Introduction to Aggregate Planning (Meaning, Concept, Objectives, Steps, Benefits, Inputs & Outputs)
Summary
TLDRAggregate planning is an intermediate capacity planning method that helps firms balance resource capacity and demand over a 2 to 18-month period. It minimizes operational costs while managing resources such as materials, labor, and machine time. The process includes forecasting demand, determining current capacity, and adjusting strategies like pricing, promotion, or subcontracting to align them. Aggregate planning focuses on optimizing inventory, workforce levels, and production rates, ensuring efficient resource use while minimizing costs. It aids in long-term operational efficiency and decision-making for future scheduling and production planning.
Takeaways
- 📅 Aggregate planning is an intermediate planning method for determining necessary resource capacity to meet expected demand, typically over a 2 to 18-month horizon.
- ⚙️ The goal of aggregate planning is to match capacity and demand in a way that minimizes costs.
- 📊 Aggregate planning involves forecasting sales, production, inventory levels, and backlogs to create a preliminary schedule of operations.
- 📉 Properly executed, aggregate planning minimizes short-term scheduling disruptions, avoiding costly fluctuations in material orders or workforce levels.
- 📈 Key objectives of aggregate planning include maximizing customer service, minimizing inventory, reducing changes in workforce levels, and ensuring efficient plant utilization.
- 🔄 The term 'aggregate' refers to planning resources in a generalized manner, such as total workers, machine hours, or raw materials, rather than focusing on specific product details.
- 🔧 Aggregate planning helps prepare for future short-term planning, such as production scheduling and material requirements planning (MRP).
- 🔀 Firms can adjust capacity or demand through strategies like pricing, promotions, backordering, or creating new demand.
- 👷 Strategies to balance capacity with demand include hiring/laying off workers, overtime, part-time labor, subcontracting, and cross-training employees.
- 📦 Finished goods inventory can be built up during periods of slack demand to meet demand during peak periods, avoiding additional labor or capacity adjustments.
Q & A
What is aggregate planning?
-Aggregate planning is an intermediate-range planning method used to determine the necessary resource capacity a firm will need to meet expected demand, typically covering a period of 2 to 18 months.
What is the primary objective of aggregate planning?
-The primary objective of aggregate planning is to match capacity and demand in a way that minimizes costs while ensuring resource availability.
Why is aggregate planning considered an operational activity?
-It is considered operational because it involves developing an aggregate plan for the production process in advance, determining how much material and other resources are needed and when they are required to minimize operational costs.
What key components are typically included in an aggregate plan?
-An aggregate plan generally includes targeted sales forecasts, production levels, inventory levels, customer backlogs, and workforce scheduling, all aimed at meeting demand forecasts at the lowest possible cost.
How does aggregate planning minimize short-term scheduling issues?
-By taking a longer-term view, aggregate planning minimizes the effects of short-sighted, day-to-day scheduling that can lead to frequent workforce layoffs, rehiring, and irregular material ordering.
What are the main objectives of aggregate planning in terms of resource management?
-The main objectives include maximizing customer service, minimizing inventory investment, reducing fluctuations in workforce levels, stabilizing production rates, and optimizing plant and equipment utilization.
How does aggregate planning differ between product and service industries?
-In product industries, aggregate units of output might include gallons, feet, or pounds, while in service industries, aggregate units might refer to hours of service delivered, the number of patients seen, or other similar metrics.
What are some methods companies use to increase demand to match capacity?
-Methods include varying pricing, promotions, back-ordering, creating new demand, and partitioning demand through scheduling systems like reservations and appointments.
What strategies can companies use to adjust capacity to meet demand?
-Companies can hire or lay off workers, use overtime, employ part-time or casual labor, build up inventory, subcontract production, or use cross-trained employees to handle varying workloads.
What are the key inputs and outputs of aggregate planning?
-Key inputs include availability of resources, equipment costs, and inventory costs, while outputs include total plan cost, estimated levels of inventory, and employment projections, all of which are crucial for decision-making.
Outlines
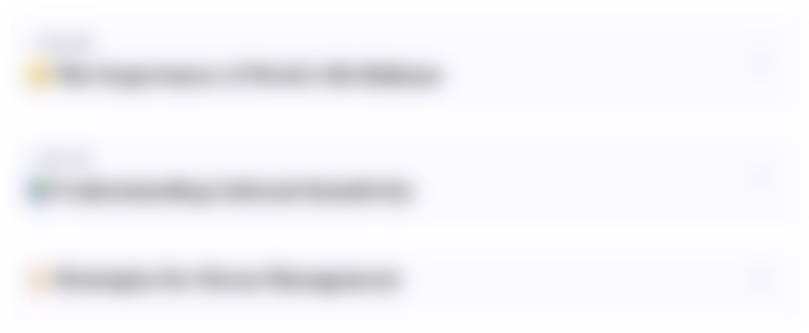
هذا القسم متوفر فقط للمشتركين. يرجى الترقية للوصول إلى هذه الميزة.
قم بالترقية الآنMindmap
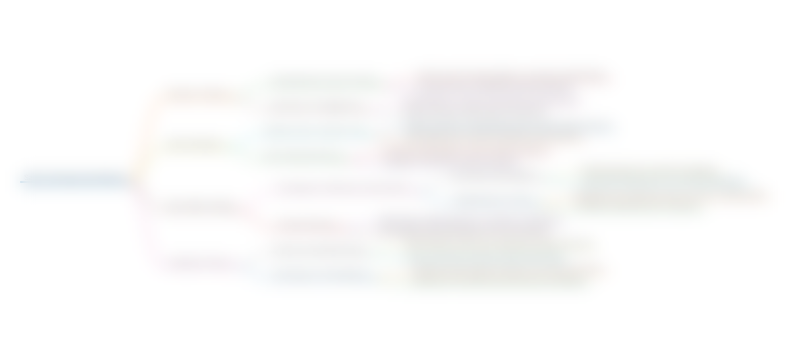
هذا القسم متوفر فقط للمشتركين. يرجى الترقية للوصول إلى هذه الميزة.
قم بالترقية الآنKeywords
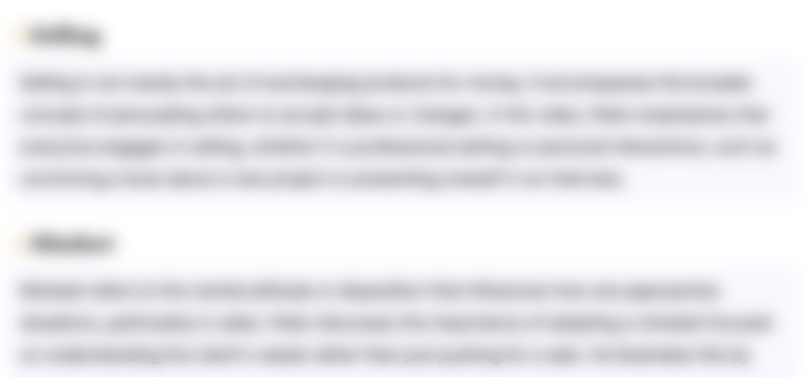
هذا القسم متوفر فقط للمشتركين. يرجى الترقية للوصول إلى هذه الميزة.
قم بالترقية الآنHighlights
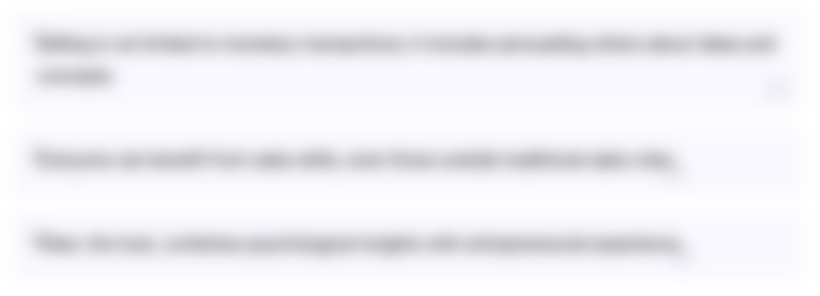
هذا القسم متوفر فقط للمشتركين. يرجى الترقية للوصول إلى هذه الميزة.
قم بالترقية الآنTranscripts
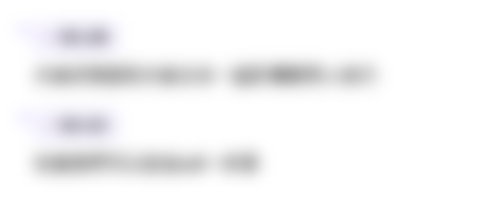
هذا القسم متوفر فقط للمشتركين. يرجى الترقية للوصول إلى هذه الميزة.
قم بالترقية الآن5.0 / 5 (0 votes)