PROCESSO DE FABRICAÇÃO - ESTAMPAGEM (TELECURSO 2000)
Summary
TLDRThis video script explores the process of metal stamping, a key technique in manufacturing used to shape flat sheets of metal into various forms. The lesson covers the fundamentals of stamping, including cutting, bending, and deep drawing processes. It explains the mechanical properties of metals involved, the use of specific presses, and the importance of material properties like ductility and hardness. The script also delves into various defects in stamped products and the importance of quality control, ensuring materials are properly prepared for efficient and precise manufacturing operations.
Takeaways
- 😀 Stamping is a mechanical process that shapes metal sheets through methods like cutting, bending, and deep drawing.
- 😀 The stamping process is typically performed cold and involves the transformation of flat metal sheets into desired forms.
- 😀 Materials used in stamping include low-carbon steel, stainless steel, aluminum alloys, and brass, each selected for its plasticity.
- 😀 Presses (either mechanical or hydraulic) are used to perform stamping operations, often paired with automatic feeding systems for efficiency.
- 😀 Stamping tools include the punch (upper tool) and matrix (lower tool), which work together to shape the material.
- 😀 Cutting involves forcing a punch through the material into the matrix to produce pieces of various shapes.
- 😀 Bending is done by placing a metal sheet between a punch and matrix, deforming the material beyond its elastic limit.
- 😀 The concept of 'neutral axis' in bending refers to the area of material that experiences no deformation during the bending process.
- 😀 Deep drawing is a process that creates cup-like shapes, requiring careful control to prevent surface wrinkles and ensure a smooth finish.
- 😀 Common defects in stamped products include wrinkles, cracks, and thickness variations, often caused by material quality issues or improper stamping techniques.
- 😀 The quality of the metal sheets, including their thickness and resistance, plays a crucial role in the success of the stamping process and the avoidance of defects.
Q & A
What is stamping in the context of industrial processes?
-Stamping is a mechanical forming process where a flat sheet of metal is transformed into a new geometric shape, typically performed cold. This process involves cutting, bending, or deep drawing to shape the metal into desired forms.
What are the basic operations in stamping?
-The basic operations in stamping include cutting, bending, and deep drawing. These operations rely on the plasticity of metals to change the shape of the material without cracking.
Which types of metals are commonly used in the stamping process?
-Metals commonly used in stamping include low carbon steel, stainless steel, aluminum alloys, manganese-aluminum, magnesium-aluminum, and brass 7030, which is known for its excellent stamping properties.
Why is it important to know the material properties of metal sheets before stamping?
-It is crucial to know the material properties like hardness and tensile strength, as well as the sheet's chemical composition, to ensure the stamping process goes smoothly. The properties affect the ability to shape the material and the quality of the final product.
What role do press machines play in the stamping process?
-Press machines, either mechanical or hydraulic, are used in stamping to apply the force necessary for cutting, bending, or deep drawing. Hydraulic presses are typically used for deep drawing, while mechanical presses are used for shallower operations.
What is the importance of the die in the stamping process?
-The die is a critical tool in stamping, as it shapes the material. It consists of a punch (or male die) and a matrix (or female die), which work together to cut, bend, or form the metal into the desired shape. The die's design determines the precision and quality of the stamped parts.
What is the role of lubrication in the stamping process?
-Lubrication plays an important role in reducing friction between the punch and the die, which helps prevent damage to the tools, ensures smoother material flow, and reduces heat generation during the stamping process.
What is the difference between mechanical and hydraulic presses in stamping?
-Mechanical presses use mechanical energy to apply force and are typically used for operations like cutting and bending. Hydraulic presses, on the other hand, use hydraulic pressure to apply force and are ideal for deep drawing due to their ability to exert more precise and adjustable force.
What is the 'neutral line' in bending operations?
-The neutral line is the area within the material that experiences no tension or compression during bending. The material on the outside of the bend undergoes stretching (tension), while the material on the inside is compressed.
What are some common defects in stamped products, and what causes them?
-Common defects in stamped products include wrinkles, cracks, and uneven thickness. These can occur due to issues such as poor material quality, improper die design, insufficient lubrication, or improper pressure application during the stamping process.
Outlines
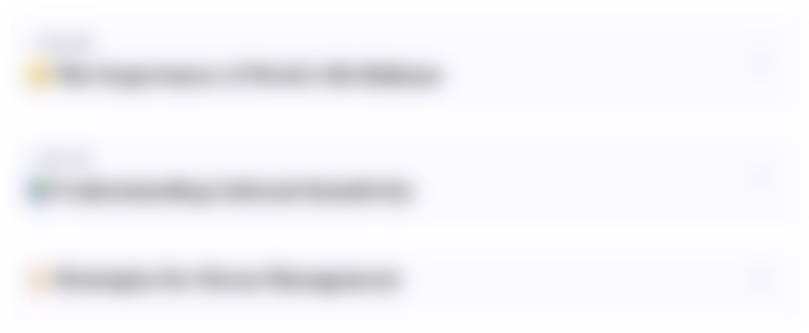
Esta sección está disponible solo para usuarios con suscripción. Por favor, mejora tu plan para acceder a esta parte.
Mejorar ahoraMindmap
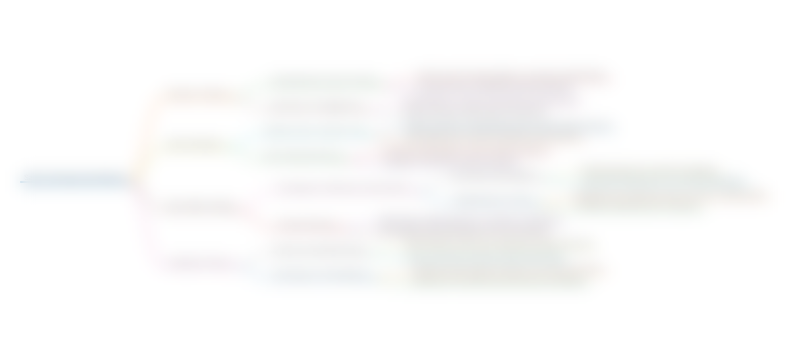
Esta sección está disponible solo para usuarios con suscripción. Por favor, mejora tu plan para acceder a esta parte.
Mejorar ahoraKeywords
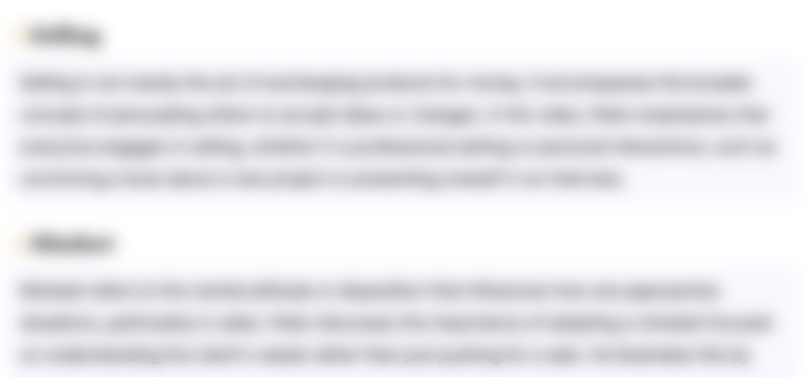
Esta sección está disponible solo para usuarios con suscripción. Por favor, mejora tu plan para acceder a esta parte.
Mejorar ahoraHighlights
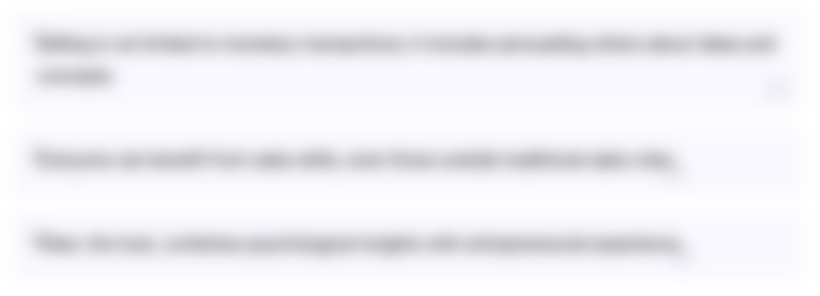
Esta sección está disponible solo para usuarios con suscripción. Por favor, mejora tu plan para acceder a esta parte.
Mejorar ahoraTranscripts
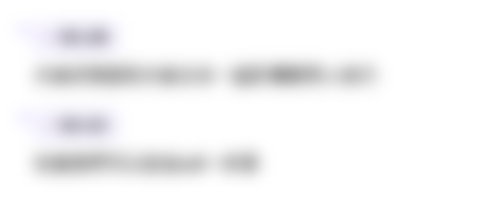
Esta sección está disponible solo para usuarios con suscripción. Por favor, mejora tu plan para acceder a esta parte.
Mejorar ahoraVer Más Videos Relacionados

Telecurso 2000 Processos de Fabricação 10 Dando forma as chapas
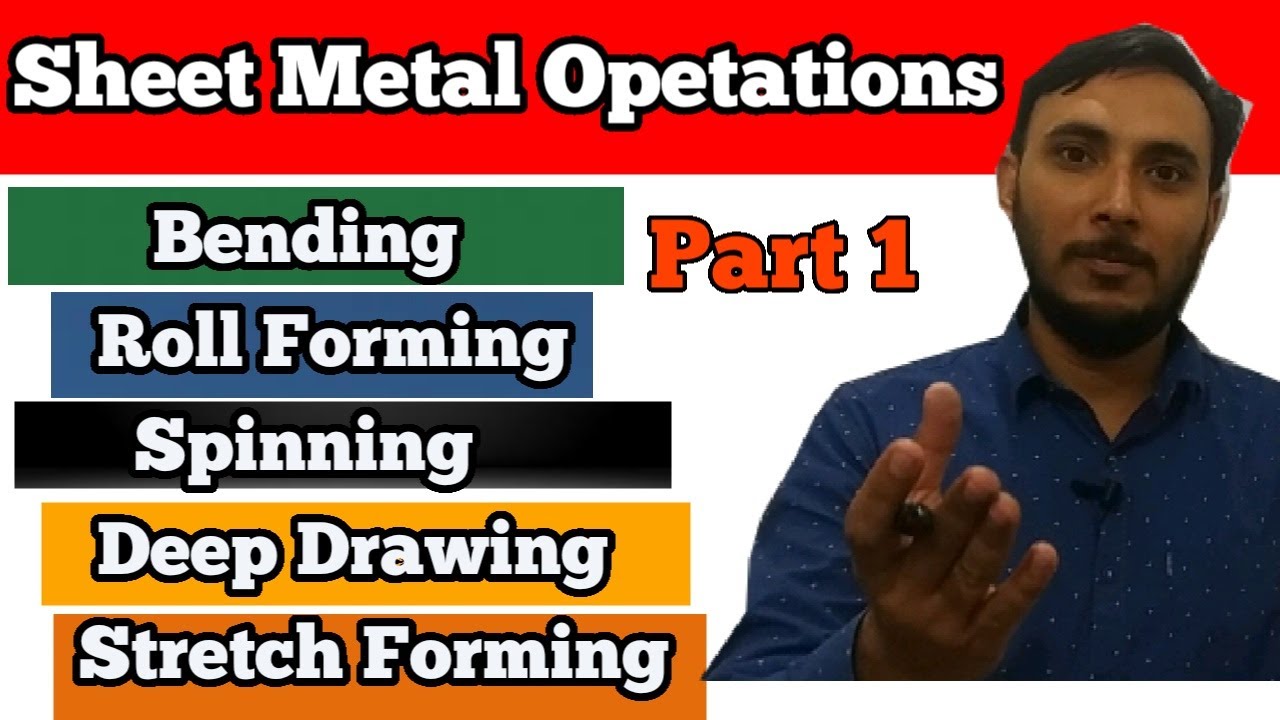
Sheet Metal Oprations || Part 1 || Metal Forming Processes
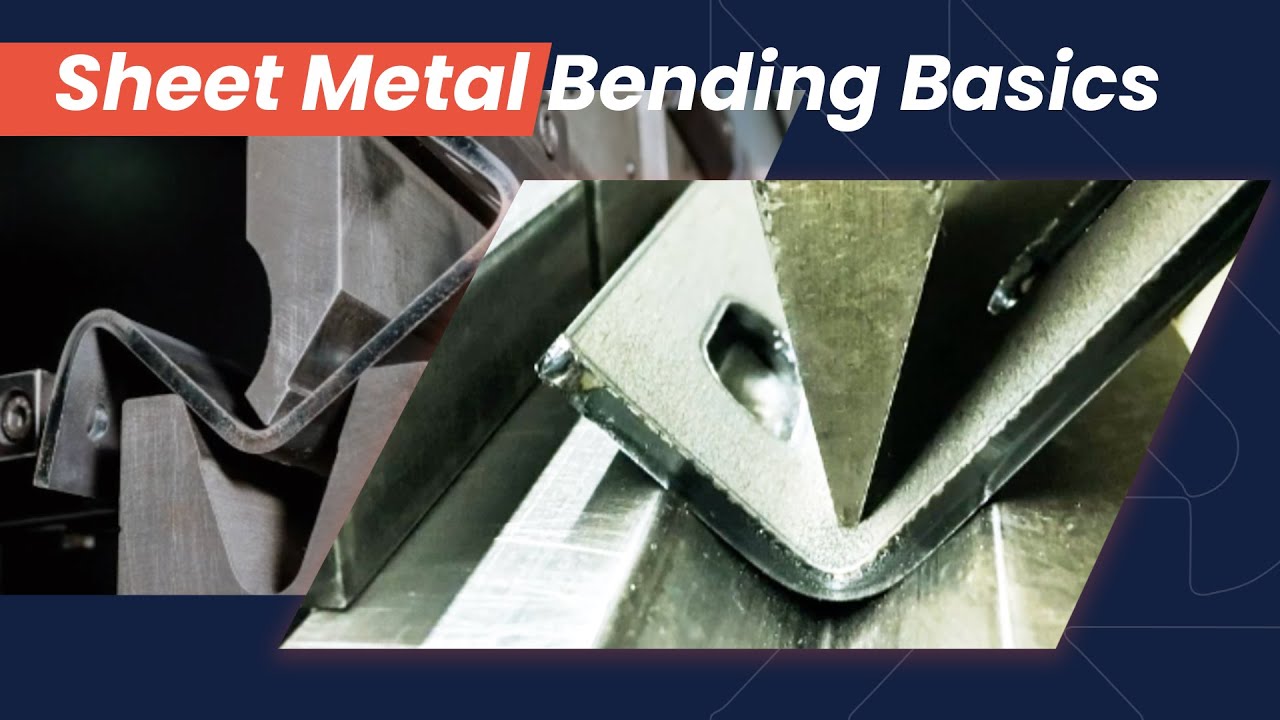
Sheet Metal Bending: Basics, Allowances, and Tips for Best Results

Laser Cutter Machines - How its Made

Proses Pengecoran
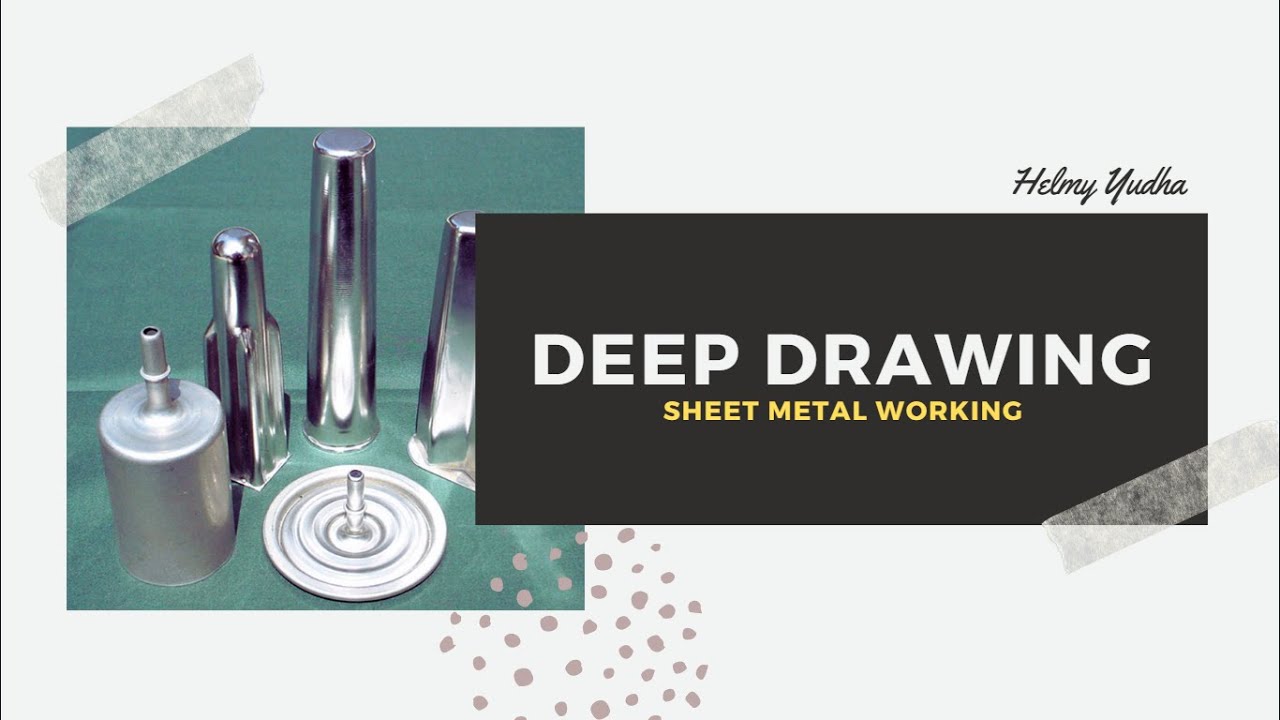
DEEP DRAWING IN SHEET METAL WORKING || Pembentukan Logam Lembaran
5.0 / 5 (0 votes)