Updated BP Texas City Animation on the 15th Anniversary of the Explosion
Summary
TLDRThe US Chemical Safety Board is developing an interactive training app based on OSHA's PSM regulation, using the 2005 BP Texas City Refinery explosion as a case study. The tragedy, caused by a combination of human error, inadequate safety measures, and equipment malfunction, resulted in 15 deaths and over 180 injuries. The incident underscores the critical need for robust process safety management in industrial settings.
Takeaways
- 🔥 The BP Texas City Refinery explosion in 2005 was a catastrophic event that resulted in 15 fatalities and over 170 injuries.
- 🛠 Maintenance and startup procedures at the refinery were not followed correctly, leading to a series of operational errors.
- 🏢 BP had placed trailers close to process units for contractor use without warning them of the potential hazards.
- 📈 The level indicator in the raffinate splitter tower was not designed to measure liquid levels above 9 feet, but the tower was overfilled to 13 feet.
- ⏰ Operators routinely deviated from written procedures during startups, which contributed to the unsafe conditions.
- 🛑 A high-level alarm activated, but a second alarm failed to go off, indicating a failure in the safety systems.
- 📝 Communication and logbook entries were inadequate, leading to a lack of clear instructions and understanding of the startup process.
- 👷♂️ The absence of experienced supervision and the elimination of a second board operator position due to budget cuts compromised safety.
- 🚫 Operators were unaware of the actual liquid levels and the growing danger due to improper calibration of the level indicator.
- 🌀 A flammable vapor cloud formed and was ignited by a pickup truck, leading to a series of powerful explosions and fires.
- 🏗️ The disaster resulted in significant damage to the ISOM unit and surrounding areas, with the unit being shut down for over two years.
Q & A
What is the purpose of the new interactive training application being developed by the US Chemical Safety Board?
-The new interactive training application is focused on OSHA's Process Safety Management (PSM) regulation, aiming to educate and train on the 14 elements of PSM using the 2005 explosion at BP's Texas City Refinery as a model.
What was the situation at BP's Texas City Refinery on March 23, 2005?
-Several units at the refinery had been shut down for lengthy maintenance projects, which required nearly a thousand contractors and BP employees to be onsite. BP had positioned portable trailers close to process units for the use of contractors and other maintenance workers.
Why were the trailers located near the isomerization unit potentially hazardous?
-The trailers were located near the isomerization unit, but the occupants were not warned when the ISOM unit was about to start up, which is a potentially hazardous operation.
What was the issue with the level indicator at the base of the raffinate splitter tower?
-The level indicator was not designed to measure liquid above the 9-foot mark, which led to operators being unable to know the actual level during startups when the tower was routinely filled above the 9-foot mark.
Why did operators deviate from written procedures during startups?
-Operators routinely deviated from written procedures and filled the tower above the 9-foot mark because they were concerned that if the liquid level fluctuated too low, it would cause costly damage to the furnace.
What happened at 1:14 p.m. that led to the disaster?
-At 1:14 p.m., the three emergency valves opened, sending nearly 52,000 gallons of flammable liquid to the blow down drum, which overflowed into a process sewer and created a huge flammable vapor cloud that eventually ignited.
What was the role of the control board operator in the lead-up to the explosion?
-The control board operator, who had been working a 12-hour shift for 30 days in a row, was left without a qualified supervisor to run three refinery units, including the ISOM unit, due to budget cuts and a last-minute family medical emergency of the day supervisor.
How did the ignition of the vapor cloud occur?
-The ignition occurred when flammable vapor entered the air intake of a pickup truck parked near the base of the blow down drum, causing the diesel engine to race and backfire, which ignited the vapor cloud.
What were the consequences of the explosion for the workers and the facility?
-The explosion resulted in the deaths of 15 workers, injuries to 180 others, and significant damage to the facility, including the destruction of trailers and damage to 50 large chemical storage tanks. The ISOM unit remained shut down for more than two years.
What was the significance of the BP Texas City disaster in terms of refinery accidents?
-The disaster at BP Texas City was the most serious refinery accident ever investigated by the CSB, highlighting the importance of proper safety management and adherence to procedures in the chemical industry.
Outlines
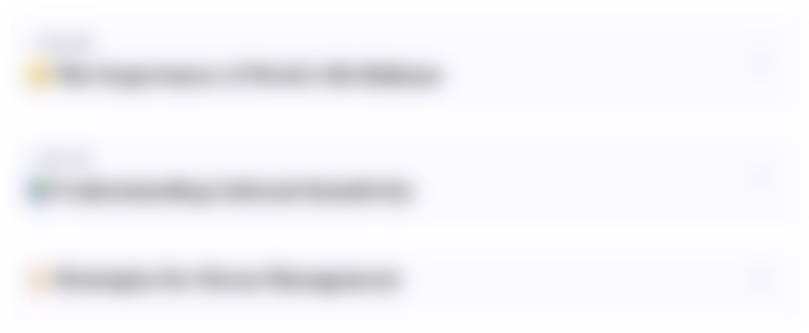
このセクションは有料ユーザー限定です。 アクセスするには、アップグレードをお願いします。
今すぐアップグレードMindmap
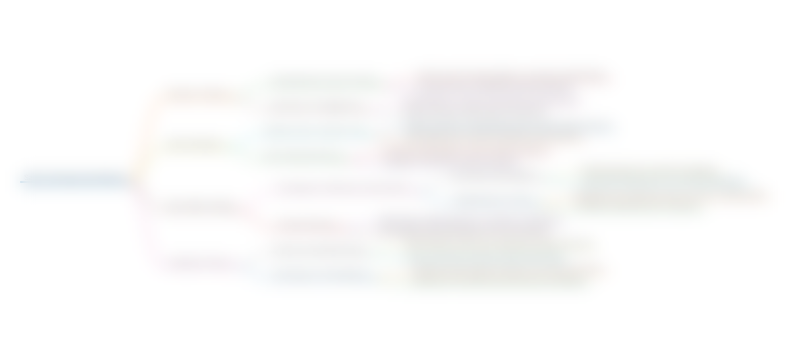
このセクションは有料ユーザー限定です。 アクセスするには、アップグレードをお願いします。
今すぐアップグレードKeywords
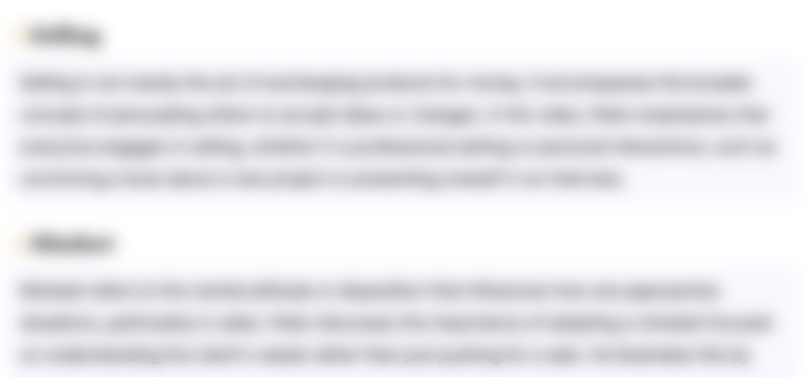
このセクションは有料ユーザー限定です。 アクセスするには、アップグレードをお願いします。
今すぐアップグレードHighlights
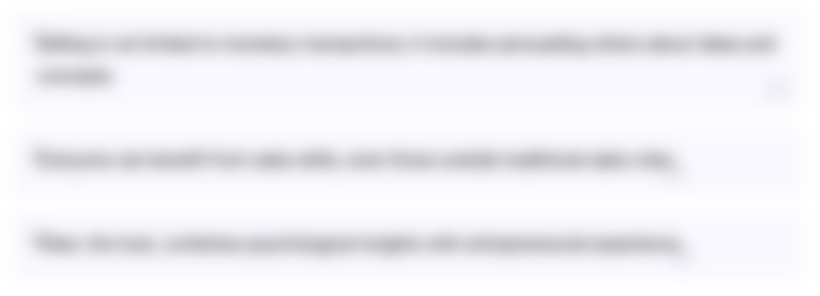
このセクションは有料ユーザー限定です。 アクセスするには、アップグレードをお願いします。
今すぐアップグレードTranscripts
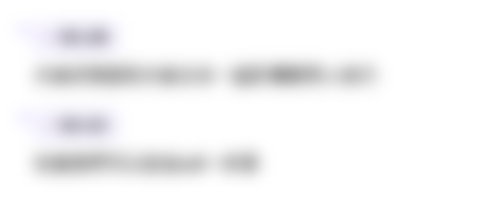
このセクションは有料ユーザー限定です。 アクセスするには、アップグレードをお願いします。
今すぐアップグレード5.0 / 5 (0 votes)