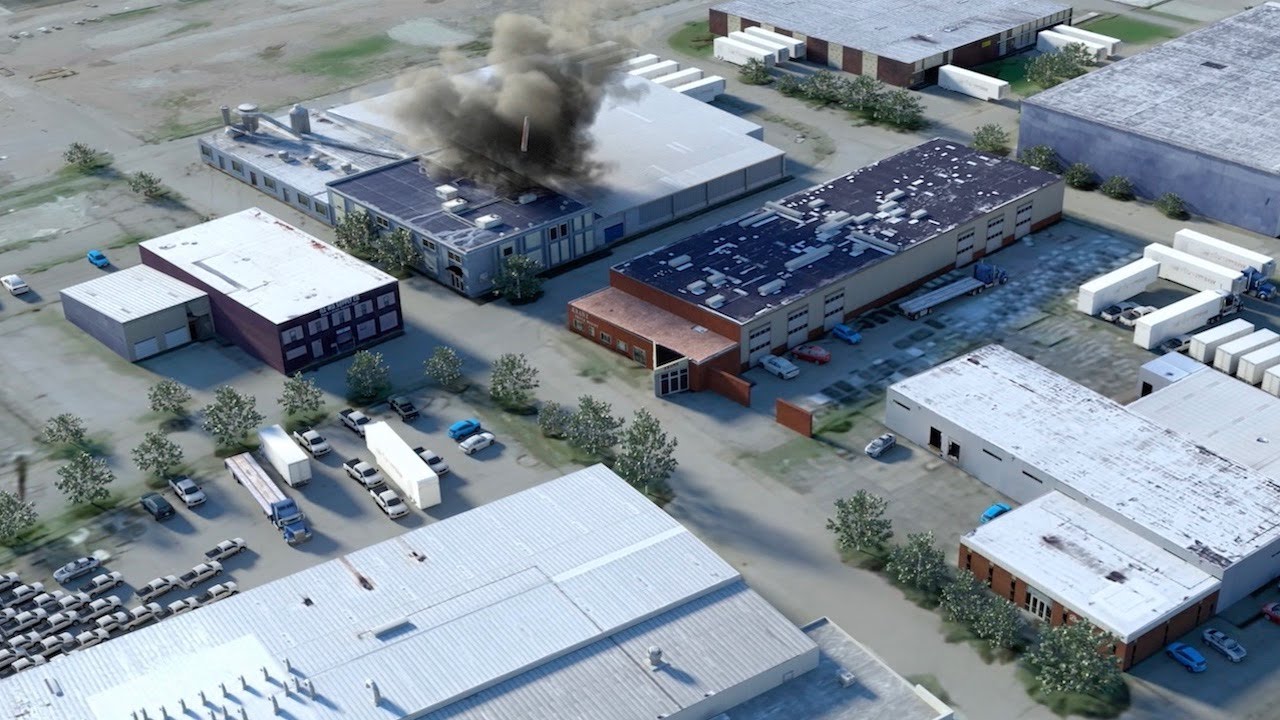
Ignored Warnings: Explosion in St. Louis
5.0 / 5 (0 votes)