Part #11: Analytic design & sensitivity analysis of V-type IPM motors
Summary
TLDRThis educational video delves into sensitivity analysis, a crucial step in the design optimization process. It teaches viewers how to perform sensitivity analysis in Excel, focusing on how dependent variables like motor weight change with independent variables such as aspect ratio and magnetic loading. The video uses practical examples to illustrate the impact of design variables on motor characteristics and includes a discussion on mechanical constraints. It concludes with an overview of the code behind the analysis, offering insights into the design process for electric motors.
Takeaways
- 🔍 Sensitivity analysis is a crucial step in the design optimization process, focusing on how dependent variables change with respect to independent variables.
- 📊 The sensitivity analysis sheet in Excel is used to perform this analysis, with inputs including cell references for decision variables, mean and max values, and the number of calculation points.
- 📈 An example is given where the weight of the motor's active parts is analyzed as a function of the aspect ratio, showing an increase in weight with an increase in aspect ratio.
- 📉 The video demonstrates how to conduct sensitivity analysis by adjusting the cell references and values for independent and dependent variables, and then running the analysis to generate graphs.
- 📋 Discretization during the analytic design can cause jumps in the sensitivity analysis curves, which are explained as a result of the design process.
- 🧲 The video explains why the outer diameter of the stator lamination is not sensitive to magnetic loading, contrary to initial expectations, by reviewing the motor output equation.
- 🔌 The variation of the stator board diameter with respect to magnetic loading is investigated, showing a decrease in diameter as magnetic loading increases.
- 🔥 An increase in electrical loading leads to a decrease in motor weight due to improved cooling methods, but also results in increased copper losses, as demonstrated in the sensitivity analysis.
- 🛠️ Mechanical constraints, such as the outer diameter of the stator lamination and stack length, are considered in the sensitivity analysis to ensure they fall within specified limits.
- 💻 The code behind the sensitivity analysis is discussed, including functions for sensitivity analysis and slot pole combination, which can be customized based on the design requirements.
Q & A
What is sensitivity analysis and why is it important in the design optimization process?
-Sensitivity analysis is a method used to understand how different variables affect a particular output or decision by systematically changing input variables and observing the changes in the output. It is important in the design optimization process because it helps identify which variables have the most significant impact on the design's performance, allowing for more informed decisions and more efficient optimization.
How is the sensitivity analysis sheet set up in the Excel file mentioned in the script?
-The sensitivity analysis sheet in the Excel file consists of five inputs: a cell reference for the decision variable, the mean value and maximum value of the selected decision variable, a cell reference for the objective (a dependent variable), and the number of calculation points. These inputs allow users to perform sensitivity analysis by varying the independent variables and observing the effects on the dependent variables.
What is an example of an independent variable and its corresponding cell reference in the sensitivity analysis?
-An example of an independent variable is the aspect ratio, and its corresponding cell reference is P18. This variable is used to investigate how the weight of the motor varies as a function of the aspect ratio.
What is the purpose of setting a minimum and maximum value for the independent variable in sensitivity analysis?
-Setting a minimum and maximum value for the independent variable allows the sensitivity analysis to cover a range of possible values for that variable. This range is used to generate calculation points and observe how changes within this range affect the dependent variable, providing insights into the variable's sensitivity and potential constraints.
How does the number of calculation points affect the sensitivity analysis?
-The number of calculation points determines the granularity of the sensitivity analysis. A higher number of points provides a more detailed view of how the dependent variable changes with the independent variable, but it may also increase computation time. Conversely, a lower number of points may result in a less detailed analysis but is quicker to compute.
What does the script suggest about the relationship between the weight of active parts and the aspect ratio?
-The script suggests that the weight of active parts of the motor increases as the aspect ratio increases. This relationship is visualized through a graph generated by the sensitivity analysis, which shows the variation of the weight of active parts as a function of the aspect ratio.
Why might there be jumps in the sensitivity analysis curve?
-Jumps in the sensitivity analysis curve may occur due to discretization. The script mentions two types of discretization during the analytic design: one for fixing the number of turns and another for the proper selection of wire gauge size from the SWG table. These jumps reflect the discrete changes in the design variables that can affect the output.
How does the script explain the insensitivity of the stator lamination's outer diameter to magnetic loading?
-The script explains that although one might expect the outer diameter of the stator lamination to decrease with increased magnetic loading, the motor output equation shows that the weight of active parts (and thus the volume) should decrease as the motor output constant increases with magnetic loading. This is because the equation includes the inner diameter (d), not the outer diameter (do), and the aspect ratio is held constant.
What is the significance of investigating the variation of the motor's electrical loading in sensitivity analysis?
-Investigating the variation of the motor's electrical loading is significant because it affects the motor's cooling method and copper losses. Higher electrical loading can lead to better cooling methods but also results in increased copper losses, as shown when the objective is set to copper losses (PCU) in the sensitivity analysis.
How does the script use sensitivity analysis to address mechanical constraints?
-The script uses sensitivity analysis to address mechanical constraints by investigating how changes in the aspect ratio affect the outer diameter of the stator lamination. By adjusting the aspect ratio and observing the changes in the outer diameter, the script demonstrates how to meet a mechanical constraint that requires the outer diameter to be within a certain limit.
What is the purpose of the code behind the sensitivity analysis module mentioned in the script?
-The code behind the sensitivity analysis module is designed to automate the process of running sensitivity analyses. It includes functions for generating the analysis and selecting the best combination of design variables like the number of stator slots and poles based on the application. The code is customizable to fit different designs and inputs, and it includes constraints for the number of samples to ensure accurate and reliable analysis.
Outlines
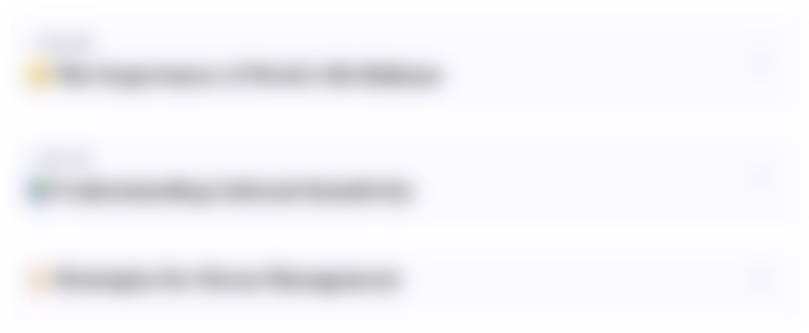
هذا القسم متوفر فقط للمشتركين. يرجى الترقية للوصول إلى هذه الميزة.
قم بالترقية الآنMindmap
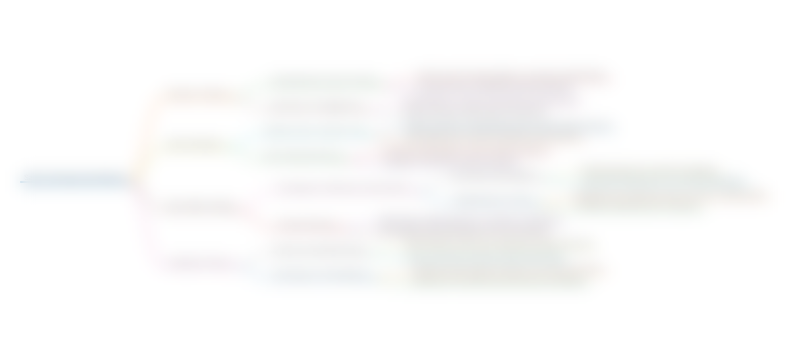
هذا القسم متوفر فقط للمشتركين. يرجى الترقية للوصول إلى هذه الميزة.
قم بالترقية الآنKeywords
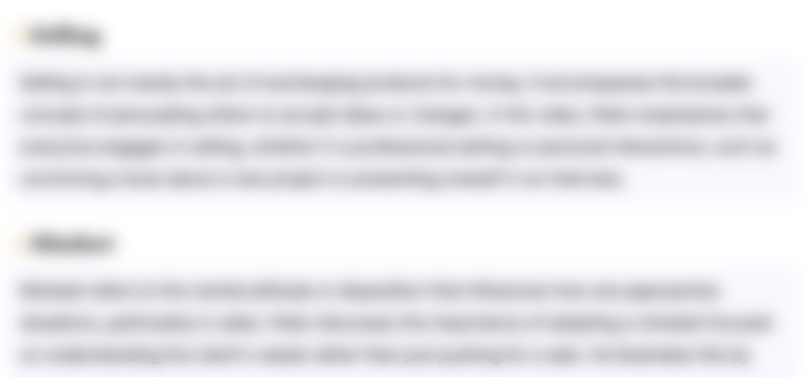
هذا القسم متوفر فقط للمشتركين. يرجى الترقية للوصول إلى هذه الميزة.
قم بالترقية الآنHighlights
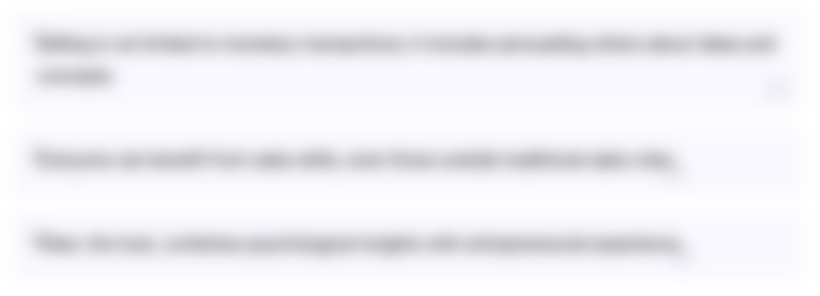
هذا القسم متوفر فقط للمشتركين. يرجى الترقية للوصول إلى هذه الميزة.
قم بالترقية الآنTranscripts
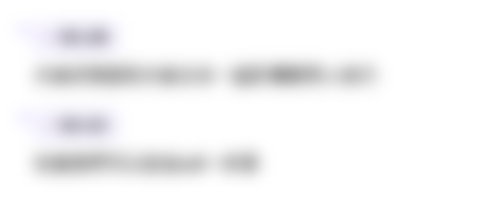
هذا القسم متوفر فقط للمشتركين. يرجى الترقية للوصول إلى هذه الميزة.
قم بالترقية الآنتصفح المزيد من مقاطع الفيديو ذات الصلة

His tag protein purification | Application of his tag purification | Affinity chromatography

The Ultimate UX Design Process | Step by Step Guide From Research to Prototype & Beyond
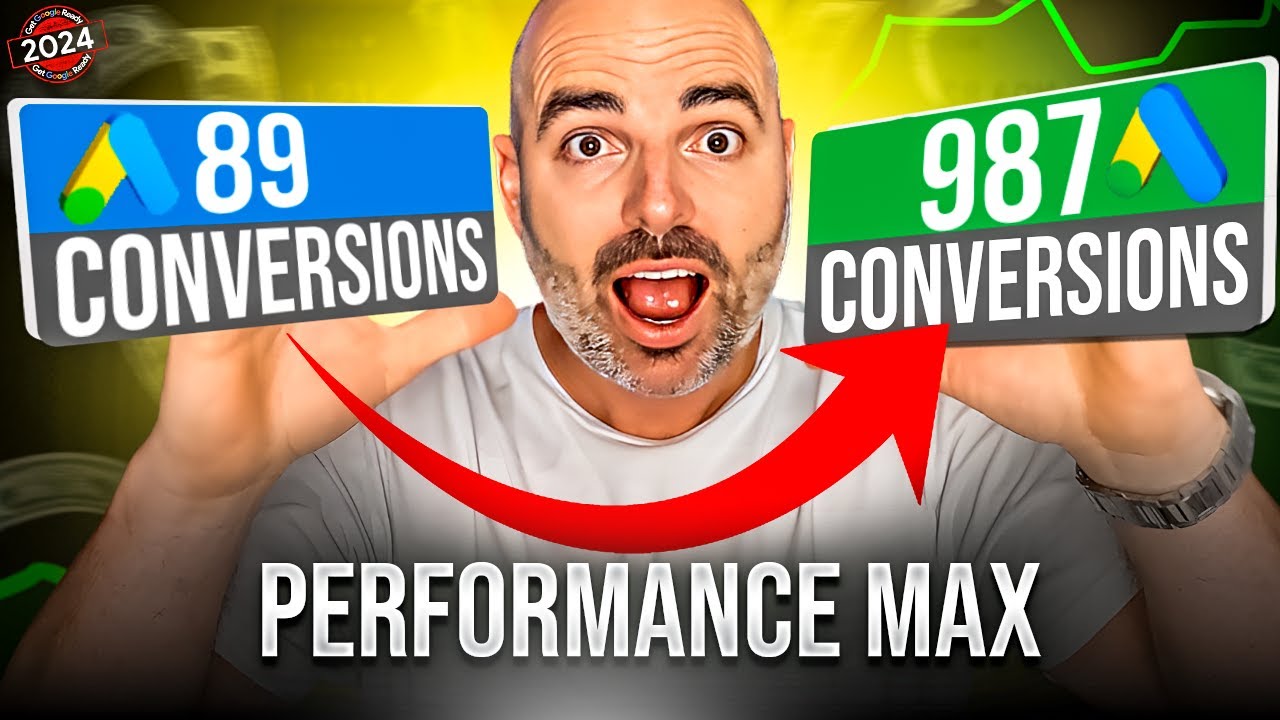
Optimising Performance Max Campaigns in 2024
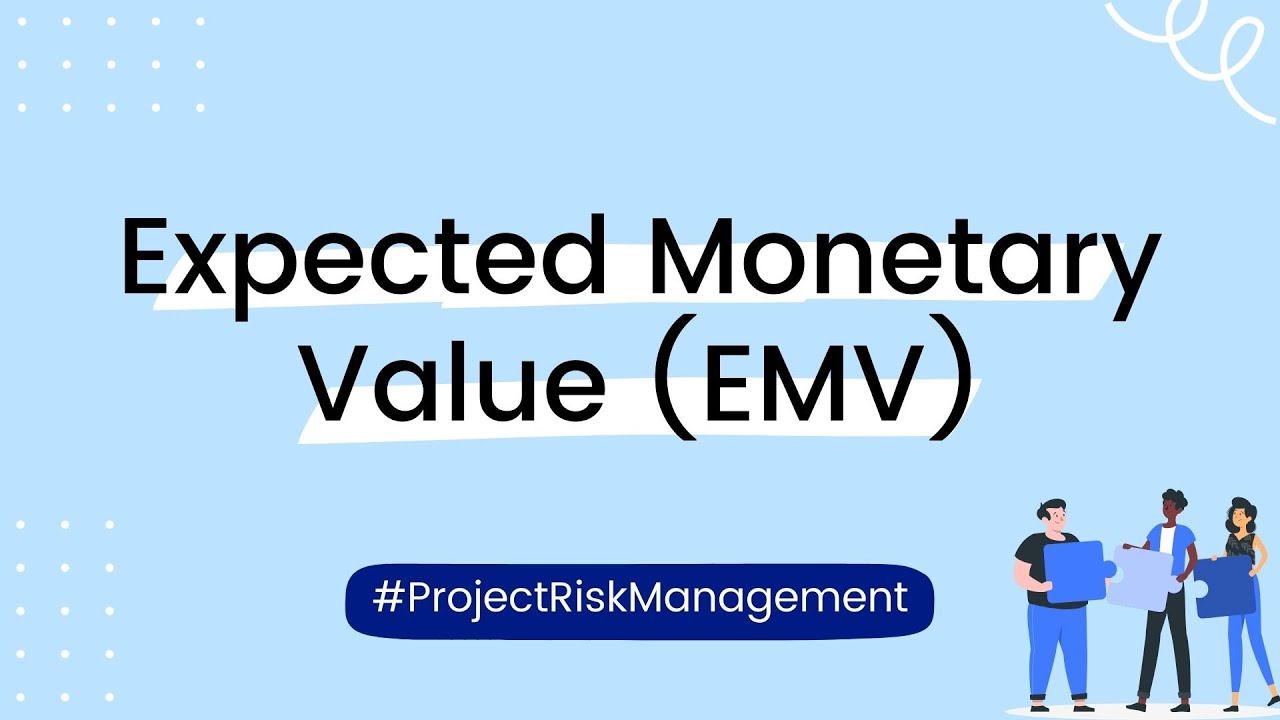
Project Risk Management: Expected Monetary Value (EMV)

Free Local SEO Course ($5,000 + Value)

Dear all calculus students, This is why you're learning about optimization
5.0 / 5 (0 votes)