MRP Basics & Your First Manufacturing Order | Odoo MRP
Summary
TLDRThe video introduces the manufacturing process at Stealthy Wood, highlighting the company's need for an integrated solution to handle growing demand. Instead of using multiple apps, they adopt Odoo's manufacturing system. The video walks through creating a manufacturing order for a desk combination, managing components, tracking progress, and calculating production costs. Key features like bills of materials, work orders, and real-time tracking are showcased. The process is simplified and user-friendly, making it easy to scale as production becomes more complex. The video ends with encouragement to explore more advanced features.
Takeaways
- 🚀 Stealthy Wood is growing rapidly and needs to implement a manufacturing process to meet demand.
- 💡 Many companies use up to 10 apps for manufacturing, but Stealthy Wood chose Odoo's all-in-one solution for its integration and affordability.
- 👶 The manufacturing process at Stealthy Wood is still in its early stages, so they are starting with basic steps like creating manufacturing and work orders.
- 🛠️ A bill of materials (BOM) is essential to track the components required for manufacturing products like the desk combination.
- ✅ The system checks component availability, and if all components are in stock, production can proceed smoothly.
- 🕒 Work orders can be timed to track how long each operation takes, and workers can manage tasks with the timer feature.
- 📱 A tablet view is available for workers to manage operations like pausing or continuing tasks, making the system user-friendly.
- 🎯 Real-time tracking allows the company to monitor production progress, pause, and log actual time spent on tasks.
- 💲 The system provides a cost analysis report that calculates total production costs, including components and operator labor.
- 🔄 The company can now scale up to more advanced manufacturing flows, including managing complex bills of materials and work centers.
Q & A
What is the main challenge Stealthy Wood is facing that led to the need for a manufacturing process?
-Stealthy Wood has been growing rapidly, and to meet the increasing demand, they need to implement a manufacturing process to streamline production and ensure timely deliveries.
Why did Stealthy Wood decide not to use multiple apps for their manufacturing process?
-Using up to 10 different apps to transform raw materials into a final product seemed too expensive, time-consuming, and costly to maintain for Stealthy Wood.
Why did Stealthy Wood choose Odoo Manufacturing for their process?
-Stealthy Wood chose Odoo Manufacturing because it integrates all processes into one modern, user-friendly, and affordable solution, making it easier to manage and scale their manufacturing activities.
What are the initial steps Stealthy Wood plans to take in their manufacturing process?
-Stealthy Wood plans to start with simple steps by creating a manufacturing order and a work order. The foreman will create the manufacturing order, check the components' availability, and plan production. The work orders will then be forwarded to the manufacturing operators.
What is the purpose of the Bill of Materials (BOM) in the manufacturing process?
-The Bill of Materials (BOM) lists all the required components needed to produce a product. In Stealthy Wood's case, it includes the necessary parts for manufacturing items like the desk combination.
How does Stealthy Wood check the availability of components before starting production?
-Once a manufacturing order is created, Stealthy Wood checks the availability of the components through the 'reserved' section, which shows if the components are available (in green) or unavailable (in red). They can also reserve available items and wait for the unavailable ones.
What happens when Stealthy Wood activates work orders in their manufacturing process?
-When work orders are activated, the pending manufacturing orders turn into work orders. This includes additional information like the work center, scheduled start date, expected duration, and real duration of the production process.
How does Stealthy Wood track the actual time spent on production?
-Stealthy Wood uses a timer feature that records the real duration of production. Workers can start, pause, and continue the timer to record accurate time logs. The system also tracks the time spent on breaks and other activities.
What functionality does the tablet view provide for workers at Stealthy Wood?
-The tablet view allows workers to see instructions, pause or continue the timer, block components, scrap components, or add new components. It offers a more mobile and accessible way for operators to manage the work orders.
What kind of reports does Stealthy Wood generate after completing a manufacturing order?
-Stealthy Wood generates traceability reports to track stock movements before, during, and after production, as well as cost analysis reports that show the cost of components and the cost of operations, including labor costs.
Outlines
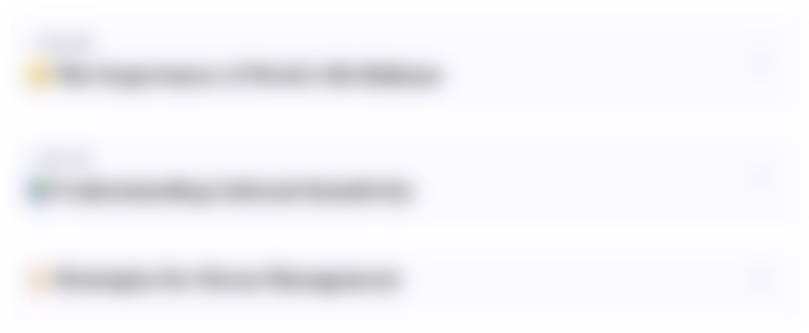
Dieser Bereich ist nur für Premium-Benutzer verfügbar. Bitte führen Sie ein Upgrade durch, um auf diesen Abschnitt zuzugreifen.
Upgrade durchführenMindmap
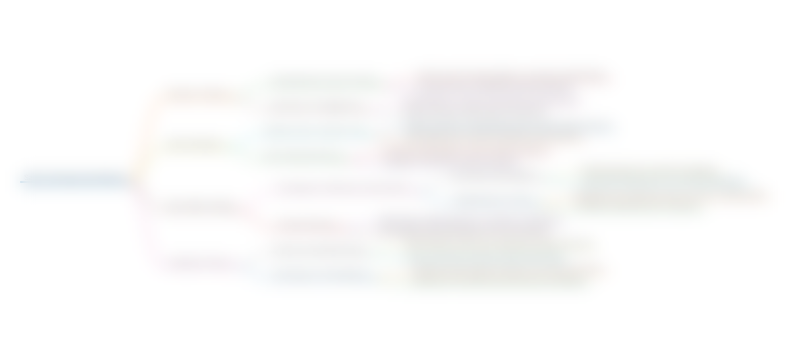
Dieser Bereich ist nur für Premium-Benutzer verfügbar. Bitte führen Sie ein Upgrade durch, um auf diesen Abschnitt zuzugreifen.
Upgrade durchführenKeywords
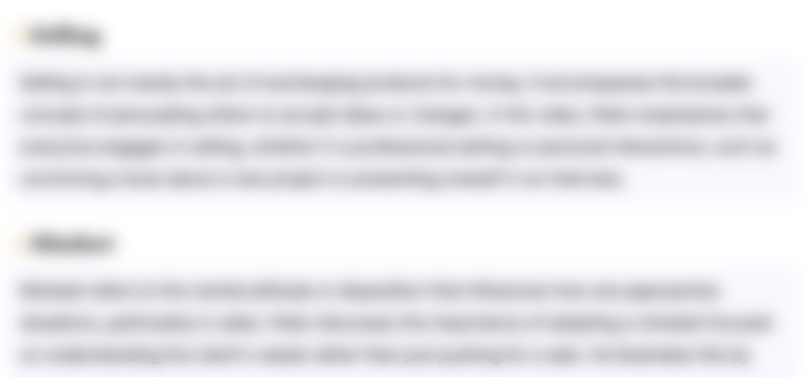
Dieser Bereich ist nur für Premium-Benutzer verfügbar. Bitte führen Sie ein Upgrade durch, um auf diesen Abschnitt zuzugreifen.
Upgrade durchführenHighlights
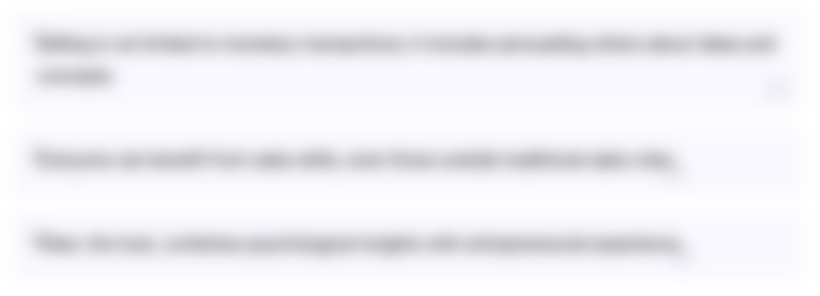
Dieser Bereich ist nur für Premium-Benutzer verfügbar. Bitte führen Sie ein Upgrade durch, um auf diesen Abschnitt zuzugreifen.
Upgrade durchführenTranscripts
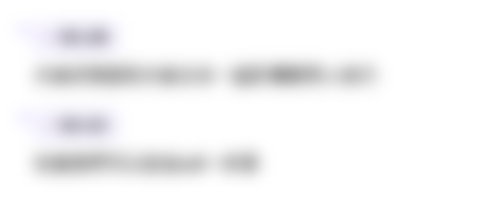
Dieser Bereich ist nur für Premium-Benutzer verfügbar. Bitte führen Sie ein Upgrade durch, um auf diesen Abschnitt zuzugreifen.
Upgrade durchführenWeitere ähnliche Videos ansehen
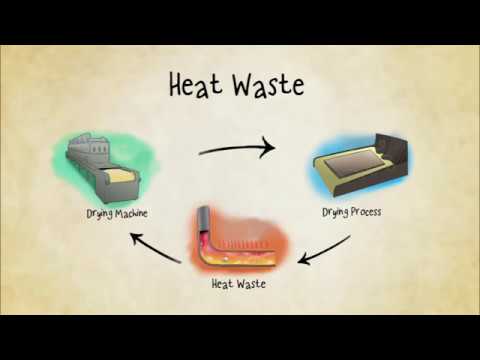
CONWOOD Production Process

Quality Overview | Odoo Quality
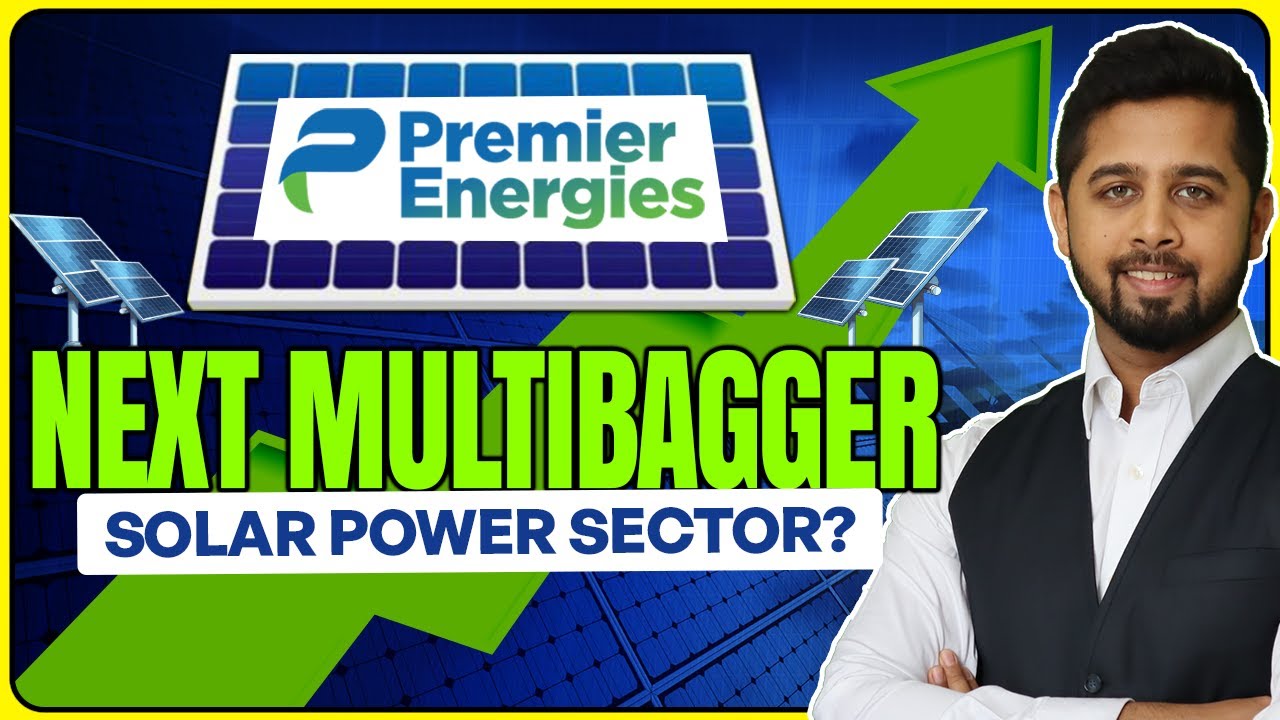
Premier Energies - Worth investing even after IPO? Premier energies fundamental Analysis
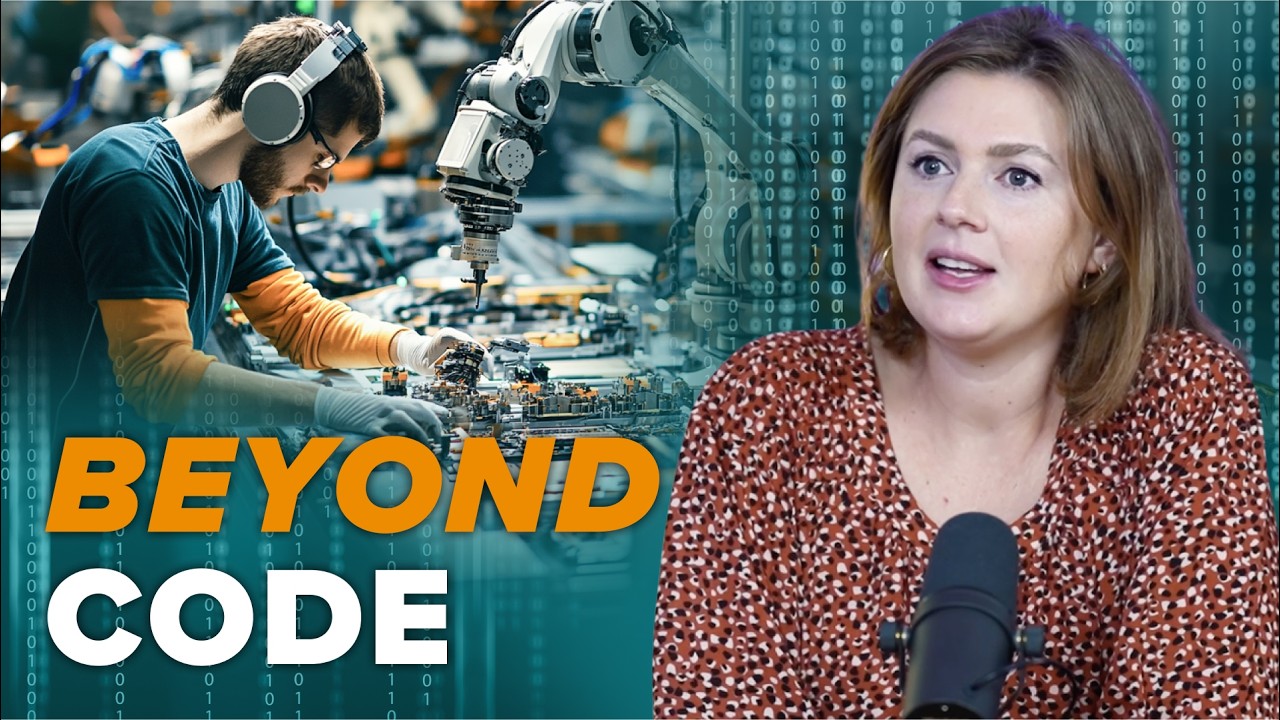
Jobs of the Future: Where Hardware Meets Software

The Paper Making Process
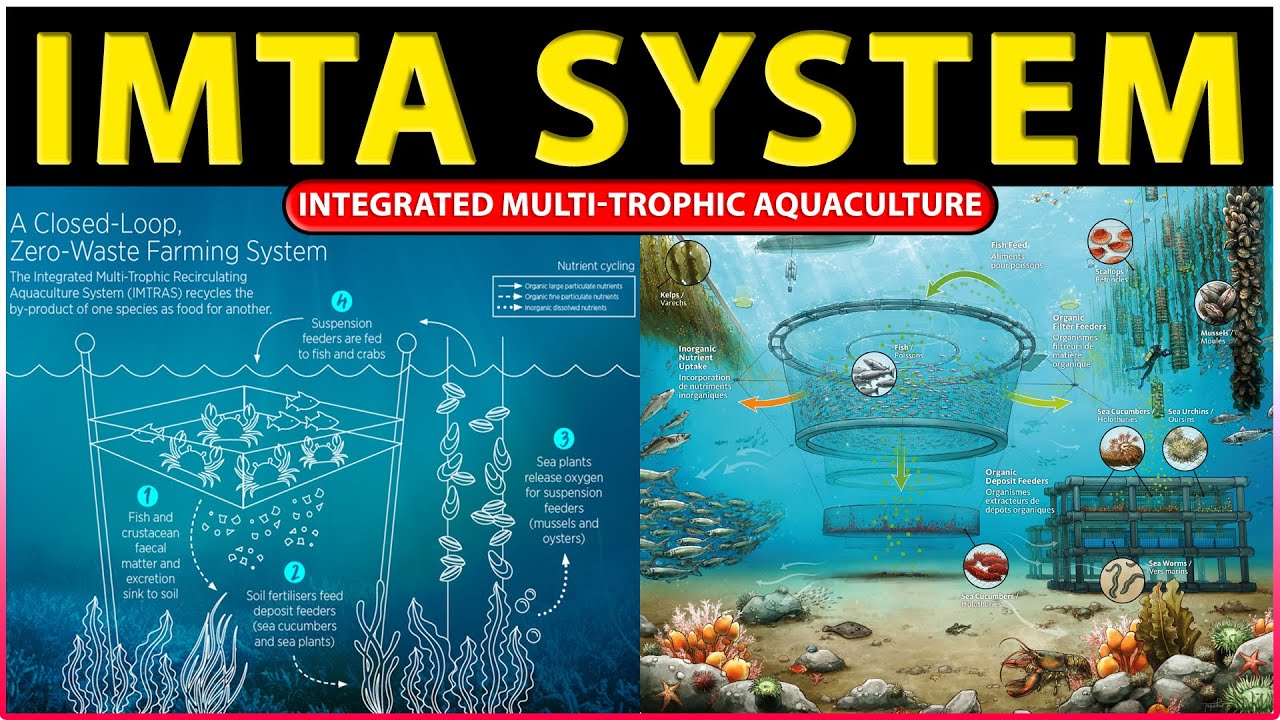
What is Integrated Multi-Trophic Aquaculture (IMTA) System? | Sustainable Aquaculture Farming
5.0 / 5 (0 votes)